Газообразные топлива. Курсовая работа (т). Химия.
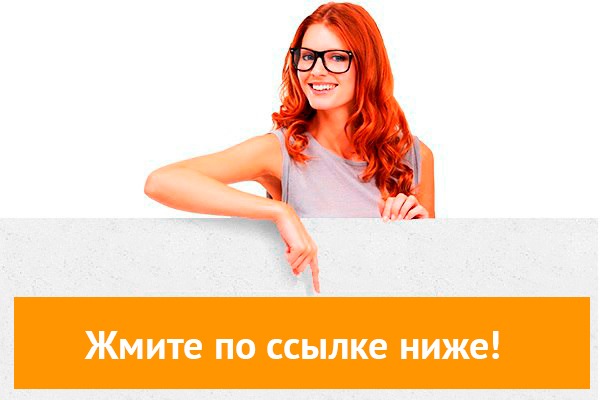
🛑 👉🏻👉🏻👉🏻 ИНФОРМАЦИЯ ДОСТУПНА ЗДЕСЬ ЖМИТЕ 👈🏻👈🏻👈🏻
Вы можете узнать стоимость помощи в написании студенческой работы.
Помощь в написании работы, которую точно примут!
Похожие работы на - Газообразные топлива
Скачать Скачать документ
Информация о работе Информация о работе
Скачать Скачать документ
Информация о работе Информация о работе
Скачать Скачать документ
Информация о работе Информация о работе
Скачать Скачать документ
Информация о работе Информация о работе
Скачать Скачать документ
Информация о работе Информация о работе
Скачать Скачать документ
Информация о работе Информация о работе
Скачать Скачать документ
Информация о работе Информация о работе
Нужна качественная работа без плагиата?
Не нашел материал для своей работы?
Поможем написать качественную работу Без плагиата!
. Классификация и состав
газообразных топлив
. Подготовка газа к фракционированию
(процесс очистки и осушки)
.2 Очистка и осушка газа
короткоцикловой безнагревной адсорбцией
. Разделение газа на фракции на установке
ГФУ
. Получение и применение продуктов
газофракционирования
Нефтеперерабатывающая и нефтехимическая
промышленность является одной из ведущих отраслей тяжелой промышленности. В
последние годы добыча нефти значительно сократилась.
Перед нефтеперерабатывающей промышленностью
поставлена задача повысить эффективность использования нефти, обеспечить
дальнейшее улучшение её переработки.
В настоящее время особая роль отведена
увеличению глубины переработки нефтяного сырья с помощью различных термических
и химических методов, с целью получения из нефти большего количества светлых
нефтепродуктов. Широкое применение в нефтепереработки имеет газ. Газ
применяется как хладагент, топливо.
В топливном балансе, газообразное топливо
занимает существенное место. С каждым годом его потребление возрастает не
только в промышленности, но и в хозяйстве. Газообразное топливо имеет ряд
существенных преимуществ по сравнению с другими видами топлива: оно широко
распространено, дешево, имеются его большие запасы, легко осуществляется
дозировка и регулировка с воздухом. Многие газы обладают высокой тепловой
ценностью. При сгорании они развивают высокую температуру, полностью сгорают с
небольшим коэффициентом избытка воздуха, не содержат коррозионно-агрессивных
веществ. Газообразное топливо очень удобно в использовании: в помещениях
сохраняется чистота, так как при его сгорании не выделяются копоть и смолы, не
остается золы, а продукты сгорания почти не содержат веществ, вредных для
окружающей живой природы. Хранение газообразного топлива централизованно, что
удобно для потребления: не нужны индивидуальные складские помещения,
специальные хранилища. Использование газовых магистралей особенно важно для тех
районов, где нет запасов твердого и жидкого топлива.
Основной недостаток многих видов газообразного
топлива - их высокая взрывоопасность (природные газы, водород, метан). Легкая
утечка горючих газов через мельчайшие неплотности требует внимания и
осторожности при использовании. Те газы, в состав которых входит окись
углерода, сильно ядовиты. Однако соблюдение правил технической и
противопожарной безопасности, а также выполнение рекомендуемых мер, делает
эксплуатацию газовых установок надежной и безопасной.
1.
Классификация и состав газообразных топлив
Газообразные топлива - это в основном смесь
различных газов, таких как метан, этилен, и других углеводородов. Также в
состав газообразного топлива входят оксид углерода, диоксид углерода или
углекислого газа, азот, водород, сероводород, кислород и другие газы, а также
водяные пары.
Все виды газообразного топлива по теплоте
сгорания делят на три группы: 1) низкокалорийные газы (генераторный, смешанный,
доменный, рудничный и др.), выделяющие до 10000 кДж/м³;
2) среднекалорийные (водяной, светильный, коксовый и др.), при их сгорании
выделяется 10000-20000 кДж/м³;
3) высококалорийные - более 20000 кДж/м³,
к их числу относятся различные природные газы газовых месторождений, нефтяные
или попутные газы, добываемые вместе с нефтью из нефтяных скважин, сжиженные
газы, а также различные крекинговые и другие газы, получаемые при переработке
нефти.
Газообразное топливо может быть естественным и
искусственным. К естественным относятся легкие газообразные углеводороды,
улавливаемые при добыче нефти, и природные газы чисто газовых месторождений. По
составу и тепловой ценности природные газы различных месторождений отличаются
незначительно. Их главная составная часть (92-99%) - метан СН4, что и
обусловливает высокую взрывоопасность. Природный газ - самое дешевое топливо,
что делает его чрезвычайно перспективным для использования во многих отраслях
хозяйства. С каждым годом он находит все более широкое применение и в сельском
хозяйстве и для обеспечения различных технологических и бытовых нужд.
Искусственные горючие газы получают при
переработке твердых и жидких топлив (процессы сухой перегонки, коксования,
полукоксования и др.). Наиболее распространены светильный, коксовый, водяной,
смешанный, крекинговый. По тепловой ценности искусственные газы бывают как
низко, так и высококалорийными. Их используют как топливо, а также часто
смешивают с природным для снижения взрывоопасности. Смешивание проводят на
специальных станциях, а к потребителю уже поступает готовый двойной или тройной
газ. Однако необходимо помнить, что газ, поступающий
к потребителю, все равно взрывоопасен, а часто и ядовит (если в нем содержится
окись углерода) и поэтому требует осторожного обращения с ним.
Газовое топливо представляет собой смесь горючих
и негорючих газов. Горючими являются метан, пропан, бутан, этан, водород и
окись углерода; негорючими - азот, углекислый газ и кислород, а также некоторое
количество примесей как горючих, так и негорючих веществ, количество которых
лимитируется ГОСТ 5542-78.
С помощью приборов, называемых
газоанализаторами, определяют состав газообразного топлива.
В состав сухого газообразного топлива
входят:
CH4+ C2H4+ CO2 + H2+ H2S + CmHn+ N2
+ O2+… =
100.
Метан (СН4) - основная составляющая часть многих
природных газов. При сгорании 1 м³ метана
выделяется 35 800 кДж теплоты. Метана в природных газах может содержаться до
93-98%.
Этилен (С2Н4) - при сгорании 1 м³
этилена
выделяется 59000 кДж теплоты. В газах может содержаться небольшое его
количество.
Водород (Н2) - при сгорании 1 м³
водорода
выделяется 10800 кДж теплоты. Многие горючие газы, кроме коксового, содержат
относительно небольшое количество водорода. Однако в коксовом газе его
содержание может достигнуть 50-60%.
Пропан (С3Н8), бутан (С4Н10) - при горении этих
углеводородов выделяется большее количество теплоты, чем при сгорании этилена,
но в горючих газах их содержание незначительно.
Оксид углерода (СО) - при сгорании 1 м³
этого
газа выделяется 12770 кДж теплоты. Оксид углерода - основная горючая
составляющая доменного газа. Этот газ не имеет ни цвета, ни запаха, очень
ядовит.
Сероводород (H2S) - при горении 1 м³
сероводорода
выделяется 23400 кДж теплоты. При наличии в газообразном топливе сероводорода
повышается коррозия металлических частей печи и газопровода. При одновременном
присутствии в газе кислорода и влаги коррозирующее воздействие сероводорода
усиливается. Сероводород - тяжелый газ с неприятным запахом, обладает высокой
токсичностью.
Остальные газы (СО2, N2, О2) и пары воды -
балластные составляющие. Их присутствие в топливе приводит к понижению
температуры его горения. При повышении содержания этих газов снижается
содержание горючих составляющих. Содержание в топливе более 0,5% свободного
кислорода считается опасным по условиям техники безопасности.
Природные газы чисто газовых месторождений
состоят в основном из метана (СН4), относятся к категории сухих (тощих) газов и
характеризуются относительным постоянством состава, в то время как состав газов
газонефтяных месторождений непостоянен и зависит от природы нефти, величины
газового фактора и условий разделения нефтегазовых смесей.
Попутные газы из газовых шапок нефтяной залежи,
как правило, содержат меньше тяжелых углеводородных газов, чем газы, получаемые
из месторождений нефти, в которой они были растворены.
В народном хозяйстве широко применяются
сжиженные углеводородные газы, которые находят применение в сельской местности
и населенных пунктах, удаленных на значительные расстояния от магистральных
газопроводов.
К сжиженным углеводородным газам относятся такие
углеводороды, которые при нормальных условиях находятся в газообразном
состоянии, а при относительно небольшом повышении давления (без снижения
температуры) переходят в жидкое состояние.
Сжиженные газы представляют собой смесь
углеводородов, в основном пропана и бутана, с небольшими примесями более
тяжелых. Источниками их получения являются попутные газы нефтяных и
газоконденсатных месторождений и газы, образующиеся при переработке нефти. При
атмосферных условиях сжиженные газы переходят в газообразное состояние, а при
повышении давления или при снижений температуры превращаются в жидкость. Для
транспортировки и хранения эти газы обычно сжижают, а у потребителей они
используются в газовой фазе.
При снижении давления эти углеводородные
жидкости испаряются и переходят в паровую фазу. Это позволяет перевозить и
хранить сжиженные углеводороды, как жидкости, а контролировать, регулировать и
сжигать газообразные углеводороды, как газы.
Доменный газ получается при выплавке чугуна в
доменных печах как побочный продукт, Процесс образования доменного газа связан
с взаимодействием углерода кокса с дутьем и реакциями восстановления железных
руд. Состав доменного газа зависит от влажности и температуры подогрева дутья,
обогащения его кислородом
Особенностями газообразных углеводородов
являются: высокая плотность, значительно превышающая плотность воздуха;
медленная диффузия в атмосферу, низкие температуры воспламенения, низкие
пределы взрываемости в воздухе, высокий объемный коэффициент расширения жидкой
фазы и другие факторы, которые повышают требования при их
использовании.
Из углеводородных сжиженных газов в качестве
топлива главным образом используются пропан, бутан и их смеси. Соотношение
пропана и бутана в смеси этих газов устанавливается по соглашению между
потребителем и поставщиком газа.
Технический пропан является универсальным
сжиженным газом, так как он может применяться при естественном и искусственном
испарении жидкости в пределах изменения температур от +45 до -35°С. Это
позволяет в любое время года устанавливать баллоны и резервуары с жидким
пропаном в отапливаемых и неотапливаемых помещениях, снаружи здания и в грунте.
Достоинством пропана является и то, что образующиеся в начале и в конце
опорожнения емкостей пары при любом методе испарения почти однородны по своему
составу.
Основными видами газообразного топлива,
используемого для газоснабжения городов и населенных пунктов, являются горючие
газы с низшей теплотой сгорания не менее 12,57 мДж/м³
и
согласно ГОСТ 5542-78 он
должен соответствовать
следующим требованиям: содержание в нем вредных примесей на 100 м³
газа не должно превышать (г):
Цианистых
соединений
нафталина
зимой - 5.
Содержание кислорода не должно быть более 1% по
объему.
Запах нетоксичных газов должен ощущаться при
содержании их в воздухе в количестве не более 1/5 от нижнего предела
воспламеняемости, а запах токсичных газов - при содержании их в воздухе и в
количествах, допускаемых санитарными нормами, для чего газ должен одорироваться,
если он не обладает достаточно сильным и характерным запахом.
Газы сухой перегонки твердого
топлива можно подразделить на две группы: на газы с низким содержанием балласта
и газы с высоким содержанием балласта.
Запах нетоксичных газов должен
ощущаться при содержании их в воздухе в количестве не более 1/5 от нижнего
предела воспламеняемости, а запах токсичных газов - при содержании их в воздухе
и в количествах, допускаемых санитарными нормами, для чего газ должен
одорироваться, если он не обладает достаточно сильным и характерным запахом.
Газы с малым содержанием
балласта получают ісухой перегонкой углей и сланцев в печах с внешним
обогревом. Их можно получить также при нагреве перерабатываемого топлива
твердым теплоносителем, например золой или песком, при температуре около 900
°С.
К числу газов с малым
содержанием балласта принадлежат газы, производимые полукоксованием, т. е.
нагревом угля или сланцев до 500-550 °С, и газы, полученные в процессе
коксования, т. е. нагревом каменных углей до температуры порядка 1000 °С.
При сухой перегонке топлива с
высоким содержанием кислорода в горючей массе (древесина
<#"821159.files/image001.jpg">
Рисунок 1 Схема устройства по очистке и осушке
газа
Устройство для очистки и осушки газа содержит
адсорберы А, Б, В, Г и Д с двухслойным адсорбентом, в которые очищаемый газ
подается по коллектору подачи очищаемого газа (1), а очищенный и осушенный газ
по коллектору отвода (2) отводится сверху. К этому последнему коллектору
подсоединен ресивер (3) для накопления и подачи продувочного газа на
регенерацию через вихревую трубку (4), установленную после ресивера. Для
откачки продуктов очистки используется эжектор (5), установленный также после
ресивера. Снизу к адсорберам присоединен и коллектор отвода продувочного газа
(6), на котором установлен теплообменник (7), одновременно размещенный на
потоке газа между ресивером и вихревой трубкой. Управление арматурой для
переключения адсорберов с режима адсорбции на регенерацию и обратно
осуществляется командным блоком (на чертеже не показаны)
Принцип работы устройства заключается в
следующем. Сырой исходный газ под давлением пропускают через, например,
адсорбер А, где газ, проходя через первый слой адсорбента-силикагеля или окиси
алюминия, подвергают предварительной осушке и очистке, а во втором слое
адсорбента - цеолите производят окончательную глубокую осушку и очистку газа,
который направляют потребителю, отбирая часть газа в ресивер для продувки
адсорбента и откачки адсорбера. После насыщения адсорбента продуктами очистки
адсорбер А переводят в режим регенерации, а адсорбер Б - в режим очистки и
осушки. Процесс регенерации адсорбента состоит из следующих операций: снижение
давления газа в адсорбере до величины, при которой проводится продувка
адсорбента горячим очищенным и осушенным газом, снижение давления в адсорбере
ниже продувочного с помощью эжектора и откачка продуктов очистки, повышение
давления в адсорбере до величины, при которой проводится продувка адсорбента
холодным потоком очищенного и осушенного газа, медленное повышение давления
газа в адсорбере до рабочего значения режима очистки и осушки за счет подачи
сырого исходного газа. Все адсорберы периодически и последовательно проходят
режимы адсорбции и регенерации. Очищенный и осушенный газ для продувки отбирают
из ресивера и через теплообменник направляют в вихревую трубку, где разделяют
на холодный и горячий потоки, при этом долю холодного потока выбирают таким
образом, чтобы обеспечить не только высокую температуру горячего потока, но и
достаточный расход газа для продувки. Для обеспечения непрерывности работы
вихревой трубки режим продувки организуют так, что пока в одном адсорбере
продувают адсорбент горячим газом, то в это же время идет продувка адсорбента
холодным потоком газа в другом адсорбере при одинаковых давлениях. Продувочные
газы и газ после эжектора сбрасывают в магистраль газа низкого давления. Для
снижения температуры сбрасываемого газа смешивают горячий поток после
теплообменника с холодным потоком после эжектора.
Очистка природного газа от диоксида углерода и
осушки от влаги перед его ожижением для предотвращения конденсации указанных
компонентов на теплопередающей поверхности холодильников при температуре 110К
осуществляется следующим образом.
Очищаемый природный газ в количестве 9000 нм3/ч,
давлением 4,5 МПа, с температурой 278К и содержанием диоксида углерода 0,1%
(об.) при 100% относительной влажности подают на адсорбер A снизу. В адсорбере
A природный газ вначале осушается на слое силикагеля до абсолютного
влагосодержания, соответствующего точке росы -40oC, кроме того, в этом слое
адсорбируются тяжелые углеводороды, имеющие сравнительно высокую температуру
конденсации, затем газ осушается в слое цеолита до точки росы -70oC и очищается
от диоксида углерода до остаточного содержания 40 ppm и подается на ожижение.
Часть очищенного газа отбирают в ресивер, где
поддерживают давление газа, равное давлению газа на выходе из адсорберов.
Количество адсорбента, засыпанного в адсорберы, обеспечивает очистку и осушку
газа указанного расхода в течение 60 мин.
По истечении этого времени c помощью управляемых
клапанов адсорбер А переводят в режим регенерации, а в режим очистки и осушки
включают адсорбер Б. В режиме регенерации вначале снижают давление газа с 4,5
МПа до 0,6 МПа в течение 30 мин со скоростью 0,13 МПа в мин, а затем продувают
адсорбенты горячим потоком газа с температурой 355К и расходом 360 нм3/ч в
течение 60 мин. Продувку производят обратным потоком, подавая горячий газ в
адсорбер сверху и отводя продувочные газы снизу через теплообменник в
магистраль низкого давления газа. Утилизации тепла продувочных газов позволяет
повысить температуру газа на входе в сопло вихревой трубки до 310 К и получить
на выходе ее горячего конца - 355К. После прогрева адсорбента прекращают его
продувку и откачивают продукты очистки с помощью эжектора, снижая давление в
адсорбере до 0,15-0,2 МПа. Откачку адсорберов производят в течение 30 мин,
затем вновь повышают давление газа в адсорбере до 0,6 МПа в течение 30 мин.
Такое повышение давления в адсорбере предусмотрено для выравнивания давления
газа между горячим и холодным потоками. После повышения давления в адсорбере
продувают адсорбент холодным потоком газа с температурой 268K в течение 60 мин,
снижая температуру адсорбента до 273K и повышая динамическую активность
адсорбента. Продувочный холодный газ в количестве 440 нм3/ч отбирают с
холодного конца вихревой трубки и после адсорбера сбрасывают в коллектор
низкого давления, где он смешивается о горячим потоком газа после
теплообменника. На этом процесс регенерации адсорбента завершается. Для
подготовки адсорбера к режиму очистки и осушки в нем повышают давление до
рабочего значения 4,5 МПа за счет подачи исходного очищаемого газа.
Все адсорберы работают 60 мин в режиме адсорбции
и 240 мин в режиме регенерации, то есть цикл регенерации адсорбента занимает в
4 раза больше времени, чем его работа в режиме адсорбции. Это также является
существенным отличием от традиционной короткоцикловой безнагревной адсорбции,
где полуциклы адсорбции и регенерации равны. Это позволяет значительно
сократить количество циклов срабатывания управляемой арматуры. Так, например, в
выпускаемых блоках осушки воздуха, работающих по принципу короткоцикловой
безнагревной адсорбции с 2-мя адсорберами и продолжительностью полуцикла
адсорбции и регенерации по 10 мин при круглогодичной работе блока очистки и
осушки газа (8000 часов) количество переключении клапанов составит 48000, а по
предлагаемой схеме - количество переключений клапанов составляет 1600 циклов.
Надежность работы предлагаемого устройства будет значительно выше и
экономичнее, чем известные способы короткоцикловой безнагревной адсорбции.
3.
Разделение газа на фракции на установке ГФУ
Газофракционирование - получение индивидуальных
легких углеводородов или углеводородных
фракций высокой чистоты из нефтезаводских газов.
Газофракционирующие установки (ГФУ) - комплекс
устройств для разделения смеси лёгких
углеводородов на индивидуальные или технически чистые вещества. Ha ГФУ
перерабатываются
газовые бензины, получаемые из нефтяных (попутных), природных и
нефтезаводских
газов, жидкие продукты, выделенные из газов коксования каталитич.
риформинга
и термич. крекинга. В состав сырья входят в основном индивидуальных
низкомолекулярных
углеводородов С1 С6 (как предельных,
так и непредельных, нормального или
изостроения) или их фракций высокой чистоты, являющихся компонентами
высокооктановых
автобензинов, ценным нефтехимическим сырьем, а также сырьем для
процессов
алкилирования и производств метилтретбутилового эфира и т.д.
На нефте-
и газоперерабатывающих заводах наибольшее распространение получили
следующие
физические процессы разделения углеводородных газов на индивидуальные или
узкие
технические фракции: конденсация, компрессия, ректификация и абсорбция. На ГФУ
эти
процессы
комбинируются в различных сочетаниях. До фракционирования углеводородные
газы
направляются вначале в блоки очистки от сероводорода и осушки.
Смеси углеводородов разделяются ректификацией в
колонных аппаратах ГФУ. Ректификация
является завершающей стадией разделения углеводородных газов. Особенность
ректификации
сжиженных газов, по сравнению с ректификацией нефтяных фракций, необходимость
разделения очень близких по температуре кипения компонентов или фракций
сырья
при высокой четкости фракционирования.
Абсорбция позволяет перевести извлекаемые газы в
жидкое состояние при сравнительно невысоких давлениях. Количество и качество
абсорбента, а также температура и давление абсорбции зависят от состава
разделяемого газа и заданной глубины извлечения отдельных компонентов;
97,8%-ное извлечение пропан-пропиленовой фракции удается осуществить при
давлении 12 атм и подаче 7 л абсорбента на 1 м? газа, не прибегая к
искусственному холоду. Абсорбционный метод извлечения газов начал успешно
применяться после разработки головной, комбинированной аб-сорбционно-отпарной
колонны, называемой также фракционирующим абсорбером.
Для каждой установки разрабатывается своя
технологическая карта, в которой указывают: оптимальный
режим работы всего оборудования - пределы изменений основных параметров
процесса
- давление в колоннах и емкостях орошении, температура верха и низа (на
контрольной
тарелке) колонн, расход сырья, расход орошения, уровни в кипятильниках,
емкостях
орошения и химический состав получаемых продуктов.
Газофракционирующая установка (ГФУ)
служит для разделения смеси лёгких углеводородов на индивидуальные, или
технически чистые, вещества.
ГФУ входит в состав газобензиновых,
газоперерабатывающих, нефтехимических и химических заводов. Мощность ГФУ
достигает 750 тыс.
т сырья в год.
Для переработки на ГФУ поступает
сырьё - газовые бензины, получаемые из природных и нефтезаводских газов,
продукты
стабилизации нефтей, газы пиролиза и крекинга. В состав сырья входят в основном
углеводороды, содержащие от 1 до 8 атомов углерода в молекуле. Разделение
смесей углеводородов осуществляется ректификацией в колонных аппаратах.
Из верхней части колонны отводятся
пары пропана, которые конденсируются в конденсаторе-холодильнике и поступают в
ёмкость орошения. Часть пропана возвращается на верх колонны как орошение, а
избыток отводится в виде готового продукта. Жидкость с низа колонны после
подогрева поступает для дальнейшего разделения по такой же схеме в следующую
колонну, где из неё выделяется в виде верхнего продукта смесь бутанов, а из
нижней части отводится бензин. Аналогичным образом производится разделение
бутанов на изобутан и нормальный бутан, а бензина - на изопентан, нормальный
пентан, гексаны и т.д. Примерное содержание чистого вещества (в%) в товарном
продукте того же наименования при переработке газового бензина: пропан 96;
изобутан 95; нормальный бутан 96; изопентан 95; стабильный бензин 74.
Установки разделения газов (ГФУ) подразделяются
по типу перерабатываемого сырья - на установки предельных и непредельных газов
и по типу применяемой схемы извлечения целевых компонентом из газов - на
установки конденсационно-компрессионные и абсорбционные. При необходимости
продукты подвергаются дополнительной очистке от меркаптанов раствором щелочи.
В качестве примера приводится описание
технологической схемы установки конденсационно-компрессионного типа для
переработки предельных углеводородов (рисунок 2) и установки абсорбционного
типа для переработки газов каталитического крекинга (рисунок 3).
Рисунок 2. Технологическая схема
газофракционирующей установки конденсационно-компрессионно-ректификационного
типа: I - газ установок
первичной переработки нефти; II
- головка стабилизации установок первичной переработки нефти; III
- головка стабилизации каталитического риформинга; IV
- пропановая фракция; V
- изобутановая фракция; VI
- бутановая фракция; VII
- изопентановая фракция; VIII
- пентановая фракция; IX
- газовый бензин (С6 и выше); X
- сухой газ; XI - аммиак
Современные установки разделения газов работают
по разным технологическим схемам: с нисходящим и восходящим режимом давления.
По схеме с нисходящим режимом давления первой по
пути сырья является этановая колонна, с верха которой отбираются углеводороды
С1-С2. Кубовый продукт этой колонны поступает в следующую колонну, с верха
которой отбирается пропан, и так далее. Наивысшее давление поддерживается в
первой колонне (3,0 МПа), затем оно постепенно снижается в последующих
колоннах. Схема с нисходящим режимом давления требует меньшего числа насосов,
так как кубовый продукт самотеком проходит из колонны в колонну. Если в
поступающем на ГФУ сырье немного пропана и бутана, то экономические
преимущества оказываются на стороне схемы с восходящим режимом давления. На
рис. 2 приведена принципиальная технологическая схема газоразделения с
нисходящим режимом давления.
Прямогонный газ через сепаратор С-1 подается на
сжатие компрессором ЦК-1. При сжатии газ нагревается до 120 °С. Сжатый газ
затем конденсируется в водяном конденсаторе-холодильнике ХК-1 и в конденсаторе-холодильнике
ХК-2, охлаждаемом испаряющимся аммиаком. В ХК-1 охлаждение и конденсация
заканчивается при 50 °С, а в ХК-2 - при 4 °С. После каждой ступени конденсации
газожидкостная смесь разделяется на газ и жидкость в сепараторах С-2 и С-3. Газовые
конденсаты из сепараторов С-1, С-2 и С-3 совместно с головками стабилизации
установок первичной перегонки и риформинга подаются на блок ректификации.
В блоке ректификации из углеводородного сырья
сначала удаляются метан и этан. Удаление происходит в ректификационной колонне,
которая называется деэтанизатором. Верхний продукт этой колонны - метан и этан,
нижний - деэтанизированная фракция. Верхний продукт деэтанизатора охлаждается
искусственным хладагентом - аммиаком.
Деэтанизированная фракция из колонны К-1
поступает в депропанизатор К-2, верхним продуктом которого является пропановая
фракция, а нижним - депропанизированная фракция. Верхний продукт после
конденсации в воздушном конденсаторе-холодильнике ХК-4 и охлаждения в концевом
холодильнике выводится с установки, предварительно пройдя щелочную очистку.
Нижний продукт из депропанизатора К-2 подается в дебутанизатор К-3.
Ректификатом колонны К-3 является смесь бутана и
изобутана, а остатком - дебутанизированный легкий бензин. Ректификат
конденсируется в конденсаторе-холодильнике ХК-5, а затем подается на разделение
в бутановую колонну К-4. Остаток из колонны К-3 переходит в депентанизатор К-5.
Рисунок 3. Технологическая схема
газофракционирующей установки абсорбционно-ректификационного типа: I
- жирный газ; II - свежий
раствор МЭА; III -
сероводород; IV - сухой
газ; V - нестабильный
бензин; VI -
бутан-бутиленовая фракция; VII
- стабильный бензин; VIII
- пропан-пропиленовая фракция.
Установка, схема которой приведена на рисунке 3,
предназначена для стабилизации бензина каталитического крекинга, очистки газа
каталитического крекинга от сероводорода, извлечения из газа углеводородов
С3-С4, разделения смеси этих углеводородов на пропан-пропиленовую и
бутан-бутиленовую фракции.
Жирный газ с установки каталитического крекинга
поступает на очистку моноэтаноламином в абсорбер К-1. Очищенный газ сжимается
компрессором ПК-1 до 1,4 МПа, охлаждается и подается во фракционирующий
абсорбер К-2, под 22-ю тарелку. На эту же тарелку, но выше ввода газа подается
конденсат компрессии.
Во фракционирующий абсорбер вводится также
нестабильный бензин, являющийся основным абсорбентом.
Фракционирующий абсорбер, иначе называемый
абсорбер-десорбером, отличается от обычного абсорбера тем, что представляет
собой комбинированную колонну. В верхней части фракционирующего абсорбера
происходит абсорбция, т. е. извлечение из газа целевых компонентов, а в нижней
- регенерация абсорбента за счет подводимого тепла. Стекая сверху вниз по
тарелкам фракционирующего абсорбера, насыщенный тяжелыми компонентами абсорбент
встречается со все более горячими парами, десорбированными из жидкости, которая
стекает в нижнюю часть колонны. С верха фракционирующего абсорбера уходит сухой
газ, содержащий углеводороды C1-С2, а с низа вместе с тощим абсорбентом
выводятся углеводороды С3-С4. В отличие от обычных абсорберов, куда питание
подается только в газовой фазе, во фракционирующие абсорберы оно вводится и в
виде жидкости, и в виде газа.
Для доабсорбции унесенных с сухим газом
бензиновых фракций в верхнюю часть К-2 подается стабильный бензин. Температура
в абсорбционной части поддерживается промежуточным охлаждением абсорбента.
Насыщенный и деэтанизированный абсорбент из К-2 подается в стабилизатор К-3,
верхним продуктом которого является головка стабилизации, а нижним - стабильный
бензин. Головка стабилизации поступает на блок очистки, где очищается от
сернистых соединений раствором МЭА и щелочью. Затем из очищенной головки в
пропановой колонне К-4 выделяется пропан-пропиленовая фракция. Остаток
пропановой колонны в бутановой колонне К-5 разделяется на бутан-бутиленовую
фракцию и остаток, который объединяется со стабильным бензином.
4. Применение продуктов
газофракционирования
Природный газ отлично вступает в химическую реакцию
горения. Поэтому чаще всего из него получают энергию - электрическую и
тепловую. Но на основе газа можно сделать еще удобрение, топливо, краску и
многое другое.
Во многих странах около половины поставок газа
приходится на энергетические компании и коммунальное хозяйство. Даже если в
доме нет газовой плиты или газового водонагревателя, все равно свет и горячая
вода, скорее всего, получены с использованием природного газа.
Природный газ - самое чистое среди
углеводородных
Похожие работы на - Газообразные топлива Курсовая работа (т). Химия.
Реферат: Доктрина "Москва - Третий Рим": суть и влияние
Контрольная работа: Контрольная по экономике 2
Реферат На Тему Природа І Наука У Філософському Осмисленні
Произведения Под Направления Итогового Сочинения 2022 2022
Шрифт Для Дипломной Работы По Госту 2022
Биофизика как наука
Егер Мен Мектеп Директоры Болсам Эссе
Реферат: Фантастическое и реальное в творчестве Н.В.Гоголя. Скачать бесплатно и без регистрации
Реферат по теме Глобальное потепление, усиление землетрясений и стихийных бедствий вследствие истощения озонового слоя
Контрольная работа по теме Технологическая карта на производство монолитного каркаса многоэтажного здания
Сочинение по теме Венецианский купец. Уильям Шекспир
Курсовая работа по теме Оценка затрат на собственный капитал
Сочинение Грустная Осень
Факторы, влияющие на величину стоимости бизнеса
Реферат: Процессоры ЭВМ
Распорядительные Документы Курсовая
Курсовая работа по теме Исследование конъюнктуры рынка
Реферат: Механизм выпуска и обращения простого и переводного векселя
Реферат по теме Екологічні проблеми Венеції
Современная Картина Мира Эссе
Доклад: Демократия и экономическое развитие
Доклад: Натуральное седативное средство в психиатрии и соматической медицине
Курсовая работа: Автоматизация линии раздачи кормов в свинарнике