Key Elements When Selecting A Cutting Tool
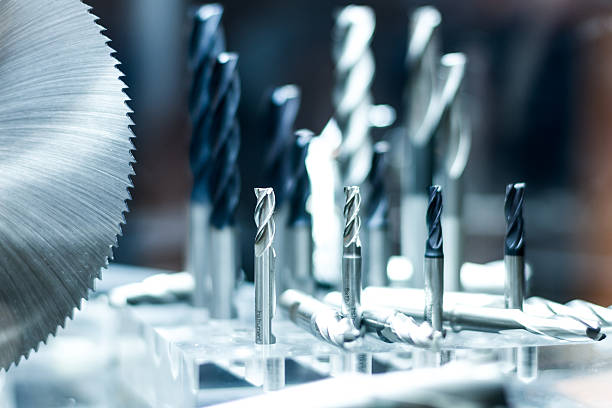
When choosing a cutting tool, you need to consider the material's properties as well as how it will cut the material. Here we will go over the K quality chemical stability, side cutting edge angle, and other considerations.
A cutting tool that is as good similar to pencil grinders and straight grinders can help reduce time and cost and provide high-quality outcomes. Listed below are some essential aspects to consider when choosing a cutting tool. Ask your machine shop about special equipment in case you're uncertain about what you want. Look at this website to find out a useful reference on pcd mill bits.
1. Material Property
Material properties are essential for machining processes of all kinds. The tools, in contrast to knives, must be able to withstand temperatures above 100°C without loosing their cutting edge. Also, they need to resist abrasion, adhesion as well as thermal conductivity.
These factors are crucial for an optimal performance of cutting tools. This article will discuss the characteristics of materials to understand the use of as well as the lifespan of cutting equipment.
Cutting tool life and speed is crucial to the manufacturing procedure. The life of the cutting tool is influenced by several factors, including feed rate, tool geometry and wear on the tool. These factors will impact tool performance and prolong the life of your tool.
An effective cutting tool can be used for a long time and will last through hundred of thousands cuts. The life of any cutting device will be determined by the rate at which it is able to cut different substances. Cutting equipment must be durable and have high cutting rates. You must take note of cutting speed as well as feed rates before buying a tool.
2. K Factor
The K-factor of cutting tools defines the design that the edge of cutting. The radius of the cutting edge is a function of a variety of factors, such as the materials used, the machining procedure, as well as the kind of layer being used.
It is assessed based on cutting speed which are about 35 milliseconds. The measurement area along the cutting edge can be seen in Fig. 1. Additionally, the dimensions of the Sa and Sy affect the force load and heat load.
To measure the K factor of cutting instruments, a device is composed of steel as well as alumina and an abrasive. Its K factor is influenced by the length of the contact as well as the angle g. As the rake angle grows, the objective roughness function also increases.
The more roughness is the objective function, the more complex the materials are. An increase in the K factor indicates that the cutting tool is not functioning optimally.
3. Chemical Stability
Cut-off tools that are made of cubic boron Nitride (CBN) are among the most complex materials. They are also high-temperature resistant and possess excellent thermal stability. They can be classified as low-c-BN or high-c BN. A low-cBN model has no CBN while the high-cBN tools have 75-95 vol% of boron-nitride with metal binder.
Although greasy oil is the most used cutting fluid, the other characteristics are not outstanding. They're also costly and emit a significant amount of smoke which makes them unsuitable for modern production. The EP additives and mineral oils can be blended to produce greasy oils low viscosity. The result is good lubricity and extended tool life.
4. Side Cutting Edge Angle
Back rake angles define the angle of a cutting edge. It's the angle between the tool's face with a perpendicular plane taken from the base. The point of the tool is positive when the slope is down, however, it is negative when the slope is upwards.
The back rake is usually between 5 to 15 degrees. It's crucial to be aware of this angle when you are designing or fabricating an instrument.
The rake of a cutting tool is determined by the angle formed between the face of the tool and the line that runs parallel to the base of the tool. The angle decreases friction between the tool and workpiece, which results in a thinner and better chips.
Positive angle rake angles weaken the strength of the cutting edge segment and decrease the heat conduction capability of the tool. A positive rake angle is more suitable for alloys made of tough metals. Negative rake angle is preferred for soft or weak materials.
5. The High Yield at Operating Temperature
The high yield strength is among of the best-known characteristics of HSS tools. However, in this type of cutting device, the edge is loaded near the limits of yield strength, which causes severe adhesive wear.
Cutting with materials that are chemically aggressive will increase this wear. HSS tools are also susceptible to having a sharp edge due to friction. This article examines the factors which affect the yield of cutting equipment.
The operating temperature of a tool is the primary element that decides on the amount of temperature produced by the cutting device. The maximum temperature of the cutting device increases with increasing cutting speed because the temperature of the work material is influenced by the degree of heat entering the tool.
The impact of this can be seen most clearly in the case of the cutting process that is intermittent. The operating temperature can play a significant role in the lifespan of a tool and its quality. The tool must be capable of cutting at a specific temperature in order for a longer life span and reduce heat production.
6. Tool Material
High-temperature tool hardness determines the capacity of a material's materials to resist the heat, prevent plastic deformation and keep its toughness, even when temperatures are extremely high. This also impacts wear resistance.
The more stable thermally an item is, the better the chance it has to stand up to the cutting process. The higher it's thermal conductivity the lower its temperature when cutting. Selecting a material that is able to be able to withstand cutting at high speeds is crucial.
For industrial use The quality of the cutting tools is crucial. The cutting tool's material is crucial in industrial processes.
Final Said Words
When selecting the best tools and materials, the manufacturer will reduce the amount of scrap used, boost production, and increase the quality of parts. This ensures longevity and success for its processes. In order to choose the best tool material suitable for the specific cutting process, the manufacturer should first establish the specific needs.