Галерея 2937428
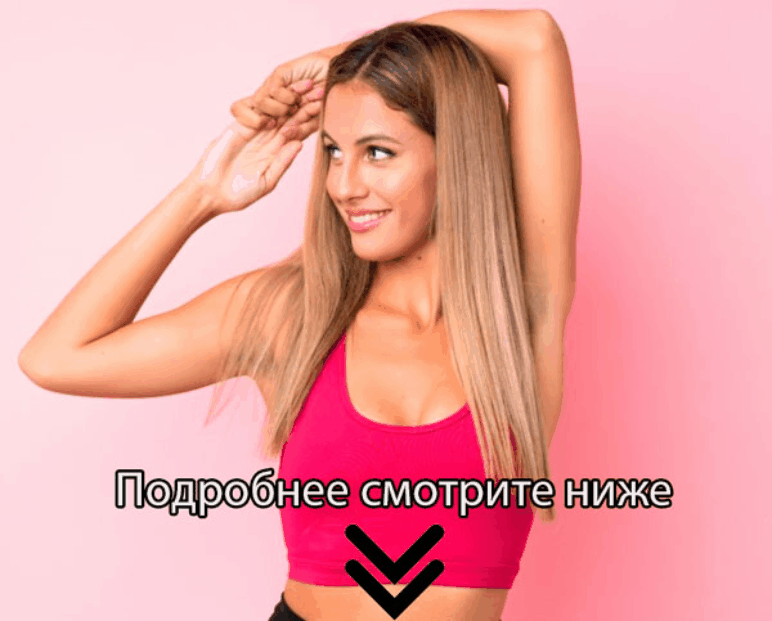
🛑 ПОДРОБНЕЕ ЖМИТЕ ЗДЕСЬ 👈🏻👈🏻👈🏻
Галерея 2937428
888.687.0539 |
225.706.4858
Caterpillar
Cummins
Detroit Diesel
Deutz
Isuzu
John Deere
Kubota
Northern Lights
Perkins
Westerbeke
Yanmar
Murphy Controls
Twin Disc
Starters and Alternators
Home
/
02937428
8784 S. Choctaw Dr. Baton Rouge, LA 70815
Privacy Notice
Terms of use
About us
You have no items in your shopping cart.
This item is a genuine Deutz part shipped with a 12-month factory warranty.
Do not hesitate to call us at 855.470.3523 if you have any questions about this item. As always, your satisfaction is guaranteed !
Join our newsletter and stay informed on current promotions and manufacturer updates
Caterpillar® and all of the Caterpillar® engine models listed on this website are registered trademarks of Caterpillar, Inc. Cummins® and all of the Cummins® engine models listed on this website are registered trademarks of Cummins. Detroit Diesel® and all of the Detroit Diesel® engine models listed on this website are registered trademarks of Daimler AG. John Deere® and all of the John Deere® engine models listed on this website are registered trademarks of John Deere. Allison Transmission® and all of their transmission models listed on this website are registered trademarks of Allison Transmission®. Diesel Parts Direct is not an authorized dealer for Caterpillar, Cummins, Detroit Diesel, John Deere, or Allison Transmission. None of the parts beginning with "DS" or "R" are genuine Caterpillar, Cummins, Detroit Diesel, John Deere, or Allison Transmission items.
For additional information on FMCSA regulations see their documentation
For information on valid Electronic Logging Devices (ELDs) and their requirements see ELD.report
State
AL AK AS AZ AR CA CO
CT DE DC FL GA GU HI
ID IL IN IA KS KY LA
ME MD MA MI MN MS MO
MT NE NV NH NJ NM NY
NC ND MP OH OK OR PA
PR RI SC SD TN TX UT
VT VA VI WA WV WI WY
All DOT numbers registered in OLATHE, CO
DOT.report is the most comprehensive up-to-date database of all known USDOT numbers. This page contains all freight carriers and commercial limo services that are registered in OLATHE, CO
Below you will find a field to search for a particular DOT number, as well as a list of USDOT numbers registered in OLATHE, CO. To find additional information on a number or company, simply click on the respective USDOT number or company name
Use of this information constitutes acceptance for use in an AS IS condition. There are NO warranties, implied or otherwise, with regard to this information or its use. Any use of this information is at the user's risk. It is the responsibility of user to evaluate the accuracy, completeness or usefulness of any information, opinion, advice or other content. EACH USER WILL BE SOLELY RESPONSIBLE FOR ANY consequences of his or her direct or indirect use of this web site. ALL WARRANTIES OF ANY KIND ARE EXPRESSLY DISCLAIMED. This site will NOT BE LIABLE FOR ANY DIRECT, INDIRECT or any other kind of loss.
HIGH COUNTRY BUILDING COMPONENTS LLC
FLETCH'S LANDSCAPING & EXCAVATION LLC
DUKE EXCAVATION & DIRECTIONAL DRILLING
JAKE'S CRANE SERVICE AND TIM'S CUSTOM CABINETS
DUKE EXCAVATION & DIRECTIONAL DRILLING
ALEXANDER PURDUM CONSTRUCTION SERVICE INC
THE DAVIS MANUFACTURING AND SUPPLY CO
May 24, 1960 Filed March 13. 1958 A. POCIDALO APPARATUS FOR MAKING A SOAP CAKE 3 Sheets-Sheet 2 INVENTOR.
ADOLPHE. Po c l DALO May 24, 1960 A. PQCIDALO APPARATUS FOR MAKING A SOAP CAKE Filed March 15. 1958 3 Sheets-Sheet 3 Figure 11 INVENTOR.
Avon-vae Po en cabo BY 59d', 'anm United States Patent O APPARATUS FOR MAKING A SOAP CAKE Adolphe Pocidalo, Cleveland, Ohio, assigner to Des Fleurs, Inc., Cleveland, Ohio, a corporation of Ohio Filed Mar. 13, 1958, Ser. No. 721,166
6 Claims. (Cl. 25d?) This invention relates to improvements in apparatus.
for making a soap cake enclosing indicia.
One of the objects of the present invention is to provide a machine which, when fed with a series of soap blanks, will automatically form an upper cake hal-f, a lower cake half, place a printed or otherwise formed indicia on one of those halves, on the side thereof towardthe adjacent half, and then press the two halves together so that a completed cake of soap is formed with indicia between the halves. It is intended that the soap be of a transparent character so that the indicia may be read in the completed cake but the character of the soap has practically nothing to do with the apparatus and method for making the soap cake.
Another and more specific object of the invention is to provide a rotatable indexing plate and a rotatable carrier wheel for forming the upper half of the soap cake and a like set of one indexing wheel and one carrier wheel for forming the lower half of the cake, together with common drive means for driving all of the rotatable wheels in timed relationship, separate ram means for forming the upper and lower cake halves respectively from soap blanks, separate ram means for operating a die cutting device for cutting and depositing indicia between the cake halves from a continuous strip of indicia, ram means for pressing the upper and lower cake halves together, and ram means for ejecting the finished soap cake from the machine, together with control means for operating all said ram means simultaneously and in timed relationship with said wheel drive means.
Other objects and advantages will be apparent from the accompanying drawings and description and the essential features thereof will be set forth in the appended claims.
In the drawings, Fig. 1 is a top plan View of an advertising soap forming and assembly machine embodying my invention; y
Fig. 2 is a sectional view taken along the line 2 2 of Fig. 1;
Fig. 3 isv a fragmental sectional view, enlarged, taken along the line 3-3 of Fig. 1;
Fig. 4 is a fragmental sectional view, enlarged, taken along the line 4-4 of Fig. 1;
Fig. 5 is a fragmental sectional view, enlarged, taken along the line `5 5 of Fig. 1;
Fig. 6 is a central sectional view, enlarged, taken through the shearing die head of Fig. 4;
Fig. 7 is a side elevational view, enlarged, of the rollup advertising tape index linkage mechanism takenalong the line 7-7 of Fig. 8;
Fig. 8 is a top plan view (diagrammatic) of the gear train which drives the machine, this gear train lying directly under the table top or base plate of Fig. l
Fig. 9 is a top view of the advertising soap product showing how the center paper of advertising material shows through the clear soap Surrounding it;
Fig. 10 is a cross sectional view taken along the line 10-10 of Fig. 9; l
Fig. 11 is a control diagram of the electrical and pressure iiuid actuating means for operating the machine.
To further explain the details of the machine mechanism and method of manufacturing the advertising soap, attention is called to Fig. 1. For the time being it will be assumed that the movements to be described are actuated by satisfactory actuating mechanisms later described. The left half of the machine in Fig. 1 will be described first. Starting in the upper left-hand corner of the drawing, the raw blanks or rough chunks of clear soap formula 1, are gravity fed down the chute 2. The soap blanks 1 are individually picked up from the gravity chute by the Y notched indexing wheel 3 by the notches 5. The left index wheel-4 revolves in a clockwise direction. The right hand indexing wheel 35 revolves in a counter-clockwise direction. The soap blankpick-up wheel is intermittently driven by the drive gears and power source shown in Fig. 8, which will be described later.
The cycle at the left half of the machine, Figs. l and 2, is that the clockwise rotating soap blank pick-up wheel 3 transfers the soap Iblank 1 as it rests on the under ange 4a of guide rail 4 to a position over one of the openings; 12 of the carrier star wheel 7. The operations thus far described can be more clearly understood by referring to the enlarged cross sectional view in Fig. 3. The soap blank is now rotated by the carrier wheel 7 continuing in a counter-clockwise indexing direction, as the soap blank 1 rides on the under slide surface 13, shown in Fig. 3. The carrier index wheel 7 transfers the soap blank 1 to a position under the first pressing ram 8, Fig. 2, and positions the blank 1 by gravity fall onto the bottom ram anvil 9 attached to lower hydraulic plunger cylinder assembly 10. Slide plate 13is cut away above anvil to permit the soap cake to drop, The ram 11 piston operated from cylinder 8 and the anvil plunger 9 piston operated from lower cylinder 10 come togetherl conning and compressing the soap in opening 12 and forming the soap blank 1 to lill the lower portion of the confining opening 12 in the carrier wheel 7. This operation forms the lower half of 'the soap cake. Plungers 1'1 and 9 withdraw from the mold cavity 12 leaving the Iformed half cake of soap sticking to the sides of the confined area 12.
The left carrier Wheel 7, next indexes the formed half cake under the advertising placement ram 14, Fig. 1. This station in the cycle can best be seen in Fig. 4, where printed advertising matter is on a continuous tape rolled on a reel 16, carried rotatably on shaft 16a and having a certain amount of spring frictional tension (not shown) exerted on the shaft which in turn is mounted in bracket 106 on table 6. A ratchet indexing wheel 17, has circumferentially spaced spikes 18 on its periphery which fit into mating holes in the tape 15. At the proper synchronized moment in the operational cycle, the ratchet linkage 19 is actuated by other moving parts of the machine not shown in this view. The linkage 19 pulls down on the ratchet and pawl assembly 20, to rotate the ratchet wheel 17 in a clockwise direction, pulling the advertising tape 15 under the shearing die head 14. VThe remaining selvage tape or Waste is rolled uponto reel 62, Fig. 4. The shaft 62a of this reel is driven by a light torque continuously driven motor 21 through a slip clutch (not shown) in the direction of the arrow of Fig. 4. The motor and clutch drive 21 is shown in Fig. 1 in the lower left hand corner of the View. The holes in the advertising tape 15, which mate with the sprocket spikes 18, can best be seen in Fig. 5, which is a sectional view of Fig. l taken in the direction of the arrows along the line 5 5. Further details of the paper shearing ram 14 are shown in Fig. 6. This view also shows how the tape 15 is guided under the die head 14, by right and left flanged rollers 22 and 23, respectively, as well as the upper and lower horizontal guide plates 24 and 25,
respectively. In this same Fig. 6 it can be seen by the dotted lines that when the die head 14, pierces through the tape 15, pushed down by ram 14a, the advertising piece 26, sheared through die plate opening a, is forced down onto the tacky surface of the formed half cake 1. At this point, lower ram 14b makes an upward stroke limited to just firmly engage the underside of half cake 1. Plate 13 is cnt away for operation of ram 14b upwardly.
The ram 14, having been retracted through the program timed cycle of the machine, not shown, the next operation in the cycle is performed.
Before describing this next operation, reference should be had to the right-hand half of Fig. 1. Here, the soap blanks 33, preferably about the size of a half dollar and about a quarter inch thick, are fed down the chute 34 to the indexing wheel 35 which receives them in notches 37. The indexing wheel rotates in a counter-clockwise direction by means later described and carries the soap blanks over a flange 36a like 4a and along the guide rail 36 to a position over one of the openings 32a in a carrier wheel 32 which is like wheel 7 earlier described. Slide plate 13a is directly beneath wheel 32. This carrier wheel rotates in a clockwise direction as viewed in Fig. l and carries the soap blank beneath a forming ram 39 which is exactly like the ram 8 previously described. Beneath this ram is another lower ram 40 exactly like ram 10 previously described. The blank drops through a hole in the slide plate 13a onto ram 40. Here the upper cake half is formed by the upper and lower rams meeting together while the soap is confined in one of the openings 32a so that an upper half of the cake is formed exactly like the lower half previously described. Further indexing of the wheel 32 carries the upper cake half to the center of the machine shown in Figs.` l and 2. Referring to the center of Fig. 2, the soap blank operational carrier wheel 7 carries the pressed lower half section of soap 1, with the advertising piece 26, adhered to its tacky top surface to the center station of Fig. 2. An upper half cake 33 arrives at the center station at the same time by the timing of the machine. At this operation in the program timed cycle, the upper and lower rams 27 and 28, respectively, of cylinders 29 and 30, come together within the contines of opening 12 in carrier wheel 7, pressing the two half sections of soap together. Plates 13 and 13a have openings for operation of rams 27 and 28. The upper ram 27, during this operation ejects the top soap section 33 from the cavity 31 of the carrier wheel 32 into the opening 12 of the carrier wheel 7 which at that movement is in direct vertical alinernent. The pressing rams 27 and 28 then withdraw to their respective retracted positions and the carrier wheels 7 and 32 index to their next respective positions, as indicated. Wheel 7 carries the finished product to a station beneath cylinder 41, shown in Figs. l and 5, where the ram 42 of cylinder 41 ejects the finished product through an opening in plate 13 into chtite 107 onto a moving belt 43, which carries the product away from the machine to further operations of processing and wrapping.
In Fig. l it may be observed that there are four rotating members above the surface of the machine table and super-structure 6. These rotating members are 3, 7, 32 and 35 and are driven by the gears 44, 45, 46 and 47, respectively, of Fig. 8 through shafts 44a, 45a, 46a and 47a. In Fig. 8 it can be seen that there are also intermediate gears 48, 49, 50, 51, 52 and 53, which interconnect the direct driving gears 44, 45, 46 and 47. The main drive gear 54 rotates at a constant speed through a drive motor 83, later described. Gear 54, in turn, intermittently drives gear 55, through a Geneva locking gear, commonly used in intermittent motion applications. Geneva gear 55 and intermediate gear 52 are keyed to the same shaft.
Another motion necessary to the main indexing functions of the machine may also be seen in Fig. 8. This is the linkage which operates the advertising tape ratchet wheel 20, shown in Fig. 4. Referring again to Fig. 8, the rotation of the Geneva drive wheel 55 also causes the crank 56 to actuate the arm linkage 57, at each rotation of the wheel 54. The movement of this linkage 57, and its function can best be understood by referring to Fig. 7, which is a side view of the mechanism of Fig. 8 taken in the direction of the arrows on line 77. As linkage 57 is pulled through its crank arm connection with Geneva gear 54, it rotates the bar 58, by way of crank arm 59, and double ball and socket linkage 60. The bar 58, in turn, oscillates through a sufficient angle to move the arm 61, attached to the linkage 19, which operates the ratchet 17. Arm 59, bar 58 and arm 61 are inter-keyed to move or oscillate as one unit.
In Fig. 1l a single phase, 110 volt-220 volt, 60 cycle current supply 64, commonly referred to as an Edison system, furnishes the electrical power to the machine. The operation of the machine is initiated by engaging the three blade knife switch 65. Current across the two outer lines 66 and 67 supplies 220 volts, while the current supply across the center conductor 68 to either of the outer conductors 66 and 67, respectively, is 110 volts. On engaging blade switch 65, with the supply lines 64, current is supplied to the air pump motor 69, through the conductors 66 and 67, across the normally closed contacts 70, of the relay 71, creating air pressure by way of the pump 74 into the air supply tank 75. Air pressure builds up in the tankl 75, creating pressure above the exible diaphragm 76, of the pressure switch 77. When the pressure builds up to a predetermined value, as shown by the gauge 78, and controlled by the reaction spring 79, air pressure on top of the diaphragm 76 forces the attached under switch 80 to close its contacts, thus supplying current from the left common supply conductor 66, through conductor 81 to the relay coil 73, and simultaneously to pilot light 82, completing the respective circuits and energizing the relay coil 73, and pilot light 82, through the common ground conductor 68. The air supply to the machine is now up to pressure and the pump motor stops by discontinuance of the supply current through contacts 70, which opened at the instant relay 71 was energized through coil 73. At the same instant, relay contacts 72 closed. The purpose of this function will be explained later.
The indicator pilot light 82 is now lit and the machine is ready to start.
The main drive motor 83 of the machine is started by pressing the start button 84. Pressing the start button 84 completes the circuit from the left conductor 66 to the relay coil 86, of the relay 87, by way of conductors S8 and 89 through the new closed contacts 72, of relay 71 to the common ground conductor 68. Contacts 90, 91 and 92 of relay 87 close on energizing the coil 86, of relay 87. The instant relay 87 is energized by pressing the start button 84, contacts 90, now being closed, furnishes a holding circuit from conductor 88 by way of the bypass conductor, across contacts and conductor 93, bridging the gap of the start button contacts 84. Relay contacts 91, now being closed, current is paralleled to relay coil 86 by also carrying the current to conductor 89 through t
Русская молодая женщина купальнике
Латиноамериканка вогнала в себя длинный искусственный член
Пьяная блондинка пизде не хозяйке