Cone Penetration Test
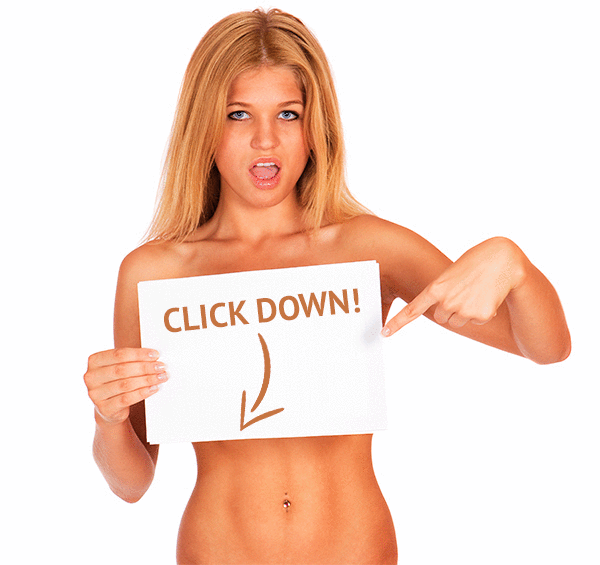
⚡ ALL INFORMATION CLICK HERE 👈🏻👈🏻👈🏻
Cone Penetration Test
URL: https://www.sciencedirect.com/science/article/pii/B9780080443812500230
URL: https://www.sciencedirect.com/science/article/pii/B9780081019443000085
URL: https://www.sciencedirect.com/science/article/pii/B9780081027660000031
URL: https://www.sciencedirect.com/science/article/pii/B9780080439815500547
URL: https://www.sciencedirect.com/science/article/pii/B9780128161913000043
URL: https://www.sciencedirect.com/science/article/pii/B9780081027660000055
(6.24) q u l t = α ¯ × q ¯ c , g = ( α 1 + α 2 ) / 2 × q ¯ c , g
(6.29) r = B 2 tan ( π 4 + φ 2 ) × 1 cos ( π 4 − φ 2 ) e θ tan φ
(6.30) D = y = r 0 e θ tan φ × sin ( θ − π 2 − ( π 4 − φ 2 ) )
(6.31) m = B 2 tan ( π 4 + φ 2 ) × 1 cos ( π 4 − φ 2 )
(6.32) D f B = tan ( π 4 + φ 2 ) e θ tan φ 2 cos ( π 4 − φ 2 ) sin ( θ − 3 π 4 + φ 2 )
(6.33) L θ = m 1 + t a n 2 φ t a n φ × ( e θ t a n φ − 1 )
(6.34) α 1 = L 0 L θ = ( π + π 4 − φ 2 ) = e θ t a n φ − 1 e ( 5 π 4 − φ 2 ) − 1
(6.35) A θ = m 2 4 tan φ ( L 0 L θ = ( π + π 4 − φ 2 = e θ t a n φ − 1 e ( 5 π 4 − φ 2 ) − 1 )
(6.36) A θ = m 2 / 4 tan φ ( e 2 θ tan φ − 1 )
(6.37) α 2 = A o A θ = ( π + π / 4 − φ / 2 ) = e 2 θ tan φ − e 2 ( 3 π / 4 − φ / 2 ) e 2 ( 5 π / 4 − φ / 2 ) − e 2 ( 3 π / 4 − φ / 2 )
(6.38) φ = log ( q ¯ c γ ' z ) + 0.5095 0.0915
q cg ¯ = q c 1 × q c 2 × q c 3 × … × q c 12 12 = 8683.1 Kpa = 86.83 kg cm 2
q c γ ' z ¯ = ( q c 1 γ ' z 1 ) × ( q c 2 γ ' z 2 ) × ( q c 3 γ ' z 3 ) × … × ( q c 12 γ ' z 12 ) 12 = 227.6
ϕ = [ l o g ( q c γ ' z ¯ ) + 0.5095 ] 0.0915 = 31.33
q u l t = α ¯ × q c g ¯ = 0.15 × 86.83 = 1.302 M P a
q u l t = F . S . × α × q c ¯ = 3 × 0.10 × 9.603 = 2.881 M P a
URL: https://www.sciencedirect.com/science/article/pii/B9780081027660000067
URL: https://www.sciencedirect.com/science/article/pii/B9780128042021000012
URL: https://www.sciencedirect.com/science/article/pii/B9780128046555000028
URL: https://www.sciencedirect.com/science/article/pii/B9780081027660000043
The cone penetration test (CPT) is where a pilot hole is drilled into the seabed and a special cone is then driven through the hole into the ground.
Jean M. Audibert , Jun Huang , in Handbook of Offshore Engineering , 2005
The CPT device and its peripheral systems are mounted onto a standard ROV tooling skid ( fig. 16.51 ). A Work-class ROV is then attached to the skid and the CPT and its sub-systems take their power from the vehicle's supply.
The 1 m long CPT push rod is thrust into the soil by a hydraulic ram. Due to the limited reactive force provided by an ROV, the CPT's cone area is reduced to 5 cm 2 .
The water depth capabilities of ROV CPTs are often only limited by the capacity of the vehicle. Hence, deployment down to 3000 m is quite feasible, although 1500 m is more the norm.
Mohamed A. El-Reedy PhD , in Onshore Structural Design Calculations , 2017
The cone penetration test (CPT) was invented and developed in Europe but has gained increasing importance in other parts of the world, especially in connection with soil compaction projects. Different types of mechanical and electric cone penetrometers exist, but the electric cone is most widely used. A steel rod with a conical tip (an apex angle of 60° and a diameter of 35.7 mm) is pushed at a rate of 2 cm/s into the soil. The steel rod has the same diameter as the cone.
The penetration resistance at the tip and along a section of the shaft (friction sleeve) is measured. The friction sleeve is located immediately above the cone and has a surface area of 15,000 mm 2 . The electric CPT is provided with transducers to record the cone resistance and the local friction sleeve.
A CPT probe equipped with a pore-water pressure sensor is called a CPTU. It is important to assure complete saturation of the filter ring of the pore-water (piezo) element as shown in Fig. 8.3 . Otherwise, the response of the piezo-transducer, which registers the variation of pore water pressure during penetration, will be slow and may give erroneous results. The CPTU offers the possibility to determine hydraulic soil properties (such as hydraulic conductivity–permeability), but it is most widely used for identification of soil type and soil stratification.
Figure 8.3 . Cone penetration test.
The CPT can also be equipped with other types of sensors, including vibration sensors (an accelerometer or geophone) for determination of vibration acceleration or velocity. The “seismic cone” is not yet used on a routine basis, but because of the relative simplicity of the test, it has potential for wider application especially on soil compaction projects.
The CPT is standardized, and the measurements are less operator-dependent than the SPT, thus giving more reproducible results. The implementation of the CPT is presented in Fig. 8.4 .
The CPT measures the cone resistance ( q c ) and the sleeve friction ( f s ) from which the friction ratio FR can be determined. FR is the ratio between the local sleeve friction and the cone resistance, expressed as a percentage ( f s / q c ). In spite of the limited accuracy of sleeve friction measurements, the valuable information which can be obtained in connection with compaction projects has not yet been fully appreciated. As will be discussed later, the sleeve friction measurement reflects the variation of lateral earth pressure in the ground, and can be used to investigate the effect of soil compaction on the state of stress. Cone and sleeve friction measurements are also strongly affected by the effective overburden pressure. It is necessary to take this effect into account, similar to the SPT.
One important objective of the CPT investigations in connection with soil compaction is to obtain information concerning soil stratification and variation in soil properties both in horizontal and vertical directions. The friction ratio is often used as an indicator of soil type (grain size) and can provide valuable information when evaluating alternative compaction methods.
Measurement of the excess pore water pressure with the CPTU can detect layers and seams of fine-grained material (silt and clay). It is also possible to obtain more detailed data concerning soil permeability and thus soil stratification.
The CPT tanks used to advance the cone into the ground mainly consist of a hydraulic jack and a reaction system. In some cases, other equipment such as an anchored auger is incorporated as well. The axial bearing capacity required for the test varies typically between 100 and 200 kN. However, there are also some systems with capacity ranging from 20 to 50 kN, which can be employed in soft soils.
The CPT tanks are usually placed in a truck weighing 15 ton or more, and torsional anchors can be implemented to provide the required reaction force. The power for the hydraulic jack is supplied by the truck's motor. The electrical equipment and computers needed for recording the test's measurements are located inside of the truck to provide an appropriate condition for monitoring the temperature and suitable protection of the electrical equipment. Different examples of CPT rigs and trucks are shown in Fig. 3.6 .
Figure 3.6 . Examples of cone penetration test trucks ( Robertson and Cabal, 2010 ).
A 20-ton penetrating system usually provides an insertion down to a depth of 30 m in medium dense sands and stiff clays. In weaker soils, penetration to the depths of more than 100 m requires the rods to be advanced adequately vertically. Layers with gravel or boulders, or zones with hard cemented soils considerably restrict the penetration, can damage the cone and rods, and deviate the rod from vertical alignment.
The cone penetration test (CPT) has been widely used in geotechnical engineering as an in-situ test to map soil profiles and assess soil properties. For instance, CPT test results in sand are often used to estimate soil friction angle and shear modulus. The applicability of estimation from such tests depends mainly on the proper interpretation of the test results. For this purpose, many studies have been oriented to the analysis of cone penetration and various empirical correlations have been proposed based on some simplified theories, such as, theory of bearing capacity ( Durgunoglu and Mitchell 1975, Robertson and Campanella 1983 ), the cavity expansion method ( Vesic 1972, Salgado et al. 1997 ) and calibration chamber test ( Houlsby and Hitchman 1988 ), etc. A good review was given by Yu and Mitchell (1998) .
In the past two decades, Numerical analysis of cone penetration has been performed by many researchers. However, due to the difficulties in modeling strong geometric nonlinearity of the problem, many analyses are limited to small strains or small-sliding on interface. For instance, small strain assumption is adopted by de Borst and Vermeer (1982). Baligh (1985) introduced the strain path method and a related finite analysis method, in which the pattern of deformation is described and the equilibrium equations may not be strictly satisfied. A special finite element procedure is also developed by treating the cone penetration as a steady state problem ( Herrmann and Mello 1994, Yu et al. 2000 ). In these analyses, the penetrometer is embedded in the soil and only a small penetration depth can be considered. Other finite strain studies include those proposed by Kiousis et al.(1988) and Gupta (1992) . But in these analyses, remeshing is necessary for the finite sliding on the penetrometer-soil interface.
The work presented here is on a rigorous finite element analysis of cone penetration in sands. The commercial finite element program ABAQUS is used for calculations due to its capacity of dealing with geometric nonlinearity and simulating large sliding on the penetrometer-soil interface as well. In this study, the penetrometer is assumed rigid. The soil is described with the Mohr-Coulomb elastic-perfect-plastic model. The full penetration process from ground surface to a certain depth of steady state is simulated (refer to Fig.1 ). The influences of various factors to the cone resistance are examined and results are compared with empirical correlations.
Fig. 1 . Finite element mesh: (a) undeformed and (b) deformed.
Mohamed Abdallah El-Reedy Ph.D. , in Offshore Structures (Second Edition) , 2020
By using CPT measurement as the basis for the previous methods to calculate the unit skin friction and end bearing for the pile there are some precautions and information that should be considered as in obtaining t–z data for axial load–deformation response, the peak unit skin friction in compression and tension at a given depth, f cz and f tz , are not unique and are both dependent on pile geometry. In general, the axial load and deformation response are affected by the pile penetration depth, the pile diameter, and its wall thickness. Noting that, an increased pile penetration will decrease these ultimate values at a given depth.
In the case of doing the test to obtain the q–z data for axial load–deformation response, the end bearing ( Q p ) is assumed to be fully mobilized at a pile tip-displacement value of 0.1 D .
Soil types such as carbonate sands, micaceous sands, glauconitic sands, volcanic sands, silts, and clayey sands have unusually weak structures with compressible grains. These require special consideration in situ and in laboratory tests for the selection of an appropriate design method and design parameters according to Thompson and Jardine (1998) and Kolk (2000) for pile design in carbonate sand, and Jardine et al. (2005) .
It is worth mentioning that in the case of using CPT in cohesionless soil, such as gravel, when particle sizes are in excess of 10% of the CPT cone diameter, they are misleading, and one possible approach could be to use the lower-bound q c profile. In this case, one can estimate the end-bearing capacity profile from the adjacent sand layers.
In the case of using CPT in weaker clay layers near the pile tip, it is recommend that obtaining q c data averaged between 1.5 D above the pile tip to 1.5 D below the pile tip level should generally be satisfactory, provided q c does not vary significantly. The UWA method should be used, if there is significant q c variations occur, to compute q c,av .
The case of a thin clay layer, which is less than around 0.1 D thick, is a problem, especially when CPT data are discontinuous vertically or not all pile locations have been investigated. From a practical point of view, the offshore piles usually develop only a small percentage of q p under extreme loading conditions. Therefore the finite element method can be used in calculating the pile capacity and settlement of a pile tip on sand containing weaker layers, and may be considered to assess the axial pile response under such conditions.
It is recommended that the end-bearing component be reduced in the case that the pile tip is within a zone up to ±3 D from such layers. When q c data averaging is also applied to this ±3 D zone, the combined effects may be unduly cautious and such results should be critically reviewed; this rule is applied also in the case of large pile diameter ( D >2 m).
The CPT methods (mechanical cones) do not correct for the pore pressure on the cone shoulder, and the profiling developed based on CPT data may not be relevant outside the local area where they were developed. The error due to omitting the pore water pressure correction is large in fine-grained soils and small in coarse-grained soils.
Except for the profiling chart by Begemann (1965) and Eslami-Fellenius (1997) , all of the referenced soil profiling methods plot the cone resistance versus its own inverse value in one form of another. This generates data distortion and violates the rule that dependent and independent variables must be rigorously separated.
Some profiling methods, e.g., Robertson (1990) , include normalization which requires complicated manipulation of the CPT data. For example, in a layered soil, should a guesstimated “typical” density value be used in determining the overburden stress or a value that accurately reflects the density? Moreover, regardless of soil layering, determining the effective overburden stress (needed for normalization) requires knowledge of the pore pressure distribution, which is not always hydrostatic but can have an upward or downward gradient, and this information is rarely available.
The normalization by division with the effective overburden stress does not seem to always lead to correct classification. For example, the normalized values of fine-grained soils obtained at shallow depth (where the overburden stress is small) will often plot in zones for coarse-grained soil.
The Robertson (1990) and the Eslami–Fellenius (1997) CPTu methods of soil profiling were applied to data from three geographically apart sites having known soils of different types and geologic origins. Both methods identified the soil types accurately.
Eslami–Fellenius (1996) method has the advantage over Robertson (1990) that it avoids the solecism of plotting data against their own inverted values and associated distortion of the data.
Eslami–Fellenius (1997) method has the additional advantage over other referenced piezocone methods in that it allows the user to directly assess a value without first having to determine distribution of total and effective stress to use in a subtraction and multiplication effort in calculating a “normalized” set of values.
A soil profiling chart based on a Begemann-type plot, such as the Eslami–Fellenius (1996) method can easily be expanded by adding delineation of strength and consistency of fine-grained soils and relative density and friction angle of coarse-grained soils per the user-preferred definitions or per applicable standards.
No doubt, CPTu sounding information from a specific area or site can be used to further detail a soil profiling chart and result in delineation of additional zones of interest. However, there is a possibility in producing a very detailed chart inasmuch as the resulting site dependency easily gets lost, leading an inexperienced user to apply the detailed distinctions beyond their geologic validity.
The CPTu is an excellent tool for the geotechnical engineers in developing a site profile. Naturally, it cannot serve as the exclusive site investigation tool, and soil sampling is still required. However, when the CPTu is used to govern the depths from where to recover soil samples for detailed laboratory study, fewer samples are needed, reducing the costs of site investigation while simultaneously increasing the quality of the information.
The attempts to predict pile toe capacity from CPT data were generally successful, whether the unit toe resistance was taken directly from the q c value at pile toe level or taken as the average of q c values for some distance above and below the pile toe. However, there is still some skepticism regarding application of small-scale cone penetrometer to large-scale deep foundations, which referenced as scale effect. Considerable insight into these problems was provided by De Beer (1963) in a thorough study of the effect of pile or penetrometer size on the ultimate toe bearing capacity. By considering penetrometers of different size, De Beer showed that all penetrometers should ultimately attain the same point resistance and the depth at which this constant value occurs must be proportional to the penetrometer size.
The explanation offered by De Beer (1963) for this phenomenon was that the bearing capacity failure which occurs beneath the cone tip gradually changes from that for a shallow foundation to that of a deep one as shown in Fig. 6.2 .
During the transition between the shallow- and deep-type base failure, the point resistance increases linearly with depth, but after the deep foundation condition is reached, point resistance only increases slightly with increased penetration. The depth in which this condition is met is termed the critical depth (D c ). The correct value of D c is more difficult to determine. Meyerhof (1976), De Beer (1963) , and Eslami and Fellenius (1997) have shown that the D c is a function of the foundation size and soil density. Thus it is more convenient to express this depth in terms of the ratio of the foundation size to the critical depth, i.e., (D/B) c . Both experimental and theoretical studies have denoted that (D/B) c for sands is a function of the sand density and varies from about 5 for loose sands to about 15 for dense sands.
Research by De Beer (1963), Meyerhof (1976) , and Eslami and Fellenius (1997) indicated that a type of logarithmic spiral failure zone and attributed rupture surfaces to reach penetrometer body need a penetration depth of almost 10 times of penetrometer diameter to fully mobilize the ultimate unit toe resistance. In other words, penetration depth of at least 10 footing width or cone diameter is required to transform shallow to deep mechanism of rupture surface. In the former, the rupture surface extent to the ground level but for the latter, the rupture surface reaches to the penetrometer or footing body at deep soil level.
A direct CPT method by Eslami and Gholami (2006) was developed based on an analytical model for determining ultimate bearing capacity, q ult , of shallow foundations from CPT cone resistance, q c . Regarding the basic bearing capacity formula, the length (L) confining and depth of rupture surface, i.e., embedment depth (A), have a major role in mobilized foundation bearing capacity. These two key factors can be regarded in a rational matter for connection of shallow rupture surface to deep entirely mobilized failure zone. Therefore, the q ult to q c in direct approach can be correlated by a general rule as follows:
q ¯ c , g = geometric average of q c values from footing base to 2B beneath footing dept
Charmel Lingerie
Nudists Albums
Overwatch Watch