Drilling Holes
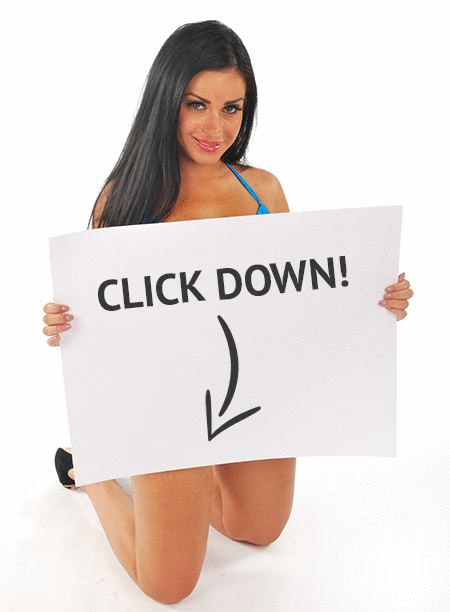
⚡ ALL INFORMATION CLICK HERE 👈🏻👈🏻👈🏻
Drilling Holes
The browser you are using is old and is no longer supported. Please upgrade to a newer version.
Sandvik Coromant use cookies and other technologies to give you the best experience on our website. Read more on Cookie policy
Was this page helpful?
Yes
No
Performance & security by Cloudflare
You cannot access www.familyhandyman.com. Refresh the page or contact the site owner to request access.
Copy and paste the Ray ID when you contact the site owner.
Ray ID:
759f3cc759ce16cb
759f3cc759ce16cb Copy
For help visit Troubleshooting guide
CNC Programming / GCode
CNC Programming Courses
G-Code Simulator
G-Code / M-Code List
Note : This is Lesson 15 of our Free Email Feeds & Speeds Master Class. Click here to learn more about the Master Class.
Ever do a job requiring hundreds or even thousands of holes to be drilled?
How about one where the holes were deep enough you started breaking twist drills?
Deep Hole Drilling is hard, and this article surveys the various techniques needed including peck drilling, parabolic flute drills, custom g-code cycles, and gun or BTA drilling.
Most CNC’ers know about Peck Drilling to help with deep holes. Some use high performance geometries like Parabolic Flute drills.
But it turns out there are a whole host of lessor known techniques to help you succeed when drilling deep holes. I’ve rounded up a number of things that will help you out a lot with Deep Hole Drilling.
The first is my CNC Chef Video on Deep Hole Drilling. I make these videos for Cutting Tool Engineering Magazine , one of the industry’s most respected publications when it comes to all things Cutting Tool-oriented and CNC. My video column there is called “CNC Chef”, which is a play on CNCCookbook.
The second thing is the graphic that’s visible in the video right behind me. That graphic is your handy thumbnail references to when to use these techniques. In fact, I’m going to give you not just that slide, but the whole Slideshow I used for the video. You can print the chart to hang on your wall for reference, or whatever helps.
Now if you download the slides, I’d just like to ask for one favor. Scroll down and subscribe to our blog newsletter. I want us to stay connected and that’s really the best way to ensure you get all our blog articles as they’re published.
For even more detail, keep reading. I’ve even got a cool Custom Deep Hole Drilling Cycle g-code generator for you.
Most tooling manufacturers regard any depth that is more than 3 or 4 times the diameter of the twist drill as a deep hole. There are various fancy geometries, such as parabolic flute drills, that help you to go deeper, but they will also have a limit.
Here’s the graphic at screen scale to help you what technique is best for your deep hole drilling:
We’ve prepared articles to help you drill down and get the full details on each of these techniques:
BTW, G-Wizard Calculator will tell you as part of its hints when you need to adopt a Parabolic flute drill as well as when you may need to start using a peck drilling cycle .
Peck drilling cycles are common on most CNC machines. With peck drilling, the twist drill is retracted periodically some distance to facilitate chip breaking and clearing. There are a lot of different kinds of peck cycles, and the deeper you’re drilling the more frequently you should peck and the further the retraction. The most important thing to keep in mind for peck drilling is the need to avoid trapping chips at the bottom of the hole. If there are chips left at the bottom, they interfere with the ability of the twist drill to re-establish its “bite”, which can result in premature dulling of the drill and poor surface finish.
When pecking, consider pausing the retraction after a very slight retract–say 0.001″. Left the twist drill spin for a couple of revolutions to pull the chips out of the deepest part of the hole. Also, never retract the tip clear of the hole if you’re going back into the hole. Doing so makes it easier for coolant to push chips back into the hole.
G-Wizard Calculator will automatically recommend when peck drilling should be used.
When drilling deeper than 7 x Diameter, twist drills with parabolic flutes are helpful with chip extraction. You can go a lot deeper with a parabolic flute drill–20 x Diameter vs only 7 x Diameter.
G-Wizard Calculator will automatically recommend using a parabolic flute drill when it would be helpful. For more, see our article on parabolic drills .
The biggest obstacle in making deep holes are the chips:
The choice of tooling, technique, and coolant delivery all have a role to play.
Certain kinds of tooling have inherent advantages for deep holes. Parabolic Flute twist drills change the geometry to optimize chip removal for deeper holes. Gun and BTA Drills are all about the needs of deep holes and especially chip evacuation.
Coolant is critical in chip evacuation. The best approach is coolant delivered with as much pressure as possible at the tool tip. High pressure coolant right to the tip brings considerable force to pushing the chips up and out of the hole.
Through spindle coolant delivers coolant at pressure through holes drilled along the length of the bit. This helps blast the chips up and out of the hole from the bottom, and really facilitates deep hole drilling.
Through spindle coolant holes in a twist drill. Note the extra grind to reduce web thickness with a split point…
Peck Drilling Cycles are all about chip breaking and evacuation. Each peck will typically break the chips. Long stringy chips catch on everything and are harder to evacuate. Compact chips can be evacuated more efficiently from deeper holes. The deeper the hole, the more frequently the twist drill must peck to ensure chips stay compact.
In addition, the retract distance is important. Retracting further helps pull chips out of the hole. But, it slows things down the further the bit must be retracted and in addition, care should be taken not to retract completely clear of the hole. An open hole is an invitation for chips to be washed all the way down to the bottom where they must be evacuated a second time.
Custom Deep Hole Cycles use custom g-code to optimize the peck strategy for each stage as the hole gets deeper and deeper.
Unfortunately, canned drilling cycles often have limitations when it comes to drilling very deep holes. What’s needed is a Custom Deep Hole Drilling Cycle.
What’s different about a Custom Cycle versus the normal Canned Drilling Cycles?
First is the pecking strategy. It’s important to be able to start out with a small peck and only go to bigger pecks as the hole gets deep. Doing the full retraction early before the hole has gotten deep is a waste of motion that serves no useful purpose. Ideally, you want to plunge without pecking to a couple of diameters or so and then start pecking. The frequency of the peck needs to increase the deeper the hole is bored. The nature of the peck has to change too based on the hole depth. We start out with a little short retraction–just enough to break the chip. But, as we get deep, longer and longer retractions are necessary as we need to not only break the chips but facilitate chip extraction. Lastly, we want to be able to prevent the twist drill from retracting entirely clear of the hole so that chips are not washed back down the hole.
Second is our feeds and speeds. As the hole gets deeper, we benefit by reducing the feedrate and spindle rpm. There’s no need to do this until the hole reaches a threshold depth, but once we’re at that depth it helps a lot.
Lastly, as long as we’re programming a custom cycle, we want to consider whether to use rapids or feedrate speeds for the peck and retraction from the hole. This is the reverse motion that isn’t cutting anything, and we have the potential of saving more time versus canned drilling cycles that keep all the motions at feedrate speeds.
By using custom g-code to implement all of these considerations, we waste as little time as possible on pecking while ensuring that when the going gets tough we’re doing enough to keep our tool happy without breaking. While Canned Drilling Cycles differ from controller to controller, very few will offer the flexibility to control all of these variables.
G-Wizard Conversational CNC is a set of Wizards that go with the G-Wizard Editor, our g-code editor and cnc simulator . These wizards let you answer a few simple questions and then they generate g-code based on your answers. It’s faster and easier than most CAM programs and helps you get the job done faster. One of the Wizards we’ve included makes it easy to create Custom Deep Hole Drilling Cycles such as we’ve been discussing. Here’s a screen shot of the Deep Hole Cycle Wizard:
You can see all of the capabilities we talked about are built into the Wizard. In addition, the default values chosen by the Wizard represent the Best Practices we uncovered in researching deep hole drilling. You can start from those best practices and customize the Wizard to be either more or less aggressive depending on your application. It will then generate the g-code needed to get the hole drilled.
The techniques described so far can get you all the way to about 20 diameters deep. After that, we need a completely new approach, and that approach is gun drilling and its relatives:
1. Fire up G-Wizard Editor and check out the Conversational CNC Wizards. Go through the process of creating a Custom Deep Hole Drilling Cycle.
Twist Drills can go down 5 diameters deep without issue. From 5 to 7 diameters, you should use Peck Drilling. From 7 to 10 diameters, use a parabolic flute drill with peck drilling. Any deeper will require a Deep Hole Drilling Technique.
Custom G-Code that’s optimized to change the peck strategy and parameters continuously as the hole gets deeper. A good deep hole custom cycle will not only take a twist drill deeper, it’ll also go faster than canned cycles. Custome Deep Hole Cycles can take you from 10 to 20 diameters deep. See this article to learn more.
When the hole gets past 20 diameters, gun drills and similar tooling is necessary.
By blasting the coolant through internal passages in the drill to the very tip, you get a high pressure coolant helping push chips up and out of the hole, plus better cooling and lubrication.
Join 100,000+ CNC'ers! Get our latest blog posts delivered straight to your email inbox once a week for free. Plus, we’ll give you access to some great CNC reference materials including:
Just enter your name and email address below:
All Material © 2020 CNC Cookbook, Inc.
We and selected third parties use cookies or similar technologies for technical purposes and, with your consent, for other purposes as specified in the cookie policy . Denying consent may make related features unavailable.
With respect to advertising, we and selected third parties , may use precise geolocation data, and identification through device scanning in order to store and/or access information on a device and process personal data like your usage data for the following advertising purposes : personalized ads and content, ad and content measurement, audience insights and product development .
You can freely give, deny, or withdraw your consent at any time by accessing the preferences panel.
In case of sale of your personal information, you may opt out by using the link " Do Not Sell My Personal Information ".
To find out more about the categories of personal information collected and the purposes for which such information will be used, please refer to our privacy policy .
You can consent to the use of such technologies by using the “Accept” button, by scrolling this page, by interacting with any link or button outside of this notice or by continuing to browse otherwise. By closing this notice, you continue without accepting.
We use cookies to make wikiHow great. By using our site, you agree to our cookie policy . Cookie Settings
{"smallUrl":"https:\/\/www.wikihow.com\/images\/thumb\/6\/6c\/Drill-a-Hole-in-the-Wall-Step-1.jpg\/v4-460px-Drill-a-Hole-in-the-Wall-Step-1.jpg","bigUrl":"\/images\/thumb\/6\/6c\/Drill-a-Hole-in-the-Wall-Step-1.jpg\/aid10927326-v4-728px-Drill-a-Hole-in-the-Wall-Step-1.jpg","smallWidth":460,"smallHeight":345,"bigWidth":728,"bigHeight":546,"licensing":"License: Creative Commons<\/a>\n<\/p>
\n<\/p><\/div>"}
Use a drywall bit if the wall is sheetrock or plasterboard. Before you start drilling, take a look at your wall and determine what it’s made of. If your wall is smooth and sounds hollow when you knock on it, it’s likely a form of drywall, such as sheetrock or plasterboard. For drilling a simple hole into this type of wall, a drywall bit is your best bet. [1]
X
Research source
You can purchase drywall bits and other types of drill bits at most hardware or home improvement stores.
If you’re planning to hang something (such as a picture) on a hollow section of drywall, you might choose to drive in a drywall anchor using a power screwdriver for greater security. [2]
X
Research source
If you’ll be drilling into a stud behind the drywall, opt for a wood drill bit. [3]
X
Research source
{"smallUrl":"https:\/\/www.wikihow.com\/images\/thumb\/a\/ab\/Drill-a-Hole-in-the-Wall-Step-2.jpg\/v4-460px-Drill-a-Hole-in-the-Wall-Step-2.jpg","bigUrl":"\/images\/thumb\/a\/ab\/Drill-a-Hole-in-the-Wall-Step-2.jpg\/aid10927326-v4-728px-Drill-a-Hole-in-the-Wall-Step-2.jpg","smallWidth":460,"smallHeight":345,"bigWidth":728,"bigHeight":546,"licensing":"
License: Creative Commons<\/a>\n<\/p>
\n<\/p><\/div>"}
Get a masonry bit if your wall is brick, stone, or concrete. If your wall is made of a hard material, such as brick, block, concrete, or stone, choose a masonry bit. [4]
X
Research source
These bits are composed of soft steel with a tip made of tungsten carbide, which allows them to cut easily through hard walls.
You will probably need to use a drill with hammer action to drive the bit into your wall.
{"smallUrl":"https:\/\/www.wikihow.com\/images\/thumb\/d\/dc\/Drill-a-Hole-in-the-Wall-Step-3.jpg\/v4-460px-Drill-a-Hole-in-the-Wall-Step-3.jpg","bigUrl":"\/images\/thumb\/d\/dc\/Drill-a-Hole-in-the-Wall-Step-3.jpg\/aid10927326-v4-728px-Drill-a-Hole-in-the-Wall-Step-3.jpg","smallWidth":460,"smallHeight":345,"bigWidth":728,"bigHeight":546,"licensing":"
License: Creative Commons<\/a>\n<\/p>
\n<\/p><\/div>"}
Choose a spur point bit for wood walls. If you’re drilling into a wall with wood paneling, opt for a spur point bit. [5]
X
Research source
These are also known as wood bits. They are designed with a sharp point at the tip to help keep the bit on track as it enters the wood.
Spur point or wood bits are also useful for drilling into studs behind hollow walls.
{"smallUrl":"https:\/\/www.wikihow.com\/images\/thumb\/5\/5a\/Drill-a-Hole-in-the-Wall-Step-4.jpg\/v4-460px-Drill-a-Hole-in-the-Wall-Step-4.jpg","bigUrl":"\/images\/thumb\/5\/5a\/Drill-a-Hole-in-the-Wall-Step-4.jpg\/aid10927326-v4-728px-Drill-a-Hole-in-the-Wall-Step-4.jpg","smallWidth":460,"smallHeight":345,"bigWidth":728,"bigHeight":546,"licensing":"
License: Creative Commons<\/a>\n<\/p>
\n<\/p><\/div>"}
Opt for a tile bit for tile, ceramic, or glass. If you’re drilling into a brittle material such as tile, ceramic, or glass, you’ll need a specialized bit to pierce the material and prevent the wall from shattering. [6]
X
Research source
These drill bits have spear-like carbide tips and straight shanks that allow them to cut smoothly through these hard-to-drill materials.
You may also be able to use a carbide-tipped masonry bit for some types of tile wall. [7]
X
Research source
{"smallUrl":"https:\/\/www.wikihow.com\/images\/thumb\/f\/f6\/Drill-a-Hole-in-the-Wall-Step-5.jpg\/v4-460px-Drill-a-Hole-in-the-Wall-Step-5.jpg","bigUrl":"\/images\/thumb\/f\/f6\/Drill-a-Hole-in-the-Wall-Step-5.jpg\/aid10927326-v4-728px-Drill-a-Hole-in-the-Wall-Step-5.jpg","smallWidth":460,"smallHeight":345,"bigWidth":728,"bigHeight":546,"licensing":"
License: Creative Commons<\/a>\n<\/p>
\n<\/p><\/div>"}
Avoid drilling above or below light switches and outlets. Accidentally drilling into your electrical wiring can be a dangerous and costly mistake. You can help prevent mishaps by making sure not to drill directly above or below light switches, outlets, and other obvious electrical fixtures in your walls. If you locate a switch or outlet on an upper floor, try not to drill directly beneath it on the floor below. [8]
X
Expert Source
Gino Colucci Home Improvement Specialist
Expert Interview. 7 January 2021.
You can also avoid accidents by using a wire detector. [9]
X
Research source
A deep scan stud finder can also detect electrical wires and metal. [10]
X
Expert Source
Gino Colucci Home Improvement Specialist
Expert Interview. 7 January 2021.
If you must drill near live wires, shut off the power to the area where you’ll be working beforehand.
If you’re drilling into a bathroom wall or another wall located near plumbing or a radiator, you may wish to consult a plumber first. They can help you avoid accidentally drilling into a pipe. [11]
X
Expert Source
Gino Colucci Home Improvement Specialist
Expert Interview. 7 January 2021.
{"smallUrl":"https:\/\/www.wikihow.com\/images\/thumb\/e\/ea\/Drill-a-Hole-in-the-Wall-Step-6.jpg\/v4-460px-Drill-a-Hole-in-the-Wall-Step-6.jpg","bigUrl":"\/images\/thumb\/e\/ea\/Drill-a-Hole-in-the-Wall-Step-6.jpg\/aid10927326-v4-728px-Drill-a-Hole-in-the-Wall-Step-6.jpg","smallWidth":460,"smallHeight":345,"bigWidth":728,"bigHeight":546,"licensing":"
License: Creative Commons<\/a>\n<\/p>
\n<\/p><\/div>"}
Look for studs if you’re drilling into drywall. If your wall is sheetrock or plasterboard, you’ll need to find a stud if you want your drill hole to support anything heavy (such as a mirror, a large painting, or a shelf). [12]
X
Research source
The easiest way to find a stud is to use an electronic stud finder. Turn on the stud finder a
Gives Nice Handjob
Hair Lesbiyanki Sex
Muscle Sex Guy