Black Hole Defect Defect
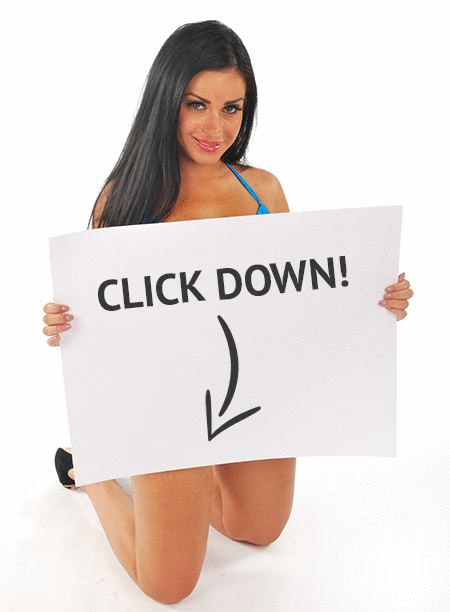
🔞 ALL INFORMATION CLICK HERE 👈🏻👈🏻👈🏻
Black Hole Defect Defect
Product inspection
Pre-shipment Inspection
During Production Inspection
Pre-production Inspection
Container Loading Supervision
Supplier audit
Supplier Qualification Audit
Extensive Factory Audit
Social Audit
Environmental Audit
Lab testing
Consumer product lab testing
Recycled Polyester Testing
Our Partners
US Safety Compliance Testing
EU Safety Compliance Testing
Value Added
FBA Inspection
Technical Compliance File
Defect Sorting
Production Monitoring
Softlines
Textiles & garments
Bags & accessories
Footwear
Fabrics
Other softlines
Hardlines
Furniture
Homeware/ Kitchenware
Building Materials
Automotive Parts
Other Hardlines
Electronics
Household Appliances
Consumer Electronics
Lighting
Other Electronics
Toys
Children/Baby Toys
Pet Toys
Blog
Market Insight
Sample report
Glossary
AQL
Company
Accreditations
Jobs & Careers
Coverage area
Trade show & Event
Home
Manufacturing and QC blog
3 Types of Quality Defects for Defect Classification
Defect classification is a vital step for determining if goods should pass or fail inspection. Check out these 3 types of quality defects for your different product types.
Why is it important to clearly define and classify quality defects for your products?
Imagine you’re manufacturing women’s blouses in Indonesia. A product inspection report from your QC partner shows about one third of the blouses have untrimmed threads.
Would you classify this quality defect as “minor” or “major”? You might say untrimmed threads are a “minor” defect that don’t affect the salability of the product. Or you might consider them a “major” defect if you distribute your product to a high-end retailer with a lower tolerance for quality issues.
Defect classification is a vital step for determining if goods should pass or fail inspection. And considering the quantity and severity of different types of defects found helps you make an informed shipping decision.
A professional inspection company often has established standards for classifying various types of defects for a particular product type. But it’s ultimately your responsibility as the buyer to decide your tolerance for different defects, often using a system like AQL ( related : The Importer's Guide to Managing Product Quality with AQL [eBook] ).
Here we’ll help you get started by explaining the most common ways to classify defects in different products.
Quality control professionals typically classify quality defects into three main categories: minor , major and critical. The nature and severity of a defect determines in which of the three categories it belongs.
Importers have the power to specify how many of each type of defect they’re willing to accept in their finished goods. This tolerance, in turn, impacts how many units per SKU an inspector would check during inspection—the sample size.
Importers commonly set these quality tolerances using a statistically valid acceptance sampling method known as acceptable quality limits, or acceptable quality levels (AQL) ( related : 10 AQL Terms Importers Should Know to Succeed with AQL for Inspection ).
An importer’s tolerance for minor defects tends to be greater than that for major or critical defects, given their relative severity. Let’s look at each of these defect types in detail.
Minor defects are usually small, insignificant issues that don’t affect the function or form of the item . In most cases, the customer wouldn’t even notice a minor defect on a product. And the customer wouldn’t likely return an item due to a minor defect alone.
Importers often set the highest tolerance—or AQL, if applying that standard—for minor defects in their inspected sample size. But an item can still fail inspection if the number of minor defects found exceeds the limit set by their tolerance ( related : How AQL Sampling Affects Your Inspection Results ).
Major defects are more serious than minor defects. A product with a major defect departs significantly from the buyer’s product specifications. Major defects are those which could adversely affect the function, performance or appearance of a product.
These defects are readily noticeable by the customer. And these defects would likely cause a customer to return the product, lodge a complaint or request a refund in response.
Most importers set a lower limit for major defects than minor defects in their inspected sample size. They’ll often accept an order with relatively few major defects. But they’re likely to reject an order, or ask their supplier to hold or rework it, if the goods fail inspection due to an excessive number of major defects found.
Critical defects are the most serious of the three defect types. Critical defects render an item completely unusable and/or could cause harm to the user or someone in the vicinity of the product.
These defects put businesses at serious risk of product liability issues, lawsuits and product recalls.
Many importers have a “zero tolerance” policy for critical defects in their orders commensurate with this risk. An item will often fail product inspection if a single critical defect is found within the order.
Different quality defects can appear in different products depending on materials, production processes and standards used. Below are some common examples of minor, major and critical defects in different product types.
Softline products include raw fabric, home textiles, garments and other woven or knitted products and footwear. Garments, in particular, tend to be more vulnerable to quality defects because of the labor-intensive production processes involved in their manufacturing.
Human hands involved in sewing and stitching, for example, raise variability in production. Whereas more automated production processes, like the use of injection molding in hardlines goods or robotics in electronic assembly, tend to lower variability. This typically results in more consistent product quality throughout a production run.
Some common softline defects include:
Hardline products include a broad range of goods typically made of metal, wood or plastic materials. This category includes most furniture, sporting equipment, cookware, building materials and tools.
Some common hardline defects include:
Electrical and electronic (E&E) products include consumer electronics, many household appliances, certain toys, power tools and other products that require electricity to function.
Some common defects in electronics include:
Industrial components is a broad term that can include fabricated steel, conduit piping, gas valves, wind turbines, maritime equipment and other machinery or materials designed for industrial use.
Some common defects in industrial products include:
A QC professional can often suggest appropriate tolerances for known defects for your product. But it’s ultimately up to you as the buyer to specify your tolerance for each kind of quality defect.
Importers often list their defect classifications and tolerances in a document known as a quality control, or QC, checklist ( related : 5 Essentials of a QC Checklist [eBook] ). A QC checklist also typically includes other information like packaging requirements, on-site testing procedures and required inspection equipment.
This document should include an exhaustive list of common and known quality defects with your product type.
Accounting for every single quality defect may not be possible. But the more complete the list of potential defects you provide, the more likely your supplier will be to heed your tolerances. Your QC inspector is also far more likely to apply the same standard when checking your products against a complete QC checklist.
A defect classification list might look something like the below example for footwear:
This defect classification information can help:
This defect classification list might extend to include 20 or even 30 different types of defects depending on your product type. The more information you can provide, the better prepared your QC team and supplier will be.
Identifying quality defects in your order before shipment is essential to ensuring your goods meet your customers’ expectations.
Third-party inspection companies can inspect your order and report to you the number and types of defects found in the inspected sample size. Their report will typically show you the total number of defects found in comparison to the number of defects allowed based on your tolerances.
The order will fail inspection if the number of defects found exceeds the allowed number. As you can see in the below excerpt, this order would fail inspection due to the number of minor defects exceeding the allowed number:
While this order would fail inspection based on AQL standards, it’s up to you as the importer to decide whether to ship the order ( related : What Inspection Results Do and Don’t Mean for Your Shipment ).
You might want to address any quality defects before approving a shipment. To address product defects found in your order during inspection, you might:
And remember to continually update your defect classifications to add new quality defects or adjust your tolerances for new orders. Updating your QC checklist can help prevent the recurrence of known quality defects in your received shipments.
These are rough guidelines QC professionals typically follow for defect classification ( related : Why QC Professionals Use AQL Sampling for Product Inspection ) . But as the buyer, always consider the severity of different defect types and their effect on your customers and brand when setting tolerances.
Tell your inspector if they’ve classified a defect in a different category than you consider appropriate. This feedback allows them to adjust reporting for future inspections. Likewise, if an inspector finds “defects” you do not consider to be defects at all, inform the inspector to disregard those in future reporting.
These changes help ensure you receive the most accurate reporting possible so you can take appropriate action to address issues before they affect your customers.
If you'd prefer to listen to this topic instead, check out this manufacturing podcast !
Editor’s note: This post was originally published in November 2015 and has been updated for freshness, accuracy and comprehensiveness.
Journals
Books
Databases
From the journal:
Nanoscale
Julian
Gaberle
a
and
Alexander L.
Shluger
* a
This article is part of the themed collection:
Recent Open Access Articles
Fig. 1
Top left: Black phosphorus monolayer and unit cell structure illustrating the lattice directions. Top right: Position of the band edges with respect to the work-function of common metals (* stainless steel). Bottom left: Total DOS of monolayer BP (grey) and projections on s-orbitals (red), p-orbitals (blue) and d-orbitals (green). Bottom right: Total DOS of multilayer BP (grey) and projections on s-orbitals (red), p-orbitals (blue) and d-orbitals (green).
Fig. 2
Defect structures in monolayer BP with their respective formation energies given above: (a) Neutral (5 | 9) phosphorus MV. (b) Negatively charged (55 | 66) MV. The central P atom is four coordinated in a sp 3 d 2 hybridisation state. (c + d) Stone–Wales defects.
Fig. 3
Schematic illustrating the defect induced Kohn–Sham states in the bandgap of BP. Filled circles indicate a filled state and empty circles an empty state, while a circle on the right/left indicates the spin up/down channel. All energies are referenced to the vacuum level (0 eV). The states for adsorbed O atom are deep in the valence band and are not shown.
Fig. 4
(a–h) The eight lowest energy DV structures in monolayer BP; their respective formation energies are shown in Table 1 . The rings are labelled according to how many atoms make up the ring structures and are coloured as a visual aide.
Fig. 5
Diffusion barrier for a neutral MV along the zz direction in monolayer BP. The inset shows the transition point geometry. On the right, the geometry of the vacancy at each minima in the diffusion path is illustrated. Note the asterisk signifies a commensurate structure translated by half a unit vector and two asterisks denote a commensurate structure after translation by a whole unit vector. Red lines represent the upper and blue lines the lower zigzag. The 5 and 9 member rings are coloured in pink and cyan as a visual aid.
Fig. 6
Summary of impurity defects in BP (P is grey). Geometries are shown for Fe (magenta), Ni (yellow), Cu (orange), Zn (cyan), Sn (green), I (brown) and O (red) in adsorbed (top), substitutional (middle) and intercalated (bottom) configurations.
F. Wang
, W. K. H. Ng
, J. C. Yu
, H. Zhu
, C. Li
, L. Zhang
, Z. Liu
and Q. Li
, Appl. Catal., B ,
2012, 111–112
, 409 —414
CrossRef
CAS
.
Z. Shen
, Z. Hu
, W. Wang
, S.-F. Lee
, D. K. L. Chan
, Y. Li
, T. Gu
and J. C. Yu
, Nanoscale ,
2014, 6
, 14163 —14167
RSC
.
H. Wang
, X. Yang
, W. Shao
, S. Chen
, J. Xie
, X. Zhang
, J. Wang
and Y. Xie
, J. Am. Chem. Soc. ,
2015, 137
, 11376 —11382
CrossRef
CAS
PubMed
.
L. Li
, Y. Yu
, G. J.
Fucking Older Grandma
Curly Haired Girl Porn
Busty Milf Handjob And Pussy Rubbing