Help - drill holes are not detected!
GIBcam TeamA call for help reaches the GIBcam team on the support hotline! After the data import including surface check and repair, the component data is sent through the AI algorithm of feature scan in the usual way - but no features are generated for some (seemingly obvious) drill holes.


What's going on here? What happened?
No matter which parameter setting you choose for the feature scan, the result is always the same - this is also logical, because the AI works exactly within the restrictions given to it.
Possibly the surfaces are defective? But all surfaces have been checked - and no defects were found. At least no repairable geometric defects or faulty definition.
This means, however, that the component does not contain any form elements that can be classified as drill holes by the AI ... i.e. the visible drill holes are not drill holes! This is easy to check -> the surfaces of a drill hole must have a constant value in the radius analysis. The result is surprising, the radius value differs by several tenths of a millimetre -> but leads to the objective conclusion that these elements are not drill holes. The differing radius describes an ellipsoid, i.e. a form element that cannot be produced by drilling.
Unless …
Can this be? - Perhaps it is also a design error, e.g. due to incorrect creation of 3D surface geometry. It can happen that inclined circular cylinders are created - i.e. an ellipsoid.
Before proceeding with this analysis result, it is essential to clarify this assumption (i.e. inclined circular cylinders that obviously describe drill hole geometry as an indication of design errors)!
If the assumption is confirmed, the correction should preferably be made on or with the generating CAD system.
If this is not possible, GIBcam offers a solution with the help of which a 'repair' can be carried out by means of a surface approximation. However, the approximation of new circular cylinder surfaces is only a pragmatic solution and does not represent a correct and complete constructive correction of the component geometry!
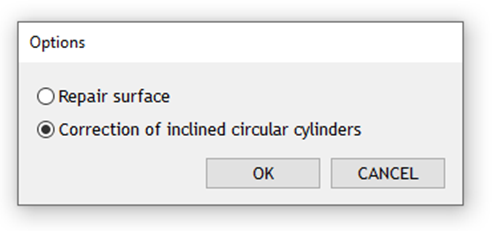
This special method can be done either with the surface repair function when calling up individual surface elements separately or as part of the function for extracting rotational surface geometry.
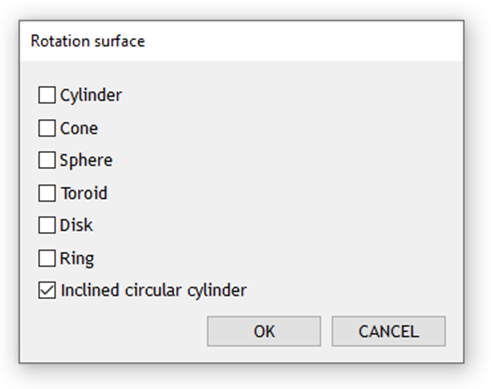


The new surfaces created in this way can be handled by the AI of the feature scan and generate the expected feature ..
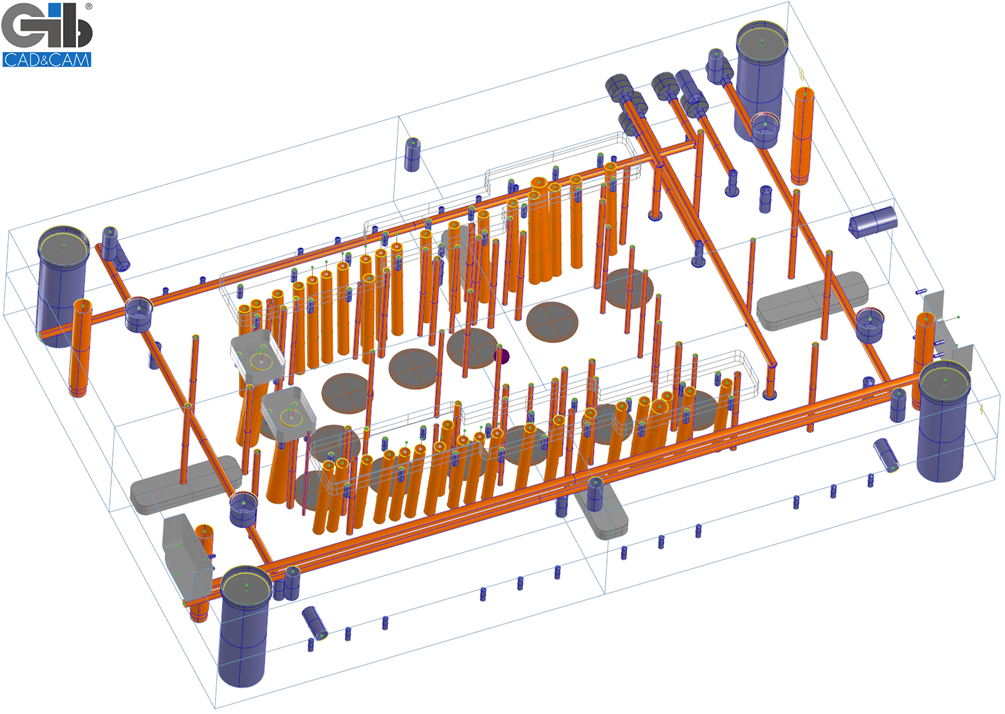