Испытания смонтированного оборудования трубопроводов. Курсовая работа (п). Неопределено.
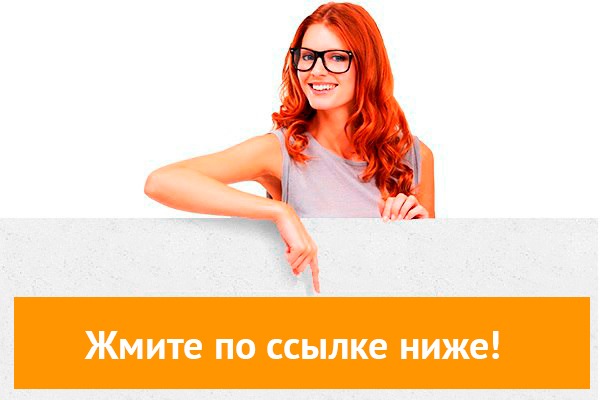
⚡ 👉🏻👉🏻👉🏻 ИНФОРМАЦИЯ ДОСТУПНА ЗДЕСЬ ЖМИТЕ 👈🏻👈🏻👈🏻
Вы можете узнать стоимость помощи в написании студенческой работы.
Помощь в написании работы, которую точно примут!
Похожие работы на - Испытания смонтированного оборудования трубопроводов
Скачать Скачать документ
Информация о работе Информация о работе
Скачать Скачать документ
Информация о работе Информация о работе
Скачать Скачать документ
Информация о работе Информация о работе
Скачать Скачать документ
Информация о работе Информация о работе
Скачать Скачать документ
Информация о работе Информация о работе
Скачать Скачать документ
Информация о работе Информация о работе
Нужна качественная работа без плагиата?
Не нашел материал для своей работы?
Поможем написать качественную работу Без плагиата!
2. Испытания смонтированного
оборудования трубопроводов:
2.1. Подготовка к испытаниям и приёмка смонтированных трубопроводов.
2.2 Гидравлическое испытание стальных
трубопроводов.
2.3 Пневматическое испытание
трубопроводов.
2.4. Промывка и продувка
трубопроводов.
2.5. Приёмно-сдаточная
производственная документация.
3. Методы неразрушающего контроля
качества сварных соединений.
4. Охрана труда при изготовлении и
монтаже трубопроводов:
4.1. Сварочные работы и термическая
резка.
4.2. Монтаж и испытание
трубопроводов.
Изготовление и монтаж
технологических трубопроводов в настоящее время имеет огромное значение в промышленности.
Такого рода работы имеют место при строительстве предприятий нефтяной,
химической, пищевой, металлургической промышленности, а также объектов по
производству минеральных удобрений.
В общем объёме монтажных
работ стоимость монтажа технологических трубопроводов достигает 65% при
строительстве предприятий нефтяной и нефтехимической промышленности, 40% м –
химической и пищевой, 25% – металлургической.
Технологические
трубопроводы работают в разнообразных условиях, находятся под воздействием
значительных давлений и высоких температур, подвергаются коррозии и
претерпевают периодические охлаждения и нагревы. Их конструкция в связи с
расширением единичной мощности строящихся объектов год от года делается всё
более сложной за счёт увеличения рабочих параметров транспортируемого вещества
и роста диаметров трубопроводов.
Для сооружения
технологических трубопроводов, особенно в химической и пищевой промышленности,
всё шире начали использовать полимерные материалы. Увеличение объёмов и области
применения указанных труб объясняется их высокой коррозионной стойкостью,
меньшей массой, технологичностью обработки и сварки, низкой теплопроводностью
и, как следствие, меньшими затратами на теплоизоляцию.
Всё это требует от
монтажников более глубоких знаний, чёткого соблюдения требований применения
разнообразных материалов, выполнения правил и специальных технологических
требований по изготовлению и монтажу трубопроводов.
В последние годы в
широких масштабах внедряются индустриальные методы производства трубопроводных
работ, что обеспечивает на 40% повышение производительности труда и в 3-4 раза
снижает объём работ, выполняемых непосредственно на монтажной площадке, при
этом сроки монтажа трубопроводов сокращаются в три раза. Сущность
индустриализации трубопроводных работ заключается в перенесении всех
трубозаготовительных работ в заводские условия, имея в виду превратить
строительное производство в комплексно-механизированный процесс монтажа
объектов из готовых узлов и блоков заводского изготовления.
Испытания
смонтированного оборудования трубопроводов.
Подготовка
к испытаниям и приёмка смонтированных трубопроводов.
Технологические
трубопроводы сдают в эксплуатацию, как правило, одновременно с технологическим
оборудованием, к которым они относятся после окончания работ по их монтажу.
Исключением могут служить межцеховые трубопроводы, обслуживающие несколько
объектов или установок, которые сдают в эксплуатацию самостоятельно по
окончании всех относящихся к ним монтажных работ. Окончанием работ по монтажу
трубопроводов и оборудования следует считать завершение индивидуальных
испытаний и подписания рабочей комиссией акта их приёмки. Порядок и сроки
проведения индивидуальных испытаний и обеспечивающих их пусконаладочных работ
должны быть установлены графиками, согласованными монтажной и пусконаладочной
организациями, генподрядчиком, заказчиком и другими организациями, участвующими
в выполнении строительно-монтажных работ.
К индивидуальным
испытаниям трубопроводов относят их испытание на прочность и герметичность.
Трубопроводы, транспортирующие горючие, токсичные и сжиженные газы, подвергают
также (в период пусконаладочных работ) дополнительным испытаниям на плотность с
определением падения давления во время испытания. При испытании на прочность в
трубопроводе создают рабочее давление, при котором производят осмотр и
обстукивание с целью выявления неплотности системы в виде сквозных трещин,
отверстий и т. д. При испытании на плотность в трубопроводе создают рабочее давление,
которое выдерживают не менее 12ч. При этом по манометру определяют величину
падения давления за время испытания, по которой судят о плотности системы. Этот
вид испытания позволяет выявить мельчайшие неплотности трубопровода.
При испытаниях на прочность
и герметичность давление измеряют двумя манометрами, один из которых
контрольный. Манометры должны иметь класс точности не ниже 1,5 (ГОСТ 8625-77Е),
диаметр корпуса не менее 150мм и шкалу на номинальное давление около ¾
измеряемого давления. Цена деления шкалы термометров, применяемых при
пневматическом испытании, должна быть не более 0,1 о С.
При подготовке к
испытанию разрабатывают схему трубопровода, на которой указывают места
подключения временных трубопроводов для подачи воды или воздуха, установки
опрессовочных агрегатов, врезки спускных линий, установки воздушников и
временных заглушек, а также определяют порядок и последовательность заполнения
трубопроводов и их опорожнения. Испытываемый трубопровод отключают от
оборудования и неиспытываемых участков трубопроводов инвентарными заглушками, а
в отдельных случаях применяют приварные заглушки и днища. Использование для
этой цели установленной на трубопроводе запорной арматуры не допускается. Для
герметизации гладких концов испытываемых трубопроводов применяют инвентарные
заглушки. Для испытаний трубопроводов с D у =80…700мм на давление до 2,5 Мпа и
спользуют инвентарныю заглушку с круглым резиновым кольцом. При завинчивании
гаек диски подтягиваются один к другому и своими конусами разжимают манжету,
которая плотно прилегает к стенке трубы, обеспечивая полную герметичность. Воду
подают через штуцер. Для предохранения от выдавливания заглушек из труб
устанавливают 3-4 ( в зависимости от диаметра трубы) упорные струбцины. Для
испытания трубопроводов с D у =100…1000мм на давление до 2,5 МПа
применяют инвентарные заглушки с конусным или резиновым кольцом. Их
отличительная особенность состоит в наличии разрезной цанги, которая упирается
в стенки трубы и предотвращает выдавливание заглушки под действием внутреннего
давления жидкости. Для герметизации концов трубопроводов с фланцами применяют
винтовые и межфланцевые заглушки.
Испытанию следуют по
возможности подвергать всю линию трубопровода. Разделение (в случае
необходимости) трубопроводов на участки производит монтажная организация, если
отсутствуют соответствующие указания в рабочей документации. Перед испытанием
трубопроводов производят проверку законченности всех монтажных работ,
выполненных в соответствии с проектом, а также готовности к проведению
испытаний, при этом проверяют:
·
правильность
выполнения всех монтажных работ и их соответствие проекту, включая
термообработку и контроль качества сварки;
·
соответствие
заданных уклонов трубопроводов и типов установленной арматуры;
·
правильность
монтажа арматуры и дистанционных приводов к ней, легкость открывания и
закрывания арматуры;
·
законченность и
правильность расположения и установки дренажей, воздушников, сливных линий,
штуцеров и диафрагм;
·
отсутствие
защемления трубопроводов в опорах и строительных конструкциях, перекрытиях и
стенах;
·
наличие и
соответствие проекту расстояний между параллельно проложенными трубопроводами,
между трубопроводами и строительными конструкциями;
·
наличие
контрольно-измерительных приборов и автоматики;
·
наличие площадок
и лестниц для обслуживания арматуры, расположенной в труднодоступных местах;
·
соответствие
проекту типов опор и подвесок, мест их расположения и правильность их установки
и закрепления;
·
комплектность и
правильность оформления монтажной механической документации.
Проверка производится
представителями монтажной организации и заказчика. После устранения выявленных
недоделок монтажная организация должна получить от заказчика письменное
разрешение на проведение испытаний трубопровода.
Трубопроводы пара горячей
воды (трубопроводы 1-й категории с D у > 70мм,
а также 2-й и 3-й категории с D у > 100мм) до пуска их в
эксплуатацию подлежат техническому освидетельствованию, которое заключается в
проверке монтажной технической документации, наружном осмотре и проведении гидравлического
испытания. Техническое освидетельствование проводится инспектором местного
органа Госгортехнадзора.
Испытания трубопроводов
на прочность и герметичность обычно производят гидравлическим или
пневматическим способом, а испытание на плотность – только пневматическим.
Пневматический способ допускают в следующих случаях: когда опорные конструкции
или газопровод не рассчитаны на заполнение его водой; если температура воздуха
отрицательная и отсутствуют средства, предотвращающие замораживание системы. Пневматические
испытания на прочность не допускаются для трубопроводов, расположенных в
действующих цехах; расположенных на эстакадах, в каналах и лотках рядом с
действующими трубопроводами; при давлении более 0,4 МПа, если на трубопроводе
установлена арматура из серого чугуна.
Вид и способы испытаний,
продолжительность и оценку результатов испытаний принимают в соответствии с
рабочей документацией. При отсутствии этих указаний способ испытаний
(гидравлический или пневматический) выбирает монтажная организация и
согласовывает с заказчиком, а вид и значения испытательных давлений принимают в
соответствии с правилами Гостехнадзора (табл.1).
Смонтированные
трубопроводы, как правило, испытывают до их изоляции. Разрешается проводить
испытания трубопроводов из бесшовных труб или заранее изготовленных и
испытанных блоков независимо от вида труб с нанесенной тепловой или
антикоррозионной изоляцией при условии, что сварные монтажные стыки и фланцевые
соединения оставляют неизолированными и доступными для осмотра. Трубопроводы
пара и горячей воды испытывают с нанесенной изоляцией (кроме сварных и
фланцевых стыков) после получения разрешения местного органа Госгортехнадзора.
В случае выявления в процессе испытания трубопроводов дефектов, допущенных при
производстве монтажных работ, испытание должно быть повторено после устранения
дефектов.
Табл.1. Испытательные
давления для стальных трубопроводов общего назначения.
Трубопроводы с рабочим
давлением до 0,5МПа при температуре среды до 400 о С
Трубопроводы с рабочим
давлением до 0,5МПа и выше при температуре среды до 400 о С
Трубопроводы с рабочей
температурой среды выше 400 о С независимо от рабочего давления
Трубопроводы для пара и
горячей воды*
Трубопроводы для
горючих, токсичных и сжиженных газов с рабочим избыточным давлением, МПа:
Гидравлическое
испытание стальных трубопроводов.
Гидравлическое испытание
трубопроводов, как правило, проводят одновременно на прочность и герметичность
при положительной температуре окружающего воздуха, обычно не ниже 5 о С.
Процесс гидравлического
испытания трубопровода состоит из следующих операций:
· заполнение трубопровода водой, при
этом все воздушники держат открытыми до появления в них воды, что
свидетельствует о полном вытеснении воздуха из трубопроводов;
· осмотр трубопровода при заполнении
водой с целью выявления течи через трещины и неплотности в соединениях;
· спуск воды и устранение выявленных
дефектов;
· вторичное заполнение трубопровода водой
и постепенный подъем давления до рабочего, предусмотренного рабочей
документацией и повторный осмотр трубопровода;
· подъем давления до испытательного и
выдержка при этом давлении в течение 5 мин (испытание на прочность);
· снижение давления до рабочего и
окончательный осмотр трубопровода с легким обстукиванием сварных швов на
расстоянии 15…20мм по обе стороны шва молотком массой не более 1,5кг (испытание
на герметичность).
Время проведения
испытания на герметичность при отсутствии указаний в рабочей документации
должно определяться продолжительностью осмотра трубопровода. Трубопровод
считается выдержавшим гидравлическое испытание на прочность и герметичность,
если во время испытаний не произошло падения давления по манометру и не
обнаружено течи и запотевания в сварных швах, фланцевых соединениях, на
корпусах и сальниках арматуры, на поверхности труб и деталей трубопроводов, нет
признаков разрывов и видимых остаточных деформаций. Дефекты устраняют только
после снижения давления в трубопроводе до атмосферного. Обнаруженные дефекты
сварных швов подчеканкой исправлять не допускается. Все участки сварных швов,
подвергавшиеся исправлению, проверяют радиографическими методами контроля.
Трубы и детали с дефектными продольными швами заменяют новыми. При обнаружении
течи в разъемных фланцевых соединениях их разбирают, определяют причину течи и
устраняют ее.
После устранения дефектов
(повреждений или неплотностей), обнаруженных во время окончательного осмотра
трубопровода, испытания повторяются, включая этап подъема давления до
испытательного на прочность, выдержку под ним, снижение до рабочего, повторный
осмотр. По окончании испытания воздушники должны быть обязательно открыты, и
трубопровод полностью освобожден от воды.
Для создания
испытательного давления в трубопроводе применяют наполнительно-опрессовочные
насосы (табл.2), используют действующую водопроводную сеть или эксплуатационные
насосы. При испытании в летний период нельзя оставлять трубопровод длительное
время заполненным водой, так как от нагрева солнечными лучами или окружающим
воздухом давление в трубопроводе может повышаться. В осенне-зимний период, а
при соответствующих технических требованиях и в другие времена года
трубопроводы после их испытания и опорожнения должны быть продуты воздухом.
Табл.2. Технические
характеристики насосов для гидравлического испытания трубопроводов.
Максимальное рабочее давление
жидкости, МПа
Примечание: В числителе
даны характеристики при низком давлении, в знаменателе – при высоком.
При необходимости
проведения испытания трубопровода при отрицательных температурах окружающего
воздуха должны быть приняты меры против замерзания воды в трубопроводе,
обеспечивающие надежное освобождение его от воды, а именно:
·
предварительный
прогрев трубопровода паром или прокачиванием горячей воды и испытание его
горячей водой с температурой не выше 60 о С (все дренажные штуцеры и
спускные линии должны быть при этом утеплены);
·
испытание
трубопровода с применением водных растворов, имеющих температуру замерзания
ниже 0 о С, например раствора хлористого кальция, с последующей
промывкой трубопровода горячей водой и продувкой воздухом.
Температура замерзания
раствора хлористого кальция:
Содержание хлористого кальция в
растворе, %
Пневматическое
испытание трубопроводов.
Пневматическое испытание
трубопроводов проводят для проверки их прочности. Испытание на плотность с
определением падения давления производят только после предварительного их
испытания на прочность любым способом. При пневматическом испытании на
прочность предельное давление и длина испытываемого участка трубопровода при
наземной прокладке не должна превышать величин, указанных в следующей таблице:
Предельное испытательное давление,
МПа
Наибольшая длина участка
трубопровода, м
Пневматическое испытание
производят воздухом или инертным газом, для чего используют компрессоры или
воздухогазонадувки. Если испытательное давление превышает давление воздуха или
газа в действующей сети, можно заполнять испытываемый трубопровод от
действующей сети, а подъем давления до требуемого производить от передвижного
компрессора. В процессе заполнения трубопровода воздухом или инертным газом и
подъема давления необходимо постоянно наблюдать за испытываемым трубопроводом.
Утечки обнаруживают по звуку. При обнаружении значительных утечек во фланцевых
соединениях или сальниках арматуры испытание прекращают, снижают до атмосферного
и устраняют обнаруженные дефекты. Обстукивание молотком трубопроводов, находящихся
под давлением, при пневматическом испытании не допускается.
До начала пневматических
испытаний должна быть разработана инструкция по безопасному ведению
испытательных работ в конкретных условиях, с которой должны быть ознакомлены
все участники испытания.
При пневматическом
испытании давление в трубопроводе поднимают постепенно с осмотром на следующих
ступенях: при достижении 60% испытательного давления – для трубопроводов,
эксплуатируемых при рабочем давлении до 0,2МПа, и при достижении 30 и 60%
испытательного давления – для трубопроводов, эксплуатируемых при рабочем
давлении 0,2МПа и свыше. На время осмотра подъем давления прекращается.
Испытательное давление выдерживают в течение 5мин, после чего его снижают до
рабочего и окончательно осматривают трубопровод, при этом не допускается
увеличения давления. Если пневматическому испытанию предшествовало
гидравлическое, трубопровод следует продуть воздухом для удаления оставшейся
воды.
При испытании выявляют
дефекты обмазкой соединений трубопровода мыльным раствором (40г мыла или
мыльного порошка на 2л воды); чтобы раствор не высыхал, в него добавляют
несколько капель глицерина. Сварные стыки и разъемные соединения обмазывают с
помощью кисти, а в недоступных местах – с помощью краскораспылителя и следят за
появлением пузырей. За соединениями, недоступными для визуального осмотра,
наблюдают через небольшие зеркала. При испытании трубопроводов в зимнее время
при температуре окружающего воздуха до –25 о С мыльные растворы
следует приготовлять на незамерзающих растворителях (460г глицерина, 515г воды
и 35г мыла). Результаты пневматического испытания считаются
удовлетворительными, если за время испытания в сварных швах, фланцевых
соединениях и сальниках не обнаружено утечек и пропусков.
Трубопроводы, по которым
транспортируют сильнодействующие ядовитые вещества и другие продукты с
токсическими свойствами (сжиженные нефтяные газы, горючие и активные газы, а
также легковоспламеняющиеся и горючие жидкости, транспортируемые при
температурах, превышающих температуру их кипения), как правило, подвергают
дополнительному испытанию на плотность, определяя падение давления за время
испытания (об этом делается указание в проекте). Пневматическое испытание
внутрицеховых трубопроводов с определением падения давления производят в процессе
комплексного опробования объекта совместно с оборудованием после завершения
всех монтажных работ (испытаний на прочность и герметичность, промывки,
продувки, установки измерительных диафрагм). Межцеховые трубопроводы подвергают
дополнительному испытанию на плотность отдельного оборудования. Длительность
дополнительного испытания на плотность с определением падения давления за время
испытания принимается не менее 12ч. Утечка воздуха (газа) в трубопроводе за это
время:
100 (1 – P кон Т нач /P нач Т кон )
Где Р - утечка за 1ч,%; Р
нач и Р кон – сумма манометрического и барометрического
давления соответственно в начале и конце испытания, МПа; Т нач и Т кон –
абсолютная температура воздуха (газа) соответственно в начале и конце
испытания, о С; n –
продолжительность испытания трубопровода, ч.
Трубопровод признают
выдержавшим дополнительное испытание на плотность, если процент падения давления
(от испытательного) составляет: для трубопроводов внутрицеховых,
транспортирующих токсичные продукты, не более 0,05%, а межцеховых с D у < 250мм – не более 0,1%; для трубопроводов
внутрицеховых, транспортирующих взрывоопасные, легковоспламеняющиеся, горючие и
сжиженные газы – не более 0,1%, а межцеховые с D у 250мм – не более 0,2%. При испытании межцеховых трубопроводов
с D у > 250мм нормы падения давления
определяют умножением приведенных выше цифр на коэффициент К=250/D в (D в – внутренний диаметр трубопровода, мм).
Если испытываемый
трубопровод состоит из участков труб различных диаметров, средний внутренний
диаметр трубопровода определяют по формуле:
D 2 в1 L 1 + D 2 в2 L 2 +…+ D 2 в n L n
D в 1 L 1 + D в 2 L 2 +…+ D в n L n
где D в1 , D в2 , Dвn – внутренние диаметры участка
трубопровода, мм;L 1 , L 2 ,…,Ln –длины
соответствующих участков трубопровода, мм.
Давление во время
испытания на плотность замеряют после выравнивания температур внутри
трубопровода, для чего в начале и конце испытываемого участка устанавливают
термометры. При пневматических испытаниях трубопроводов с определением падения
давления применяют пружинные манометры с диаметром корпуса не менее 160мм, классом
точности 0,5 или 1, предназначенные для работы в эксплуатационных условиях при
температуре окружающей среды от –50 до 60 о С, а при испытательных
давлениях ниже 0,1МПа – ртутные или водяные манометры. При наблюдении за
изменением барометрического давления используют данные метеорологических
станций или показания барометров.
Во время проведения
пневматических испытаний на прочность как внутри помещения, так и снаружи,
необходимо ограничить охраняемую зону и отметить ее флажками. Минимальное
расстояние от испытываемого трубопровода до границы зоны в любом направлении
должно составлять при надземной прокладке 25, а при подземной 10м. Для
наблюдения за охраняемой зоной устанавливают контрольные посты. Во время
подъема давления в трубопроводе и при испытании его на прочность должно быть
исключено пребывание людей в охраняемой зоне. Компрессор, используемый при
проведении испытаний, должен находиться вне охраняемой зоны. Подводящую линию
от компрессора к испытываемому трубопроводу предварительно проверяют
гидравлическим способом на прочность. Осмотр трубопровода разрешается лишь
после того, как испытательное давление снижено до рабочего.
Промывку или продувку
трубопроводов производят по окончании монтажа и испытания трубопроводов с целью
очистки внутренней поверхности от механических загрязнений или удаления влаги и
выполняют обычно в период пусконаладочных работ. Эти операции производят
согласно разработанным схемам, предусматривающим их технологическую
последовательность. О выполнении промывки и продувки составляются акты.
Промываемый или
продуваемый трубопровод должен быть отделен от других трубопроводов заглушками.
Промывать трубопроводы следует достаточно интенсивно, обеспечивая скорость воды
в трубопроводе 1…1,5м/с, до появления чистой воды из выходного патрубка или
устройства, диаметр которых должен быть не менее 50% сечения промываемого
трубопровода. Во время промывки все запорные органы на трубопроводах полностью
открывают, а регулирующие и обратные клапаны вынимают.
На всасывающем патрубке
трубопровода устанавливают временный фильтр или конусную сетку с размерами
ячейки или диаметром отверстий 4мм. Размеры конуса и число отверстий выбирают с
таким расчетом, чтобы суммарная площадь отверстий (живое сечение) была в 2…3
раза больше площади поперечного сечения всасывающей трубы.
Во время промывки
обстукивают такие участки трубопровода, где возможна задержка грязи (переходы,
отводы и др.). Обычно промывку ведут в 3–4 этапа с перерывами. Каждый этап
промывки продолжают 10…15мин. Продувают трубопроводы воздухом под давлением,
равным рабочему, но не более 4МПа. Продолжительность продувки, если нет особых
указаний в проекте, составляет не менее 10мин.
После окончания промывки
или продувки восстанавливают проектную схему трубопровода, демонтируют
временный промывочный трубопровод, осматривают и очищают арматуру,
установленную на спускных линиях и тупиках. Монтажные шайбы, временно
установленные в контрольно-измерительных приборах, вынимают и заменяют их
диафрагмами.
Приемно-сдаточная
производственная документация.
Приемно-сдаточную
производственную документацию по монтажу технологических трубопроводов
оформляют и комплектуют по линиям. Производственная документация на
трубопроводы пара и горячей воды должна соответствовать правилам и нормам
Госпроматомнадзора.
При сдаче в эксплуатацию
технологических трубопроводов на Р у до 10МПа монтажная организация
должна передать рабочей комиссии следующую производственную документацию: акт
освидетельствования скрытых работ при монтаже трубопроводов (укладку футляров,
очистку внутренней поверхности, предварительную растяжку компенсаторов,
промывку и продувку и др.); журнал сварочных работ (только для трубопроводов I и II категории); список сварщиков и термистов; журнал учета и
проверки качества контрольных стыков (только для трубопроводов I и II категории); журнал термической обработки; исполнительные
чертежи трубопроводов (только для трубопроводов I категории). В качестве исполнительных чертежей трубопроводов
должны, как правило, использоваться аксонометрические (деталировочные) чертежи
этих трубопроводов с внесением в них фактических данных и подписанных
ответственным представителем монтажной организации.
При производстве трубопроводных
работ монтажная организация совместно с другими участниками строительства при
необходимости составляет и оформляет оперативную документацию, в которую входят:
журнал учета качества сварочных материалов и защитных газов для сварки
трубопроводов; протокол проверки внешним осмотром и измерением размеров сварных
соединений; протокол вырезки производственных сварных стыков; список
дефектоскопистов по контролю качества сварных соединений, протокол механических
испытаний и металлографических исследований образцов сварных соединений;
заключение о результатах и журнал радиографического, ультразвукового контроля и
цветной дефектоскопии.
Для регистрации
трубопровода пара и горячей воды монтажная организация представляет в местные
органы Госгортехнадзора: паспорт трубопровода, содержащий данные о его
характеристике, рабочих параметрах, результатах освидетельствования и др.;
свидетельство о качестве изготовления узлов трубопроводов; свидетельство о
качестве монтажа трубопроводов; аксонометрическую схему трубопровода.
Свидетельство о качестве
изготовления узлов и монтажа трубопроводов содержит: сертификаты на металл труб
и всех деталей трубопроводов; паспорта арматуры; сертификаты на применяющиеся
при монтаже электроды; удостоверения и данные о результатах проверки
электросварщиков; денные о результатах испытаний пробных образцов сварных
стыков; журнал термообработки сварных стыков из легированной стали; протокол
испытания сварных стыков неразрушающими методами контроля; журнал измерений
диаметров паропровода для наблюдения за ползучестью металла; журнал фиксации
оси трубопровода; журнал исходных измерений положения паропровода по реперам
термического перемещения.
На аксонометрической
схеме трубопровода, в качестве которой обычно используют исполнительные деталировочные
чертежи линий трубопроводов, должны быть указаны: диаметр и толщина стенки
труб; расположение опор и подвесок, сварных стыков с указанием клейм сварщиков,
выполняющих эти стыки; расположение арматуры, спускных продувочных и дренажных
устройств; нумерация точек для наблюдения за ползучестью. Разрешение на пуск в
эксплуатацию вновь смонтированных трубопроводов, подлежащих освидетельствованию
и регистрации местными органами Госпроматомнадзора, выдается инженером-контролером
Госпроматомнадзора на основании акта приемки трубопровода заказчиком и
произведенного им технического освидетельствования.
Методы
неразрушающего контроля качества сварных соединений.
Рентгеновский контроль.
Рентгеновские лучи обладают свойством проникать через непрозрачные тела. Пронизывая
сварной шов и встречая на своём пути дефекты, они изменяют интенсивность, что
фиксируется на рентгеновской плёнке.
Для просвечивания сварных
швов применяют рентгеновские аппараты типа РУП. Так, аппарат РУП-120-5-1
используют для просвечивания сварных соединений из стали толщиной до 25мм и
лёгких сплавов толщиной до 100мм.
При контроле источник излучения
(рентгеновскую трубку) помещают на определенном расстоянии от шва. С
противоположной стороны шва размещают кассету с рентгеновской пленкой и усиливающими
экранами.
При просвечивании пленку
выдерживают под лучами определенное время, называемое экспозицией. Она зависит
от толщины металла, фокусного расстояния, интенсивности излучения и
чувствительности пленки. Усиливающие экраны служат для уменьшения экспозиции.
Затем пленку вынимают из
кассеты и проявляют. На полученном изображении участка шва степень потемнения
отдельных мест будет неодинаковой. Лучи, попавшие на пленку через дефект,
поглотятся в меньшей степени по сравнению с лучами, прошедшими через плотный
металл, поэтому сварочный дефект на пленке будет выглядеть как более темное
место.
При просвечивании рядом
со швом, со стороны источника излучения, устанавливают дефектометр, который
служит для определения величины дефекта и глубины его нахождения в шве.
Дефектометр – это пластинка, изготовленная из того же материала, что и
просвечиваемый металл. Толщина пластинки должна быть равна усилению шва. На
дефектометре имеются канавки различной глубины. По рентгенограмме величину
дефекта (по высоте) определяют, сравнивая его потемнение с потемнением канавок
дефектометра.
С помощью рентгеновского
контроля можно обнаружить большинство внутренних дефектов: непроваров, пор,
включений, трещин.
Гамма-контроль.
Гамма-лучи, так же как и рентгеновские, представляют собой электромагнитные
волны. Некоторые элементы (уран и др.) обладают свойствами самопроизвольно
испускать лучи. Это явление называется радиоактивностью.
Для
Похожие работы на - Испытания смонтированного оборудования трубопроводов Курсовая работа (п). Неопределено.
Сочинение А Н Радищева Называется
Отчет по практике: Регистрация и учет налогоплательщиков Алтайского края
Практическая Работа Оценка Влияния Температуры
Сочинение Рассуждение Я Добрый Человек 9 Класс
Сочинение На Тему Герой Романа
Дипломная работа по теме Особенности заключения и исполнения договора страхования гражданской ответственности организаций, эк...
Курсовая работа по теме Разработка плана производственно-экономической деятельности железнодорожной станции
Эссе На Тему Мой Любимый Поэт
Государственные Закупки Диссертация
Курсовая работа по теме Современные сигнальные процессоры фирмы Texas Instruments серии TMS320 платформы C5000. Их сравнение по возможностям и быстродействию с сигнальными процессорами фирмы Analog Devices серии TigerSharc
Реферат по теме Cтиль вещания
График Контрольных Работ По Русскому Разумовская
Реферат: Биологический редукционизм: расово-антропологическая школа. Скачать бесплатно и без регистрации
Реферат по теме Водопропускные трубы
Реферат по теме Освободительная война украинского народа 1648–1654 годов
Система Маркетингу Реферат
Реферат: Анализ ликвидности бухгалтерского баланса, краткосрочной дебиторской и кредиторской задолженности. Скачать бесплатно и без регистрации
25.15 8 Контрольная Работа По Информационному Праву
Дипломная работа по теме Создание малого инновационного предприятия
Реферат: Evil And Gender Archetypes In Macbeth Essay
Курсовая работа: Бюджетное финансирование и основные направления его совершенствования в РФ
Контрольная работа: Модернизация электронного термометра
Дипломная работа: Виды, методы и программы налоговых проверок