Галерея 2665118
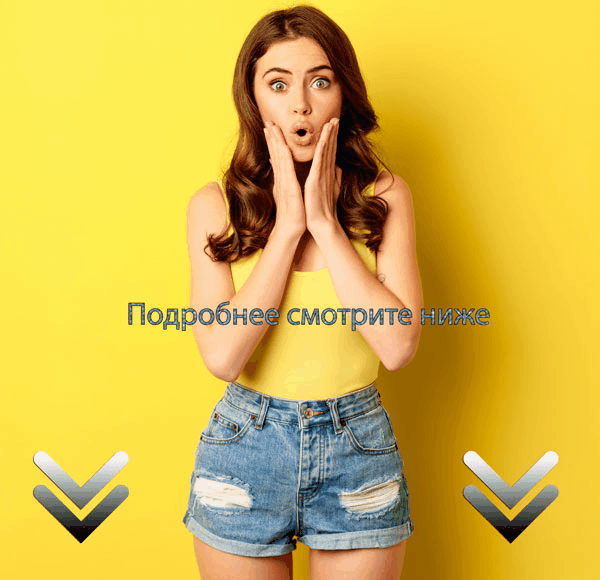
⚡ ПОДРОБНЕЕ ЖМИТЕ ЗДЕСЬ 👈🏻👈🏻👈🏻
Галерея 2665118
B. O. BROMAN Jan. 5, 1954 APPARATUS FOR CLEANING GAS SWEPT HEATING SURFACES 2 Sheets-Sheefll Filed June 2, 1949 INVENTOR 5.0.5/PaM/7/ ATToRNEYs Jan. 5, 1954 B. o. BROMAN 2,565,118
APPARATUS FOR CLEANING GAS SWEPT HEATING SURFACES Filed June 22, 1949 2 Sheets-Sheet 2 INVENTORY 5. 0. aka/v27,
W MVM ATTORNEYS Patented Jan. 5, 1954 APPARATUS FOR CLEANING GAS SWEPT -HEATING SURFACES Bror 010i Broman, Stora Essingen, 'Sweden, "assignor to Aktiebolaget A.-Ekstroms Maskinaffar,
Stockholm, Sweden Application June 22, 1949, Serial No. 100,645
Claims priority, application Sweden January 19, 1949 11 Claims.
This invention relates to a methodand an apparatus for cleaning, during operation, heating surfaces swept by air or gas by using sand, fine gravel, granulated metal particles (particularly steel shot) or similar solidparticles which are caused to drop by gravity on the heating surfaces, their falling speed in some cases being increased on account of the velocity of the gas along the surfaces, the particles, however, never being directly blown against the heating surfaces by the action of compressed air or the like.
Tests have established that in order to obtain the highest practical effect, the cleaning operation in accordancewith this invention must be continuous. For this purpose a fixed portion of solid particles (for example steel pellets) which may be relatively small, is, by means of suitable arrangements, causedto circulate throughthe apparatus to be cleaned. The steel pellets or particles may also be cleaned during the circulation, possibly by washing, be dried and :even cooled in order to save the transportdevices.
For cleaning gas-swept heating surfaces for instance in boilers and economizers during operation blowing with steam or air iswidely used.
In certain cases, especially for economizers and air pre-heaters heated with combustion gases from soda furnaces in cellulose plants the heating surfaces are cleaned during operation by means of water or some alkaline solution sprinkled or flushed thereon.
The above-mentioned cleaning methods suffer from serious disadvantages.
When blowing with steam or air, the costof the requisite apparatus is relatively high, and the costs for steam'and compressed air are also quite considerable.
The sprinkling with water or some alkaline solution entails risks to the heatingsurfaces on account of the resulting considerabletemperature stresses which in many cases cause considerable damage to the constructions in a relatively short time.
When cleaning is effected by means of water, air or steam, it is necessary as a minimum to effect a cleaning operation once every eighth hour i. e. three'times during each period of 24 hours in continuous operation of the plant.
It has further been suggested to employ sandblasting, i. e. injecting solid particles with .the aid of compressed air. However, in practice this method has not proved acceptable as the heating surfaces become damaged by the sandblasting.
The general object of this invention is therefore to provide a method of cleaning gas-swept 2 heating surfaces of-a heat plant during operation at lowcosts and'without any risks-of damagingthe heating surfaces or any other parts of the plant by using solid cleaning particles which are circulated through the plant andare caused to drop against the surfaces to be cleaned.
' A further object of the invention is to provide apparatus by which the cleaning particles are circulated through the plant and caused to fall against the surfaces to be cleaned.
A still further object of the invention is to provide distributing means for spreading the cleaning particles over the surfaces to becleaned in a predetermined manner prior to their falling steel pellets and Figs. 6 and 7 show corresponding views of another embodiment of such distributor.
As regards the drawing, Figure l discloses the invention with reference to heat interchanging apparatus that are associated with the boiler plant. The apparatus includes a casing l embodying side walls and a top-wall. An upper gas inlet l communicates with the casing through a side wall thereof at an area adjacent the top wall-and a lower gas outlet 1 communicates with the casing adjacent the lower extremity thereof. Within the casing are arranged tube means through which fluid passes for heat exchanging relationship with the gas that flows through the casing. The tube means include a preheater 2 for preheating primary combustion air, an economizer 3 consisting of spaced banks of tubes extending through the casing a horizontal relationship and a preheater 4 for secondary combustion air. These respective tube means are mounted vertically above one another. Above the casing is a container 5. This container at its lower endcommunicates through cated generally at 1 is secured to the bottom end of the hollow shaft and, as apparent from Figures 4 to 6, this rotary distributing member has an outer contour of spiral form that extends from the vicinity of the center rotation thereof outward toward and terminates at its greatest radius. An electric motor 8 and suitable gear means rotates the hollow shaft that supports the rotary distributing member "I so that solid cleaning particles, for instance shot pellets, are effectively distributed within the casing above the tubes and spread throughout substantially the cross-sectional area of the casing so that they fall by gravity and cascade through the casing to impact and ricochet against the surfaces of the tubes to pick up material accumulated thereon and to dislodge material therefrom so as to clean the tubes. Beneath the casing and thus beneath the gas outlet are means for collecting the cleaning particles which includes a conduit 9 constituted by a return pipe connected to the container at one end and its other end is in communication with a fan It] that blows air through the conduit or pipe 9 for returning the particles to the container 5 so that continuous circulation can be maintained.
In the embodiment according to Fig. 2 a screw conveyor Ii and a bucket carrier l2 are substituted for the return pipe, but otherwise the apparatus is analogous to and operates in the same manner as the one according to Fig. 1. In the apparatus according to Fig. 3, the path of the gas from a boiler I3 through the apparatus is indicated by arrows, and the velocity of the flowing gas will contribute to the acceleration of the speed of the cleaning particles.
Figs. 4 and 5 show an embodiment of a distributor member. The numeral i l designates the hollow shaft for feeding the cleaning particles, to which a plate 'I is secured, the contour of which follows a spiral line, said plate being provided with radial ridges l5. The purpose of this device is to bring about an even distribution of the cleaning particles over the cross section of the apparatus located underneath. On the plate, directly under shaft [4 a wear resistant plate I6 is arranged, having sloping sides in order to prevent the cleaning particles from collecting in a heap below the shaft; instead it is immediately shoved out to the periphery of the plate.
The plate 16 is made of particularly wear-resistant material to insure long life of the distributor member. The plate forming the base of distributing member 1 extends transverse to the axis of the shaft l4 and is in spaced relation with respect to the lower end of this shaft. The vanes l5 that extend radially of the hollow shaft from the shaft toward and terminate at the outer marginal edges of the plate are substantially equispaced and of unequal length as shown in Figure 5.
Another distributing member for the same purpose is shown in Figs. 6 and 7 and consists mainly of two more or less conically shaped plates I! and I8, arranged above each other and held together by radial walls and stays. The plates have a spiral-like, outside contour and the upper plate ll is provided with an inlet 19, eccentrically fastened to the pipe [4. The eccentricity being adjustable, the desired distribution characteristics of the steel particles is attained in operation. Right below the inlet I9 is disposed a plate 20, having sloping sides and made of wear-resistant material to minimize the effect of wear and tear caused by the particles.
In the arrangement of Figures 6 and 7, the distributing member, as indicated, includes a collar constituting the inlet I9 and the conically shaped plates I1 and [8 each have the aforedescribed spiral contour and the plate 18 is smaller than the plate ll. Radial vanes l5 arranged similarly to the vanes [5 of Figures 4 and 5 extend between the plates from the outer edges thereof toward and terminate adjacent the collar. The uppermost plate has an aperture therein at its apex and the insert 20 of wear resistant material is mounted in an aperture in the lowermost plate that is in alignment with the aperture in the uppermost plate.
In order to limit the free fall of the particles, groups of spaced rods I extend between the walls of the casing above the tubes to be cleaned but in spaced relation beneath the distributing member.
It is therefore clear that the solid cleaning particles are continuously fed to the distributing member and effectively distributed throughout the entire cross-sectional area of the casing so that they fall downwardly therethrough in the same direction as the gas flow striking the outer surface of horizontally arranged tubes and passing between the tubes of nests of tubes and thus internally of the vertically arranged tubes of the preheater 2.
The cleaning particles may be introduced by means of a low-speed air blow or blast, but no real sand-blowing effect may be directed towards the heating surfaces proper.
The method according to the present invention has proved most valuable especially when the gases carry a large percentage of solid matter, or when said matter is of a sticky nature, causing injurious coatings on the heat surfaces, or when the gases contain substances which chemically attack these surfaces. Besides, the apparatus according to this invention is less expensive, both as to cost and operation, than the methods and apparatus heretofore used for the purpose.
From practical tests according to the invention, when using steel pellets, it has been established that the height of free drop of the solid particles should preferably not be too long. For this purpose, for instance, one or more sets of rods may be arranged, preferably above the topmost set of tubes in the boiler, to prevent the pellets from falling directly on the tubes. For different tubes, the height of free fall for the particles of pellets has different maximum values. In some cases it should not be more than 250 mm. above the topmost group of tubes to break the fall. The size, shape and weight of the particles also have influence upon the cleaning effect, imparted to the heating surfaces.
Having now described my invention, what I claim as new and desire to secure by Letters Patent is:
1. In heat interchanging apparatus, a casing including side walls and a to wall, an upper gas inlet communicating with the casing through a side wall thereof adjacent the top wall and a lower gas outlet communicating with a side wall of the casing, tube means within said casing and through which fluid passes for heat exchanging relationship with gas flowing through the casing, a rotatable hollow shaft projecting through the top of the casing and terminating above the tube means therewithin, a rotary distributing member secured to said hollow shaft and said member having an outer contour of spiral form extending from the vicinity of the center of rotation thereof outward toward and terminating at its greatest radius, means for feeding solid cleaning particles into the hollow shaft so that said particles are distributed within the casing above the tubes and spread throughout substantially the crosssectional area of the casing to fall by gravity and cascade through the casing and impact and ricochet against the surfaces of the tubes to pick up material accumulated thereon and to dislodge material therefrom to clean the tubes, and means beneath the casing and beneath the gas outlet to collect said cleaning particles after they have passed through the casing.
2. In heat interchanging apparatus as defined in and by claim 1, in which said rotary distributing member is eccentrically and adjusta-bly secured to said hollow shaft.
3. In heat interchanging apparatus as defined in and by claim 1, in which said rotary distributing member is fixedly secured to said hollow shaft comprises a plate extending transversely of the axis of the shaft and in spaced relation with respect to the terminal end of the shaft, said plate having the said outer contour of spiral form extending from the vicinity of the center of rotation of the shaft outward toward and terminating at its greatest radius, and vanes mounted on said plate and extending radially of said hollow shaft from the shaft to and terminating at the outer marginal edge of the plate, said vanes being substantially equi-spaced and of unequal length.
4. In heat interchanging apparatus as defined in and by claim 3, in which said plate is of wear resistant material to minimize wear occasioned by the movement of the cleaning particles relative to the plate.
5. In heat interchanging apparatus as defined in and by claim 1, in which said rotary distributing member includes a collar, vertically spaced plate members carried by the collar and having said spiral outer contour, said plate members further having conical shape in cross-section and the lowermost plate being smaller than the uppermost plate, radial vanes extending between the plates from the outer edges thereof toward and terminating adjacent the collar, said uppermost plate having an aperture therein at the apex thereof surrounding said collar.
6. In heat interchanging apparatus as defined in and by claim 5, in which the lowermost plate has an aperture therein at the apex thereof and an insert of wear resistant material disposed in said aperture to minimize wear occasioned by movement of said particles relative to said plate.
7. In heat interchanging apparatus as defined in and by claim 1, and further including particle receiving means disposed above said casing and conveying means extending between the collecting means and said particle receiving means to convey particles from the collecting means to the receiving means and conduit means connecting said receiving means with the said feeding means.
8. In heat interchanging apparatus as defined in and by claim 1, and groups of spaced rods supported within the walls above the tubes and spacedly beneath said distributing member to limit the height of free fall of the cleaning particles.
9/Means for cleaning gas-swept heating surfaces of heat interchanging apparatus, which apparatus is of the type embodying walls defining a casing and means providing heat exchange surfaces within the casing and gas inlet and outlet means communicating with the casing, comprising a rotary distributing member disposable within the casing directly above the surfaces to be cleaned, said member having an outer contour of spiral form extending from the vicinity of the center of rotation thereof outward toward and terminating at its greatest radius, and means for feeding solid cleaning particles to said distributing member so that the particles are simultaneously introduced within and spread throughout substantially the cross-sectional area of the cas ing directly above the surfaces to be cleaned.
10. A rotary distributing means for simultaneously introducing and distributing solid cleaning particles within the walls of a casing of a heat interchanging apparatus and above the heat exchange surfaces within the casing that are to be cleaned, comprising a hollow rotatable shaft and 1 cans providing rotary distributing surfaces extending transversely of the axis of the shaft and having an outer contour of spiral form extending from the vicinity of the center of rotation of the shaft outward toward and terminating at the greatest radius of said member, spaced radial vanes extending inwardly from the outer edge of said transversely extending means toward said shaft, and means securing said transversely extending means to said hollow shaft.
'11. A rotary distributing means as defined in and by claim 10, in which said last mentioned means adjustably eccentrically secure said transversely extending means to said hollow shaft,
References Cited in the file of this patent UNITED STATES PATENTS Number Name Date 1,613,638 Altimari et a1 Jan. 11, 1927 1,795,348 Schmidt Mar. 10, 1931 1,916,337 Schmidt July 4, 1933 2,379,195 Simpson et al June 26, 1945 2,468,712 Kohler Apr. 26, 1949 FOREIGN PATENTS Number Country Date 587,774 Great Britain May 6, 1947
US2665118A
true
US2665118A
( en )
US100645A
Expired - Lifetime
US2665118A
( en )
Apparatus for cleaning gas swept heating surfaces
US2733550A
( en )
*
US2761652A
( en )
*
Device for cleaning gas-swept heating surfaces in heating apparatus and the like
US2765588A
( en )
*
Device for uniform distribution of material over a horizontal cross-sectional area of a vertically extending zone
US2792316A
( en )
*
Method for cleaning gas-swept heating surfaces
US2836398A
( en )
*
Regenerative heat exchanger for gas turbines
US2946669A
( en )
*
Chemical and heat recovery apparatus
US2970815A
( en )
*
Regenerative heat exchanger for gas turbines
US2978378A
( en )
*
Method and apparatus for cleaning heat exchange apparatus connected to receive flue gases from soda recovery-boilers
US3726045A
( en )
*
US3778938A
( en )
*
Method for decontamination of surfaces of nuclear reactor components
US3831326A
( en )
*
US3894364A
( en )
*
Method of cleaning nuclear power plants
Анальная групповуха с двумя красивыми блядями
Интимные фото итальянки Сары
Девушка трахается как бревно