Deep Hole Machining
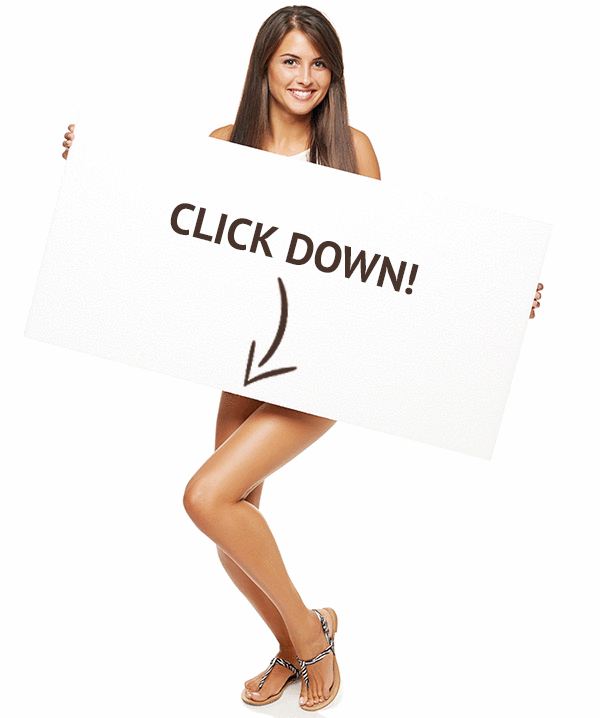
🛑 ALL INFORMATION CLICK HERE 👈🏻👈🏻👈🏻
Deep Hole Machining
Deep hole processing characteristics Shank of drill machine has a slender and rigid rigidity, and it is difficult to discharge the chips. Due to the tool cutting ability in the hole, cutting conditions and tool wear cannot be observed. Drilling deep hole method Diameter 3 ~ 20mm with a gun hole drill. Diameter 20 ~ 65mm with high-pressure internal chip removal deep hole drilling or with the suction drill, can also be used with indexable insert staggered deep hole drilling
Common problems and solutions Rough surface Chip bonding: reduce the cutting speed; avoid chipping; replace cutting fluid with high pressure and improve the filtration; increase pressure and flow of the cutting fluid. Poor coaxial: adjust the coaxiality of machine tool spindle and drill sleeve; use appropriate drill sleeve diameter. The cutting speed is too low, the feed rate is too large or uneven: use the appropriate cutting amount. Tool geometry is not suitable: change the geometry of cutting edge and the shape of a guide block
The orifice is flared Poor coaxial: adjust the coaxiality of machine tool spindle, drill sleeve and support sleeve; use the appropriate diameter of drill sleeve to replace oversized drill sleeve in time. Bit break The chip breaking is not good, the chips can not be discharged: change the size of chip breaking groove to avoid too long and too shallow; find the chipping situation in time and replace it; increase the pressure and flow of cutting fluid; use workpiece with the uniform material organization. The feed is too large, too small, or uneven: use the appropriate amount of cutting. Excessive wear of the drill bit: Regularly replace the drill bit to avoid excessive wear. The cutting fluid is not suitable: select the appropriate cutting fluid and improve the filtration. Low bit of life The cutting speed is too high or too low, and the feed rate is too large: use the appropriate cutting amount. Inappropriate bit: Replace tool material; change the position and shape of the guide block. The cutting fluid is not suitable: use the cutting fluid with high extreme pressure; increase the pressure, flow, and filtration of the cutting fluid.
Other Chips in strip shape: chipbreaker geometry is not suitable; cutting edge geometry is not suitable; feed amount is too small; workpiece material organization is uneven: variable chipbreaker and cutting edge geometry; increase feed rate; A material that is evenly organized. The chip is too small: the chipbreaker is too short or too deep; the chipbreaker radius is too small: the geometry of the chipbreaker is varied. Excessive chip: the chipbreaker is too long or too shallow; the chipbreaker radius is too large: the geometry of the variable chipbreaker
Tel: +82 51 315 1818 Fax: +82 51 311 1819 Add: 59, Nakdong-daero 916 beon-gil, Sasang-gu. Republic of Korea
Tel: +86 512 6290 1818 Fax: +86 512 6290 1819 Add: No.2018-E2, Haizang Road, Luzhi Town, Wuzhong District, Suzhou City, Jiangsu Province, 215127, China
This 5-Axis multifunctional machine is a column moving type gun drilling M/C. Machine’s work table can be classified into a fixed type, a rotary type and a type that can be transferred to front and back.
This BTA drilling machine is a column moving type deep-hole drilling machine equipped with the gun-drilling function with a small diameter and the BTA-drilling function with a large diameter or a combination.
Our drill center is 2-spindle gantry type drill center. While each spindle head is individually transferred, it is possible to execute duties at the same time.
Lathe type BTA drilling machine is a BTA drilling machine mainly used for shafts. It can be classified into a fixed tool with rotating workpiece and a rotating tool with rotating workpiece.
Our multi-axis gun drill machine is an exclusive 2-4 spindle equipment used for the processing of automobile steering rack bars, other automobile components and air craft parts.
Our special purpose gun drill machine is used to engrave notches on the steel roller.
Single Flut Gun Drilling Tools (Brazed Type) can be seen as the advanced and high-efficient deep hole process technology.
Twin Fluted Gun Drills Tools can be seen as the advanced and high-efficient deep hole process technology.
Shin-il BTA System Drilling Process can be seen as the advanced and high-efficient deep hole process technology.
From the shank to the tip, solid carbide CNC gun drills have full carbide construction, better for cooling liquid flowing.
Shin-il Machinery Co., Ltd. was established in 1971 and is a specialized manufacturer of special CNC machines with a history of nearly 50 years . The main products are CNC gun drilling machine (1 spindle, 2 spindles, multi-axis gun drill), BTA tube sheet drilling machine, high-speed drill center, a portable boring machine which supplied in fields of aerospace, medical, automobile, mold, petrochemical, nuclear power, wind power, heavy industry, construction industry, etc. We have successfully provided thousands of units for our customers.
We show our true hearts to serve every clients.
The problem of chip removal in gun-drilling deep hole drilling is still a technical problem. If the chips cannot discharge when processing steel, the chips
Gun drill deep hole processing has a long history. With the development of machinery manufacturing technology, the gun drill has become an effective method and
In the process of deep hole drilling, to improve the cutting efficiency, improve the accuracy of the workpiece, reduce the surface roughness of the workpiece,
Processing characteristics of deep hole drilling The tool holder is limited by the aperture, small diameter, and considerable length, resulting in insufficient rigidity, low strength,
The deep hole drill is a drill bit specially designed for machining deep holes, which can be divided into two types: outer chip removal and inner chip removal.
The biggest drawback of deep drilling is the difficulty of heat dissipation and chip evacuation.
The drill is specifically designed to machine deep holes.
When a hole depth ratio greater than 6 is usually referred to as a deep hole in machining.
In deep hole drilling, heat dissipation and chip removal are difficult, and the drill pipe is slender and has poor rigidity, which is prone to bending and vibration.
Cooling and chip removal problems are generally addressed by means of a pressure cooling system
Deep hole drill is divided into two types: outer chip removal and inner chip removal according to chip removal method.
There are gun drills, electric flute drills,s and deep hole twist drills for external chip removal; the internal chip removal is divided into three types: BTA deep hole drill, jet drill, and DF deep hole drill.
By using CNC spindles gun drills are usually with high-speed steel or hard alloy features.
Various types of internal chip removal deep hole drills can be constructed according to the size of welded or mechanically clamped indexable carbide inserts.
The guide block on the deep hole drill and centers to reduce deflection of borehole and vibration during cutting.
The arrangement of the teeth and guide blocks of deep hole drill mainly considers radial force balance during chipping and cutting.
The body and the drill pipe can be joined by welding or square threads.
No products were found matching your selection.
Drilling Machine: The process of machining a hole in a solid material with a drill bit is called drilling, and the special device for drilling is called a drilling machine.
Deep hole drilling machine : Deep hole drilling machine is one of the working parts of the tool that is mostly surrounded by the machined surface.
Therefore, there are problems such as rigidity, chip removal, guiding, and cooling lubrication of the tool.
The bit of deep hole drilling machine has poor rigidity and is easy to “bias” when drilling.
Limitation by the machining hole is the reason, which is generally long, and at the same time, it is required to have the largest possible chip on the drill bit.
The groove facilitates chip evacuation, which makes the core thinner and thus less rigid.
Due to the rigidity and guiding of the drill bit (drilling, only two narrow edges of the drill bit are in contact with the hole wall), the two main cutting edges are difficult to be symmetrical, and the radial forces cannot cancel each other out.
Moreover, the first contact with the machined surface during drilling is the chisel edge with a large negative rake angle, which makes it difficult for it to enter the cutting.
Therefore, the carbide drill bit is prone to “biasing” when drilling, resulting in the axis of a drilled hole. Skew or aperture expansion, not round, etc.
When drilling a deep hole with a special deep hole drill, the tool will exit quickly after a certain period of feed, the workpiece will be chipped, and then quickly approach machining part and continue to feed, so many times to reciprocate until required hole depth is processed.
Shin-il Stark Machinery (Suzhou) Co., Ltd
Copyright © 2019 Shin-il Stark Machinery (Suzhou) Co., Ltd
Complex machine parts, such as fuel injectors, Fuel Rails for diesel engines, heat exchanger tube sheets, aircraft landing gear, etc., need deep hole drilling machines. Deep hole drilling technology makes precision cuts considering the material types and thickness. Thus, most of the manufacturing industries are developing this specific deep hole drilling machine for more accuracy.
As long as we use metals, we must consider advancing the CNC machinery in the manufacturing area. However, this content will demonstrate a basic introduction to deep hole drilling, the different deep hole drilling technologies, applications, and upsides. In addition, we will also talk about some common issues you may encounter while using a deep hole drilling machine.
Deep hole drilling is a sort of drilling technology that can be manual or computer operated. A basic definition of Deep Hole Drilling would be its depth-to-diameter ratio (D:d). In this situation, you may term deep holes if the holes are larger than 10:1.
We have previously stated that DHD into metal offers a variety of applications across many sectors. Why is DHD valuable? Well, DHD enhances the many metals uses with its foundations going back to the requirement for straighter, more accurate gun barrels and extending as other industries adopted DHD techniques to improve their applications and quality.
Deep hole drilling methods operate by utilizing specific drilling tools and setups to supply high-pressure coolant, expel chips cleanly, and create depth-to-diameter holes into metal beyond what a typical CNC machine can reach. This process enables manufacturers to meet their manufacturing tolerances, and production needs reliably, precisely, and efficiently.
Deep hole drilling is usually done on specialized deep hole drilling equipment designed and constructed to optimize the procedures for straightness and efficiency.
However, DHD advancements in technology enable CNC machining centres, equipped with high pressure, through-spindle coolant, to allow different DHD Drilling up to a restricted depth-to-diameter ratio. There are a large number of machine vendors manufacture intelligent DHD machines improving the various application.
Deep hole drilling also varies from conventional drilling. Depending on the drilling procedure and the drilling diameter, one must supply cooling lubricants to the cutting blades in massive amounts and under high pressure.
This cooling lubricant provides excellent cooling and, at the same time, good lubrication of the contact regions between the workpiece and the cutting edge of the tool on the one hand and the workpiece and guiding pads of the device on the other. In addition, the cooling lubricant leads to continuous removal of chips from the cutting zone, which makes surface-damaging and time-consuming chip removal strokes unnecessary and thus enhances the quality of the borehole and the productivity of the operations.
Deep holes exist in various applications, spanning almost every sector, each with its own set of stringent criteria and unique difficulties, from tight tolerances to rigid materials to high production objectives.
DHD technology may accomplish the creation of deep holes using several different Deep Hole Drilling methods. Shops must achieve precision, repeatability, and excellent surface polish while preserving predictable tool life to produce a high-quality end product and keep costs under control.
However, Selecting the most suitable instrument for the task and applying the proper operating methods may enhance this challenging process, making it productive and lucrative.
In the following, we’ll discuss five deep hole drilling equipment and technologies: gun drilling, BTA drilling, ejector drilling, bottle boring tooling, and counterboring tooling .
Gundrilling is a deep hole drilling technique that utilizes a long, thin cutting instrument to create holes at high depth-to-diameter ratios. Gundrilling is usually successful in sizes from 1 – 50 mm [~0.04 – 2.00 in].
A gun drill varies from a typical twist drill by its unique head geometry; a standard gun drill has a single effective cutting edge that eliminates chips as it progresses into the workpiece.
Gun drills are renowned for producing long, straight, tight tolerance holes with excellent surface quality at a high penetration rate. A gun drill diverges from a conventional twist drill by its unique head geometry. A typical gun drill has a single effective cutting edge that eliminates chips as it progresses into the workpiece.
The gun drilling method can drill deep holes beyond what is feasible with traditional equipment and tools like twist drills using high-pressure coolant for clean chip removal, even at extreme depths.
These deep hole drilling tools maintain a position to exact tolerances, produce burr-free holes. You can resize them for precise requirements. Additionally, this process has unique, repeatable holes with excellent surface finishes, which avoids the necessity for one or more secondary or finishing operations.
Gun drills are readily connected with CNC machining centres, lathes, and milling machines for a relatively modest investment, making these tools cheap for small or big businesses with varied production needs.
There are various kinds of gun drills, Single Flute Solid Carbide, Two Flute, Indexable .
The gun drilling method can drill deep holes beyond what is feasible with traditional equipment and tools, such as twist drills, by utilizing high-pressure coolant for clean chip exhaust, even at extreme depths.
This drilling process is a deep hole drilling technique that utilizes a specialized drilling tool on a long drill tube to create deep holes in metal, from holes with a diameter of 20 mm [0.80 in] and bigger, up to depth-to-diameter ratios of 400:1. BTA drilling is the most successful way of drilling deep holes. It is a cleaner, more dependable, and competent operation than traditional twist drills and can reach bigger diameters and higher feed rates than the alternative gun drilling.
The drilling tool heads are threaded or fixed onto long drill tubes and utilize numerous cutting surfaces on a single tool to remove chips effectively, exhausting them using high-pressure coolant via holes in the tool head, then out the drill tube and into the machining spindle. Manufacturers offer BTA tooling in brazed or inserted carbide versions.
BTA stands for Boring and Trepanning Association . It is also frequently referred to as STS (single-tube system) drilling since it utilizes one single drill tube for the BTA tool instead of other procedures like ejector drilling, which requires two.
Ejector Drilling is a version of the BTA drilling technology. People primarily utilize this DHD technique on traditional machine tools and machining centres.
However, except for BTA deep-hole drilling, there is no sealing to restrict the escape of the metal-working fluid at the workpiece. Therefore, you may utilize this drilling method if it is not feasible to close the metal-working fluid circuit, e.g., for oblique boring or discontinuous workpieces. Drilling depths of up to 100 times D are achievable with this technique.
The machine supplies the metal-working fluid via an annular gap between the drill tube and an inner tube (double-tube system) (double-tube system). The fluid emerges from the side of the drilling head, runs over it, and then flows back into the inner tube together with the chips. It injects some of the fluid into the internal tube ring nozzle. The resultant under pressure at the chip mouth allows backflow (the ejector effect) (the ejector effect). An ejector cooling-lubricant feed system is needed to produce the ejector effect.
This DHD process is a tool that is used to create an internal profile inside the length of a bore utilizing a cutting insert, which is extended and retracted using CNC capabilities on a BTA-equipped deep hole drilling machine.
Bottle boring tools as a unique tool solution for customized design adaption to your requirements, Large feed-out stroke ratio, and maximum stability.
This DHD method is a tool that is used to implement complete bores by removing stock. This kind of tooling is usually utilized on BTA-equipped deep hole drilling machines.
Advantages of multi-edged counterboring tools include increased feed rates and better workpiece quality. Constant wall thickness is frequently a desirable outcome, which may be accomplished utilizing tool guiding in the tube.
In the operation of deep hole drilling, issues such as dimension accuracy, surface quality, and tool life frequently arise. How to minimize or perhaps prevent these issues is a significant problem to be addressed. After deep research, we have collected the most common points that you will find. We will try to mention them as straightforward as possible. Consecutively, we will also tell you how to prevent these issues.
This problem may arise due to the following situation:
Solve: The reamers with inadequate stiffness may adopt reamers with uneven tooth spacing, and the installation of reamers should adopt a rigid connection to enhance the primary deviation angle.
This issue may develop due to the following situation:
Solve: You can efficiently address this problem by taking care of the circumstances above, such as decreasing the cutting speed, selecting cutting fluid according to the processing material, etc.
This issue may arise due to excessive reaming allowed, improper distribution of rough and fine reaming allowance and selection of cutting parameters during reaming taper holes, tiny chip space of reamer teeth, and chip blockage.
Solve: You may address this issue by modifying the pre-machined aperture size and the allowance allocation. Also choosing the cutting parameters appropriately, decrease the number of reamer teeth, increase the chip space or grind the clearance of the cutter teeth will help you solve this issue.
This straightness issue may arise due to the following reason:
Solve: Increasing the reaming or drilling process corrective hole and decreasing the primary deviation angle may address this problem. Furthermore, you may also try adjusting the suitable reamer. And after that replace the reamer with the guiding part or extend the cutting portion. Always pay attention to the proper functioning.
DHD or Deep Hole Drilling is a famous drilling technology in the modern manufacturing industry. Generally, the drilling ratio between the length and diameter of the hole should be more than 10:1 to perform DHD.
Gundrilling and BTA drilling is the most common DHD procedure in metal drilling technology. There is a specific limitation for these two drilling processes. During operating these machines, you may encounter few common problems. We have stated them above.
Hair Women Porn
Horny Grandma Fuck
Mlp Hard Porn