Everything To Know About High-Pressure Boilers
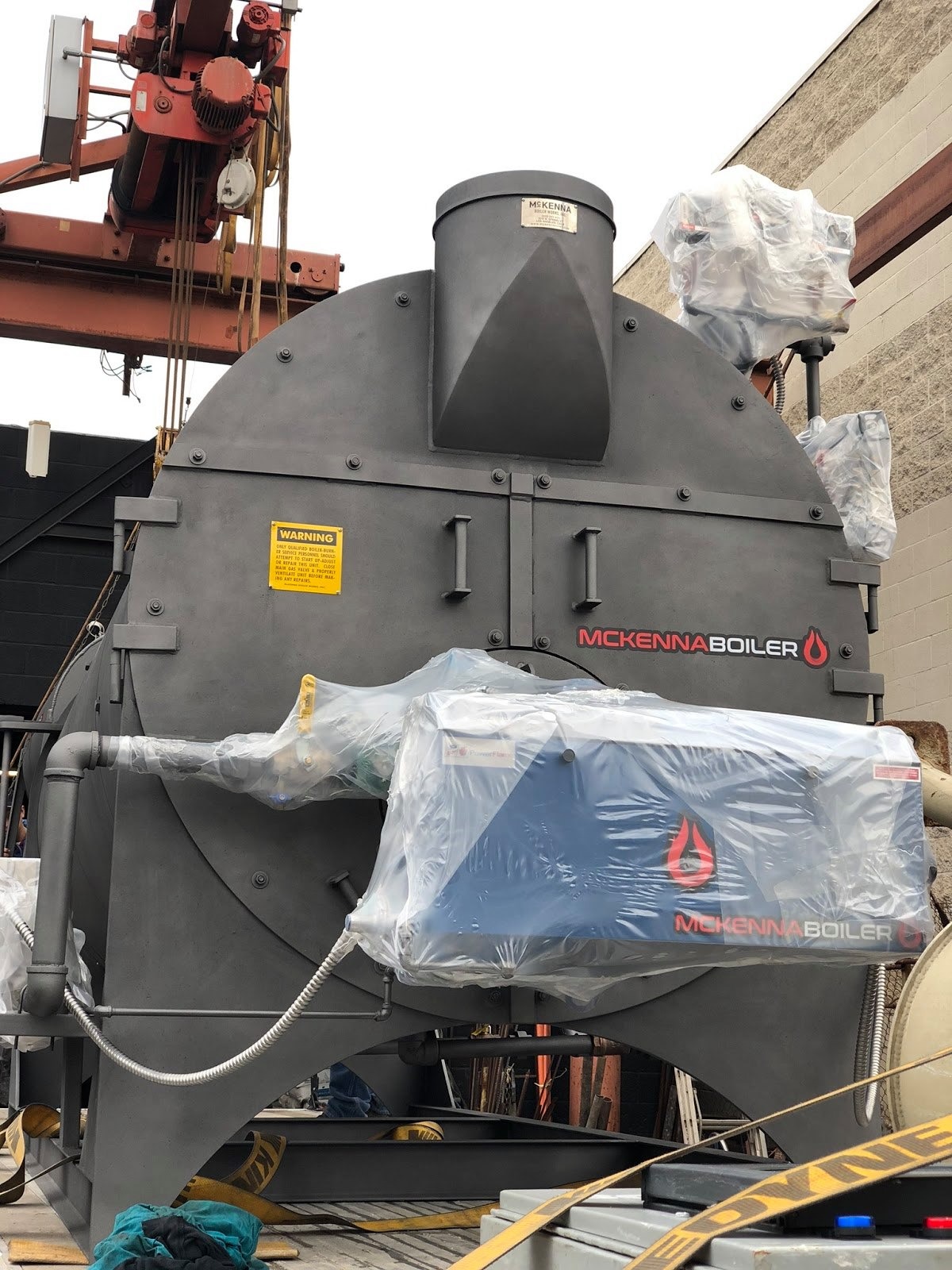
A high-pressure boiler is a shell and tube heat exchanger that produces steam or hot water to use for powering larger machines. They generate electricity by turning water into steam using thermal energy in a metal tank or enclosure, which is then utilized to power machinery.
A high-pressure boiler generates pressure and steam by burning fuel such as coal, natural gas, or petroleum. Natural convection or a pump is used to circulate the warm gases produced by the burning fuel. To enhance the evaporation rate to 210 k of force per square centimetre, a centrifugal pump is used to create forced circulation. Natural circulation is substantially more limited, with a force per square centimetre that is far smaller. It is crucial to understand that to keep high-pressure boilers running at full capacity, you need the best services at your side.
High-Pressure Boilers' Characteristics
1. Water circulation by force — water circulation by force is maintained in all modern high-pressure boilers using pumps. It boosts the pump's assistance. It raises the boiler's average temperature of heat addition and evaporation capacity.
2. A large number of small diameter tubes — Using small-diameter tubes raises the surface-area-to-volume ratio (area density). It aids in the rapid transfer of heat to the water moving inside the tubes. As a result, in forced circulation, many small density tubes are used in a zigzag pattern for water circulation. Furthermore, using a small tube decreases pressure loss and improves steam quality control.
3. Higher steam pressure and temperature - with two superheaters in series, steam is generated at a pressure of 80 bar to 300 bar and a temperature of 450°C to 585°C.
4. Improved heat transfer mechanisms & contemporary high-pressure boilers use radiation as well as conduction and convection to transfer heat. There are various parts to the entire heat-receiving device. As a result, they may be conveniently placed in various furnace zones for the most efficient heat transfer to the water circuit.
5. Water directly flashes into steam in the tube itself after being constructed in a high-pressure boiler operating at and above the critical pressure. It does away with the necessity for a boiler drum.
High-Pressure Boilers Have a Lot of Benefits
1. High-pressure boilers use forced water circulation to ensure positive water circulation and increased evaporation capacity.
2. They require less vaporization heat.
3. They are compact, so they take up less space on the floor.
4. The potential for scale formation is reduced due to the fast velocity of the water.
5. All elements are uniformly heated, reducing the risk of overheating.
Discovering Boiler Advantages for a Power Plant Company
Large barrels are used to retain the water in most boilers. Small drums are used in high-pressure units, which may even eliminate the need for drum containers. This allows power companies to reduce the need for enormous boiler storage chambers, saving both space and money.
High-pressure steam tanks are more efficient than low-pressure steam tanks in terms of efficiency. Within minutes of turning on the boiler, high-pressure steam is produced. This unit is faster than the majority of others. High-pressure boilers are roughly 40% more efficient than normal steam boilers.
Power companies can save money by using high-pressure steam boilers in two separate ways. The use of tiny drums and lightweight tubes in high-efficiency boilers decreases the amount of foundation required. This saves money for the company during the installation and maintenance of the units. Because the boilers are more efficient than traditional steam boilers, they utilize less electricity, lowering power plant operating costs.