Галерея 2635263
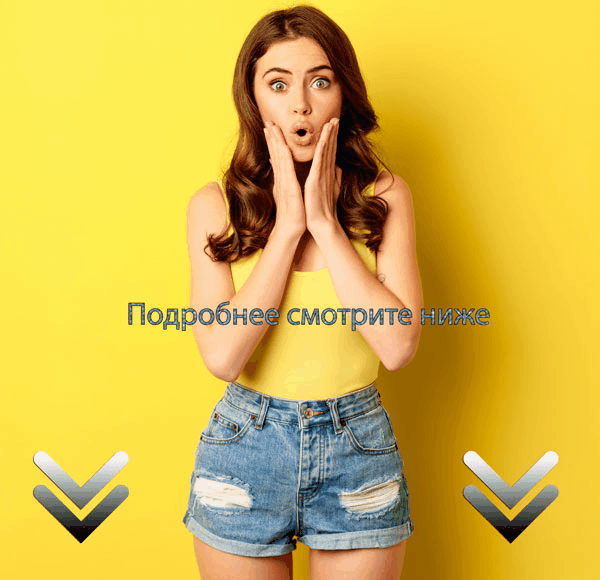
🛑 ПОДРОБНЕЕ ЖМИТЕ ЗДЕСЬ 👈🏻👈🏻👈🏻
Галерея 2635263
Hierzu gibt es keine Street View-Bilder.
Hierzu gibt es keine Street View-Bilder.
A ril 21, 1953 A. s. CLARK 2,535,263
- MACHINE FOR OPERATING UPON INSOLES Filed April 18, 1951 5' Sheets-Sheet 1 A. s. CLARK MACHINE FOR OPERATING UPON iNsoLEs April 21, 1953 5 Sheets-Sheet 2 Fi d A pri1l18, 1951 lfz venzm Alfred S. Clark By )2's April 21, 1953 A. $.CLARK 2,635,263
- y MACHINE FOR OPERATING UPON INSOLES I Filed April 18, 1951 s Sheets-Sheet 4 ln verz'z0w. Alfred 5'. Clark Anril 1, 1953 A. s. CLARK 2,635,263 v MACHINE FOR OPERATING UPON INSOLES Filed April 18, 1951 5 Sheets-Sheet 5 Ty]. R
Patented Apr. 21, 195 3 MACHINE FOR OPERATING UPON INSOLES Alfred S. Clark, Beverly, Mass, assignor to United Shoe Machinery Corporation, Flemington, N. J., a corporation of New Jersey Application April 18, 1951, Serial No. 221,576
This invention relates to machines for operating upon insoles and is illustrated herein with reference to machines for attaching ribbed strips to insoles to provide sewing ribs thereon.
In machines of the type referred to, a preformed ribbed strip is pressed against the outer surface of an insole on a support to attach the strip adhesively to the insole and thereby provide a rib on said surface suitable to serve as a sewing rib in constructing a welt shoe. These machines usually operate progressively around the periphery of the insole, similarly to an insole channeling machine, and the ribbed strip is located relatively to the marginal portion of the insole by a gage which engages the edge face of the insole and positions it laterally on the support relatively to the attaching and feeding mechanism. Since the sewing rib on a Welt insole is normally located at different distances from the edge face of the insole at diiierent portions thereof, for example, at the shank portion, the forepart or ball portion and around the toe or tip portion, the edge gage in a machine of the type referred to must be shifted relatively to the attaching mechanism to produce the desired results, that is, the variations in the position of the ribbed strip or rib widthwise of the insole margin at the different localities indicated. These variations in the position of the sewing rib on the insole are necessary to produce different widths of insole margin or feather portion at these different localities around the insole which, in turn, are desirable to facilitate the lasting and subsequent peripheral operations on the shoe, and also to produce a properly lasted and well constructed shoe.
The shifting of the edge gage in machines of this type is usually accomplished manually by the operator by means of a handle associated with the edge gage mechanism. Since the lateral position of the sewing rib is usually changed at five different places around the periphery of an insole, the operator must shift the edge gage four or five times when operating upon each insole. He must also hold the insole and guide it through the machine, taking care to keep it against the edge gage at all times. Since the insoles are fed through these machines at a relatively high rate of speed, it will be seen that the operator must be constantly alert and quick to shift the gage at the proper points around This sometimes causes fatigue which results in imperfect or defective work. Moreover, even though the op erator is giving his entire attention to the work' being operated upon, the shifting of the edgegage in this manner is still subject to variations or errors in timing or judgment so that all insoles of a particular size or style do not usually have exactly the same widths of insole margins or feathers at all portions thereof because the operator does not always shift the edge gage at exactly the same point on each insole operated upon.
An important object of the present invention is to provide a machine of the type referred to in which the position of a ribbed strip or sewing rib on the margin of an insole is determined or controlled in a manner to produce insole margins or feather portions which will be exactly the same for all insoles of the same size and shape operated upon.
To this end, the invention provides, in accordance with one feature, an improved ribbed strip attaching machine having, in combination, means for attaching a ribbed strip to an insole, a member for holding the insole having means thereon indicating the desired position of a sew ing rib on the insole, and means cooperating with said member for locating the ribbed strip in said desired position. As herein illustrated, the member for holding the insole comprises a template having a recess or depression therein for receiving the insole and holding or supporting the insole during the attaching operation. According to the present invention, the template is also provided with a surface or groove located in predetermined relation to the desired position of a sewing rib on the insole.
The means, in the embodiment of the invention illustrated herein, which cooperates with the holding means or template in positioning the ribbed strip on the insole comprises a pin or roll normally fixed relatively to the rib attaching means and adapted to engage the surface or groove in the template and thereby determine or control the position in which the ribbed strip will be applied to the margin of the insole. The ribbed strip attaching mean in the illustrated machine, as is usual in machines of this type, operates to press the ribbed strip intermittently against the insole and simultaneously to feed the combined insole and strip progressively through the machine, the insole being normally supported during this operation by a rotary table or support. Consequently, when the insole is mounted in the holding means or template referred to, the attaching and feeding means operates to feed the insole and template progressively across the support as the ribbed strip is being pressed against the outer or exposed surface of the insole. The cooperating means or pin referred to, being in engagement with the groove or surface on the template, thus causes the latter to move in a predetermined path, thereby determining or controlling the position of the ribbed strip relatively to the edge face of the insole. Since the surface or groove bears a predetermind relationship to the desired position of a sewing rib on the insole, the ribbed strip will be attached to the insole in such position or relationship. Moreover, every insole operated upon of the same size and shape will have exactly the same insole margin r feather portion because there can be no variations in the foregoing mechanical control of the insole and strip as there can be in the manual operation of the edge gage mechanism in machines used heretofore.
With the above and other objects and features in view, including improved means for varying the entire width'of the margin or feather portion' of th'e' 'insole uniformly throughout the entire periphery of the insole while maintaining the predetermined relationship'of the ribbed strip to the different portions of the edge face of the insole referred to above, the invention'will now be" described in "detail in connection with the accompanying drawings and will thereafter be pointed out in the claims.
Fig. 1' is a front elevation of the upper portion of a machine embodying the'present invention;
'Fig. '2 is an enlarged perspective view of the operating elements of the machine operating up- (in-an insole;'
Fig. 3- isa front elevation, partly broken away and in section, of the operating elements in the act-ofatt'ach'ing a ribbed strip to the insole;
*Fig-llfis'a plan view of the mechanism shown in Fig. 3 with the rib-bed member omitted? Fig.6 isa plan view of the sole-shaped template of the present invention holding an insole to 'which a ribbedstrip has been attached;
*Fig. 6' is a plan View of the opposite side of the template; and
*Figsfl, 8 and 9 are enlarged sectional views of the template and insole taken respectively on the lines VIIVII, VIIIVIII and IX IX of The invention is illustrated herein, by way of example, as embodied in a machine for forming andattaching ribbed strips'to insoles to provide" sewing ribs thereonythe machine illustrated hereinbeing of the type disclosed in 'my'copending application Ser. No. 175,174, filed July 21, 1950. It'should be understood, however, that the invention is not limited in its utility to embodiment in a machine of this particular type since it obviously could be used advantageously in other machines for operating upon insoles such, for example, as insole channelin and insole reinforcing machines. As disclosed in the applica tion referred to, the ribbed strip forming and attaching machine illustrated in Fig. 1 is provided with a' frame or head 2Q upon which is mounted ribbed strip forming and attaching instrumentalities, the strip forming instrumentalities including mechanism not shown herein for folding and otherwise shaping a single strip of tape into a tape rib or strip such as that illustrated in Figs. 3, and '7 to 9, inclusive, this strip forming mechanism being fully disclosed in my copending application.
The machine is also provided with ribbed strip strip and the pressing attaching and feeding means consisting in part of a unitary pressing member or foot made up of two independent spring-pressed elements '22 and 23 (Figs. 3 and 7) arranged to press the ribbed strip intermittently against the margin of an insole to attach the strip adhesively thereto and being actuated by continuously operating mechanism indicated generally in Figs. 1 and 2 by the numeral 25, this latter'mechanism being driven from a motor by a pulley 26 and being under the control of the operator through a treadle connected to a treadle rod 28 (Fig. 1). The ribbed strip forming and attaching machine is also provided with various other mechanisms 01" meansfor adapting the machine particularly to perform the desired operation upon the insole and ribbed strip, these mechanisms including a stationary strip guide 36 (Figs. 1 and 2) for guiding the preformed ribbed strip onto the insole, and a pair of measuring fingers or feelers 3; for automatically controlling theliigth o'f th'e ribbed strip applied to the insole. Since the coiistru'c tion and operation of'th'e'se various 'mecha'n' are fully disclosed in" the cop-ending 'appiicatr n" referred to above, no detailed descriptionof'siich mechanisms will be giveri' herein'except as" be necessary to insure aprdp'erunderstan ng of the present invention. 7 The machine is furth'e'rprovided Witha rotary support 3A which is dried against height movement during the cante nses th but is adjustable heightwis ebya FE. ya for operating upon insoles whicl differ co cler'f ably in thicknesses. T hesup-portfii cg 'n circular table provided at its' outer 'edge with a; depending wall 35 and-being"rotatably'nioun by means of a central shaft 3 6 mare p N of a casting'BB carried byth'e'frame 20; and ha ing a circular boss il formed at'its'upper receivingthe table. A bail bearingylg posed between the boss tllfand the 'd pen wall 35 of the table tofacilitaterota ror i latter. The rotation of tl efs'upportfor"tabl may be controlled, however, by, meansgofa f tion device 44 securedtd the casting 38,,by screw 56 and urged toward; the support"by. ajj. spring ts surrounding aiscrew 56 whereby the tension of the spring may be; adjustedrto jva the pressure of the device against fh In this way rotation of the support tarded as much as desired. As application referred to, the":unitary press 22, '23 is caused by thefc'onst'af lyfop mechanism 24 to press a ribbed in tently against the surface "of anfi nso rest the support 34 to attach'thest 'o'tothf' by reason of pressure-respons' cement (will 11 has been previously applied 1:611: e': the attaching face of means, tnep'res "e 22, 23 being also arranged throughi ts op mechanism to feed the combinedinsole,and's progressively across the upper surface of the ,su port simultaneously with impressing operat In the machine of the applicationftheun is guided on the support during thepre ss feedingoperation by means'of ane'dge ga ot f shown) arranged to engage the edgefa ce of th insole at the right handsi'de of the 'supp'ortfasf viewed from the front of the machine 'Z Fig". "1): and thereby to determine'or' control the lateral position of the ribbed strip relatively to the in gin or edge face of the insole while thje strip "is being attached to said margin. Thedgegagef shown in the application is of the type disc in Letters Patent" of the"United States 2,326,119, granted August 10, 1943, on an application filed in the name of Frederick E. Bertrand. This edge gage, as disclosed in the patent, is under the control of the operator by means of a handle which permits the gage to be shifted into three different predetermined positions to vary the lateral position of the ribbed strip relatively to the edge face of the insole at five different portions or sections of the insole around the periphery thereof. This manual control of the edge gage is customary practice in machines of this type and in some other types of insole machines, for example, insole channeling and reinforcing machines. The locations at which the lateral position of the sewing rib is usually changed relatively to the edge face of the insole around the periphery thereof are at the shank portion, at the sides of the forepart and around the toe portion.
The operator usually places the insole on the support or table of the machine with his left hand and starts the attachment of the ribbed strip at substantially the heel breast line so that the widest margin or feather of the insole will be located at the shank portion. After passing through the shank portion of the insole, the operator moves the edge gage inwardly toward the support with his right hand while passing around one side of the forepart of the insole, thereby producing a narrower margin or feather at this portion. He moves the edge gage outwardly into its third position when passing around the toe portion of the insole in order to increase the insole margin or feather a small amount over what it was at the forepart. He then reverses this procedure when passing around the opposite or second margin of the insole until the attaching operation terminates at substantially the heel breast line at this second margin.
It will be seen that this operation requires the constant attention of the operator who must be quick and accurate in shifting the edge gage because the insole travels at a relatively high rate of speed through the machine. Moreover, the operator is not only obliged to shift the gage quickly with his right hand but, as indicated above, he must also hold the insole and assist in guiding it through the machine with his left hand. Consequently, the continued operation upon a large number of insoles or for a long period of time is apt to produce fatigue which may result in imperfect or faulty work. Another factor to be considered is that some shoe manufacturers desire to have the sewing ribs on their insoles located in exactly the same lateral position on every insole of the same size and shape. In other words, they require what are sometimes referred to as predetermined insole margins which, in insoles having ribbed strips or tapes attached thereto for sewing ribs, means that the ribbed strip on every insole of the same size and shape must be located in exactly the same lateral position around the entire periphery of the insole, including the areas referred to where the widths of the insole margins or feather portions normally change, that is, at the shank portion, the sides of the forepart and at the toe portion, this exactness applying, of course, to both margins of the insole. Such accuracy is practically impossible in a manually controlled mechanism where the changes in the lateral position of the sewing rib depend primarily upon the speed and skill of the operator even though, for ordinary purposes and in many cases, manual control of the insole margins is satisfactory because minor 6 variations in the position of the sewing rib in such cases are not important.
In accordance with the present invention, the position of the ribbed strip or sewing rib relatively to the insole margin or edge face is determined or controlled by mechanism which is adapted to provide so-called predetermined insole margins which will be exactly the same for every insole of the same size and shape operated upon. In other words, the present invention provides mechanical means, rather than manual, for automatically determining the position in which a ribbed strip will be attached to the insole in a machine in which the rib or strip is applied by a progressive or step by step action around the periphery of the insole as distinguished from a machine in which the sewing rib is applied to, or formed on, the insole by a single pressing or molding operation with the aid, for example, of a matrix, mold or other pressing implement.
In accordance with the present invention, the position of the ribbed strip relatively to the margin or edge face of the insole is determined or controlled in the machine by the following mechanism. A fiat plate or template 52 is provided for holding and supporting the insole during the strip attaching and feeding operations, this template, as illustrated in Figs. 2, 5 and 6, conforming generally in outline to the shape of a sole member and being preferably relatively thin, for example, one quarter to three-eighths of an inch thick. It may be composed of metal such as iron or steel or it may, if desired, be composed of aluminum or similar material. The upper surface of the template 52 has a depression or recess 54 formed therein which conforms accurately in outline to the shape of the insole to be operated upon, the depth of this depression being substantially equal to the thickness of the insole so that the latter will fit into the depression and be held therein with its upper surface substantially flush with the top face of the template, as illustrated in Fig. 2, the insole shown in that figure being designated by the letter A.
The bottom surface of the template 52 is provided with a cam groove or slot 56 which, as illus trated in Fig. 6, is relatively narrow in width and extends around the marginal portion of the template in a position which is located in accordance with the desired position of a sewing rib on the insole mounted in the depression 54. In other words, the groove 55 is so shaped and positioned in the template that it corresponds accurately to the position in which it is desired that the ribbed strip should be attached to the insole A mounted in the depression 54 in the opposite side of the template. Since the groove 56 is located in a position which corresponds to that desired for the ribbed strip on the insole, it will of course be located in a predetermined position relatively to the margin or edge face of the insole so that it can be used, as will presently appear, to determine or control the position in which the ribbed strip will be attached to the insole with particular reference to the relation of the ribbed strip to the edge face of the insole at the different regions referred to above, namely, the shank portion, the sides of the forepart and the tip or toe portion. At its opposite ends the sides of the groove 56 are flared outwardly, as shown in Fig. 6, to provide enlarged openings at these ends to facilitate the use of the template. The depth of the groove is preferably about one third the thickness of the template although this may be varied as circumstances require. Fig. 6 shows predetermined insole margins.
the position of the groove ttrentivery tame edge face of-the template- 52 and-also with respect-to the shape of theclepression 54 in. the opposite side of. the template. It will be observed. in that-fig.- ure that the groove bears a diii
Толстый хуй не помещается в пизде Алексии
Молодая сучка из Эквадора ебется с приятелем
Рыжая девушка разделась в прихожей до гола