Курсовая работа: Назначение и характеристика кривошипно-шатунного механизма двигателя Д–240
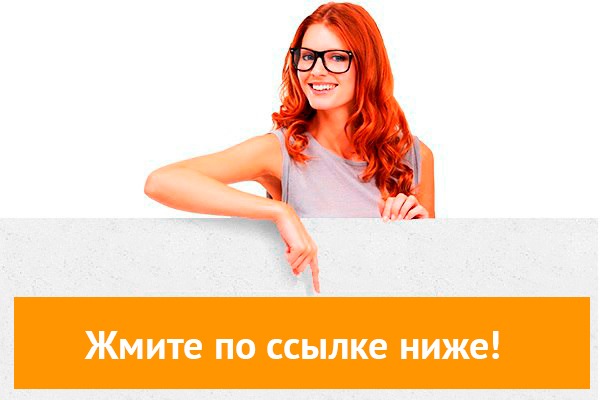
💣 👉🏻👉🏻👉🏻 ВСЯ ИНФОРМАЦИЯ ДОСТУПНА ЗДЕСЬ ЖМИТЕ 👈🏻👈🏻👈🏻
1 .Назначение и характеристика кривошипно - шатунного механизма двигателя Д – 240
2 .Назначение, устройство, анализ условий работы и дефекты коленчатого вала двигателя марки Д-240
3 .Применяемые способы восстановления коленчатого вала
4 .Проектирование технологического процесса восстановления коленчатого вала
4.1 Обоснование способов восстановления. Выбор рационального способа восстановления
4.2 Определение режимов нанесения покрытия, выбор материалов и технологического оборудования, механической обработки и норм времени выполняемых операций
4.3 Технико - экономическое обоснование проекта
1 Назначение сборочной единицы (кривошипно-шатунного механизма двигателя Д-240)
Кривошипно-шатунный механизм является основным механизмом поршневого двигателя. Он служит для восприятия давления газов в такте рабочего хода и преобразования возвратно-поступательного движения поршней во вращательное движение коленчатого вала. Он состоит из блок-картера, гильз и головок цилиндров, поршней с кольцами и поршневыми пальцами, шатунов, коленчатого вала, коренных и шатунных подшипников и маховика.
Во время работы двигателя на детали кривошипно-шатунного механизма действуют давление газов, силы инерции возвратно-поступательно движущихся масс, инерции неуравновешенных вращающихся масс, тяжести и трения. Все эти силы, за исключением силы тяжести, изменяют значение и направление рассматриваемых величин в зависимости от угла поворота коленчатого вала и процессов, происходящих в цилиндре двигателя.
2 Назначение, устройство, анализ условий работы и дефекты коленчатого вала двигателя марки Д-240
Коленчатый вал - одна из основных деталей двигателя, определяющая вместе с другими деталями цилиндропоршневой группы его ресурс. Ресурс коленчатого вала характеризуется двумя показателями: усталостной прочностью и износостойкостью. Коленчатый вал воспринимает через шатуны усилия, действующие на поршни, и передает их механизмам трансмиссии. От него приводятся в действие различные механизмы двигателя.
Коленчатый вал (рисунок 1.1) состоит из следующих основных элементов:
а) коренных шеек 1
, которыми вал опирается на коренные подшипники, расположенные в картере;
в) щек 2
и 12,
связывающих коренные и шатунные шейки; дляуменьшения концентрации напряжений, места перехода шеек в щекивыполнены в виде закруглений 13,
называемых галтелями;
Рисунок 1.1- Коленчатый вал дизеля Д-240:
1
- коренная шейка; 2
- щека; 3
- упорные полукольца; 4
- нижний вкладыш пятого коренного подшипника; 5
- маховик; 6
- маслоотражатель; 7
-установочный штифт; 8
- болт крепления маховика; 9
- зубчатый венец; 10
- верхний вкладыш пятого коренного подшипника; 11
- шатунная шейка; 12
- щека; 13
- галтель; 14
- противовес; 15
- болт крепления противовеса; 16
- замковая шайба; 17
-шестерня коленчатого вала; 18
- ведущая шестерня привода масляного насоса; 19
-упорная шайба; 20
- болт; 21
- шкив; 22 - канал подвода масла в полость шатунной шейки; 23
- пробка; 24
- полость в шатунной шейке; 25
- трубка для чистого масла.
При эксплуатации двигателя в результате действия высоких и непостоянных динамических нагрузок от давления газов и сил инерции возвратно-поступательно движущихся и вращающихся частей вал подвергается кручению и изгибу, отдельные поверхности (шатунные и коренные шейки и др.) - изнашиванию. В структуре металла накапливаются усталостные повреждения, возникают микротрещины и другие дефекты. Износ элементов определяют, используя универсальный и специальный мерительный инструмент. Для обнаружения трещин используютмагнитные дефектоскопы. При эксплуатации у коленчатых валов возникает, как правило, много дефектов, основные из которых приведены в таблице 1.1.
Таблица 1.1 - Основные возможные неисправности коленчатых валов и способы их устранения
коренных и шатунных шеек; овальность, конусность, задиры
Резьбы (срыв более двух ниток резьбы)
3 Применяемые способы восстановления коленчатого вала
Основной дефект коленчатых валов — износ коренных и шатунных шеек. Износ шеек устраняют шлифованием их под ремонтный размер. Для шлифования валов служат станки ЗА423 или ЗВ423. Шейки вала шлифуют электрокорундовыми кругами на керамической связке зернистостью 16...60 мкм, твердостью СМ2, CI, С2, СТ1 и СТ2. При восстановлении коленчатых валов перешлифовкой под ремонтный размер шеек практически невозможно обеспечить их 100%-й ресурс, и он уменьшается тем больше, чем больше номер ремонтного размера. Это объясняется тем, что твердость закаленных ТВЧ шеек уменьшается от поверхности по сечению вала и при шлифовании удаляется наиболее твердый слой. Некоторые ремонтные предприятия для обеспечения высокой износостойкости и ресурса валов после перешлифовки шеек выполняют их закалку ТВЧ, лазерное упрочнение и др.
Коренные и шатунные шейки, вышедшие за ремонтные размеры, восстанавливают наращиванием различными методами: наплавкой (под флюсом, плазменной, в среде защитных газов, широкослойной и др.); гальваническими покрытиями (железнением, хромированием); металлизацией; напеканием порошков; электроконтактной приваркой ленты; приваркой или приклеиванием полуколец; пластинированием и др.
Более 85 % объема восстановления шеек коленчатых валов выполняют наплавочными способами и прежде всего наплавляют под слоем флюса. При этом можно выделить следующие основные варианты технологических процессов: наплавка без термической обработки; наплавка с последующей термической обработкой; термическая обработка, наплавка, термическая обработка; наплавка, упрочнение.
Наиболее распространенной считают наплавку пружинной проволокой второго класса под слоем легированного флюса, представляющего собой смесь, состоящую из плавленного флюса АН-348А (93,2 %),
феррохрома (2,2 %), графита (2,3 %) и жидкого стекла (2,5 %). Этот метод резко снижает усталостную прочность наплавленных коленчатых валов из-за наличия огромного количества трещин.
Разработана наиболее прогрессивная технология наплавки изношенных коленчатых валов. Она предусматривает наплавку шеек валов проволокой Нп-30ХГСА под флюсом АН-348А с последующей механической обработкой и полным повторным циклом термической обработки (нормализация и закалка ТВЧ). Эта технология требует специального термического оборудования и целесообразна при большой производственной программе восстановления.
Для восстановления шеек валов используют электроконтактную припайку стальной ленты из стали 50ХФА, дуговую металлизацию порошковой проволокой ПП-ОМ-2.
Коленчатые валы некоторых двигателей (типа ЗМЗ и др.) изготавливают из высокопрочного магниевого чугуна ВЧ50 и ВЧ45. Их износостойкость и усталостная прочность примерно одинаковы с соответствующими показателями валов, выполненных из стали 45, но себестоимость получения заготовок отливкой в 2,0...2,5 раза ниже получения поковок. В то же время чугун относится к трудно-свариваемым материалам. Поэтому рассмотренные выше способы наплавки не дают хороших результатов при восстановлении чугунных валов.
Для восстановления чугунных коленчатых валов применяют следующие способы дуговой наплавки: по стальной оболочке; двухслойную наплавку; наплавку с последующей нормализацией; наплавку проволокой Нп-15 СТЮЦА под слоем флюса АН-348А; широкослойную наплавку малоуглеродистой проволокой марки 08А с добавлением в зону горения дуги ферромагнитной шихты и др.
При восстановлении валов дуговой наплавкой усталостная прочность валов достигает 80 % новых, но процесс сложен и трудоемок.
При двухслойной наплавке оболочкой служит первый наплавленный слой, который получают с помощью малоуглеродистой порошковой проволоки под слоем
флюса АН-348А. Второй слой наплавляют как бы по стальной поверхности обычными методами. Однако усталостная прочность таких валов составляет всего около 70 % новых.Наплавку с последующей нормализацией применяют для восстановления чугунных коленчатых валов двигателя ЗМЗ-53, которые разрушаются из-за усталости после наплавки по шатунным шейкам. При нормализации твердость наплавленных шатунных шеек уменьшается до HRC 25...30, снижаются внутренние напряжения, и в итоге усталостная прочность повышается до 85 % уровня новых валов. Некоторое снижение износостойкости шатунных шеек компенсируется ее запасом по сравнению с коренными шейками.К перспективным и эффективным способам восстановления стальных и чугунных коленчатых валов относится плазменная наплавка. Рекомендуют комбинированный способ наплавки, предусматривающий одновременную подачу проволоки и порошка.При восстановлении коленчатых валов, изготовленных из стали 45 (СМД-14, А-41 и др.), шейки наплавляют композицией проволока Св-08МХ или Св-08Г2С (85 %) + порошок ПГ-СР4 (15 %), а галтели - той же композицией, но в соотношении 75 и 25 %. Валы из стали 50Г (ЯМЗ-238НБ и др.) наплавляют проволокой Св-15ГСТЮЦА (75...80 %) и порошком ПГ-СР4 или ПГ-СРЗ (20...25%). При восстановлении чугунных валов применяют проволоку Св-15ГСТЮЦА (70%) и порошок ПР-Н70Х17 СЧР4 (30 %).
Для восстановления чугунных коленчатых валов разработано и внедрено два способа: постановка полуколец и пластинирование.Предел выносливости методом постановкой полуколец коленчатого вала такой же, как и нового (рисунок 1.3). Метод восстановления шеек валов пластинированием заключается в установке с последующим механическим креплением на шейках валов стальной холоднокатаной термообработанной полированной ленты, изготовленной из пружинистой стали типа 65Г (рисунок 1.2).
Рисунок 1.2 - Схема восстановления шеек коленчатого вала пластинированием
Рисунок 1.3 - Схема восстановления шеек коленчатого вала двигателя ЗМЗ-53 приваркой стальных полуколец
При использовании данного метода можно существенно упростить технологический процесс и оснастку для восстановления валов, полностью исключить сварочно-термическое воздействие на вал, отказаться от шлифования и полирования восстановленных валов, в 4...5 раз сократить расход металла и в 3 раза повысить производительность процесса по сравнению с наплавкой. Метод успешно апробирован при восстановлении чугунных валов двигателей ЗМЗ-53 и ЗМЗ-24.
4 Проектирование технологического процесса восстановления коленчатого вала
При восстановлении коленчатых валов применяют маршрутную технологию. Примерная схема маршрутов 1...Ш
восстановления стальных коленчатых валов представлена на рисунке 4.22
4.1 Обоснование способов восстановления. Выбор рационального способа восстановления
Известно, что изношенные поверхности деталей могут быть восстановлены, как правило, несколькими способами. Для обеспечения наилучших экономических показателей в каждом конкретном случае необходимо выбрать наиболее рациональный способ восстановления.
Выбор рационального способа восстановления зависит от конструктивно-технологических особенностей детали (формы и размера, материала и термообработки), от условий ее работы (характера нагрузки, рода и вида трения) и величины износа, а также стоимости восстановления.
Для учета всех этих факторов рекомендуется последовательно пользоваться тремя критериями:
- технологическим критерием или критерием применимости;
- технико-экономическим критерием (отношение себестоимости восстановления к коэффициенту долговечности).
Технологический критерий (критерий применимости) учитывает, с одной стороны, особенности подлежащих восстановлению поверхностей деталей, а с другой технологические возможности соответствующих способов восстановления.
На основании технологических характеристик способов восстановления, устанавливаются возможные способы восстановления различных поверхностей детали по технологическому критерию.
После отбора способов, которые могут быть применены для восстановления той или иной изношенной поверхности детали, исходя из технологических соображений, отбирают те из них, которые обеспечивают наибольший межремонтный ресурс этих поверхностей, т.е. удовлетворяют требуемому значению коэффициента долговечности.
Коэффициент долговечности в общем случае является функцией трех других компонентов: коэффициента износостойкости, коэффициента выносливости и коэффициента сцепляемости:
где К И
– коэффициент износостойкости;
Численные значения коэффициентов-аргументов определяются на основании стендовых и эксплуатационных испытаний новых и восстановленных деталей. Коэффициент долговечности численно принимается равным значению того коэффициента, который имеет наименьшую величину. Из числа способов отработанных по технологическому критерию, к дальнейшему анализу принимаются те, которые обеспечивают коэффициент долговечности восстановленных поверхностей не менее 0,8.
При выборе способов восстановления применительно к деталям, не испытывающим в процессе работы значительных динамических и знакопеременных нагрузок, численное значение коэффициента долговечности определяется только численным значением коэффициента износостойкости.
Если установлено, что требуемому значению долговечности для данной поверхности детали удовлетворяют два или несколько способов восстановления, то выбор из них оптимального проводится по технико-экономическому показателю, численно равному отношению себестоимости восстановления к коэффициенту долговечности для этих способов. Окончательному выбору подлежит тот способ, который обеспечивает минимальное значение этого отношения:
где К Д
– коэффициент долговечности восстановленной поверхности;
С В
– себестоимость восстановления соответствующей поверхности, руб.
При обосновании способов восстановления поверхностей значение себестоимости восстановления С В
определяется из выражения
где С У
– удельная себестоимость восстановления, руб./см 2
;
S – площадь восстанавливаемой поверхности, см 2
.
Выберем рациональный способ восстановления шатунных и коренных шеек коленчатого вала.
По групповой номенклатуре деталей коленчатый вал относится к классу деталей круглые стержни. Детали данного класса характеризуются цилиндрической формой при длине, значительно превышающей их диаметр. Материалом для них чаще всего служит углеродистая или высококачественная легированная сталь. Рабочие поверхности подвергают термической или химико-термической наплавкой, наплавкой под слоем флюса, в среде углекислого газа или электроконтактной приваркой ленты.
Рассчитаем стоимость восстановления каждого способа по формуле (3), учитывая , что удельная себестоимость восстановления составляет (руб./см 2
): вибродуговая наплавка – 0,8; наплавка под слоем флюса – 1,2; наплавка в среде углекислого газа – 0,6; электроконтактная приварка ленты – 0,85.
Произведем расчет площадей шеек вала (S Ш
) по формуле ( всего восстановлению подвергают три шейки):
S Ш
= 3,14∙(78,25∙40+88,25∙44,1)=22048,5 мм 2
=220,485 см 2
.
Рассчитываем стоимость для вибродуговой наплавки
Для наплавки в среде углекислого газа
Для электроконтактной приварки ленты
Целесообразность того или иного метода определим из выражения (2).
Для наплавки в среде углекислого газа
Для электроконтактной приварки ленты
Из сделанных расчетов видно, что самыми целесообразными методами восстановления коренных и шатунных шеек коленчатого вала будут наплавка в среде углекислого газа и электроконтактная приварка лентой. При наличии на предприятии оборудования для электроконтактной приварки ленты возможно избежать затрат на приобретение нового оборудования. Поэтому принимаем для восстановления шеек вала электроконтактную приварку ленты. С точки зрения организации производства, чем меньше количество способов, используемых для восстановления различных изнашиваемых поверхностей детали, тем меньше требуется видов оборудования, выше его загрузка, а следовательно, и выше эффективность производства.
4.2 Определение режимов нанесения покрытия, выбор материалов и технологического оборудования, механической обработки и норм времени выполняемых операций
4.2.1 Электроконтактная приварка ленты и напекание порошков.
Для приварки ленты к детали необходимы импульсы сварочного тока следующих параметров (обеспечивающие 6…7 сварных точек на 1см длины сварного шва):
а) для ленты толщиной 0,3 мм амплитуда импульса сварочного тока 14500…15900 А, длительность импульсов тока 0,008…0,009 с;
б) для ленты толщиной 0,4 мм амплитуда импульса сварочного тока 16000…17500 А, длительность импульсов тока 0,0085…0,01 с;
в) для ленты толщиной 0,4 мм, привариваемой в два слоя одновременно, амплитуда импульса тока 18000…19500 А, длительность импульсов тока 0,009…0,011 с.
Усилие сжатия электродов Q СЖ
, Н и сила сварочного I СВ
, А тока имеют следующую зависимость
Силу сварочного тока, А определяют из следующего выражения:
где – коэффициент наплавки, при наплавке постоянным током обратной полярности ( = 11…14 г/А∙ч) принимаем =12 г/А∙ч;
h – толщина наплавленного слоя, мм;
𝜸 – плотность электродной проволоки, 𝜸 = 7,85∙10 -3
г/мм 3
Толщина покрытия h, наносимого на наружные цилиндрические поверхности, мм
Z 1
– припуск на обработку на сторону (Z 1
= 0,1…0,3мм), принимаем Z 1
=0,2;
Z 1
– припуск на механическую обработку после нанесения покрытия,( для электроконтактной приварки 0,2…0,5) принимаем Z 1
= 0,4
где d ПР
– диаметр электродной проволоки, мм ( d ПР
= 0,4 мм).
1000∙V Н
/ 60∙p∙D = 1000∙22/60∙1,1∙78,25 =0,42 мин -1
Оптимальные режимы напекания порошка лежат в пределах: по напряжению 0,87…1,35 В на мм толщины слоя, по давлению 40…60 МПа, по затратам энергии 2,1…3,2 Вт∙ч/г.
Выбираем материал ленты сталь 40Х, твердостью 60 НRС.
Расход на покрытие 1 дм 2
поверхности составит: материала (ленты) 30…35 г, электроэнергии 1…1,1 кВт∙ч.
Для напекания используем порошок марки ПС – 2, твердость слоя 60 НRС.
Таблица 1.2 – Режимы приварки ленты
Основным оборудованием для электроконтактной приварки металлического слоя варки являются установки 011-1-02М, 011-1-06, 011-1-08.
4.2.2 Определение норм времени при выполнении операций
Норма времени Т выполнения операции в общем случае слагается из следующих элементов затрат:
Т Н
= Т ОСН
+ Т ВСП
+ Т ДОП
+ Т ПЗ
/ n = 183 + 10 + 19,3/1 = 212,3 мин.,
где Т ОСН
– основное время, т. е. время, в течении которого происходит изменение размеров, формы, свойств, внешнего вида обрабатываемой детали, мин;
Т ВСП
– вспомогательное время, т. е. время, затрачиваемое на действия, обеспечивающие выполнение основной работы (закрепление и снятие детали со станка, измерение детали и т. д.), мин;
Т ДОП
– дополнительное время, затрачиваемое на организацию и обслуживание рабочего места, перерывы на отдых и естественные надобности исполнителя, мин;
Т ПЗ
– подготовительно-заключительное время, затрачиваемое на получение задания, ознакомление с работой, подготовку рабочего места, наладку оборудования, сдачу изготовленного изделия, мин;
n – количество обрабатываемых деталей в партии, шт.
В технологических картах обычно проставляется штучное время Т ШТ
и подготовительно-заключительное время Т ПЗ
Основное время Т ОСН
для станочных работ, механизированной наплавки, гальванических покрытий определяемся по следующим формулам:
- При механизированной наплавке, газотермическом напылении цилиндрической поверхности
где L– длина наплавляемой поверхности, мм;
n – частота вращения детали, мин -1
;
S – продольная подача наплавочной головки, мм/об.
где n Д
– количество деталей при одной нагрузке ванны;
К В
– коэффициент использования ванн, применяется равным 0,65…0,75.
Вспомогательное время Т ВСП
в зависимости от применяемой технологической оснастки берут в пределах от 2 до 12 мин, дополнительное время Т ДОП
определяется по формуле
Подготовительное – заключительное время Т ПЗ
принимается равным 15…20 мин за партию деталей.
4.3 Технико-экономическое обоснование проекта
Экономическая эффективность восстановления изношенных деталей может быть определена из выражения
где Цн, Цв - цены соответственно новой и восстановленной деталей, руб;
, - остаточная стоимость после эксплуатации соответственно и восстановленной деталей, руб;
Тн, Тв - ресурсы соответственно новой и восстановленной деталей.
Из этой формулы следует, что экономически целесообразно восстанавливать детали, для которых Эв>0. Если принять, что = , а Тв / Тн представить как коэффициент долговечности Кд, восстанавливаемой детали, соотношение цен новой и восстановленной деталей должно удовлетворять выражению
Таким образом, максимальная цена, за которую потребитель предпочтет приобрести восстановленную деталь вместо новой.
Минимальная цена восстановления одной детали
где Сз - заводская себестоимость восстанавливаемой детали, руб.;
П - планируемая балансовая прибыль, руб.
В общем случае заводская себестоимость восстановления детали
где Св - себестоимость устранения дефектов без учета затрат на дополнительную работу детали, руб.;
Дн - себестоимость дополнительных работ, по которым необходимо выплатить, руб.;
Сф - затраты на приспособления рем. фонда, руб.
1. . « Курсовое проектирование по технологии ремонта машин». Учебное пособие- издательство, 2008г.
2. В. В. Курчаткин, Н. Ф. Тельников, К. А. Анисов и др. «Надежность и ремонта машин» - : КОЛОС. 2000г.
3. Бабусенко С. М. «Ремонт тракторов и автомобилей» - М. Агропроиздат. 1987г
4. Авдеев М. В., Воловин Е. Н. «Технология ремонта машин и оборудования» - М. Агропроиздат. 1986г
5. Буянов А. В. «Технологические требования на капитальный ремонт трактора ДТ-75, ДТ-75М» и др М. ГОСНИТИ, 1987.
Название: Назначение и характеристика кривошипно-шатунного механизма двигателя Д–240
Раздел: Рефераты по транспорту
Тип: курсовая работа
Добавлен 22:14:23 03 февраля 2010 Похожие работы
Просмотров: 11480
Комментариев: 14
Оценило: 4 человек
Средний балл: 4
Оценка: неизвестно Скачать
Шлифование под ремонтный размер. Нанесение покрытий наплавкой, электроконтактной приваркой ленты, газотермическим напылением порошковых материалов, металлизацией. Постановка полуколец, пластинирование.
посадочных мест под распределительную шестерню, шкив и маховик
Наплавка, электроконтактная приварка ленты, металлизация.
Углубление резьбы резцом до нормального профиля
Фрезерование под увеличенный размер шпонок, новой шпоночной канавки. Наплавка с последующим фрезерованием шпоночной канавки
посадочного места наружного кольца шарикоподшипника в торце вала
Растачивание посадочного места. Запрессовка втулки
Отверстий под штифты крепления маховика
Развертывание под ремонтный размер; заварка
Растачивание или зенкерование с последующим нарезанием резьбы увеличенного размера; углубление резьбовых отверстий с последующим нарезанием такой же резьбы под удлиненные болты (пробки). Постановка резьбовых спиральных вставок
Скручивание вала (нарушение расположения кривошипов)
Шлифование шеек под ремонтный размер; наплавка шеек с последующей обработкой
Подрезание торца фланца точением или шлифованием
Изгиб вала: до 0,15…0,20 мм до 0,20…1,20 мм
Шлифование под ремонтный размер. Разделка трещин с помощью абразивного инструмента, заварка
Приварка ленты на детали типа «вал»
Ширина рабочей части электродов, мм
Срочная помощь учащимся в написании различных работ. Бесплатные корректировки! Круглосуточная поддержка! Узнай стоимость твоей работы на сайте 64362.ru
Привет студентам) если возникают трудности с любой работой (от реферата и контрольных до диплома), можете обратиться на FAST-REFERAT.RU , я там обычно заказываю, все качественно и в срок) в любом случае попробуйте, за спрос денег не берут)
Да, но только в случае крайней необходимости.
Курсовая работа: Назначение и характеристика кривошипно-шатунного механизма двигателя Д–240
Курсовая Работа На Тему Особенности Иерархии Семейных Ценностей
Реферат: Airplanes How They Work Essay Research Paper
Данко Аргумент К Сочинению
Курсовая Работа Титульник
Курсовая работа: Составление водных балансов
Реферат: Власть и бюрократия в России опыт социологического исследования
Контрольная работа: Психология делового общения, его структура
Реферат по теме Гидродинамическое оборудование для интенсификации технологических процессов нефтепереработки
Курсовая работа по теме Исследование механизмов оппозитного двигателя мотоцикла
Патриотизм–источник духовных сил воина
Контрольная работа по теме Понятие, структура, нормы трудового права
Реферат: Сотовая связь 2
Уполномоченный По Правам Человека Курсовая Работа Скачать
Мой Любимый Овощ Огурец 3 Класс Сочинение
Курсовая Работа На Тему Движение Ихэтуаней В Цинской Империи
Реферат Ядерные Катастрофы
Курсовая работа по теме Вопросы регулирования труда несовершеннолетних
Реферат: Русская религиозная философия конца ХIX- начала XX вв (Соловьев, Бердяев, Розанов, Булгаков). Скачать бесплатно и без регистрации
Реферат по теме Победа в октябрьской революции 1917г. Всероссийский съезд советов
Реферат: Hamlet Madness Essay Research Paper Hamlets Unknown
Доклад: Успехи вычислительных наук
Реферат: Проблема движения
Реферат: Камп'ютэрная індустрыя ў ЗША