Bottom Hole Assembly
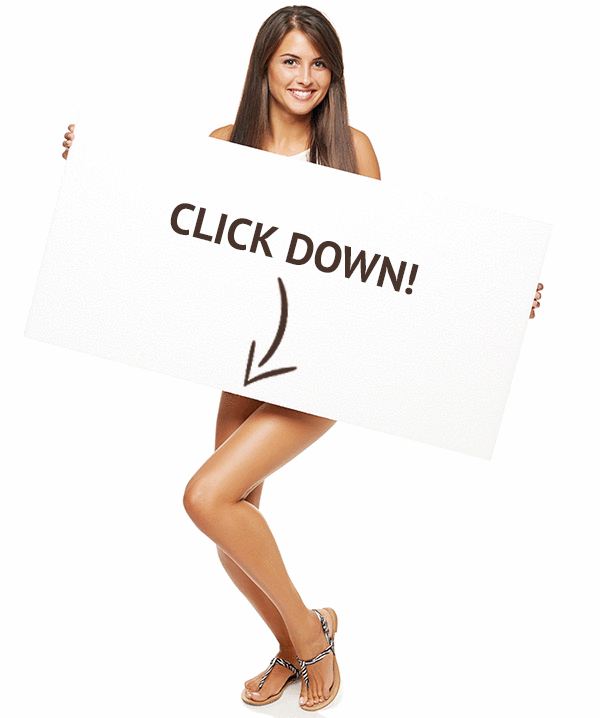
⚡ ALL INFORMATION CLICK HERE 👈🏻👈🏻👈🏻
Bottom Hole Assembly
EN
FR
DE
ES
IT
HR
SV
SR
SL
NL
Home
Oilfield Companies
Job Description
Privacy Policy
About Us
Contact Us
Sitemap
Facebook
Youtube
Twitter
Linkedin
Telegram
Pinterest
Home » Drill String » Bottom Hole Assembly BHA Components and Design
We and our partners use cookies to Store and/or access information on a device. We and our partners use data for Personalised ads and content, ad and content measurement, audience insights and product development. An example of data being processed may be a unique identifier stored in a cookie. Some of our partners may process your data as a part of their legitimate business interest without asking for consent. To view the purposes they believe they have legitimate interest for, or to object to this data processing use the vendor list link below. The consent submitted will only be used for data processing originating from this website. If you would like to change your settings or withdraw consent at any time, the link to do so is in our privacy policy accessible from our home page.
Manage Settings
Allow Necessary Cookies & Continue
Continue with Recommended Cookies
The drilling bottom hole assembly (BHA) is one of the components of the Drilling String which is below the Drill Pipes. The most common components of the BHA are Drill Collars, Stabilizers, Shock Absorbs, Jars, Reamers, Heavy Weight Drill Pipes, and The Drilling Bit.
The purpose of the Bottom Hole Assembly BHA is to drill a usable hole economically. This objective is achieved with the proper Drill Bits Selection and Drill Collars selection which are required to provide high WOB bit weights to Improve ROP The Penetration Rate.
Stabilizers are one of the bottom hole assembly BHA components needed to minimize the rate of hole angle change and prevent the formation of doglegs and key seats .
Shock absorbers play an important part to prolong the service life of the bit and drill pipe. Downhole drilling jars may be needed to unstick the BHA.
The Bottom Hole Assembly BHA design is based upon the requirements of having enough weight transfer to the bit (WOB) to be able to drill and achieve a sufficient The Penetration Rate (ROP), giving the Driller or Directional Driller directional control to drill as per the planned trajectory and to also include whatever
Logging While Drilling (LWD) / Measurement While Drilling (MWD) tools for formation evaluation. As such Bottom Hole Assembly BHA design can vary greatly from simple vertical wells with little or now LWD requirements to complex directional wells which must run multi-combo LWD suites.
Prior to running a BHA most oilfield service providers have software to model the BHA behavior such as the maximum WOB achievable, the directional tendencies & capabilities, and even the natural harmonics of the assembly as to avoid vibration brought about by exciting natural frequencies.
Rotary assemblies are commonly used where formations are predictable and the rig economics are an issue. In such an assembly the weight of the drill collars gives the BHA the tendency to sag or flex to the low side of the hole, collar stiffness length, and stabilizer diameter and placement are engineered as a means of controlling the flex of the BHA. this will bring about the desired hold, build or drop tendency. The ability to vary the directional tendency of the assembly comes from varying the weight on the bit. A fixed assembly has only one directional tendency. The weight on the bit allows you to tune that tendency
which may be using mud motor with a bent sub or using rotary steerable systems
Heavy Weight Drill Pipe Specs is important to understand as it is the entrance of the heavyweight drill pipe design. In this article, we will discuss its specs and how to select in the drill string design. In addition to that, we will talk about its main functions. you can also download the specs sheets from any size of heavy-weight drill pipes.
Drill-collar (D/C) are large diameter-small bore steel pipes that possess a great weight and great stiffness. While designing BHA, drilling engineers place D/Cs above the Drilling Bit as D/Cs are which is the predominant component of the Drilling Bottom Hole Assembly BHA components. To select the proper D/C you will have to have all information about Drill collar Weights, Size, Specs, Definition, lengths & Types.
Drilling stabilizer types & design is the main subject of this article. First, we will introduce to you the definition of stabilizer as one of the bottom hole assembly BHA components. Then we will move to the stabilizer application. And finally, we will talk about its types.
Reamers types are the subject of our article. In general, we can say that reamers types are: under-reamers type, Roller Reamers Type, RFID Reamers Type, Near-Bit Reamers Type, Expandable Reamers Type.
Drilling jar placement design is important while drilling. In general, jars are one of the bottom hole assembly BHA components that generate upward or downward impact loads to free stuck pipe or release a fish. There are many factors that affect the decision of when to use jars and where to position them for maximum benefit.
This article is including many articles which cover what you will need to understand Drill Bits.
Drill pipes are not one of the bottom hole assembly BHA components but we shall mention it as a drill string component. This article mainly explains the drill pipe description in simple points to understand how you will select the drill pipes in the drill string.:
Rotary assemblies are designed to build, drop, or hold angles. The behavior of any rotary assembly is governed by the size and placement of stabilizers within the first 120 ft from the bit.
Additional stabilizers run higher on the drill string will have a limited effect on the assembly’s performance. Rotary assemblies are not “steerable”; first, the azimuth behavior (right/left turn) of a rotary assembly is nearly uncontrollable.
Second, each rotary assembly has its own unique build/drop tendency that cannot be adjusted from the surface. Thus, tripping pipe for the assembly change is required to correct the wellbore course.
Main Rotary BHA Types are: Slick assembly, fulcrum, and Pendulum Assembly
Please consider that any articles or Ads here related to Forex, Banking, any Adult sites & any Dating Websites are haram. Thanks
Oilfield Fishing Tools With Catalogs
5 Main Junk Basket Types in Oil & Gas Market
Junk Mill In Oil And Gas Types & Guidelines
Formation Integrity Test Procedure & Calculation
How Does life on an Oil Rig Look Like?
Drill Pipe API Specifications, Thread Types &Tables
Cementing Calculations- 7 Steps & Spreadsheets
Download Workover & Drilling Rig Inspection Checklist
Free Wellbore Schematic Excel Template
Bottom Hole Assembly BHA Components and Design
Home
Oilfield Companies
Job Description
Privacy Policy
About Us
Contact Us
Sitemap
Facebook
Youtube
Twitter
Linkedin
Telegram
Pinterest
Home » Drill String » Types Of Bottom Hole Assembly BHA Used In Oilfield
In this article we will talk mainly about the application for different types of bottom hole assembly (slick bha drilling, Pendulum Assembly & Packed BHA) its design & components. This article is a part of the our drill string design guide .
In general there are three types of Bottom Hole Assembly BHA In drilling:
This type of bottom hole assembly (slick BHA) consists of a Drill Bit and Drill Collar without Stabilizer . Slick BHA is suitable for formations which have mild crooked hole tendencies. Slick bottom hole assemblies are seldom. As there are no expensive components on this type of BHA, It is more easier to fish such BHA.
Sometimes when you want to wash and ream (clean out) in some difficult holes. We choose to pull out of the current directional BHA and to try to design a slick BHA but with the same configuration of the directional BHA. In other words it will be a slick BHA, as you won’t add any BHA component but you will have to use stabilizers with the same OD and the same position of any part of directional BHA previously drilled this hole so that to keep the geometry of cleaning assembly (which will be slick BHA with some stabilizers as same as the geometry of the directional bottom hole assembly).
The Pendulum BHA Assembly is one of the types of bottom hole assembly which we can use primarily to reduce or maintain hole deviation. The pendulum technique relies on the force of gravity to deflect the hole to vertical. The force of gravity, F sin I in the above figure, is related to the length of Drill Collars between the Drilling Bit and the point of tangency. The along-hole component of the force F is F cos I, which attempts to maintain the present hole direction.
The pendulum type of bottom hole assembly BHA consists of a Drilling Bit, several Drill Collars to provide the pendulum force and one or more Stabilizers. Lubinski presented charts for determining the location of the first Stabilizer from the Drilling Bit and the weight that can be applied on the Drilling Bit to maintain best position of the Stabilizer is as high as possible provided the Drill Collars below Stabilizer do not contact or barely contact the wall of the hole .
The optimum position of the Stabilizer depends upon the size of the Drill Collars, size of hole, hole inclination and Weight On Bit (WOB). So if we can maintain the weight On Bit (WOB) from the graphs constant, the hole deviation will not change. If the Weight On Bit (WOB) increased, the hole angle will increase and the opposite is true.
Relies on the principle that two points will contact and follow a sharp curve, while three points will follow a straight line as shown . We can obtain three-point stabilization by placing three or more Stabilizers in the portion of the hole immediately above the bit.
We are using this bottom hole assembly type for formations which have mild crooked hole tendency that produce little or no deviation such as hard and isotropic rocks. The three-point stabilization is provided at Zone-1, immediately above the Drilling Bit, at Zone 2, immediately above a short, large OD drill Drill Collar; and at Zone 3, on top of a standard length drill Drill Collar.
We always utilize this type of Bottom Hole Assembly BHA for formations which have medium crooked hole tendency such as medium and soft formations. In this type of Bottom Hole Assembly BHA, we place a second Stabilizer at Zone-1 in order to provide increased Drilling Bit stabilization against deviation effects of the formation.
Drilling engineers utilize this type of Bottom Hole Assembly BHA in drilling formations which have severe crooked hole tendency such as medium and soft formations which show a great degree of dipping , fracturing and variation in strength. In this type of Bottom Hole Assembly BHA three Stabilizers are include in Zone-1.
Any types of bottom hole assembly (Drilling BHA) Tendency is affected by the Forces Acting On Bottom Hole Assembly which will drive it into a certain direction. These Forces must be understood to be able to choose the most applicable Bottom Hole assembly BHA type. Let’s move back to our main subject Step By Step Learn How To Perform Full Drill String Design
Please consider that any articles or Ads here related to Forex, Banking, any Adult sites & any Dating Websites are haram. Thanks
Derrick In Drilling Rigs Complete Guide
Oilfield Fishing Tools With Catalogs
Drill Pipe API Specifications, Thread Types &Tables
Cementing Calculations- 7 Steps & Spreadsheets
Download Workover & Drilling Rig Inspection Checklist
Free Wellbore Schematic Excel Template
Bottom Hole Assembly BHA Components and Design
Main
News
Photo
Video
Oilfield Jobs
Learning Section
Oil & Gas Calculator
The 2022 edition lists API standards, recommended practices, and other technical documents to help t…
We collected the best oilfield tattoos list. You can send your oilfield tattoos to us via IG or FB.
Drilling methods for different formations
Drilling unconsolidated formations, Drilling firm but stable formations with high drillability, Dril…
Once the hole is made and cuttings are cleared from the bit face, these cuttings must be completely…
Market quotes are powered by
TradingView.com
About Us
| Contact Us
| Privacy Policy
The bottomhole assembly (BHA) is the component of the drill string located directly above the drill bit and below the drill pipe. The primary component of the BHA is the drill collar. Therefore, it has a signifi cant effect on drill bit performance. The other components of BHA are stabilizers, jars, reamers, crossovers, shocks, hole-openers, and various subs such as bit subs, shock subs (Figure-1). In addition to these main components, the BHA typically consists of a down hole motor, rotary steerable system (RSS), and measurement and logging while drilling tools (MWD and LWD respectively. However, some classify the drill bit as a part of the BHA. It hangs below the drill pipe and provides weight to the drill bit to induce the teeth to penetrate the formation. The functions of BHA are i) to protect the drill pipe in the drill string from excessive bending and torsional loads, ii) to control direction and inclination in directional holes, iii) to drill more vertical and straighter holes, iv) to reduce severities of doglegs, key seats, and ledges, v) to assure that casing can be run into a hole, vi) to reduce rough drilling (rig and drill string vibrations), and xi) as a tool in fi shing, testing, and work over operations.
1. Drill Collars : Drill collars (DC) are heavy, stiff steel tubulars, which have a much larger outer diameter and generally smaller inner diameter than a drill pipe. They are used at the bottom of a BHA to provide weight on bit and rigidity. The primary function of the drill collar is to provide suffi cient weight on bit. The weight of the collar also ensures that the drill pipe is kept in tension to prevent buckling. Figure-2 shows a typical short drill collar and non-magnetic drill collar. It is a pipe with thick walls that are attached to the bottom of the drill string. Therefore it has a signifi cantly thicker wall
Figure-1: Schematics of bottomhole assembly [These bottomhole assemblies are designed for drilling a straight hole (left ) and a directional hole (right)].
than a drill pipe. Since the drill collars have such a large wall thickness, tool joints are not necessary and the connection threads can be machined directly onto the body of the collar. Drill collars add weight to the bit and make the bit cutters bite into the rock. Normally multiple drill collars are used to add weight. The purposes of drill collars are i) to put extra weight on bit, so they are usually larger in diameter than drill pipe and have thicker walls, ii) to keep the drill string in tension, thereby reducing bending stresses and failures due to fatigue, iii) to provide stiff ness in the BHA for directional control, iv) to stabilize the bit. The weakest point in the drill collar is the joint, therefore the correct make up torque must be applied to prevent failure. The external surface of a regular collar is round (slick), although other profiles are available. The drill collars are normally supplied in ranges two lengths (30–32 ft .). Drill pipe and drill collar come in sections, or joints, about 30 feet long. There are several types of drill collars that are explained below.
Square Drill Collars: Square drill collars provide the ability to maximize the available weight on the bit when drilling in challenging formations (Figure-3). The square design has a larger cross sectional area than round drill collars, which increases its stiff ness and rigidity to prevent deviation while drilling. The square shape also provides four point stabilization to prevent buckling. Square geometry makes for a stable and stiff BHA ideal for drilling in hard formations requiring all available weight on the bit. The square drill collar achieves four objectives – i) it provides continuous centralization over their length, ii) it maximizes bending resistance (stiff ness), iii) it maximizes torsional damping, and iv) it minimizes axial vibrations. These collars are usually 1/16 less than bit size, and are run to provide maximum stabilization of the BHA.
Spiral Drill Collars: Spiral drill collars decrease the risk of diff erential pressure sticking of the BHA (Figure-3). The spiral drill collars usually have slip and elevator recesses. Stress-relief groove pins and bore back boxes are optional. In directional drilling, spiral drill collars are preferable. The spiral grooves machined in the collar reduce the wall contact area by 40% for a reduction in weight of only 4%, thus reducing the chances of differential sticking. This is likely to happen when the formation is highly porous, a large overbalance of mud pressure is being used and the well is highly deviated. The problem can be overcome by reducing the contact area of the collar against the wellbore.
Grandma Anal Tube
Female Gagged
Home Hard Porn Video