Deep Hole Machining 2021
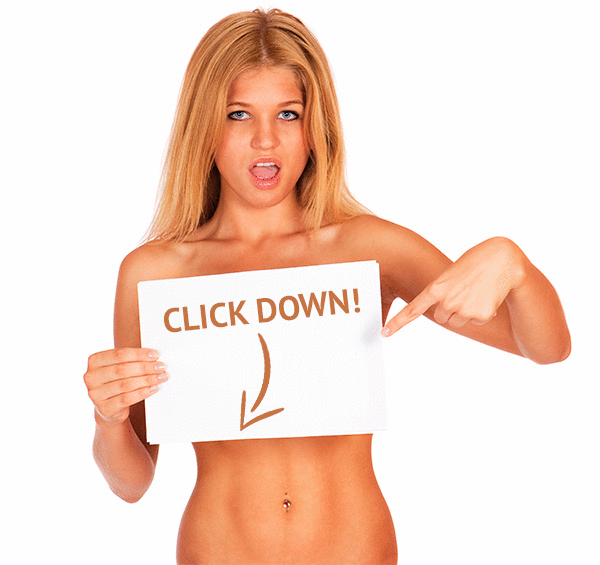
💣 👉🏻👉🏻👉🏻 ALL INFORMATION CLICK HERE 👈🏻👈🏻👈🏻
DHD System
Engineering
Set up
Micro Setting
Fine Finish
Fine Finish
We make your business our business and we know the importance of high quality and reliable delivery.
Copyright © 2021 MIT-Technologies. All Rights Reserved.
MIT Technologies, a leading provider of downhole intelligent products for the upstream oil and gas sector, is pleased to announce its plan to invest in a new CNC Deep Hole Drilling capability at the company’s CNC workshop in Technology Park Malaysia, Kuala Lumpur.
This investment includes CNC controlled Deep Hole Drilling Machine, tooling, and accessories capable of making holes up to 6.5m long, with more than 25 sizes of hole diameters up to 150mm. These capabilities include drilling, counter boring, skiving, and burnishing processes to achieve high quality surface finishes that are necessary for precision sealing surface.
Deep hole drilling is required for the majority of the parts incorporated in downhole oil and gas equipment. This investment will increase our ability to produce parts in-house, reduce our manufacturing cost, enhance our turnaround time, and allow us to produce more products faster to satisfy market demand more effectively. This investment will further reduce dependency on outsourcing which is essential for our business continuity amid complex logistics hurdles encountered during the COVID19 pandemic.
This major capital investment, taking place in Technology Park Malaysia, is another step towards advancing our capabilities and infrastructure; a requirement to advance towards our ambitious goals. Our R&D team continues to develop new innovative products for upstream oil and gas wells to achieve our growth targets in the domestic and international markets.
A deep hole drilling machine is a metal-cutting machine tool, designed to produce very deep precision holes into virtually any metal. Deep hole drilling machines enable the performance of specific tools – such as BTA and gundrills – to optimize the deep hole drilling process for manufacturers. Machines are engineered to integrate the technology used by these tools, and optimize all aspects of the process, to drill deep holes with accuracy, reliability, and efficiency.
Deep hole drilling machines are ideal for a variety of sizes of deep holes, production levels, and are necessary for holes that are approximately 20:1 depth-to-diameter or greater in ratio. Dedicated deep hole drilling machines provide the tooling support, coolant delivery, and process feedback that allow manufacturers to achieve their deep hole drilling goals. These features optimize the process and prioritize deep hole drilling methods, by reducing cycle time, stabilizing tooling, evacuating chips, and preventing tool breakage and process failures when compared to CNC machining centers.
Electrolyte distribution: (a) The initial time; (b) The machining process.
Initial electrolyte current density distribution.
Journal of Physics: Conference Series
Research on Electrochemical Machining Technology of Deep Small Hole
To cite this article: Sun Guorong et al 2021 J. Phys.: Conf. Ser. 1948 012201
View the article online for updates and enhancements.
This content was downloaded from IP address 194.110.89.43 on 29/06/2021 at 04:38
Electrochemical Drilling Process (ECD) provides the alternative to traditional or conventional drilling processes without a direct contact between the tool and the workpiece, with high material removal rates, irrespective of diverse mechanical properties of the workpiece. Even though ECD has a great potential, the process is still not fully explored and its research is in process. ECD involves number of phenomena such as electrochemistry, mass transfer, heat transfer and hydrodynamics. Due to this it is very difficult to predict the hole diameter accurately in ECD. This problem is considered for investigation by developing a Multiphysics simulation model for ECD and the effect of tool geometry on generated anode profile is studied to improve the dimensional control and performance of the Electrochemical Machining Process. For development of Multiphysics simulation model for the tool design in ECM hole making process, finite element analysis (FEA) software, COMSOL is used because of its capability to couple various phenomena in ECM process in a single model for better accuracy. The performance characteristics namely; overcut and height of spike generated is predicted by simulation and validated with the experimental results for the accuracy and capability. The predicted and experimental results agreed well and the developed innovative simulation model provides complete visualization and understanding of the ECD process.
Fabrication of the injection nozzle micro-hole on the aero engine is a difficult problem in today’s manufacturing industry. In addition to the size requirements, the nozzle micro-hole also requires no burr, no taper and no heat-affected zone. To solve the above problem, an ultra-short voltage pulse and a high-speed rotating helical electrode were used in electrochemical drilling (ECD) process. Firstly, a theoretical model of ECD with ultra-short voltage pulse was established to investigate the effects of many predominant parameters on machining accuracy, and the effect of rotating helical electrode on the gap flow field was analyzed. Secondly, sets of experiments were carried out to investigate the effects of many key parameters on machining accuracy and efficiency. Finally, the optimized parameters were applied to machine micro holes on 500 μm thickness of GH4169 plate, and micro-holes with the diameter of 186 μm with no taper were machined at the feed rate of 1.2 μm/s. It is proved that the proposed ECD process for fabricating micro-holes with no taper has a huge potential and broad application prospects.
Numerically controlled local wet etching (NC-LWE) has been developed as a novel noncontact subaperture deterministic figuring method for fabricating ultraprecision optics or for finishing functional materials. In this method, a localized wet etching area is formed using a combined nozzle that is constructed by coaxially arranging the supply part and the suction part of the etchant. The removal volume anywhere on the workpiece surface is determined by the convolution of the removal function and the dwelling time distribution of the nozzle. The machining properties of this method are insensitive to external disturbances, such as vibration or thermal deformation, because the removal process is performed under a noncontact condition.
Electrochemical machining (ECM) is a promising nontraditional machining method for shape generation, which has many advantages such as capable of processing difficult-to-cut metallic materials without residual stress, good surface quality, high efficiency, no tool wear, etc. However, in many cases, problems of relatively poor machining accuracy and possible environmental risks hinder further application of this process. Hence an electrolyte suction tool has been proposed for ECM, which is expected to give a solution to these problems by restraining the electrolyte flow within the suction tool. In this paper, the effects of different electrolyte flow modes in suction tool on characteristics of ECM process were investigated both theoretically and experimentally. A multi-physics model coupling with a turbulent two-phase flow field and an electrical field was established for the ECM with the suction tool. A set of observational experiments and machining experiments were designed and conducted to clarify the characteristics of the electrolyte flow field and verify the results of simulation. The results show that under the inward flow mode (IFM), much surrounding air is sucked into the machining area and a relatively stable gas-liquid zone is formed, leading to poor machining characteristics. Meanwhile, the electrolyte is confined to a small area under the outward flow mode (OFM), which effectively improves both surface quality and machining accuracy of the ECM process.
In this study, a series of deep micro holes were machined on thick GH4169 super alloy by the trepan drilling, using a millisecond pulsed laser which equipped to the numerical control processing system. The microstructure of the holes including surface and longitudinal morphologies, diameter, taper, circularity, micro cracks and recast layer were systematically characterized. The surface morphology and the longitudinal section of the drilled holes were observed by Scanning Electron Microscope and 3D Laser Scanning Confocal Microscope. The method of Minimum circumcircle method was employed to evaluate the entrance and exit end circularity. The results showed that the melt and spattering accumulating around the holes decreased with the augment of laser power. The diameter of the entrance showed an increasing tendency with the growing of laser power, but the exit end was not seriously affected by the power. The micro cracks and recast layer could be found obviously, the micro cracks appeared in those zones which thermal stress concentrated, the thickness of recast layer is about 20μm and the taper and circularity were optimized at a laser power of 80-100W.
To fabricate deep and small holes on the difficult-to-cut metals, an electrochemical drilling technology with chip removal and electrolyte replenishment was proposed. It was named electrochemical drilling of deep and small holes with high speed micro electrode. The working mechanism of the technology was analyzed and researched and the influences of some predominant parameters such as rotary speeds, voltages, pulse frequencies, and machining speeds on machining precision and stability were investigated. It points out that high machining precision and stability can be obtained by matching above parameters reasonably under a higher machining efficiency. A groups of deep holes with the diameter less than 0.5 mm and the aspect ratio more than 10 were fabricated successfully on the nickel base super-alloys GH4169 by using the hard alloy micro spiral electrode in a self-developed high-precision micro-electrochemical machining system. These holes show good morphology, lower tapers and clear-cut margins. It is proved that the high-speed electrochemical drilling process for fabricating deep and small holes has a huge potential and broad application prospects.
Forward flow pattern of electrolyte is widely used in electrochemical drilling (ECD) process. But electrolyte in the machining gap presents a sharp divergent flow which causes an abnormal dissolution and even harmful sparking. Reverse flow of electrolyte leads to a stable machining process but is rarely used due to the poor application feasibility. In this paper, an electrochemical drilling method with vacuum extraction of electrolyte has been proposed. Vacuum extraction of electrolyte greatly facilitates the application of reverse flow in electrochemical drilling. Flow distributions along the machining gap with different electrolyte flow pattern are compared numerically and experimentally. Reverse flow using vacuum extraction is shown to improve the process stability while diminishing sparking and formation of striations. Machining characteristics of vacuum extraction are investigated experimentally. To minimize the radial overcut of machined hole by electrochemical machining with vacuum extraction of electrolyte, the orthogonal design is used to optimize process parameters such as initial machining gap, applied voltage, tool feed rate, and electrolyte concentration. Good results have been obtained in the experiments with optimized parameters.
Ultraprecision machining for polymer
Grinding & Chemical mechanical polishing
July 2018 · Russian Aeronautics (Iz VUZ)
A new method of electrochemical machining of compressor blades is presented. The paper describes the sequence diagrams of electrochemical machining that contain various methods to feed electrodes.
November 2019 · Journal of the Japan Society for Precision Engineering
In tube electrode high-speed electrochemical discharge machining (TSECDM), mixed products are constantly produced in the narrow machining gap by simultaneous discharge erosion and electrochemical dissolution. For the high-efficiency removal of these products from the machining gap, a tool electrode with an optimized helical structure was utilized in TSECDM in this study. Firstly, the ... [Show full abstract] concentration distributions of the processed products in the machining gap using tube electrode tools with three typical helical structures were studied through the simulation of solid–liquid coupling; this showed that a trapezoidal helical structure benefited the reduced accumulation of products in grooves and the effective removal of products from the machining gap. Secondly, the main geometric parameters of the trapezoidal helical structure, including the helical groove depth, pitch, and tooth angle, were optimized by gap flow-field simulation to enhance the removal effect on processed products. Finally, it was verified that the trapezoidal helical electrode showed a definitive and significant advantage over the ordinary cylindrical electrode in effectively removing processed products from the machining gap by the comparison of flow-field simulations and actual machining experiments.
May 2020 · Materials and Manufacturing Processes
Electrochemical machining (ECM) is an efficient technique that can produce complex structures. However, for a blade with platform, the common ECM method only considers the machining accuracy of the profile. Owing to the stray corrosion, a taper can appear on the surface of the platform and reduce processing precision. This study presents a novel method for improving blade platform accuracy in ECM ... [Show full abstract] utilizing a cathode tool with an auxiliary electrode (AE). Specifically, an AE is installed on a cathode tool to change the electric field and restrain stray current, contributing to greater machining accuracy. In this study, the simulations for electric field demonstrate that both the range and size of stray current are reduced and the predicted taper of the platform is reduced by the AE. Blade machining experiments were conducted for three different materials, namely, SS304, Inconel 718, and Ti-48Al-2Cr-2Nb (TiAl 4822). It was confirmed that stray corrosion of the blade platform can be better controlled by utilizing an AE. The optimal tapers of the SS304, Inconel 718, and TiAl 4822 blade platforms were −0.097°, −0.086°, and −0.080°, respectively, which represented reductions of 50.7%, 61.3%, and 77.6%, compared to the processing done by utilizing a cathode with an insulating layer.
July 2017 · International Journal of Electrical Machining
The machining accuracy of electrochemical machining (ECM) is low since zones that are far away from the tool electrode are also machined. Furthermore, the scattering of electrolyte solution during processing constitutes a severe environmental problem. To overcome these problems, this study set out to develop a novel method that not only limits the working area by sucking the electrolyte into the ... [Show full abstract] region between the tool tip and the workpiece, but also prevents the electrolyte from being scattered. In this paper, the processing characteristics of an electrolyte solution combined with the proposed suction method, especially in the depth direction, were investigated.
© 2008-2021 ResearchGate GmbH. All rights reserved.
https://mit-technologies.com/news/2021/05/dhd/
https://www.researchgate.net/publication/352807649_Research_on_Electrochemical_Machining_Technology_of_Deep_Small_Hole_using_Suction_Electrode
Top Vintage Pornstar
Black African Lesbian Movies
Hd Video Nipples Sucking Lactating Milk Jav
Deep Hole Drilling & Advanced Machining | MIT-Technologies
Research on Electrochemical Machining Technology of Deep ...
Deep Hole Drilling Machining Technology - WOOCNC
Deep Hole Drilling Machining Services, Name of Institution ...
Deep Hole Machining, Deep Hole Drilling Services,Machining ...
News - Shin- il CNC Deep Hole Machinery
Deep-Hole Geometry, As Machined | American Machinist
Deep hole machining - Sandvik Coromant - PDF Catalogs ...
Sandvik Coromant: Deep Hole Machining
Modeling Electrical Discharge Machining of Deep Micro ...
Deep Hole Machining 2021

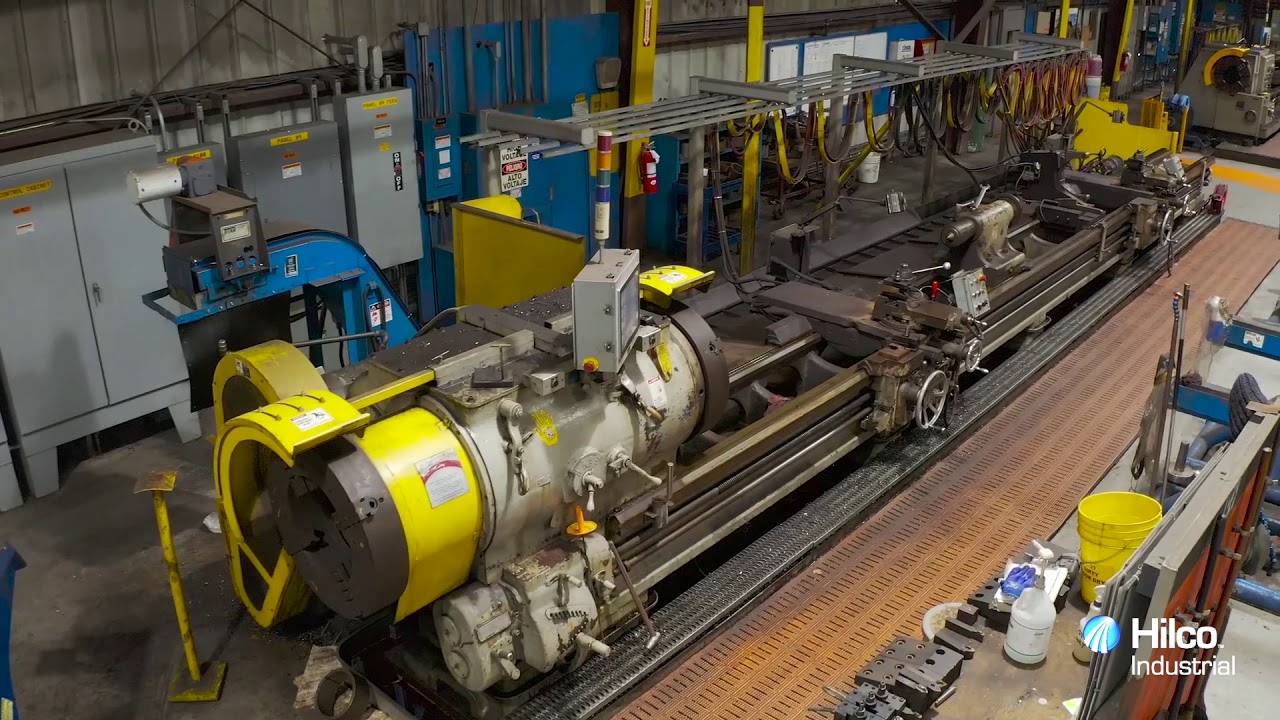


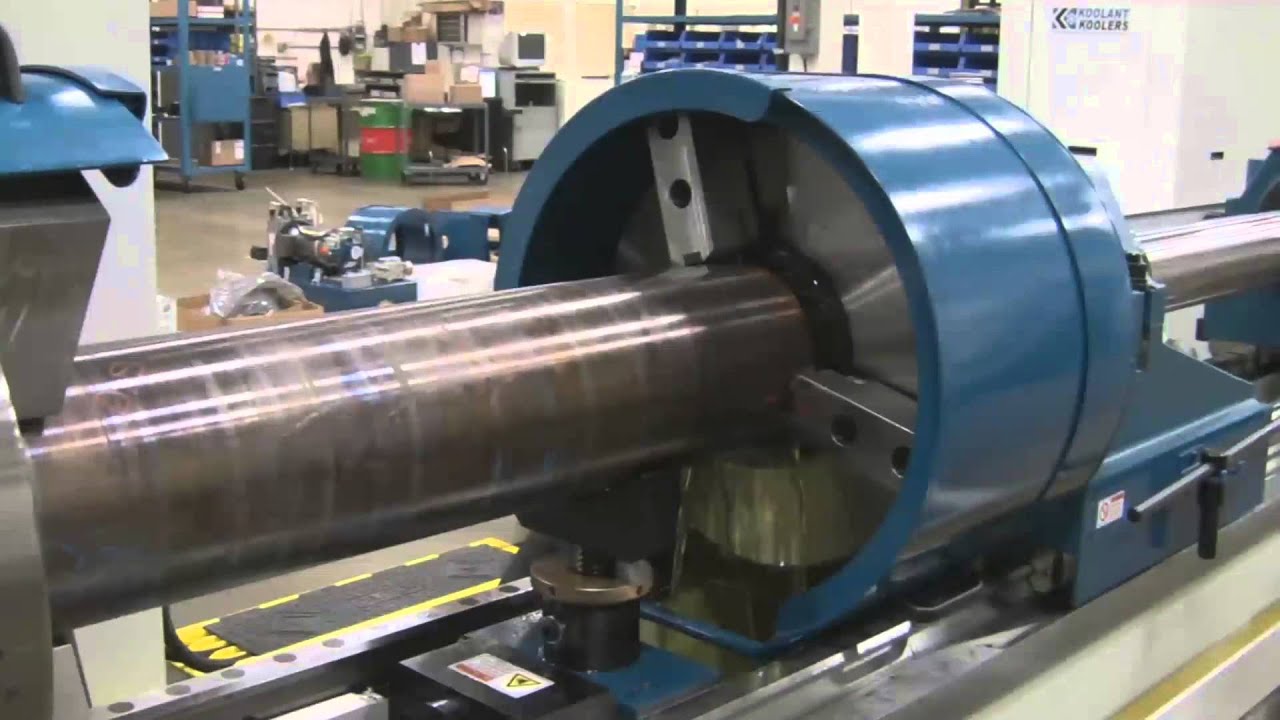
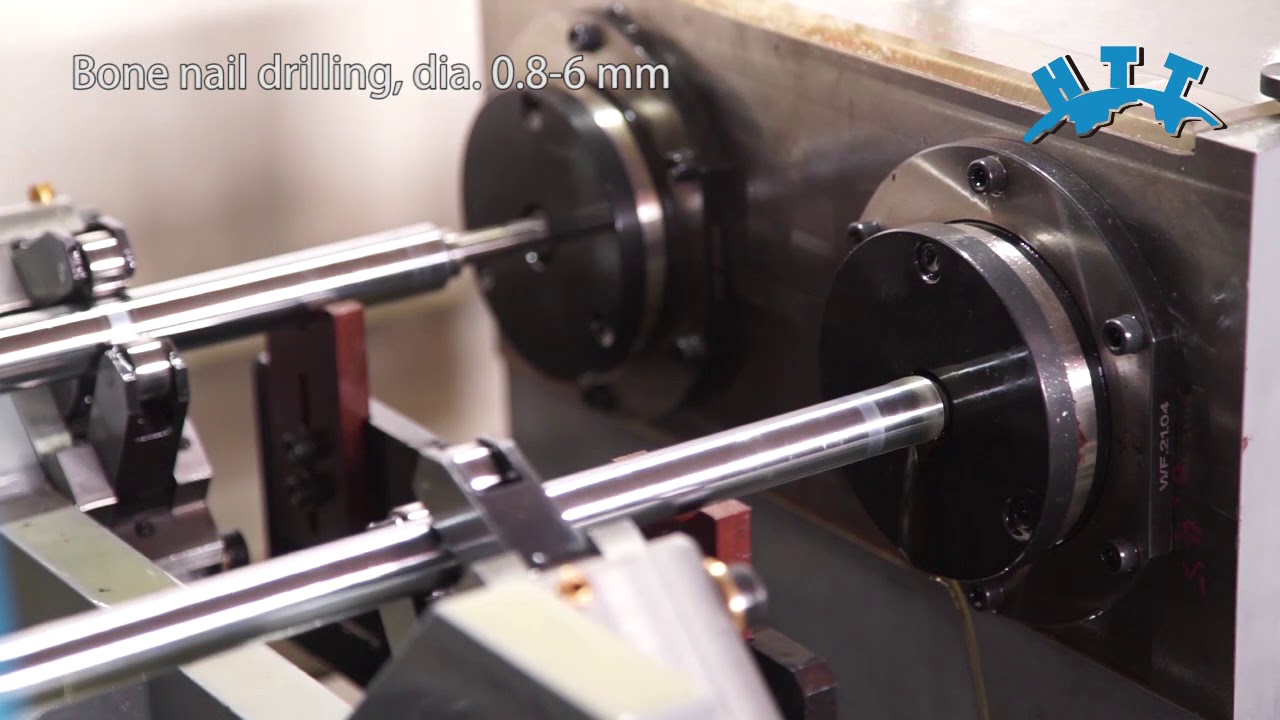


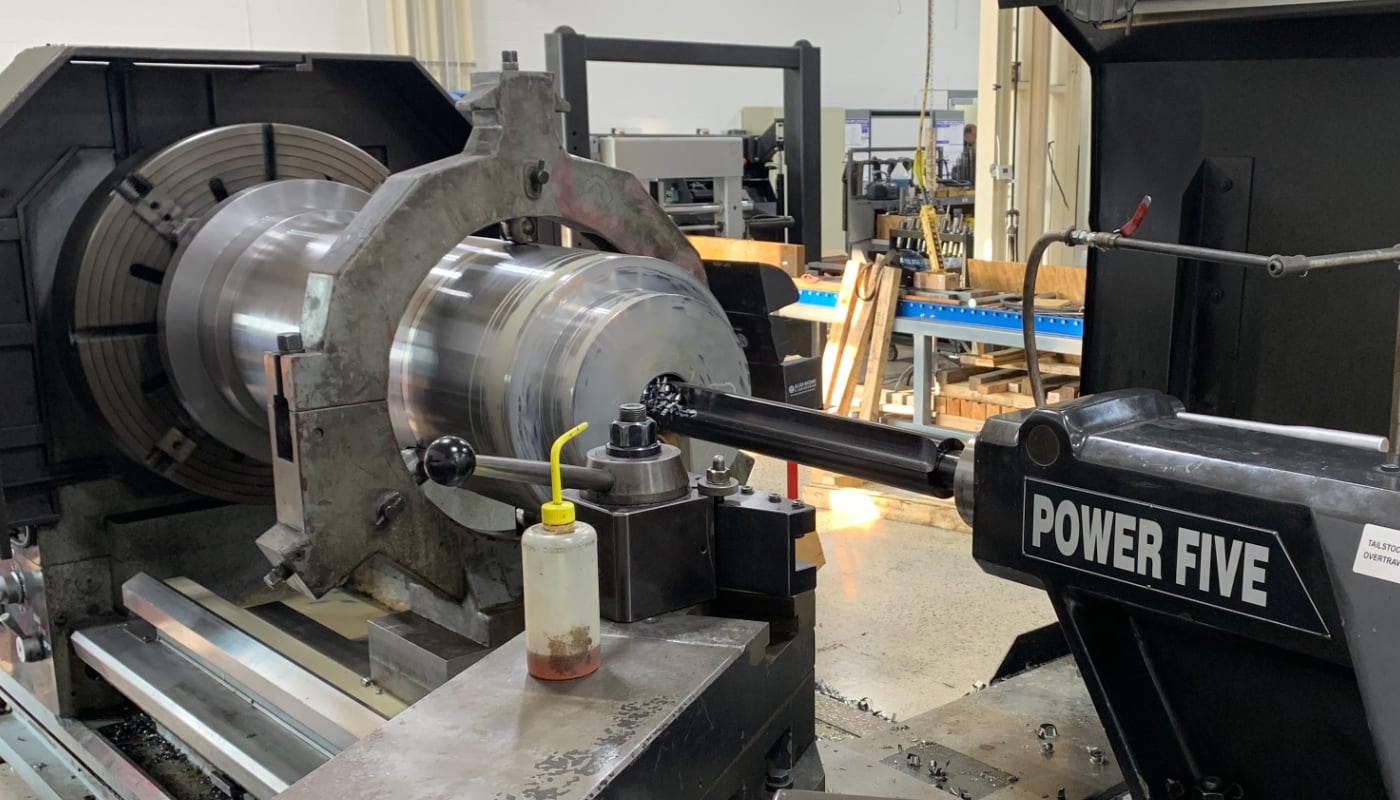
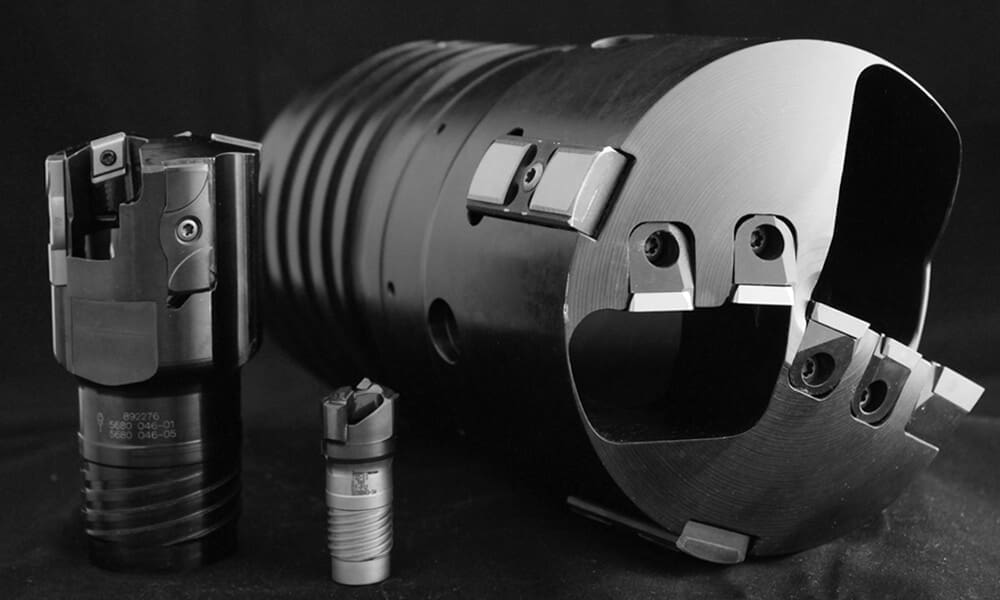
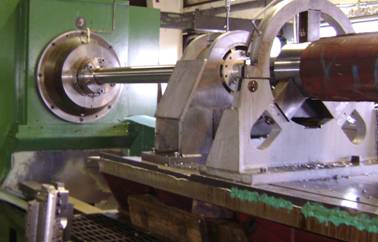



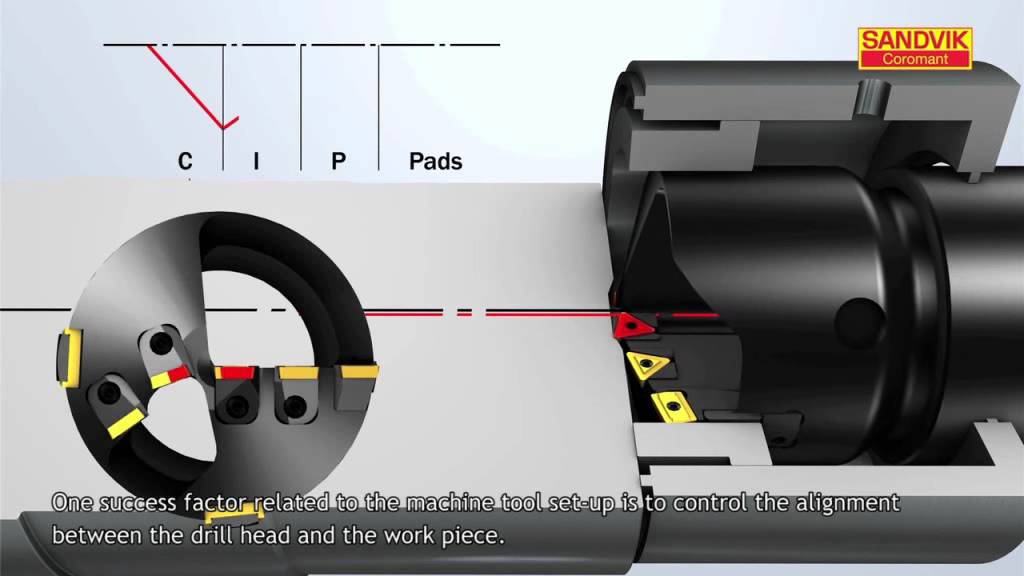

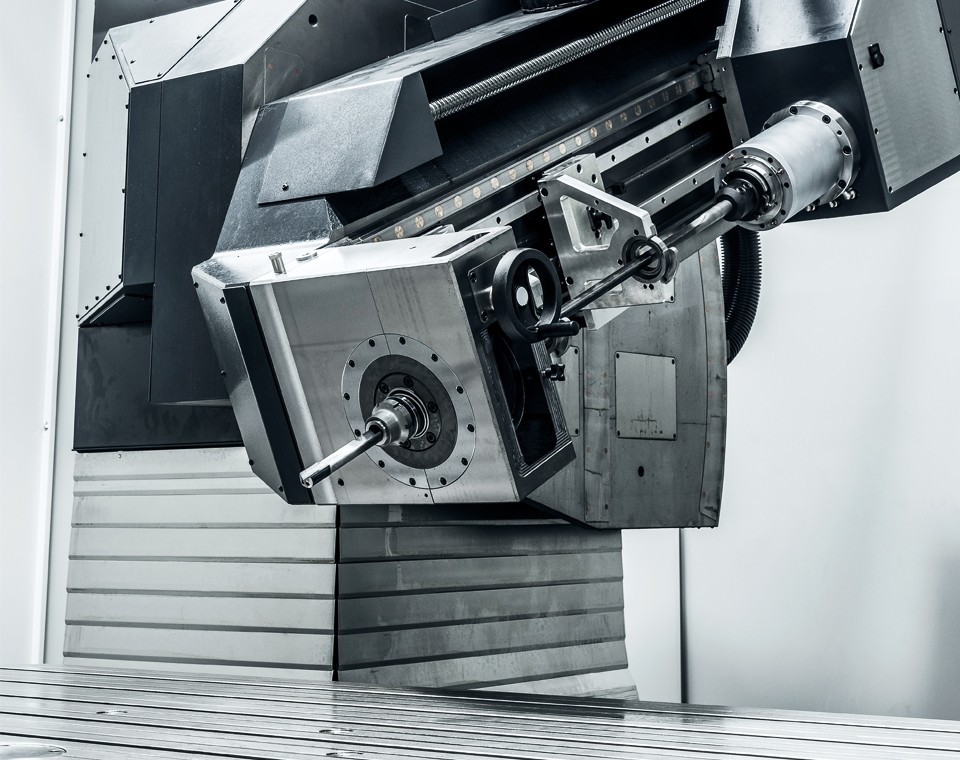










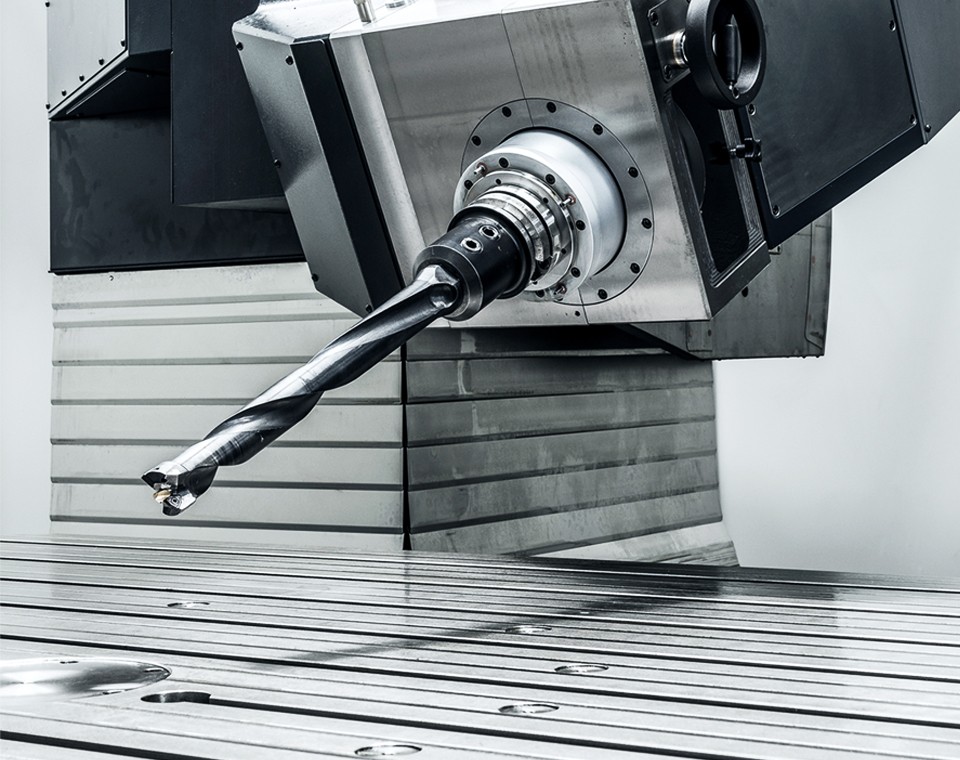


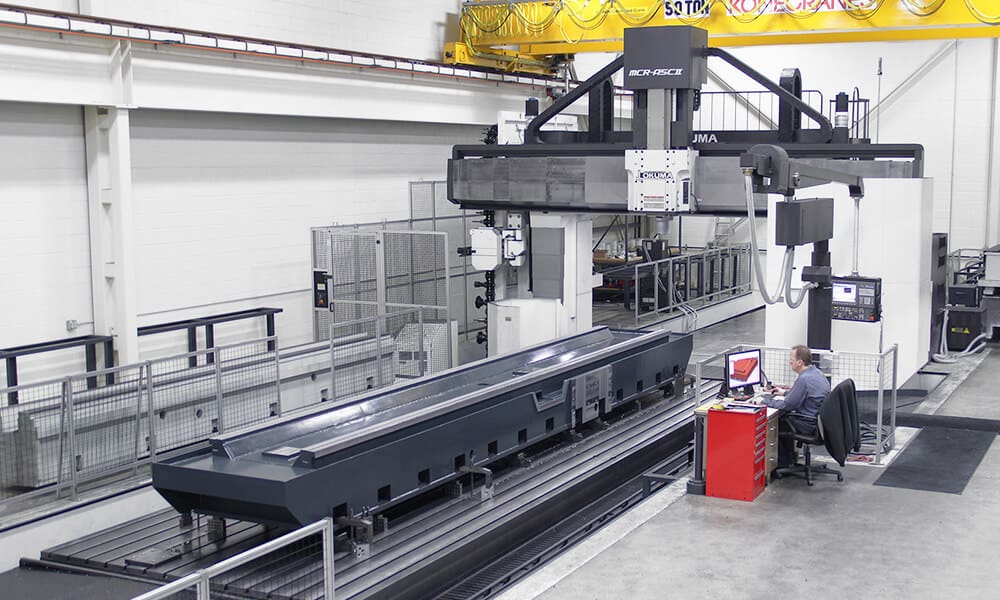

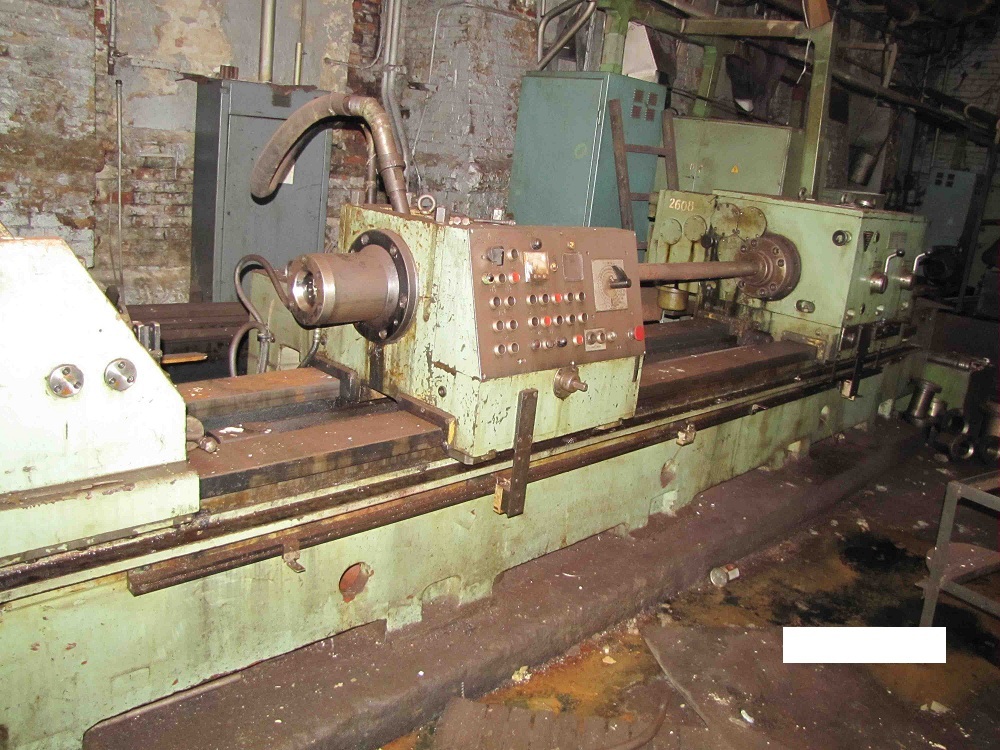






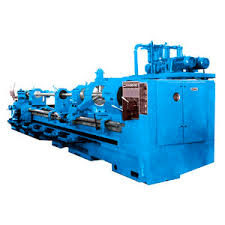

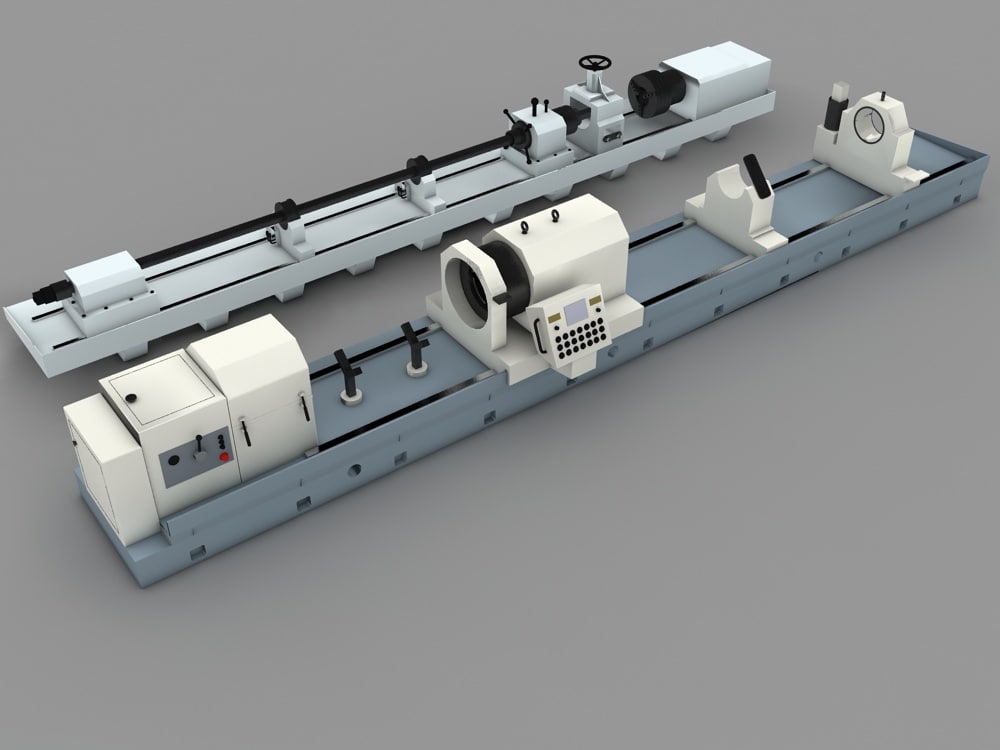


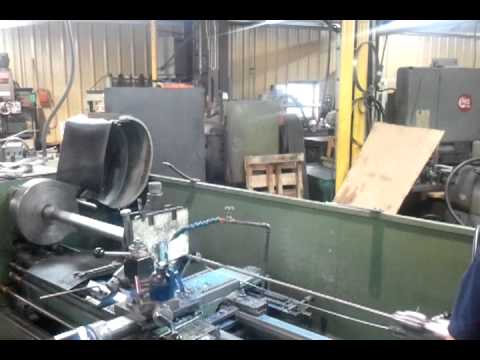


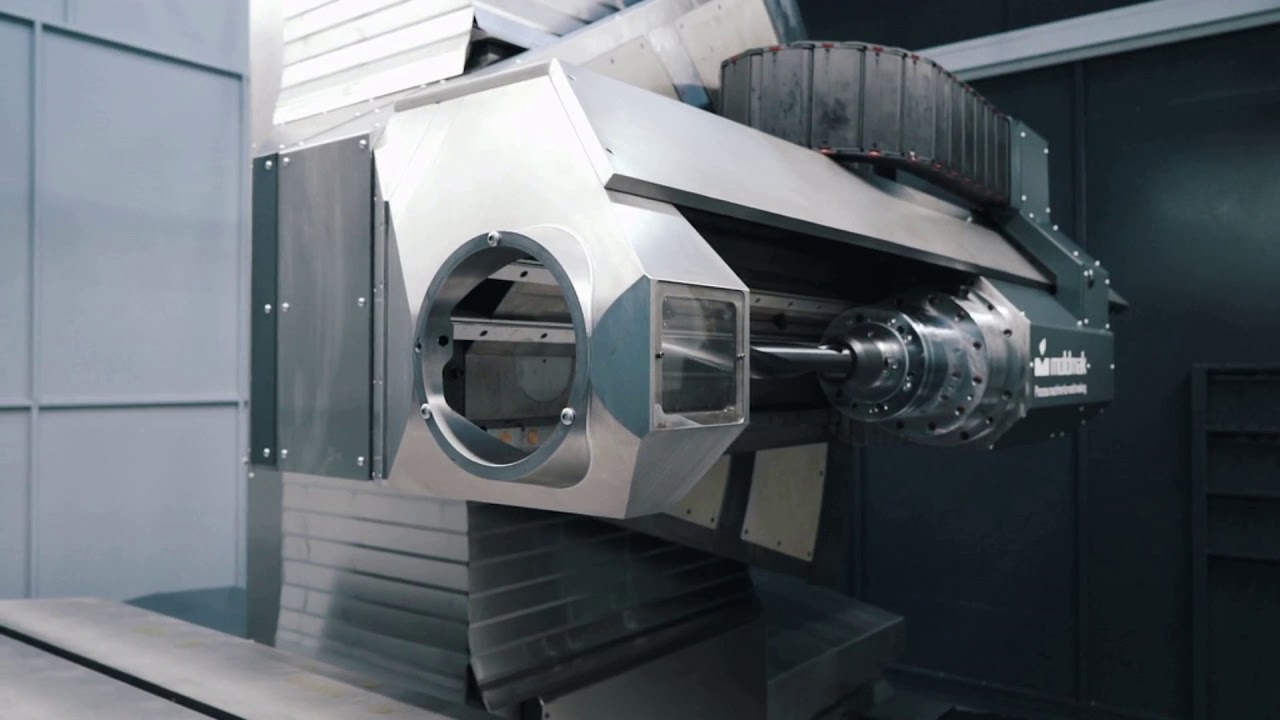





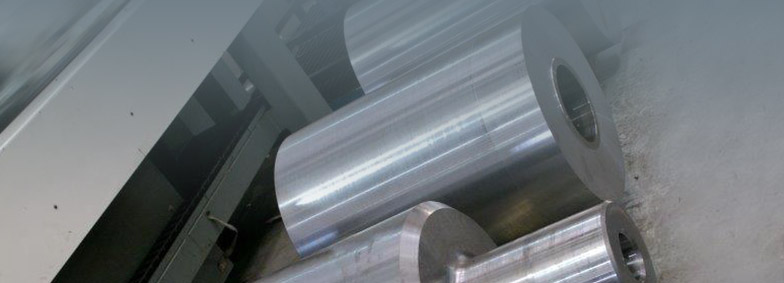

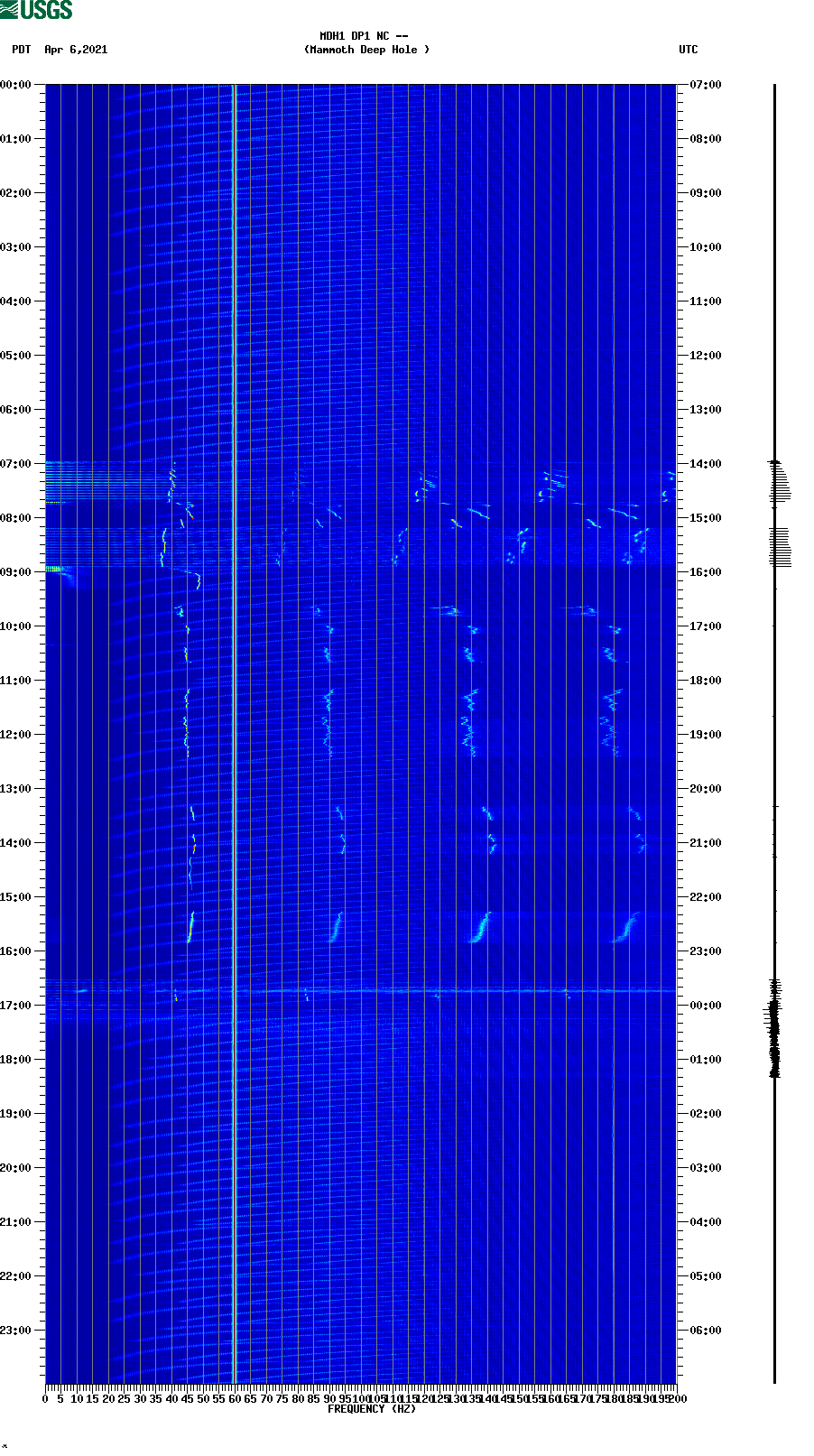



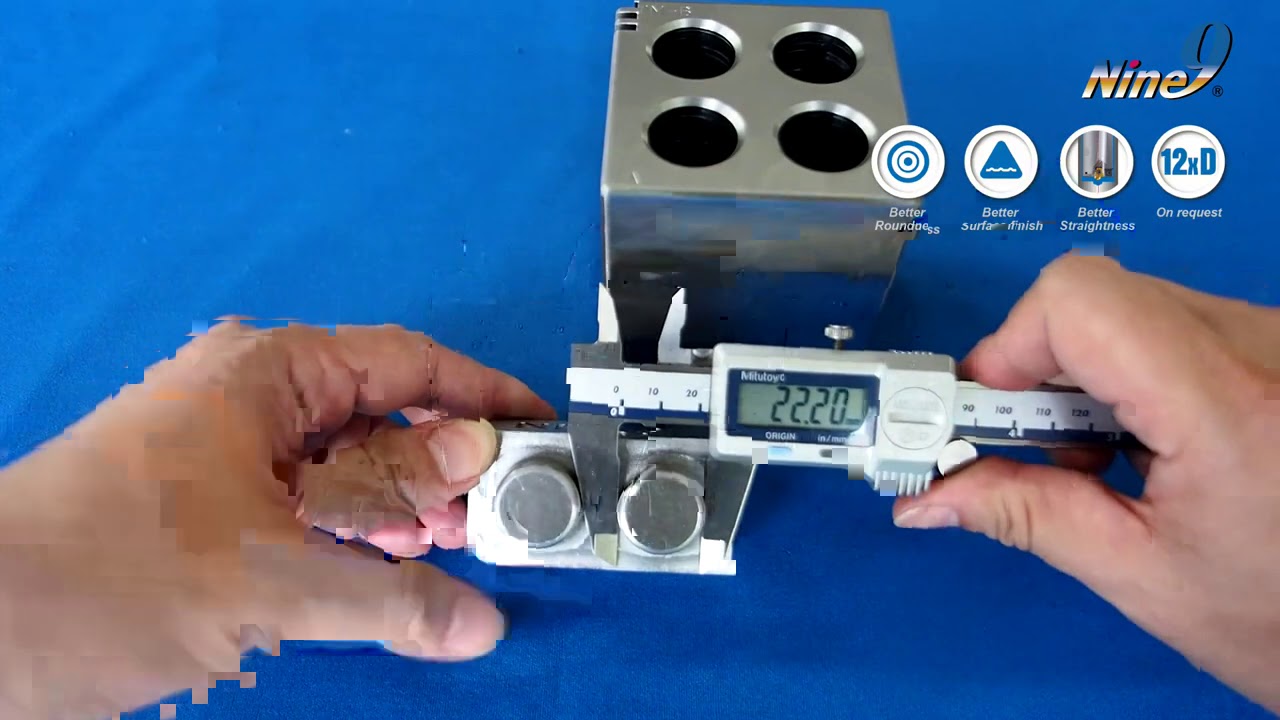
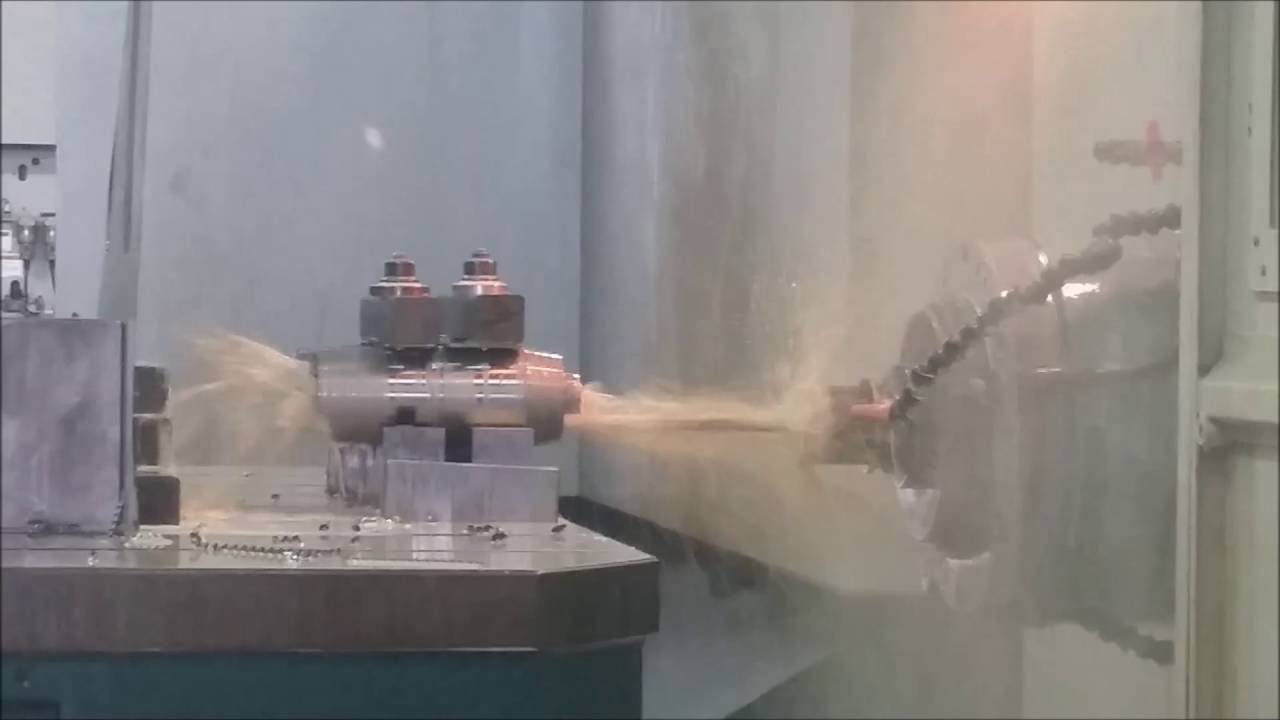
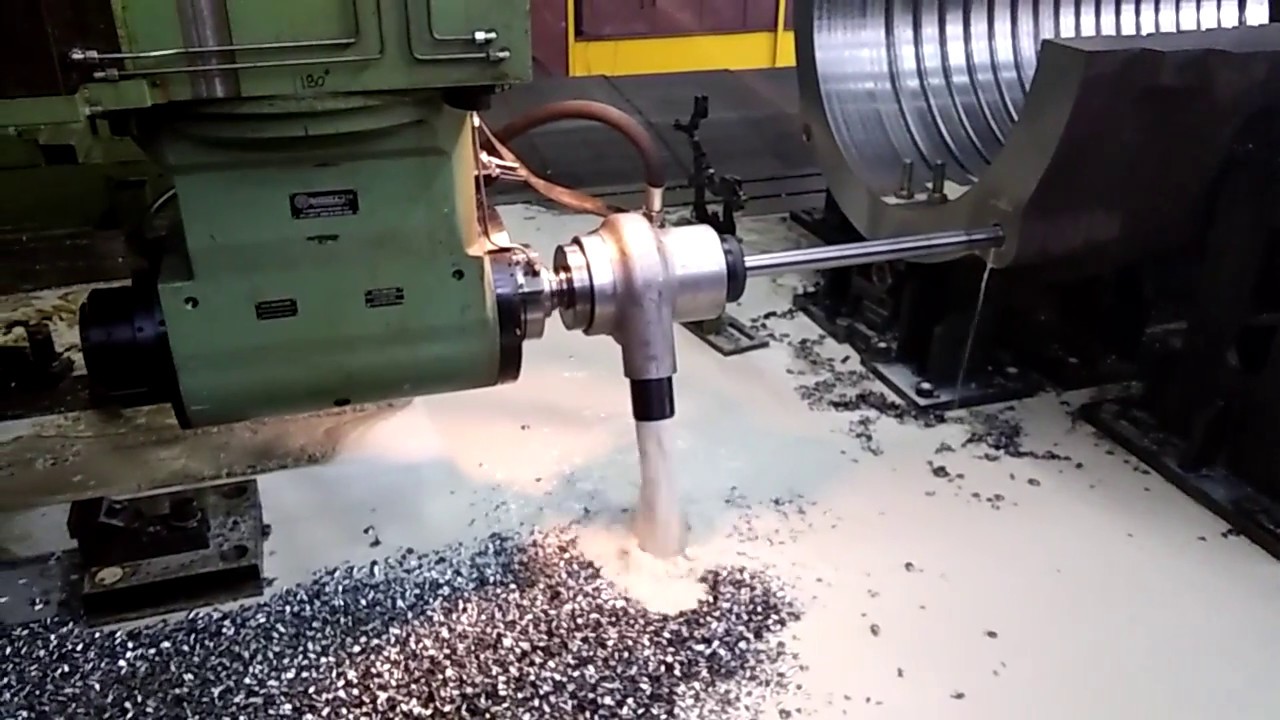




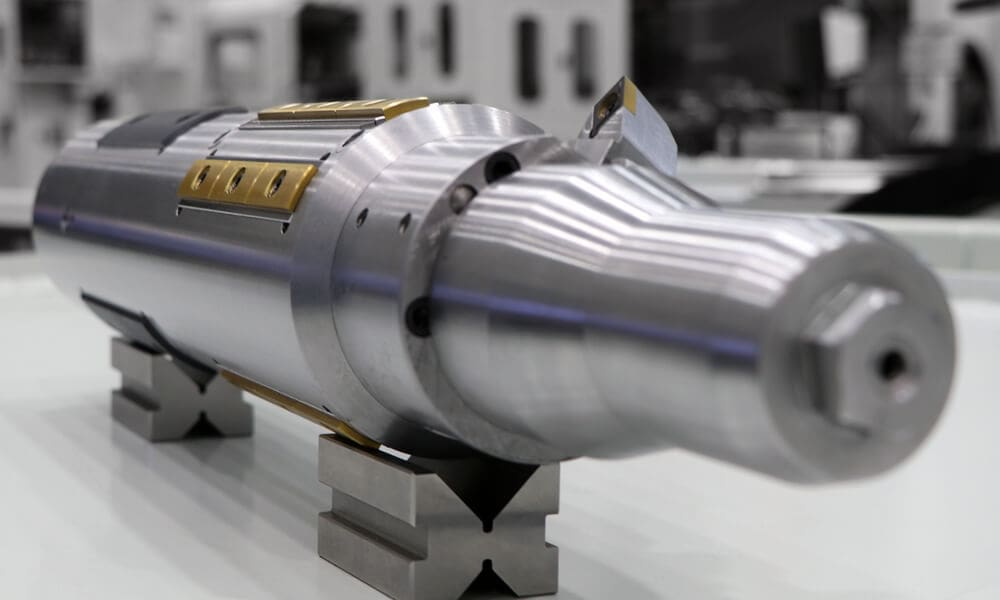

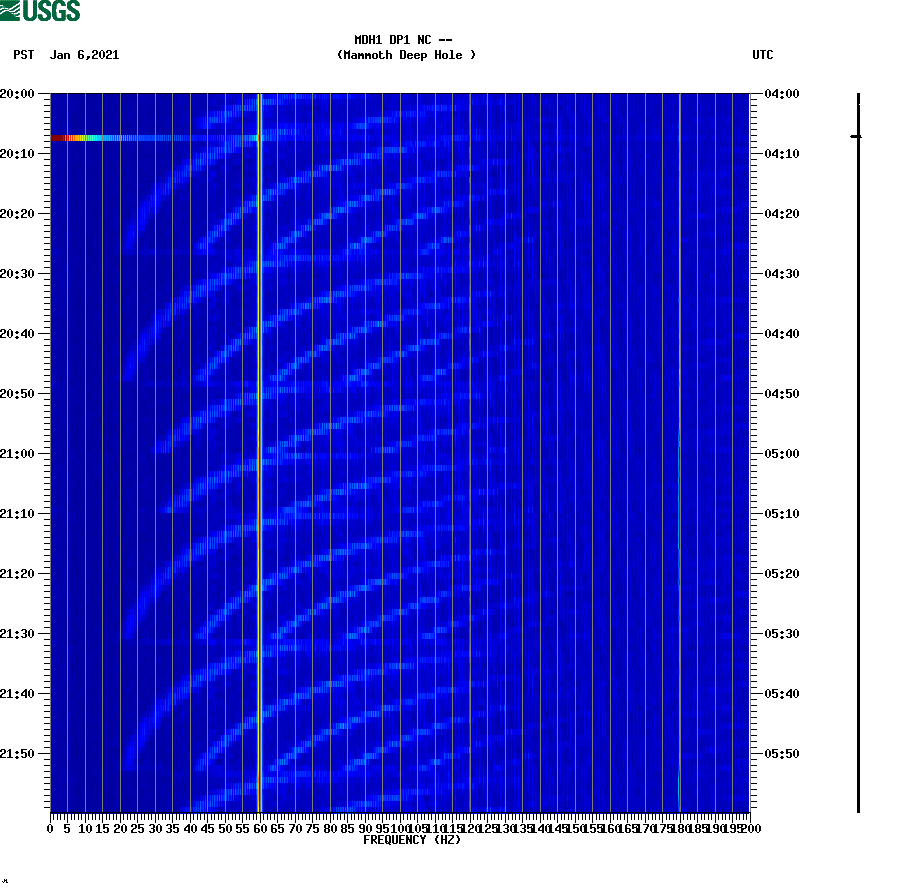



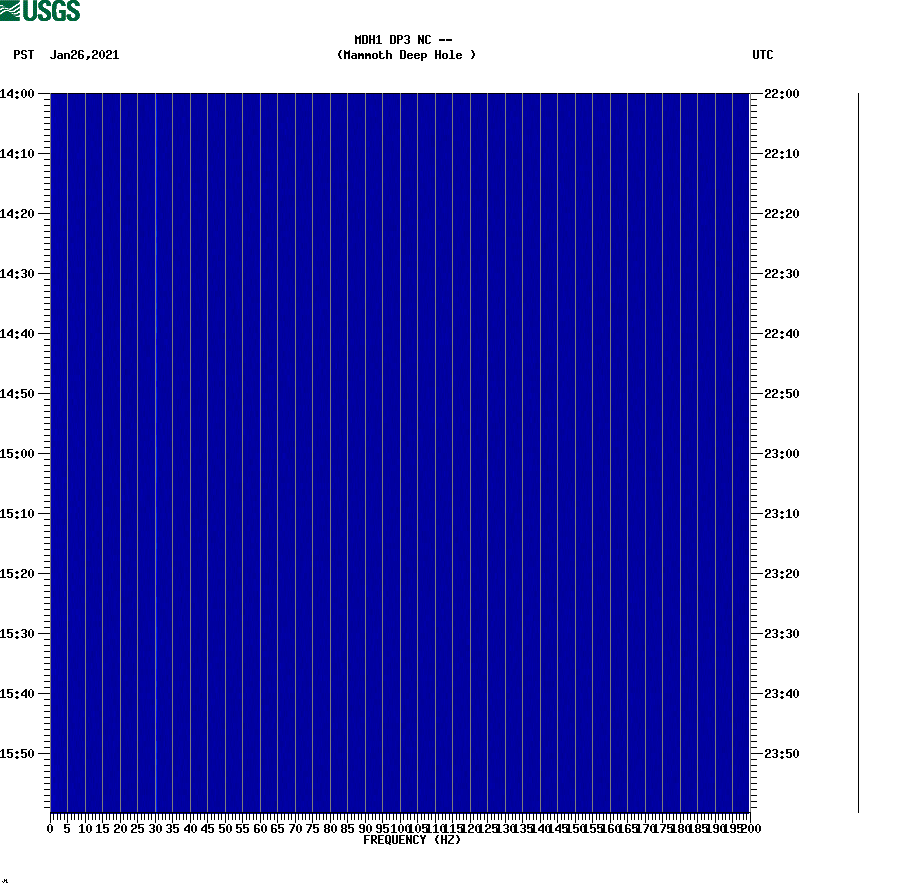

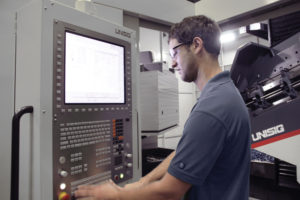
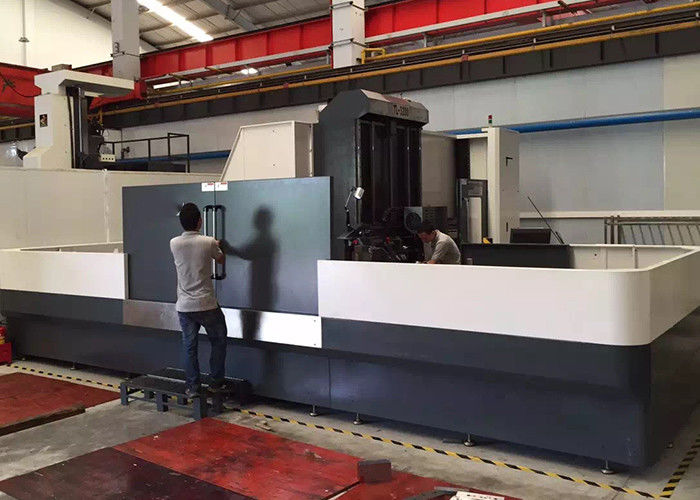


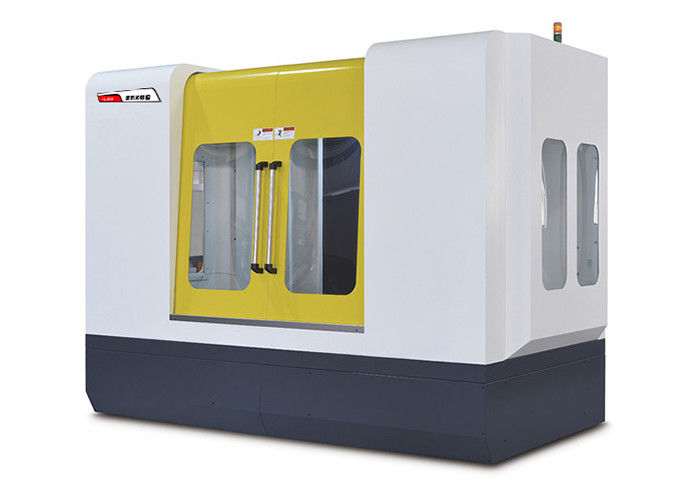

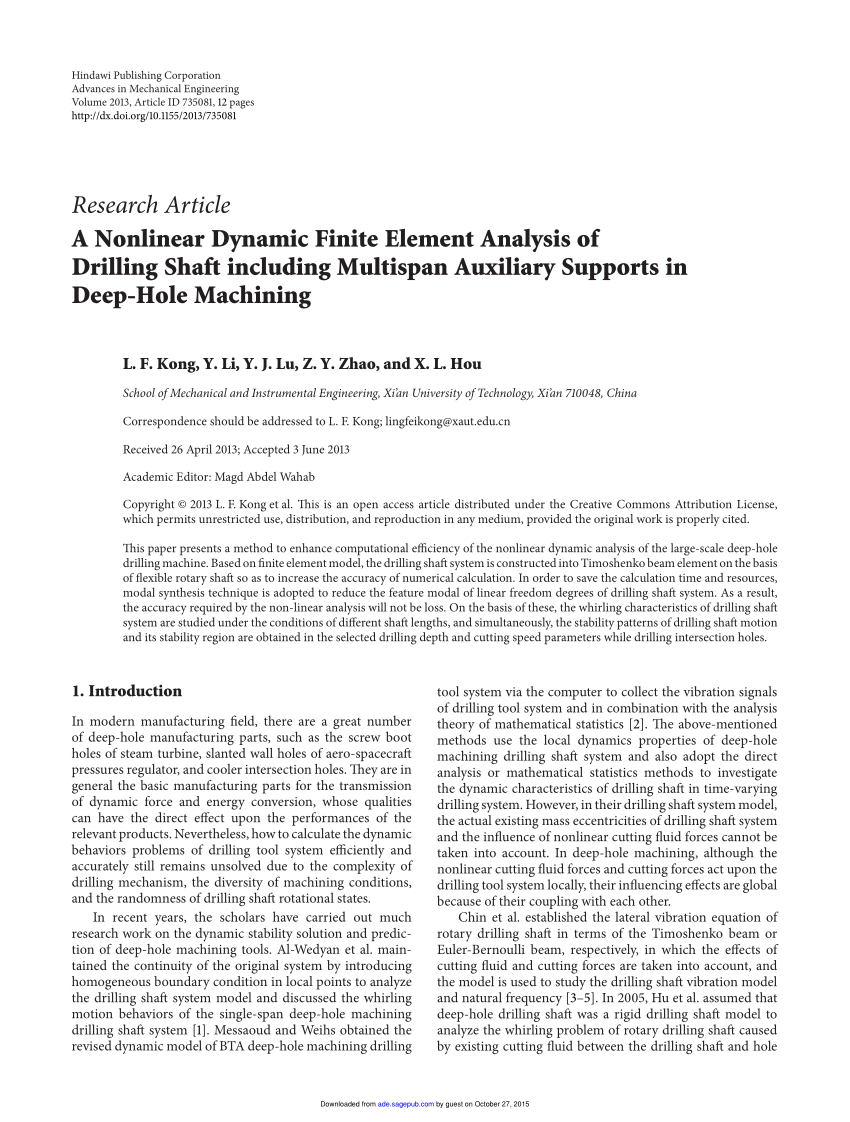
