Bottom Hole
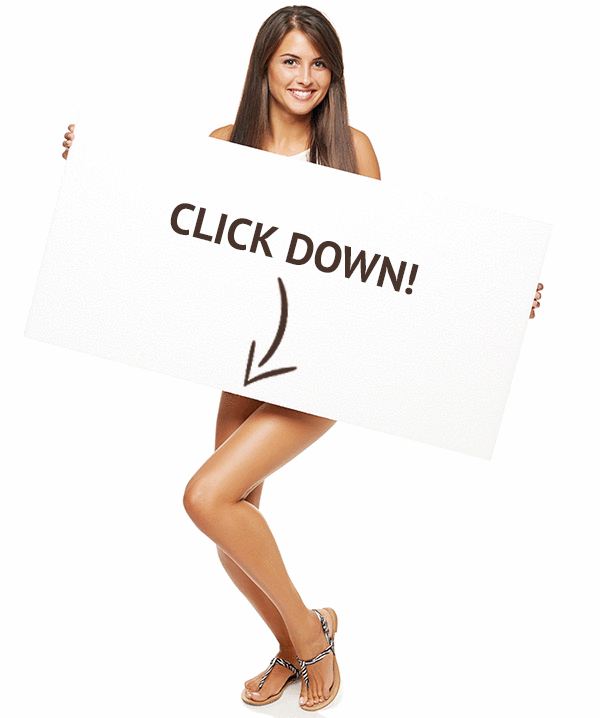
⚡ ALL INFORMATION CLICK HERE 👈🏻👈🏻👈🏻
Bottom Hole
From Wikipedia, the free encyclopedia
^ William C. Lyons, ed. (1996). Standard Handbook of Petroleum and Natural Gas Engineers . Houston Texas: Gulf Publishing Company.
^ Michael L. Payne; Lance D. Underwood. Michael J. Economides; Larry T. Watters; ShariDunn-Norman (eds.). Halliburton: Petroleum Well Construction . John Wiley and Sons.
^ Tom H. Hill; Randy C. Money. (1992). Drill Stem Design and Inspection . Houston Texas: T.H. Hill and Associates Inc.
A bottom hole assembly (BHA) is a component of a drilling rig . It is the lowest part of the drill string , extending from the bit to the drill pipe . The assembly can consist of drill collars, subs such as stabilisers, reamers, shocks, hole-openers, and the bit sub and bit. [1]
The BHA design is based upon the requirements of having enough weight transfer to the bit (WOB) to be able to drill and achieve a sufficient Rate of Penetration (ROP), giving the Driller or Directional Driller directional control to drill as per the planned trajectory and to also include whatever Logging While Drilling (LWD) / Measurement While Drilling (MWD) tools for formation evaluation. As such BHA design can vary greatly from simple vertical wells with little or no LWD requirements to complex directional wells which must run multi-combo LWD suites.
Prior to running a BHA most oilfield service providers have software to model the BHA behaviour such as the maximum WOB achievable, the directional tendencies & capabilities and even the natural harmonics of the assembly as to avoid vibration brought about by exciting natural frequencies.
Rotary assemblies [2] are commonly used where formations are predictable and the rig economics are an issue. In such an assembly the weight of the drill collars gives the BHA the tendency to sag or flex to the low side of the hole, collar stiffness length and stabiliser diameter and placement are engineered as a means of controlling the flex of the BHA. This will bring about the desired hold, build or drop tendency.
The ability to vary the directional tendency of the assembly comes from varying the weight on the bit. A fixed assembly has only one directional tendency. The weight on bit allows you to tune that tendency.
The bottom-hole assembly (BHA) can be:
Bottom-hole assemblies are also described as
This assembly is used to build angle. The assembly usually incorporates a near bit stabiliser. Behind this would be a selection of drill collars and Heavy Weight Drill Pipe (HWDP). The length of the section AFTER the near bit stabilizer would determine the extent of the angle build rate.
After the appropriate length of pipe after the near bit stabiliser you would place a drill string stabiliser.
In short the longer the gap between the near bit and the drill string stabiliser the greater the angle building rate. Care must be taken to not have this section too long as the pipe may sag too much and rub against the borehole wall. This could result in key seating and pipe digging into the borehole wall.
This assembly is usually used to maintain borehole angle. This assembly is very rigid allowing little movement of the bit.
Such an assembly would mean that the stabilisers are closely packed: a near bit stabiliser within 0–30 feet of the drill bit, and two more spaced 30 and 60 feet beyond it. If a short drill collar is used, then the stabilisers can be even closer together.
The shorter the distance between the stabilisers means that the drill collars bend less and the weight on bit (WOB) pushes directly on the bit, hence maintaining the angle.
A pendulum assembly is used to reduce the angle build rate or reduce well-bore angle.
In this assembly there is no near bit assembly. The front portion of the (BHA) is allowed to hang as a result of its own weight. In such a case the first stabiliser is placed 30–45 feet behind the bit.
This hanging means that there is a force acting on the low side of the hole, which causes the deviation. In the case of a straight hole then the bit simply continues downward.
There are three types of BHA configurations. [3] These configurations addressed are usually concerned with the use or layout of drill collars, heavy weight drill pipe and standard drill pipe.
Type 1, standard simple configuration, uses only drill pipe and drill collars. In this instance the drill collars provide the necessary weight on the bit.
Type 2 uses heavy weight drill pipe as a transition between the drill collars and the drill pipe. Weight on bit is achieved by the drill collars.
Type 3 uses the drill collars to achieve directional control. The heavy weight drill pipe applies the weight on the bit. Such a layout promotes faster rig floor BHA handling. It may also reduce the tendency for differential sticking.
In most cases the above three types of configurations usually apply to straight/vertical wellbores at most low to medium angle wellbores. For high angle and horizontal wellbore careful weight control of the BHA is a must. In this instance the weight may be applied by running the drill pipe in compression in the high angle section. The high angle may help to stabilise the drill pipe allowing it to carry some compression.
A stabiliser is used within a column of drill collars. They help guide the bit in the hole. They play a major part in directional drilling as it helps determine the well-bore path and angle.
Solid stabilisers have no moving or replaceable parts. The blades and the mandrel can be one piece (integral) or welded to the mandrel (weld-on/welded blade). The blades may be either straight or spiral. The working surface can be impregnated with tungsten carbide or diamonds inserts.
Replaceable blade stabilisers can maintain full gauge stabilization, but their blades can be changed with tools no machining or welding required
Sleeve type stabilisers have replaceable sleeves that can be changed in the field. The sleeves are either rotating or non-rotating.
Reamers are stabilisers that have cutting elements embedded on their fins, and are used to maintain a gauged well-bore. They can be used to drill out doglegs and key-seats in hard formations. Due to the cutting ability of the reamer the bit does less work in maintaining well-bore gauge and more work drilling.
An underreamer is used to enlarge the well-bore, usually beginning at some point under the surface. It does this by utilizing expandable cutters that only deploy at the designated time or depth. It is not to be confused with hole opening which occurs from the surface and in most cases the hole opener tool is of a fixed diameter.
The underreamer utilises an increase in mud pressure or flow rate to deploy the expandable cutters. A corresponding pressure drop across the tool would indicate that the tool has fully deployed.
Select Language
English
Deutsch
Chinese
Français
Dutch
Italiano
Japanese
Korean
Portuguese
Español
Taiwan
About
About PH Tool
Capabilities / Services Offered
The PH Tool Difference (Video)
RUSH Service
Giving Back
Quality
Calibration Test Blocks
Reference Standards
Reference Standards for NDT
EDM Notches
ERVW® AOD Piping Calibration Blocks with Side-Drilled Holes
U.S. Navy Standards
Ultrasonic Test Standards for Pressurized Gas Cylinders
Flat Bottom & Other Holes
Flat-bottom Holes (FBH)
Round-bottom Holes (RBH)
All Hole Types
Ultrasonic Plotting ASTM E127 FBH Block Sets
NDT Standards for Bar & Tube Inspection Systems and Metals Manufacturers
Additional Products
Precision Mechanical Gauges
Custom Tech Scales
Resources
Helpful Links
Blog
Privacy Policy
Downloads
Video Gallery
Contact
Contact Us
Request a Catalog
Newsletter Signup
Careers
Upcoming Events
PH Tool™ Holiday Hours
Hotel Accommodations
6021 Easton Road
Pipersville, PA 18947
267-203-1600
PH Tool™ offers many different types of machined holes used in NDT today. The most common types are listed below. If you don't find what you're looking for, call us and we'll be happy to discuss how it can be done. We employ both conventional machining (drilling) and non-conventional (EDM) in the hole-making process. The determining factors we consider in choosing a method are machinability of the workpiece, accessibility, hole diameter and depth.
The Flat-bottom Hole (FBH) is machined to have a flat reflecting surface at the hole bottom. The hole bottom is typically parallel to the beam entry surface, but can be machined at other desired angles. Primarily used in Ultrasonic Testing (UT,) with some application in Eddy Current Testing (ET,) In UT applications, FBHs are typically used for straight beam inspections, but they are occasionally used for angle beam inspection as well. FBHs can be machined just about anywhere they are needed for a particular inspection. Available in diameters from .004".
The majority of FBHs made for NDT processes are made by conventional drilling methods using modern CNC machining centers. The tiniest FBHs (under .010" diameter) are made via specialized EDM techniques. To ensure the best testing results, it is critical to machine a hole that is perpendicular to the eventual inspection surface. Learn more about FBHs on our dedicated FBH Page.
The Side-drilled Hole (SDH) is typically a drilled hole, the side wall of which is used as the reflecting surface. Like FBHs, the smallest SDHs (under .010" diameter) are machined via specialized EDM hole drilling techniques. Unlike the FBH, however, the bottom of a SDH serves no purpose, and is therefore most often left conical at the bottom (a vestige of the standard, pointed drill bit used in the drilling process.) The bottom of an EDM'd SDH is typically radiussed (hemispherical) as a result of the EDM process. SDHs are extremely useful for angle beam ultrasonic inspection due to the fact that they are "omnidirectional" reflectors - i.e. they can be used to calibrate at any angle, simplifying TCG calibrations.
SDHs are often machined into calibration blocks at specified locations from the diameter, e.g.: 1/4T, 1/2T, and 3/4T for setting up a distance amplitude correction (DAC) curve or time-corrected gain (TCG.) For piping applications, they can be drilled either longitudinally or tangentially to the axis of a pipe. SDHs can be machined in plate, bar or other products as well. Primary use is Ultrasonic Testing (UT,) with applications for straight beam and angle beam inspection. Multiple holes can be stacked vertically, arranged in a particular pattern, or staggered incrementally based on application. Available in diameters from .003".
The Micro-hole is a small-diameter hole used primarily in Liquid Penetrant Testing (PT) applications, where they are also referred to as, "non-linear indications." The hole diameter is normally .004 to .005", and hole depth is .008 to .010". Micro-holes of this size meet the requirements of the U.S. Navy's NSTR-99 Rev. 2 (Qualification Examination Requirements for Nondestructive Test Personnel). Other diameters and depths are available upon request.
Micro-holes can be machined in welded plate, pipe, bolts, bevel canopies, c-canopies, socket welds, lifting hooks, or any specialized test prop. They are machined via EDM techniques, and are therefore most often rounded (hemispherical) at the bottom as a result of the EDM process. Often times, the layout of Micro-holes is randomized at either our, or the customer's, discretion, and the finished test prop is provided with a map of defect locations as a part of the final certification package. Visual detectability of indications prior to performing the test is often not desired in PT props. For this purpose, Micro-holes can be hidden in weld features or rough surface textures, where they will not become visible until after penetrant and developer are applied. Micro-holes are the primary indication type in PH Tool's popular 3-Weld Liquid Penetrant Test Prop Plate. Click here for more information on this standard product offering.
The Round-bottom hole (RBH) is machined with a hemispherical shape at the hole bottom. Applications include ID pitting of tube or pipe for Eddy Current Inspection, and Liquid Penetrant test props. Larger RBHs are occasionally used in UT applications to evaluate beam spread. Available in diameters from 0.003". Holes over .010" are conventionally machined with round-nose drill bits or ball mills. Smaller holes are machined via EDM. Any hole machined on the inside of a tube is machined via EDM.
More of an art-form than a machining process! These holes and pits are machined in irregular configurations, not described above. Includes star-shaped, square holes, hex holes, and realistic pits. Custom EDM electrodes are designed and made at the hands of a skilled toolmaker. Electrode tooling can also be cast from real pits and used to reproduce actual pits very accurately. Irregular Pits are typically used in detailed corrosion mapping applications, where close simulation to real-world conditions is required. If you still haven't seen the hole you need, use your imagination... we'll figure out how to accomplish it.
This shows a cast replica of pits at 48X magnification.
Yes, we can do that too! Used on curved pipe calibration blocks for special applications. Not required by ASME Code, but available for customers who need a cylindrical reflector (hole) at a constant depth from the scanning surface. Extremely high cost and manufacturing time compared to "tangential holes" detailed in ASME Code. Tangential holes only fall at the correct depth from the scanning surface at a single point. This "tangency point" is typically located at 1/2 the length of the hole. The Curved Hole may simplify inspection by giving a consistent reflection at all points,
If you have further questions related to reference standards with specialized machined holes, please reach out to us .
This shows a cast replica of pits at 192X magnification.
Copyright © 2022 phtool.com
Website Design by IQnection - A Digital Marketing Agency
This site uses cookies. You can read how we use them in our privacy policy .
Woah Brian’s ‘ Bottom Hole ’ is looking ice cold this Tuesday morning
Home
Oilfield Companies
Job Description
Privacy Policy
About Us
Contact Us
Sitemap
Facebook
Youtube
Twitter
Linkedin
Telegram
Pinterest
Home » Drill String » Types Of Bottom Hole Assembly BHA Used In Oilfield
In this article we will talk mainly about the application for different types of bottom hole assembly (slick bha drilling, Pendulum Assembly & Packed BHA) its design & components. This article is a part of the our drill string design guide .
In general there are three types of Bottom Hole Assembly BHA In drilling:
This type of bottom hole assembly (slick BHA) consists of a Drill Bit and Drill Collar without Stabilizer . Slick BHA is suitable for formations which have mild crooked hole tendencies. Slick bottom hole assemblies are seldom. As there are no expensive components on this type of BHA, It is more easier to fish such BHA.
Sometimes when you want to wash and ream (clean out) in some difficult holes. We choose to pull out of the current directional BHA and to try to design a slick BHA but with the same configuration of the directional BHA. In other words it will be a slick BHA, as you won’t add any BHA component but you will have to use stabilizers with the same OD and the same position of any part of directional BHA previously drilled this hole so that to keep the geometry of cleaning assembly (which will be slick BHA with some stabilizers as same as the geometry of the directional bottom hole assembly).
The Pendulum BHA Assembly is one of the types of bottom hole assembly which we can use primarily to reduce or maintain hole deviation. The pendulum technique relies on the force of gravity to deflect the hole to vertical. The force of gravity, F sin I in the above figure, is related to the length of Drill Collars between the Drilling Bit and the point of tangency. The along-hole component of the force F is F cos I, which attempts to maintain the present hole direction.
The pendulum type of bottom hole assembly BHA consists of a Drilling Bit, several Drill Collars to provide the pendulum force and one or more Stabilizers. Lubinski presented charts for determining the location of the first Stabilizer from the Drilling Bit and the weight that can be applied on the Drilling Bit to maintain best position of the Stabilizer is as high as possible provided the Drill Collars below Stabilizer do not contact or barely contact the wall of the hole .
The optimum position of the Stabilizer depends upon the size of the Drill Collars, size of hole, hole inclination and Weight On Bit (WOB). So if we can maintain the weight On Bit (WOB) from the graphs constant, the hole deviation will not change. If the Weight On Bit (WOB) increased, the hole angle will increase and the opposite is true.
Relies on the principle that two points will contact and follow a sharp curve, while three points will follow a straight line as shown . We can obtain three-point stabilization by placing three or more Stabilizers in the portion of the hole immediately above the bit.
We are using this bottom hole assembly type for formations which have mild crooked hole tendency that produce little or no deviation such as hard and isotropic rocks. The three-point stabilization is provided at Zone-1, immediately above the Drilling Bit, at Zone 2, immediately above a short, large OD drill Drill Collar; and at Zone 3, on top of a standard length drill Drill Collar.
We always utilize this type of Bottom Hole Assembly BHA for formations which have medium crooked hole tendency such as medium and soft formations. In this type of Bottom Hole Assembly BHA, we place a second Stabilizer at Zone-1 in order to provide increased Drilling Bit stabilization against deviation effects of the formation.
Drilling engineers utilize this type of Bottom Hole Assembly BHA in drilling formations which have severe crooked hole tendency such as medium and soft formations which show a great degree of dipping , fracturing and variation in strength. In this type of Bottom Hole Assembly BHA three Stabili
Gilf Nude
Handjob Two Dicks
Hi Heels Porn