Галерея 2987500
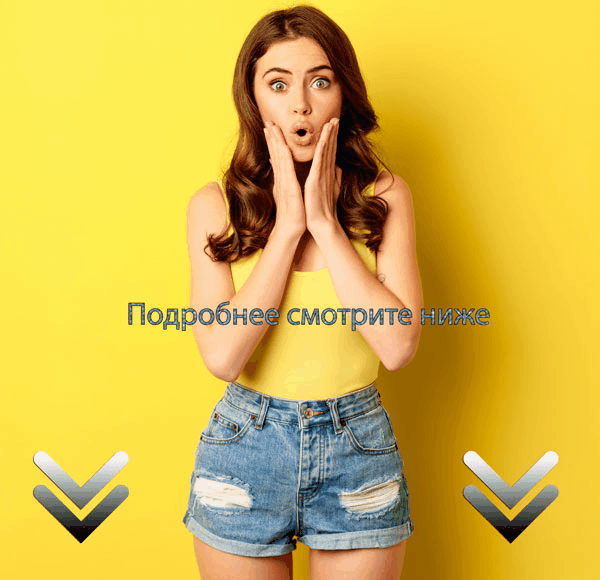
⚡ ПОДРОБНЕЕ ЖМИТЕ ЗДЕСЬ 👈🏻👈🏻👈🏻
Галерея 2987500
The invention relates to a method for producing a hardened steel component, wherein a blank is punched out and the punched-out blank is heated to a temperature = Ac3 either completely or in partial regions and is possibly held at said temperature for a predetermined time in order to perform the formation of austenite, and then the blank heated completely or in partial regions is transferred into a forming tool, is formed in the forming tool, and is cooled in the forming tool at a rate that lies above the critical hardening rate and is thereby hardened, or undergoes final cold-forming, and the formed blank is heated to a temperature = Ac3 completely or in partial regions and is possibly held at said temperature for a predetermined time in order to perform the formation of austenite, and then the blank heated completely or in partial regions and formed is transferred into a hardening tool and is hardened in the hardening tool at a rate that lies above the critical hardening rate, wherein the steel material is adjusted to delay conversion in such a way that, at a forming temperature that lies in the range of 450 °C to 700 °C, quench hardening is achieved by conversion of the austenite into martensite, wherein active cooling occurs after the heating and before the forming, in the case of which active cooling the blank or parts of the blank or the formed blank or regions thereof are cooled at a cooling rate > 15 K/s, wherein a cooling device and an object having a hot surface are moved in relation to each other in order to homogeneously, contactlessly cool the hot blanks or components, wherein the cooling device has at least two parallel, spaced cooling blades or cooling columns, wherein the cooling blades or cooling columns have a nozzle edge having nozzles toward the blank to be cooled or toward the component to be cooled, wherein a cooling fluid is directed at the surface of the blank or of the component by the nozzles and the cooling fluid flows away into the intermediate space between the blades or cooling columns after contacting the hot surface.
. . Method for Contactless Cooling of Steel Sheets and Apparatus Therefor The invention relates to a method for contactless cooling of steel sheets and to an apparatus therefor. In the technical field, cooling processes are needed in many areas, for example when it is necessary to cool flat plates, but also when it is necessary to cool glass surfaces, for ex-ample in glass production, or to cool processor units and the like. Prior cooling systems are either very expensive or are kept quite simple, e.g. by blowing air or other fluids such as wa-ter or oil; this entails the disadvantage that unfavorable, uncontrolled flow conditions always occur on the surface, which then become a problem when a particularly defined cool-ing is required. In the prior art, it must be largely assumed that disadvanta-geous flow conditions, so-called cross flow, exist on the flat surface that is to be cooled and this causes heterogeneous surface temperatures. This is particularly disadvantageous if homogeneous temperatures are required in the region of the surface in order to achieve homogeneous material properties. In particular, non-homogeneous surface temperatures also cause warpage. US 5,871,686 has disclosed an apparatus for cooling moving steel strips, which has a plurality of cooling fins extending transversely to the travel direction of the steel strip, and the cooling fins have cooling nozzles, which are aimed at the steel strip and which can blow a cooling fluid at the moving steel strip. US 2011/0018178 Al has disclosed a comparable apparatus, but which instead of cooling fins with nozzles, has a plurality of cooling cylinders that are aimed at the strip and whose free ends have outlet openings for a fluid that is to be supplied to a moving steel strip. DE 69833424 T2 has disclosed an apparatus, which has a plural-ity of cooling fins that are likewise aimed at a moving steel strip and, in a way that is comparable to the above-mentioned prior art, act on the steel strip with jets of a cooling flu-id, with the moving steel strip being tensioned by means of rollers in order to prevent movements that deviate from the unidirectional traveling movement of the strip. WO 2007/014406 Al has also disclosed an apparatus for cooling a moving metal strip, in which nozzles are used to convey a coolant from gas boxes through gas conduits and onto the strip by means of nozzle strips. Conventional cooling methods do not permit a controlled achievement of a predetermined target temperature, nor do they make it possible to systematically set virtually any cooling rate up to a maximum achievable cooling rate. There are particular difficulties if different material thick-nesses or starting temperatures are present on a cooling sur-face, which are to be cooled to homogeneous temperature condi-tions. It is known that so-called press-hardened components made of sheet steel are used particularly in automobiles. These press-
2 hardened components made of sheet steel are high-strength com-ponents that are particularly used as safety components of the vehicle body region. In this connection, the use of these high-strength components makes it possible to reduce the mate-rial thickness relative to a normal-strength steel and thus to achieve low vehicle body weights. With press-hardening, there are basically two different possi-bilities for manufacturing such components. A distinction is drawn between the so-called direct and indirect methods. In the direct method, a steel sheet blank is heated to a tem-perature above the so-called austenitization temperature and if need be, is kept at this temperature until a desired degree of austenitization is achieved. Then this heated blank is transferred to a forming die and in this forming die, is formed into the finished component in a one-step forming pro-cedure and in the process of this, is simultaneously cooled by the cooled forming die at a speed that lies above the critical hardening speed. This produces the hardened component. In the indirect method, possibly in a multi-step forming pro-cess, the component is first formed almost completely. This formed component is then likewise heated to a temperature above austenitization temperature and if need be, is kept at this temperature for a desired, necessary amount of time. Then this heated component is transferred to and inserted into a forming die that already has the dimensions of the component or the final dimensions of the component, possibly taking into account the thermal expansion of the preformed component. Af-ter the die - which is in particular cooled - is closed, the preformed component is thus only cooled in this die at a speed that lies above the critical hardening speed and is thus hard-ened. In this connection, the direct method is somewhat easier to execute, but it only enables the production of shapes that can actually be produced in a single forming step, i.e. relatively simple profile shapes. The indirect method is somewhat more complicated, but is also able to produce more complex shapes. In addition to the need for press-hardened components, a need has also arisen to not produce such components out of uncoated steel sheet, but rather to provide such components with a cor-rosion protection layer. In automotive engineering, the only options for the corrosion protection layer are aluminum or aluminum alloys, which are used much less often, or zinc-based coatings, for which there is much more demand. In this connection, zinc has the ad-vantage that it not only provides a protective barrier layer like aluminum, but it also provides a cathodic corrosion pro-tection. In addition, zinc-coated press-hardened components fit better into the overall corrosion protection of vehicle bodies since bodies are completely galvanized in current popu-lar design. In this respect, it is possible to reduce or even eliminate the occurrence of contact corrosion. Both methods, however, involve disadvantages that are also discussed in the prior art. With the direct method, i.e. hot forming of press-hardened steels with a zinc coating, micro-cracks (10 pm to 100 pm) or even macro-cracks occur in the ma-terial; the micro-cracks occur in the coating and the macro-cracks even extend through the entire cross-section of the
3 = sheet. Such components with macro-cracks are not suitable for further use. In the indirect method, i.e. cold forming with a subsequent hardening and residual forming, micro-cracks also occur in the coating, which are likewise unwanted, but are far and away less pronounced. Up to this point, except for components in the Asian market, zinc-coated steels have not come into wide use in the direct method, i.e. hot forming. In this case, steels with an alumi-num/silicon coating are used. An overview is given in the publication "Corrosion resistance of different metallic coatings on press hardened steels for automotive," Arcelor Mittal Maiziere Automotive Product Re-search Center F-57283 Maiziere-Les-Mez. This publication states that for the hot forming process, there is an alumi-nized boron/manganese steel that is sold commercially under the name Usibor 1500P. In addition, for purposes of cathodic corrosion protection, zinc-precoated steels are sold for the hot forming method, namely galvanized Usibor GI with a zinc coating, which contains low percentages of aluminum, and a so-called galvannealed, coated Usibor GA, which has a zinc layer with 10% iron. It should be noted that the zinc/iron phase diagram reveals that above 782 C, a large area is produced in which liquid zinc/iron phases occur as long as the iron content is low, in particular less than 60%. But this is also the temperature range in which the austenitized steel is hot formed. It should also be noted, however, that if the shaping takes place at a temperature above 782 C, there is a high risk of stress corro-sion due to fluid zinc, which presumably penetrates into the
4 grain boundaries of the base steel, causing macro-cracks in the base steel. Furthermore, with iron contents of less than 30% in the coating, the maximum temperature for shaping a safe product without macro-cracks is lower than 782 C. This is the reason why the direct shaping method is not used herein and the indirect shaping method is used instead. The intent of this is to avoid the above-explained problem. Another option for avoiding this problem should lie in using galvannealed, coated steel since the iron content of 10% that is already present at the beginning and the absence of an Fe2A15 barrier layer result in a more homogeneous formation of the coating from predominantly iron-rich phases. This results in a reduction or avoidance of zinc-rich, liquid phases. The paper "STUDY OF CRACKS PROPAGATION INSIDE THE STEEL ON PRESS HARDENED STEEL ZINC BASED COATINGS" by Pascal Drillet, Raisa Grigorieva, Gregory Leuillier, and Thomas Vietoris, 8th International Conference on Zinc and Zinc Alloy Coated Steel Sheet, GALVATECH 2011 - Conference Proceedings, Genoa (Italy), 2011" makes reference to the fact that galvanized sheets can-not be processed using the direct method. EP 1 439 240 Bl has disclosed a method for hot forming a coat-ed steel product; the steel material has a zinc or zinc alloy coating, which is formed on the surface of the steel material, and the steel base material with the coating is heated to a temperature of 700 C to 1000 C and hot formed; the coating has an oxide layer, which is mainly composed of zinc oxide, before the steel base material is heated with the zinc or zinc alloy layer in order to then prevent a vaporization of the zinc when it is heated. A special process sequence is provided for this.
5 EP 1 642 991 Bl has disclosed a method for hot forming a steel in which a component composed of a given boron/manganese steel is heated to a temperature at the Ac3 point or higher, is kept at this temperature, and then the heated steel sheet is shaped into the finished component; the formed component is quenched by being cooled down from the forming temperature during or after the forming in such a way that the cooling rate at the Ms point at least corresponds to the critical cooling rate and the average cooling rate of the formed component from the Ms point to 200 C lies in the range from 25 C/s to 150 C/s. EP 1 651 789 Bl, which belongs to the applicant, has disclosed a method for producing hardened components made of sheet steel; in this case, formed parts made of a steel sheet pro-vided with a cathodic corrosion protection are cold-formed followed by a heat treatment for purposes of austenitization; before, during, or after the cold-forming of the formed part, a final trimming of the formed part and any needed punch-outs are performed or a hole pattern is produced and the cold form-ing, trimming, punching, and positioning of the hole pattern on the component should be 0.5% to 2% smaller than the dimen-sions of the component after final hardening; the cold-formed formed part that is heated for the heat treatment is then heated in at least some regions - accompanied by a supply of atmospheric oxygen - to a temperature that enables an austen-itization of the steel material, and the heated component is then transferred to a die and in this die, a so-called form-hardening is carried out in which the contacting and pressing (holding) of the component by the form-hardening dies cools and thus hardens the component, and the cathodic corrosion protection coating is composed of a mixture essentially com-posed of zinc and also contains one or more elements with an oxygen affinity. As a result, an oxide skin, which is composed of the elements with the oxygen affinity, forms on the surface
6 of the corrosion protection coating during the heating, which protects the cathodic corrosion protection layer, in particu-lar the zinc layer. With the method, the reduction in scale of the component in terms of its final geometry also takes into account the thermal expansion of the component so that the form hardening requires neither a calibration nor a shaping. WO 2010/109012 Al, which belongs to the applicant, has dis-closed a method for producing partially hardened steel compo-nents; a sheet blank composed of a hardenable steel sheet is subjected to a temperature increase, which is sufficient for a quench hardening, and after a desired temperature and possibly a desired exposure time, the sheet blank is transferred to a forming die in which the sheet blank is formed into a compo-nent and at the same time, is quench hardened or else the sheet blank is cold formed and the component obtained from the cold forming is then subjected to a temperature increase; the temperature increase is carried out so that a temperature of the component is achieved that is necessary for a quench hard-ening and the component is then transferred to a die in which the heated component is cooled and thus quench hardened; dur-ing the heating of the sheet blank or component in order to increase the temperature to a temperature that is necessary for the hardening, absorption masses rest against the regions that are supposed to have lower hardness and/or higher ductil-ity or these absorption masses are spaced apart from these re-gions by a small gap; in terms of their expansion and thick-ness, their thermal conductivity, and heat capacity, and/or with regard to their emissivity are dimensioned specifically so that the thermal energy being applied to the region of the component that is to remain ductile flows through the compo-nent and toward the absorption masses so that these regions remain cooler and in particular, do not reach or only partial-ly reach the temperature that is required for the hardening so
7 that these regions cannot be hardened or can only be partially hardened. DE 10 2005 003 551 Al has disclosed a method for hot forming and hardening a steel sheet in which a steel sheet is heated to a temperature above the Ac3 point, then undergoes a cooling to a temperature in the range from 400 C to 600 C, and is only formed after this temperature range is achieved. This cited reference, however, does not address the crack problem or a coating and it also does not describe a martensite formation. The object of the invention is to produce the intermediate structure, so-called bainite. EP 2 290 133 Al has disclosed a method for producing a steel component that is provided with a metallic, corrosion-protecting coating by means of forming a flat steel product, which is composed of Mn steel and which, prior to the forming of the steel component, is provided with a ZnNi alloy coating. With this method, the sheet blank is heated to a temperature of at least 800 C, having been previously coated with the ZnNi alloy coating. This cited reference does not address the prob-lem of "liquid metal embrittlement." DE 10 2011 053 941 Al has disclosed a similar method, but in this method, a sheet blank or a formed sheet blank is only heated to temperature > Ac3 in some areas and is kept at this temperature for a predetermined time in order to carry out the austenite formation and then is transferred to a hardening die and hardened in this hardening die; the sheet blank is cooled at a speed that lies above the critical hardening speed. In addition, the material used therein is a delayed-transformation material; in the intermediate cooling step, the hotter austenitized regions and the less hot non-austenitized or only partially austenitized regions are adapted in terms of
8 their temperature and the sheet blank or the formed sheet blank are homogenized with regard to their temperature. DE 10 2011 053 939 Al has disclosed a method for producing hardened components; in this case, a method for producing a hardened steel component is disclosed, which has a coating composed of zinc or a zinc alloy. A sheet blank is stamped out of this sheet and the stamped sheet blank is heated to a tem-perature Ac3 and as needed, is kept at this temperature for a predetermined time in order to carry out the austenite for-mation and is then transferred to a forming die, is formed therein, and in the forming die, is cooled at a speed that lies above the critical hardening speed and is thus hardened. In this case, the steel material used is adjusted in a trans-formation-delaying way so that at a forming temperature that lies in the range from 450 C to 700 C, a quench hardening takes place through the transformation of the austenite into martensite; after the heating for austenitization purposes, but before the forming, an active cooling takes place so that the sheet blank is cooled from a starting temperature, which ensures the austenitization, to a temperature of between 450 C and 700 C so that despite the lower temperatures, a martensit-ic hardening takes place. This should achieve the fact that as little molten zinc as possible comes into contact with austen-ite during the forming phase, i.e. when stress is introduced, because the intermediate cooling that has been carried out causes the forming to take place at a temperature that lies below the peritectic temperature of the iron/zinc system. It should be noted that the cooling can be carried out with air nozzles, but is not limited to air nozzles, instead being equally usable on cooled tables or cooled presses.
9 The object of the invention is to further improve a method for the cooling and in particular, intermediate cooling, of a steel sheet for purposes of forming and hardening. The object is attained with a method having the features of claim 1. Advantageous modifications are disclosed in the dependent claims. Another object of the invention is to create an apparatus for carrying out the method. This object is attained by means of an apparatus having the features of claim 15. Advantageous modifications are disclosed in the
Азиатка показывает свое хрупкое тело а затем старательно ласкает мужской член чтобы довести до оргазма
Зрелая эстонка обнажается и мастурбирует дилдом
Катя уже достаточно зрелая женщина но она все еще чувствует себя сексуальной для фотосессии