Галерея 1777023
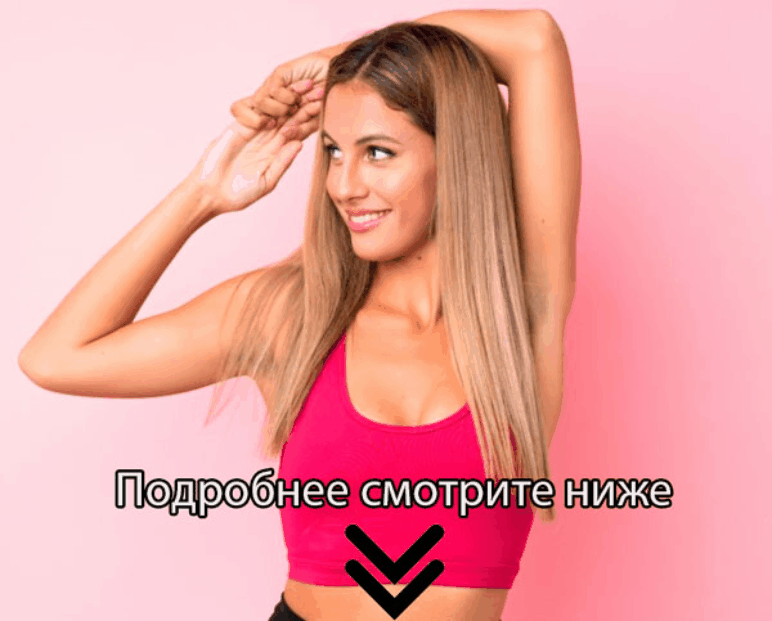
⚡ ПОДРОБНЕЕ ЖМИТЕ ЗДЕСЬ 👈🏻👈🏻👈🏻
Галерея 1777023
Sept. 30, 1930. E. WILDHABER 1,777,023
Filed AApril 6, 1927 2 sheets-sheer 1 r- 5f eillriuiruls.'
, J 65 es Y TYP( f 6 )VT/XK l 18 i] l. 4+ 2z l sept. 3o, V193:0. E, wlLDHABER 1,777,023
ROTARY ENGINE Filed April 6, E192? sheets-sheet 2 FIG@ . INVENTOR Patented Sept. 30, 1930 fren-ESTATES *PATENT :oFFeicE ROTARY ENGINE J Apiiication mea Api-ii e; ifea?. seriai 'Na iaiss.
a Thelpreseiit invention `relates to rotary enl igines, and especially to turbines using a compressible medium, suoli as `for instance steam orcombustion gases. Y vOne purpose of the present invention is to devise aiiio'vel and eiiicient arrangement of `geared turbines. lAnother object is to provide a turbine having a plurality of rotors mounted on parallelaXes and-containing a `minimum internal resistance. A further "objectais to provide afturbinehaving a plurality of rotors mounted on parallel axes and provided with velocity stages, iii-which no stationary blades are provided intermediate ls-the movabley blades. VVelocity stages, :some-` times calledf'Curtis Istages, areknown to contama' plurality `ot ringsof` blades movable in unison with each other and utilizing the lziiietic 'energy of the inediumwhile main- 1 `taining the pressure oi the medium the same beforeand after itpasses'through said` plul Qrality of ringsofblades. In standard practice, stationary blades are disposed inter`l` mediate adjacent rings of inovahle blades."I The said stationary-bladesare known to con# sinne much energy and to reduce the e'fiiciency or the velocity stages. An object of the present'inveiition is to do away with these latter losses andv to raise the efficiency of Velocity Hostages to-a much higher level', by providing movableblades only,"adjacent rows of blades` `moving in opposite directions.
Other ObjeCtsWill be apparent in the speci-' a .ication and fr'oin reciting the appended :i5 claims.v l
` My invention is illustrated by way of exaainples in the'accompanying drawings, in
which Figfl isa somewhat simplified plan' view l0 of a ygearedV steamturbine constructed in accordance `with thez'present invention, with npart ofthe upper cover removed and showing ithe rotors partly in' axial section.
FigJQ is a sectional view'ofthe sa sectioni-beingwtalzen along lines A-A` of "Fig v3l is'a side view of the geared steam 1 turbinetshown in Fig. l.
. FigMl-is afschematic plan view of another form'o; steam-'-or `gas turbine constructed rotors, the
according to the piiesentlinvention, with the upper cover removed andl showing the rotors in axial section.
5 is a diagram"-explaiiiiiigftliel preferred''arrangement when rotors areprovided.
Fig. G is a diagrammatic plan view, partly more than twoa a section, ot another form of steam turbine 'constructed' according to the present' inveii- "ance "with tlief present invention. a `Fig. 9 is a developed section through rotary bladesysimilar to vlil-ig. 8,'.sliowing however a modified arrangement.
Fig.V l() and Fig; l1 are velocity diagrams for explaining Ythe inclinations o i' the blades shown: in Fig. 8 and F ig. 9. Fig; lQis a partialsection taleiialong the aXes of a pair of rotors constructed according to amodificati on of my invention. Fig. 13 .is a View in axialdirection oi the rotors shown in Fig. l2, and of intermediate stationary parts, at halt the scale of Fig.` l2. 4In tlieiFigures l, and 3, the characters l1 and Yl2 denote. two rotors in the form of drums, which are rotatable onparallel axes 13, 14,'in the same direction of revolution, as
indicated by arrows l5, lGin Fig. 2. The
rotors are secured to flanges 18, of the shafts or axes 13, 14, by any suitable means, such as screw bolts, not' further indicated in the drawing. The rotors extend in a casing consistingy oitl two parts 2l, 22,wvliich may` be tightly bolted together with flanges 2l', 22. The shafts 13, lll project out oi the casingfV 2l, 22 on either side, andpass stuiiing boxes 24 of known structure, indicatedV by their general outline. The shafts 13, 14 are journalled in a pairof bearings 25, and on one side contain circular grooves 27, engaging a thrust bearing. rlhe casing as well as the bearings rest on a base 30, as outlined in Fig. 3.
The rotors 11 and 12 contain blades 31, 32 arranged in rings 311, 312, 313, 314, 315 and 321, 322, 323, 324, 325 of such diameter that they overlap. The overlap is seen especially in Fig. 2. Usually the blades are pieces separate from the rotor drums and are rigidly secured to them by known means such as slots 33, 34 of dove tail form or other suitable form. The blades themselves as well as the manner of securing them to the rotors are the same as in usual practice. It is understood that the blades may also be made one'piece with the rotor drums, if so desired.
A medium, such as steam, or combustion gases, is led to the blades at 35, which is a point where the rotors overlap. The medium then passes gradually through the blades from the high pressure side 35 to the low pressure side 36, high pressure side being the side of larger pressure, although the pressure in some cases may not be actually high, for instance in exhaust turbines constructed according to the present invention.
The medium passes first through the stationary nozzles 38, and then through the ring 311 of blades of rotor 11, through the ring 321 of blades of rotor 12, and continues to pass through the rings 312, 322, 31 323, 314, 324, 315, 325, which rings belong alternately to the two rotors.
The medium passes therefore through the rings not on their whole, but only on part of the circumference, namely on the part, where adjacent rings of the different rotors overlap.
Moreover it is frequently desirable to not fully utilize the whole area of overlap, but to leave out the corners 40, (Fig. 2) where the two outside circles 41, 42 intersect. The iiowing medium will then occupy an area between the dotted lines 43 and between the overlapping circles 41, 42.
The flow of the medium can be controlled by various means, such as by suitably placing the initial nozzles 38, to cover only part of the overlap if so desired, and by providing a member 44 after a ring of blades, especially after the last ring of blades 325. Member 44 has an opening or window, which ends along the dotted lines 43 (Fig. 2), and which therefore prevents the medium from passing through the extreme corners already referred to.
In addition stationary members 45, 46 (Fig. 2) are provided, which extend inside of the rectangle formed by the parallel lines 47 and 48, (or which may be made to extend all around the rotor and which occupy the space on the outside of each ring of blades, thereby preventing the medium from iiowing outside of the rings of blades.
Rotary engines constructed according to the present invention belong to the multiple rotor group already referred to, and form a. novel type of this group.
One important advantage of this group lies in the reduced number of stages required, inasmuch as rotating blades are substituted for stationary blades of the single rotor type, so that energy is transmitted to two rings of blades per stage instead of only to one.
A further important feature lies in the high eiiiciency attainable, inasmuch as the intei-nal friction losses are confined to such blades which transmit energy.
Another prominent feature lies in the fact that the outlet energy can be fully utilized. The kinetic energy of the medi um leaving one ring of rotating blades may be fully recovered in the subsequent ring of blades. This feature permits to further reduce the number of stages, as will be fully explained hereafter.
All these advantages are maintained in rotary engines constructed according to the present invention. But whereas in the known engines of the multiple rotor group these advantages are bought with complications in the further design, the further design and the general arrangement are utterly simple in the present case.
It is evident from Fig. 2, that opposite peripheral velocities of the blades result in an equal direction of revolution, as indicated by the arrows 15, 16. The rotors may therefore be provided with pinions 50, 51 meshing with the same gear 52. Shaft 53 of gear 52 is shown in the plane constituted by the two axes 13, 14. Shaft 53 is rotatably held in two bearings 54, and delivers energy on the side 56 in a manner not further indicated. Gear and pinions may be provided with herringbone teeth 58, as indicated.
The pinions are integral with their shafts 60, G1 and coaxial with the shafts or axes 13. 14 of the rotors. The pinions are driven from shafts 13, 14 by means of clutches G2, (33 ol' known design, indicated merely as rectangles. Especially in the case of more than two rotors, as outlined hereafter, the clutches are so designed as to permit engagement and disengagement while the turbine is running.
The exhaust of the turbine is received at 3G, and is led away through an exhaust pipe 65, in the case of steam turbines preferably to a condcnsor.
It is noted that shaft 53 is centrally located with respect to the turbine, whereas even in known single rotor turbines this shaft is Oifset. Moreover gear 52 can be made smaller than a gear of the same capacity in av single rotor turbine, because the load is distributed to two pinions instead of only to one.
For simplicitys sake I have omitted in the drawings most of those known parts which go with engines of the kind referred to without further explanation, especially valves, a centrifugal governor, a lubrication system.
'i ivano-23 cording to the present "inventiomand 'intend` ed especially for smaller capacities.
The medium, such as steam, is' introduced at 68, and flows inV a general `direction parallel to the axes 7 0, 71 of the rotors 72,173 to the side 74 of lower. pressure. The rotors contain each three Irings 75, 76 of blades,`
` The parallel shafts 70, 71 Vof the two rotors are journalled` in bearings 77, 78, 79, 80,' placed on a 'commonA frame Y81. "The turbine housing also stands on this frame.` It is again composed of two parts, which in operation are tiohtlT boltedl together and of which the upper partor coverhas been removed in the drawing. efore leaving 'the casing, the shaftsl 70, 71'pass oneither side through stuffing boxes 83 indicated diagrammatically by rectangles. Thestuftin'g boxes are tightly'secured to the casing by' means such as' rings 84, bolted to the casing and to the stuffing-boxes. l
Intermediate the two bearings 77, 78' and T9, S respectively and on thesideof higher pressure,i pinions, 85 are provided, which A ar'ecoaxial with Aand vfreduently also integral Ywith the shafts 70, 71. 'The -pinions 85, 85'
contain helical teeth 86 of such hand, that thel thrust resulting fromthe tooth pressure isin a direction opposite to the thrust exerted on the rotors by the medium. In this manner the thrust bearings 87, 88 are called upon tocarry only a reduced load.
The pinions inesh with the same helical gear 90, rigidly secured to a shaft 91 of 'any suitable machine, such as ,for Vinstance an' electric generator 92 indicated only withpart of its outline.
It is noted, that the energy isV here 'transmitted on the side of higher pressure, whereas the known turbines transmit the energy on the side hf lower pressure'. By providing an arrangement as shown,'the length fof -the unit may be reduced. y, f l
`An arrangement of aturbine withm'ore than two rotors is diagramm'atically 4outlined in Fig. inV which`93fd-enot'e thec'entersl of six rotors. They arearranged at equal "diss tances from a'central axis 94, and contain pinions 95 meshing with the same gear 96 rotatable on axis 94. The 'pinions receive Vthe drive 4from ytheir rotors through clutches, such as indicated at 62; 63 inA Fig. l.. A fmultiple rotor arrangement asindicated permits a high 4eiiiciencyfwithin a very great range of loads. At small loads the inlet of a number of rotors is shut ofl, the clutches of said rotors are. disengaged, and these rotors are stopped. They cease therefore to consumer energy through internal friction. I
A further vnovel application isillustrated in F ig. 6. IThe turbine outlined in F ig. 6 is a coinbinationfof the new type just described with a known type. Two rotors 100, 101 aref rotatable on parallel axes Y102, 103 inthe saine direction of revolution. They contain: onthe high pressure side blades arranged in rings of such diameter, that they overlap, as de- 'scribedwith "reference toltigs. l-ft. They'- also contain. blades arranged inlrings of a diameter smaller than the distances ofthe two axes 102, 103,0f known design, be it of the action type or of the reaction type.
The medium of such as steam, is intro* duced at a point 104 where therings of blades overlap. Itv passes first through stationary nozzles 105, and then alternately through rings of blades of thel two rotors, namely through rings 1061, 1071,' 1062, 1072, 1063, 1073.`
i So far the flow of medium'occupies only part of the circumference ofthe ringsofblades, namely the area ofoverlap, or part ofL such area. `After having passed throughtheoverlapping rings, the medium passes through rotor in a known manner,` and preferablyon `the whole circumference. 1t passes through stationary blades or channels 108,`andthen alternately through rotating blades 'and stationary blades 110. l
The casing infront may be made offaln upn per and a lower part, the two"roto1s"`being covered by the same casing 111.1K In therear preferablysepa'rate casings 112, 113'ar`e used on the two rotors. Before leaving' the easing, l
the shafts 102, 103` pass through stuffing boxes 1141; The shafts aresup'ported on bearings 115. The reduction gears are'oniitted in this figure.
Fig. 7 is a view of the rotors shown in Fig.
6 and the stationary parts 117, 118, whieh prevent theniedium frein flowing outside of the blades. The initial nozzles 105 are indicated in dotted lines. Every"ring 'of blades, in which a pressure drog takes place."
may be secured to aseparate dis {,so that the stationary members 117, 118, intermediate the disks, extend inwardly as far as thehubs 119,
ergy of the expanded steam is in known pracl tice freruiently utilized in so-called Curtis stages, that is to say the high velocity of the steam is not completely used up ina single ring of rotating blades, but in a plurality ofl rings, stationary blades for reversing 'the' Separate` disks may be used especially, when the drop 1n pressure is steam being placed between two subsequent rotating rings. In this known case the pressure of the steam is the same innnediately before entering the lirst and alter leaving the last ring oi a plurality of rotating rings oi blades.
Turbines constructed according to the present invention can utilize a similar rangement with Jarticular advantage. because they eliminate its main drawback oit low eliiciency. I therefore preferably use on the high pressure side two or more or" such stages, so that the pressure ot the medium is substantially the same betere and atter two or more subsequent rings of blades; such as before ring 106l and after ring 1071 (Fig. 6), or before ring` 106l and alter ring 108:.
I may use this type of stage-s excl .sively on the high pressure side, where the difierent rings of blades overlap, or l may combine such stages with stages of the reaction type.
Such a combination olf stages is indicated in Fig. 8, another in Fig. 9, and Fia'. 1() and Fig. 11 are explanatory velocity diagrams.
122 denotes stationary channels or nozzles having a minimum area 123 intermediate th; ends 124i, 125. They will therefore pei lit the medium to assume a velocity, at end 125, in excess of the velocity of sound, as well known. In Fig. 10, the velocities are plotted as straight lines, whose linear distances are proportional to tho velocities and whose directions are parallel to the direction of' the velocities. Absolute velocities are drawn in full lines, and relative velocities of the inedium with respect to the rotating blades are shown in dotted lines.
After having passed through and expanded in the nozzles 122, the mediinn assumes a velocity such as 126 (Fig. 10). 'l`he velocity 12T of the medium relatively to the rotating blades 128 may then be determined by plotting the peripheral velocity 12) ot blades 128 in Fig. 10, as indicated and completing the triangle 128, 127, 128. Prel'crably the blades 128 have the same inclina ion on the entering side as relative velocity 12T, as known. rlhe medium leaves the blades 128 with an equal. but oppositely directed rch'.- tive velocity, indicated at 180 in Fig. 10, no relative acceleration taking place in the rotating blades 128. rllhe absolute velocity 132 of the medium. alter leaving blades 128, may be determined by plotting the peripheral velocity at 129. and by completing triangle 130, 182, 129. rIhe medium now enters the blades 183 rotating' in opposite direction.
The relative velocity 13a may be determined as before, see Fig. 10. Ylhe relative velocity 134 of the medium, when leaving thel blades 188 is equal to but oppositely directed as compared with the relative velocity 1811 when entering. Neither in the blades 128, nor in the blades 183 does the medium experience an acceleration rolatively to the blades. The pressure oi the medium when entering blades 128 and when leaving blades 133 is theretore the same. The absolute velocity has changed from an amount 126 to an amount 135, the latter beingdetermined in the manner explained.
In the example indicated in Fig. 8, I have shown rotating blades 13G, 137, 138, 139, of dillierent type disposed after the blades 128, 183. In these blades the medium assumes a larger relative velocity when leaving the blades than when entering. fr drop in the pressure of the medium therefore takes place in the rotating blades. Blades et this type have frequently been called reaction blades. lVhen it is desired to have a particularly small number ol stages. I may prnvide blades 138,187,188 which 'form channels having a minimum area 14:0 intermediate the two ends. so that the medium may assume a velocity oeyond the velocity of sound. A velocity diagram corresponding to such blades as 186, 137, 138 is shown in Fig. 1l.
rllhe absolute velocity' oi"A the medium when entering blades 18h, is denoted by character 1451. The relative velocity 14:2 may be dctermined in the same manner as explained before. lfhe relative velocity 1li-3 ot the medium when leaving lades 13G may be determined in known manner from the area ot the channels and from the changed density or speciiic g'avity oit the medium. The absolute velocity is then les. Equal or imilar' velocities may be provided in the blades 137, 138. The last rinfr of blades is preferably so designed, that the absolute velocitv ot the medium, on the leaving side, is a minimum and directed substantially parallel to the axes ot rotation.
rllhe kinetic energy of the medium which corresponds to the said absolute. Velocity namely lost, whereas the kinetic energy nl the medium, which corresponds to an absolute velocity 1414-, may be recovered in the subsequent ring oi blades. ln all rings ol blades but the last one, large leaving veio-.- ities may therefore be provided, which icature permits to `further reduce the number ol' stages as compared with the single rotor type of turbines. i'
In Fig. 9 blades are shown arranged in a larger number of rings or stages as conipared with Fig. 8. rl`he blades 145. 146. 1l?. 148, 149 are inclined in their general direction 150 to the direction 152 ot periphera motion, as are the blades 13G-139, but they do not contain a minimum area intermediate their ends. In other words they are designed for relative velocities ot the medium not in excess of the velocity of sound.
rlhe Figs. 12 and 13 diagrammatically illustrate an embodiment ot the present invention', in which the flow of the medium extends in a
Азиатская сука сделала множество фото на вебкамеру в нижнем белье
Зрелая женщина возбудилась и потрахалась с парнем
Laura Brook накачала киску помпой