Галерея 3121451
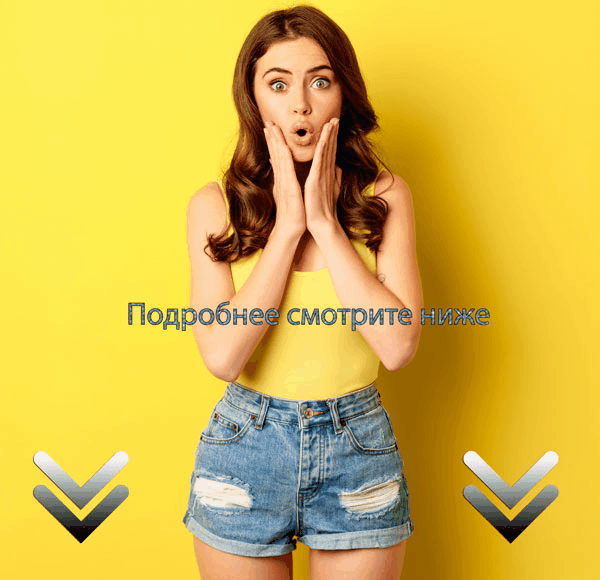
🛑 ПОДРОБНЕЕ ЖМИТЕ ЗДЕСЬ 👈🏻👈🏻👈🏻
Галерея 3121451
Feb. 18, 1964 H. u. SCHUERCH ISOTENSOID STRUCTURE 3 Sheets-Sheet 1 Filed Dec. 14, 1959 ,Hiws U. SCHUEQC/L 17v vEA/rae 5g #1 :5 Abram/1:315 1122915, 107554, Roses @Ifeem Feb. 18, 1964 H. u. SCHUERCH zsomusom STRUCTURE 3 Sheets-Sheet 2 Filed Dec. 14, 1959 Jiiws U. 50/0590;
, JM EMm/Q. B Ms A 770,?4/555 Ewe/s, hscfg B95554; .HEEM
1954 H. u. SCHUERCH ISOTENSOID STRUCTURE 3 Sheets-Sheet 3 Filed Dec. 14, 1959 w M M jlj/vs UT Sam/520M, l'ivvewrak.
5 A45 firmewzys, ,Himms, did/saw, Buses (ii-Kean United States Patent 3,121,451 ISOTENSSID STRUCTURE Hans U. Sehuerch, 73 t Arholado Road, Santa Barbara, Calif. Filed Dec. 14, 1959, Ser. No. 859,473 38 Claims. (U. 150-.5)
My invention relates to the filamented bodies, such as hollow vessels of minimum weight per enclosed volume having maximum strength-toweight ratios.
The invention comprehends filamented bodies in which filamentary reinforcements carry substantially all of the primary structural loads, these filaments being wires, threads, yarns, ropes, etc., either singly or in multiple arrays. Such filaments may or may not be bonded together by or embedded in a matrix of some difierent material filling the voids between individual filaments. Most commonly the filaments are joined or covered by a matrix material but this material serves secondary functions only, e.g., bonding or spacing of the filaments, sealing and crack barrier formation, load redistribution in case of partial failure, prevention of filament buclding in case of compressive loads, etc.
t is an object of the invention to provide a filamented structure in which the tensile or compressive force along each filament is both uniform and invariant throughout its length within close limits and in which no shearing force transfer through the matrix is required. The term isotensoid aptly describes such structures and it is an object of the invention to provide isotensoid structures of various shapes, including for instance for pressure vessels shapes bounded by surfaces of topological genus l, genus 2 or higher, which structures are able to withstand or transmit structural loads and are capable of undergoing deformations without impairment of structural integrity, e.g., Without impairment of such primary functions as load bearing, load transmitting, etc., and without impairment of such secondary functions as forming pressuretight barriers, separating dissimilar fiuids, controlling heat transfer between fluid media, etc.
ideally, the invention employs essentially endless filaments by which I have reference to lengths or configurations in which the filament may return one or several times on a on rvitious path into the vicinity of its beginning or end. The term thus includes filaments forming end loops or ti ht spirals. Essentially endless filaments may be single or multiple strand, the latter including a plurality of individual fibers which may be relatively short but which are held together as a part of the filament by mutual friction or bonding.
By utilizing filaments to resist the load and by relating shape to loads as will be described it becomes possible to stress all filaments substantially uniformly and equally at values just short of their breaking stresses. If the filaments are of uniform cross section and strength it thus becomes possible to obtain minimum-weight structures. If the invention is applied to pressure vessels the filamentary nature of the structure also may prevent explosive or catastrophic failure upon puncture because the matrix material may form an effective barrier against crack propagation. Also it becomes possible by use of the invention to make, if desired, collapsible structures that can be stored in small spaces and inflated to predetermined shape. It is an object of the invention to provide structures having high strength-to weight ratios yet which are insensitive to catastrophic crack propagation and which, if desired, can be made collapsible into small spaces.
Many extremely small filaments show remarkable strength. Thin filaments of glass, refractory fibers and filamentary crystals may have strengths of the order of "ice 10 psi. A substantial percentage of the filament strength can be retained by proper design. While it has previously been proposed to reinforce plastic structures or vessels with filamentary material, a review of the structural performance thereof shows that usually less than 50% of the potential material strength is exploited. It is an object of the present invention to provide design relationships through which it is possible to utilize practically all of the potential material strength of filamentary materials. Other objects of the invention reside in the provision of uniquely shaped structures as hereinafter suggested.
Still further objects and advantages of the invention will be evident to those skilled in the art from the following descriptions of exemplary embodiments and the accompanying drawings.
FIG. 1 represents a series of curves resulting from solutions of one of the isotensoid equations used in the invention;
FIG. 2 is a diagrammatic perspective view of one embodiment of the invention with a section cut away for better illustration;
FIGS. 3 and 4 are diagrammatic perspective views of two toroidal embodiments having doubly connected volumes and the same topology;
FIG. 5 is a perspective view of an embodiment having a doubly connected volume the aXis of which is not in a single plane;
FIGS. 6 and 7 are diagrammatic perspective views of two other embodiments;
FIG. 8 is a fragmentary cross-sectional view of a multilayer structure illustrating how multi-fiber filaments can be shaped and held together;
FIG. 9 is a diagrammatic view illustrating mechanism by (which the embodiment of FIG. 7 or other embodiments can be formed;
FIG. 10 is a perspective view of a winding form useful in conjunction with the machine of FIG. 9; and
FIG. 11 is a diagrammatic view suggesting steps that can be used in producing the embodiment of FIG. 9.
An endless filament of an isotensoid body forming essentially a closed loop can be defined with reference to any point s on the center line of the filament by the vector 5 from the origin of an arbitrary coordinate system to the point s. A summation of such vectors can define a three dimensional structure the surface of which is bounded by such filaments disposed side-by-side. In the most general relationship in which the load is not necessarily uniform at different positions along the surface, it has been determined that isotensoid relationships will result from a structure having filaments of a geometrical configuration Erelated to a volumetric load factor p (representing the load from external sources applied to a unit volume of the structure) by substantially the equation:
k=the number of filaments permeating a unit volume around point 8,
t =the force in any such filament at any point between attachments thereof other than attachments to any matrix,
ds=a small (difrerential) length along the path of a filament,
=the unit vector parallel to the tangent to the filads ment at point s, and
(hf-d8 d8 -the second derivative of the vector 5 The second derivative of the vector .5 describing the space curve of a filament path is again a vector. This vector is parallel to the radius of curvature of the space curve and is equal in magnitude to the curvature of the space curve. The unit volume referred to above has reference to a space occupied by filaments of unit length.
The mathematical relationship between load and filamentary geometry given in Equation 1 is exactly satisfied only for ideal structures consisting of filaments without internal friction and Without any restraining matrix material. In practice such conditions cannot be satisfied with mathematical precision. The isotensoid structures of the invention substantially satisfy by the above Equation 1, in the sense that deviations should not exceed the following: As to the force or load in each filament between attachments, this should be within the range of .9-1.1r. The configuration should be such that the tangent angle at any point thereon should vary from the true tangent angle by not more than of a radian (approximately 1 angular degree). 'If a matrix material is employed, it should never carry more than of the internal forces generated by external loads. In other words, in a pressure vessel for example at least 90% of any internal forces induced by pressure loads should be carried by the filaments.
The texture of an isotensoid body is given by the geometry of the filamentary paths that permeate the body. In the most general form of the invention, these paths may be completely at random, restrained only by the condition that Equation 1, relating volumetric loads and filamentary geometry, remain satisfied. In other forms to be described the filamentary paths are geodesic or meridional.
A particularly important application of the isotensoid structures of the invention is in the field of onionoid hollow pressure vessels characterized by loads that are normal to the surface of the structure. These may be bodies of revolution with rotational symmetry with respect to the z axis and with filaments arranged geodesically. The loads on these bodies may be an internal pressure normal to the internal surface of the body. This pressure p may be exerted by a contained gas, a contained liquid and/or by adjoining structural components. On the assumption that the internal pressure p may vary along the z axis albeit in a pattern rotationally symmetrically distributed, all points in the mid-surface halfway between the outer and inner surfaces of an ideal isotensoid hollow vessel will substantially satisfy the equations:
where r=radius to any point on any meridian of said midsurface measured perpendicular to the z axis,
n=number of filaments traversing a cross section,
B=helix angle between the geodesics and a corresponding meridian, and
B =-and r are arbitrary integration constants.
As before, isotensoid structures substantially satisfying Equations 2 and 3 are contemplated by the invention. Matrix materials, if used, should not carry more than 10% of the internal forces generated by external loads and the actual tensile force in each filament of the vessel should differ within the filament and from the tensile force in other filaments Within a range no greater than .9-1.1t.
In the special case under consideration, the filamentary geometry describes lines that are geodesics for the onionoid surface of the pressure vessel. Excessive buildup at or near the poles with helix angles other than zero is avoided in ways to be described, e.g. making the structure with pole openings which can be closed by separate elements made of conventional design or by use of the isotensoid principles of the invention.
If r and 5 are defined respectively as the radius and the helix angle at the equator the minimum radius controlling the size of any pole opening will be uniquely defined. An isotensoid body of revolution using geodesic winding patterns of a helix angle different from zero and shaped in accordance with Equations 2 and 3 will always have two polar openings of equal size and the equatorial helix angle .6 will be uniquely defined by the ratio of the equatorial diameter to the required diameter of the polar opening.
In the even more specific case where {3:0, i.e. where the geodesics are meridional, the mid-surface can be more simply defined. In this special case Equations 2 and 3 may be simplified to:
As before, Equation 4 would delineate an isotensoid structure with mathematical precision. The isotensoid structures of the invention conform substantially to Equation 4 in the special case under consideration, deviations being no greater than set forth above as concerns Equations 2 and 3.
Solutions of all of the Equations 1, 2, 3, or 4 cannot be expressed in closed form. A number of solutions for Equation 4 for the special case where p is uniform are shown schematically in FIG. 1 of the drawings. The outer portion of curve 10, for example, corresponds generally to the cross sectional configuration of the isotensoid structure of FIG. 2. Likewise the looped or closed portion 12a of curve 12 approximately outlines the cross section of the embodiment of FIG. 3.
Referring more specifically to FIG. 2, the hollow isotensoid structure 14 therein shown includes a multitude meridional filaments 15 only a few of which are suggested. These are anchored to rings 16 and 17 with their intersupport portions connected, if at all, by a matrix material 18 which serves primarily to retain the spacing of the filaments. The loads are taken by the filaments and are represented by isotensile stresses in the filaments as previously described. The function of the matrix material is primarily to maintain the filaments in the desired predetermined position. The shape of the structure is made in accordance with Equation 4 supra. The openings of the rings 16 or 17 may provide access to or from the interior space 19 or may be partially or completely closed by supplementary structures made in accordance with the invention or otherwise. Typical supplementary structures will be later exemplified.
The meridional filaments 15 are anchored to the rings 16 and 17 in any suitable way. There may be some overlap of the filaments at the rings to build up a somewhat thicker area which may assist the connection of structures that partially or completely close the corresponding opening. However it is preferable to avoid such overlap and to minimize or eliminate differences in spacing of the filaments near the rings as compared with near the equator. One excellent way of accomplishing the latter is to make each filament wide and thin (flat) in cross section at the equator, tapering to a cross section that is narrow and thick toward the poles. if the filament is made up of numerous bundled fibers the spacing thereof within the lament may remain essentially uniform. It is not essential to the invention that wall thickness be uniform throughout and the use of such filaments tapering in cross section between inner and outer positions or loci is not limited to the isotensoid design determined by substantial adherence to the above equations.
FIG. 3 illustrates another embodiment that is designed in accordance with Equation 4. Here the vessel Ztl is shown in an initial substantially toroidal shape but of a cross sectional shape corresponding to the portion 12a of curve 12 of FIG. 1. The outer portion 21 of the cross section is rather rounded as compared with the more sharply curved inner portion 22. The latter is reinforced circumferentially or equatorially by any suitable ring 25 which forms a second filamentary system similar in function to the rings 15 and 17 of FIG. 2. Filaments 26 (only a few of which are shown in FIG. 3) are in one of two general forms. As illustrated, they are meridional endless rings in planes radial to the central or z axis zz and are linked with the ring 25, being sometimes compacted thereadjacent as compared with a position at the crest of the outer portion 21, the compaction being either to a compact side-by-side relation or an over-la ping relation as previously mentioned. However filament spacing adjacent the ring 25 and the crest of the outer portion 21 may be uniform by using the varying cross section of the filament as described with reference to FIG. 2. Such filaments may be initially endless or may be made endless by joining the ends of individual filaments to the ring 25. Alternately, the filaments 2% may be essentially endless rings by being composed of respective turns of a long length of filamentary material wound in a general helical path around the ring 25 in closely spaced turns of the desired peripheral length. The helix angle can be so small as to be of negligible significance if the turns are tightly compacted at the inner portion 22.
In this embodiment if any matrix material 28 is utilized its function will be primarily to maintan the filaments 26 appropriately spaced. Loads inside the vessel will be taken by the filaments and will develop isotensile forces therein substantially equal in each filament at positions beyond the support formed by the ring 25 and sub stantially equal as between the different filaments.
Structures in which the filaments are turns of a long length of filamentary material are particularly useful in some instances and need not employ the ring 25. Typical forms are shown in H68. 4 and 5, the latter being shaped as determined by Equation 1 and the former being shaped in accordance with Equations 2 and 3 providing for rotational symmetry. FIG. 4 illustrates a toroidal vessel bounded by a surface of genus 2 considering the usual ingress opening or by two surfaces of genus 1 in the absence of such ingress opening and providing a doubly connected volume the axis of which is shown in a single plane. If deformation out of such plane is to be avoided upon change in internal pressure two systems of filaments are employed, composed of filaments 29 and 3t? successively wound in different layers at helix angles that are equal at corresponding points but opposite in sign, the helix angle 5 being determined by Equations 2 and 3 and being different at inner and outer portions of any cross section, being larger toward the inner portion than toward the outer portion. Any initial space between turns of each filament system may be filled in by later turns of the same filament system, the turns being joined by a matrix 31 as previously described. The embodiment of FIG. 4 with its crossing filaments eliminates the need for a ring 25, as used in FIG. 3. Additionally the crossed filaments make the structure stay flat upon change in pressure with its axis in substantially a single plane so that it retains a rotational symmetry about the z axis. The cross section of the P16. 4 embodiment is somewhat egg shaped with its inner portion more blunt than its outer portion.
In H6. 5 a single length of filamentary material is wound helically to form filaments or turns 32. shaping a doubly connected volume. Here the closed axis is not in a single plane but is of a general figure eight form spaced a diameter or more at the crossover point. The filament at no place crosses another turn in this embodiment, which can be wound either in substantially the ultimate figure eight form shown or with its closed axis forming a circle and later twisted into its ultimate form as by change in internal pressure. As before, the helix angle 8 is different at the inner and outer portions of a cross section as determined by Equation 1. A matrix material 33 may bridge or join the filaments 32, only a portion of the latter being illustrated in FIG. 5 and a reinforcing ring similar to of FlG. 3 can be employed to lie along corresponding portions of the various cross sections of the structure.
FIG. 6 illustrates a hollow vessel 34 having a main por tion 35 with end openings as and 37 partially closed by supplementary structures including a closure member 38 and a ring element 39. The main portion 35 is of filamented construction in which a long filamentary member is wound substantially helically to form filaments 40. The filaments lie substantially tangential to the openings 36 and 37 at positions thereadjacent.
The ring element 39 may be any separately formed member adhered within the opening 37. It preferably includes a flange 41 lying immediately within the opening 37 along the inner surface of the main portion 35, being suitably adhered thereto. The ring element 39 includes a neck portion i2 which may extend through the opening 37 to other supplementary structures closing or partially closing the opening.
Similarly, the closure member 38- carries a flange 43 conforming to the inner surface of the main portion 35 adjacent
Голые девки кайфуют показывая всем свои сексуальные тела и позволяя мужикам полапать себя
Блондинка с титьками пососала и дала
Минет и дрочка от пухлой харьковчанки