Aperture Science Mfc
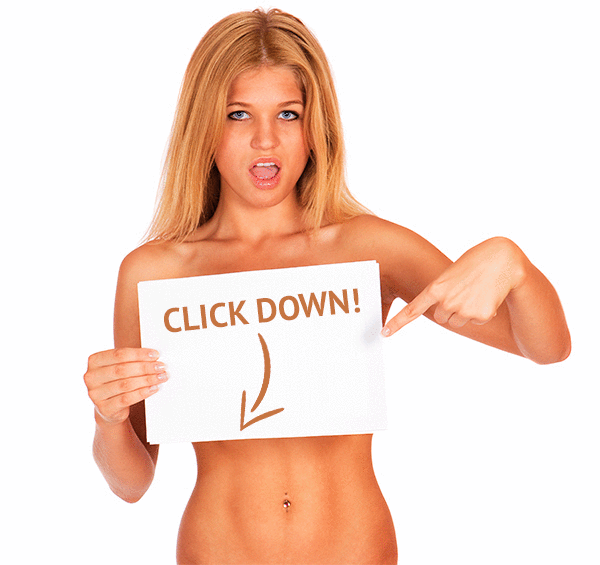
🛑 ALL INFORMATION CLICK HERE 👈🏻👈🏻👈🏻
Aperture Science Mfc
URL: https://www.sciencedirect.com/science/article/pii/B9780080445021500019
URL: https://www.sciencedirect.com/science/article/pii/B9780080967011000690
URL: https://www.sciencedirect.com/science/article/pii/B9781845691752500088
URL: https://www.sciencedirect.com/science/article/pii/B9780128119785000031
URL: https://www.sciencedirect.com/science/article/pii/B9780128126325000057
URL: https://www.sciencedirect.com/science/article/pii/B9780815511717500135
URL: https://www.sciencedirect.com/science/article/pii/B9780128126325000069
URL: https://www.sciencedirect.com/science/article/pii/B9780128142387000039
image scale = 1 EFL = radians on the sky length in the focal plane .
URL: https://www.sciencedirect.com/science/article/pii/B0122274105005342
URL: https://www.sciencedirect.com/science/article/pii/B9780128121368000050
the aperture plate cavities can be formed anywhere along this intersection, and their width can be any fraction of this length of intersection.
J.S. Harris Jr. , ... L. Goddard , in Dilute Nitride Semiconductors , 2005
The most successful method of obtaining reactive atomic N has been the use of a rf plasma source. Dissociated atomic and molecular radicals and ions are generated in the plasma and escape from a front aperture plate towards the substrate, depositing in substantial concentrations. Ions generated in the plasma can be accelerated by the rf fields and cause substantial substrate damage while radical neutrals should inflict little damage and incorporate on substitutional sites. There are many different parameters which control the plasma, including forward rf power, reflected rf power, the N gas flow rate, the number, size and configuration of holes in the front aperture. Unfortunately, there are very few analytical techniques which are available in MBE to measure the plasma properties and determine the ideal operating conditions directly. It is also not completely known which characteristics of the plasma are beneficial to high quality crystal growth and which contribute to detrimental defects. We chose a rf plasma over other options because of its low ion count and high atomic dissociation yield [30] .
During the early history of GaInNAs, rf plasma cells normally used for growing GaN were adapted for use in growth of dilute nitride (a few atomic percent) alloys. Several companies now make rf plasma cells specifically for dilute nitride-arsenide growth including Veeco Applied-Epi [31] , SVT Associates [32] , Oxford Scientific [33] , and Adon. Our group is most familiar with the SVT Associates rf plasma cell because of the circumstances surrounding available equipment during the early stages of GaInNAs growth. The SVT Associates cell was chosen at the time since it was the only model which had a removable pyrolytic boron nitride (PBN) front aperture plate in which the number, size, and orientation of holes could be modified to reduce the N flux as well as control the deposition behavior. This was particularly important initially since dilute nitride-arsenide growth was very new at the time and most N sources were used for high growth rates in GaN. Another advantage of the SVT Associates cell was the fully transparent back viewport which allowed for direct monitoring of the plasma glow.
The operation of the rf plasma was optimized to maximize the generation of atomic N within the limits of stable plasma operation. The plasma conditions that maximize the amount of atomic N versus molecular N are determined using the emission spectrum of the plasma (see Figure 1.2 ). The amount of molecular N is determined from the ratio of the integrated intensity of the first set of bands at approximately 550, 580, and 650 nm to the integrated intensity in the bands at 740, 820, and 870 nm, which is proportional to the amount of atomic N present in the plasma [11] . Hence, the ratio of the integrated peak intensities due to atomic N transitions and the integrated peak intensities due to molecular N transitions is proportional to the relative amount of atomic versus molecular N in the plasma. The total intensity integrated from 550 to 950 nm is proportional to the total amount of excited N in the plasma. The amount of atomic and excited N in the plasma as function of (a) N flow, (b) plasma power, and (c) number and diameter of holes in the plasma source front cover plate.
Figure 1.2 . Measured fluorescence from N plasma source showing transitions for molecular N2 and atomic N. The ratio of the integrated intensity from these lines was used to optimize the plasma source operating conditions to maximize the atomic N ratio.
To optimize the plasma for maximum atomic N, we investigated how the ratio of atomic N versus molecular N varied in the plasma with N flow rate and plasma power. We observed that changes in gas flow and power did not produce linear changes in atomic N and that the plasma changed modes with rather dramatic changes in output. Because the operating points for these mode changes were not particularly consistent and reproducible, we decided to operate the plasma source under constant conditions of power and gas flow where the source was very stable and the ratio of atomic N was near maximum. Not all plasma sources have such a viewport for plasma characterization; however, it also had its drawbacks. Monitoring the optical emission of the plasma in this configuration has limited utility. Only the back periphery of the glow is in reality being measured and this may not be representative of the active species emitted from the front aperture of the source. Also, the plasma is not completely confined by the PBN liner, which may change the rf environment and coupling to the plasma, thus sacrificing stable operation and reducing containment of N gas in the MBE chamber.
Plasma stability during low N flow growth is one of the biggest problems for growth of dilute nitrides and is probably the greatest cause of differences not only between wafers grown in the same system, but particularly in comparisons between different groups who think they are growing under nominally identical conditions. Some of this is the result of short-term plasma instabilities in the source, others due to long-term changes in the source. A second issue is ion or electron damage to the epitaxial films from the plasma source, which is quite dependent upon the current operating region of the source. It is also dependent upon the use of charged particle deflecting plates at the source exit. Our experience with the stability issues of plasma sources is described in the remainder of this section and ion damage in the following section.
One of the major stability issues emanates from the fact that these sources were all originally designed for high growth rate GaN deposition. Source instability came in many different forms, including: difficulty maintaining a stable flow of injected gas at low flow rates, difficulty in igniting and maintaining a consistent plasma and its degradation over time, and difficulty in reproducibility due to thermal and power instability.
The flow stability problem was one largely of system design due to rf coupling from the plasma power supply, matching network and source into the mass flow controller (MFC) which controls the flow of N gas. Improved rf shielding of the matching network and components, including the MFC, then enabled reliable control of very low and stable flow rates (as low as 0.1 seem).
The problem of igniting and maintaining the plasma is a degradation problem which gets worse with time. This manifests itself in requiring an increase in the flow rate necessary to ignite the plasma after several months of operation and in worst cases, the plasma would extinguish intermittently during growth. First, it appears that there is decomposition of the PBN crucible during operation, creating boron dust as well as plasma etching of the holes in the front aperture plate. The only solution to this problem is to replace the crucible when servicing the MBE system and to minimize the duration of plasma operation. Also, As contamination can be a problem in the crucible. During growth when the plasma cell is off, the cell is not heated and As can condense in or on the cell. This can either contaminate the inside of the cell which interferes with the plasma characteristics or coats the outside of the crucible which acts as an electromagnetic shield and reduces rf coupling into the plasma. In order to minimize this problem, a gate valve can be installed to isolate the cell from the rest of the chamber when N is not needed.
Another stability problem is the time required for temperature and power to stabilize in the cell. This is a particular problem when growing laser structures as there is more N leakage or “blow by” around the shutter than for normal evaporative sources. This results in relatively heavy N “doping” when the source is operating, but with the shutter closed. We typically see mid-1019 cm −3 levels of N in such films. This is a serious problem when growing AlGaAs as even minute quantities of N dramatically increase the trap density and non-radiative recombination rate. Our current solution to this problem is to run the cell for a period of time before the wafer is loaded and growth is started. This allows the cell to thermally stabilize before a growth starts. The source is then extinguished, but kept with below ignition rf power on to maintain the temperature while other non-N containing layers are grown and then ignited shortly before N containing alloys are grown. However, this is not always a viable solution and the blow by around the shutter is far worse when the plasma is ignited. These problems can be greatly reduced by using better shutter designs or completely eliminated by placing the source behind a differentially-pumped gate valve.
A linear analogue to the rotating-sector method was recently designed by O’Driscoll and Mahabadi. 84 A solution of monomer and photoinitiator flows through a dark tubular reactor which is covered with an aperture plate with regularly spaced slots through which UV radiation shines. The alternating dark and light regions produce a spatially intermittent polymerization system (SIP).
With the rotating-sector method, only small amounts of polymer can normally be obtained for further investigations ( e.g. determination of MWD) and the produced material shows the cumulative properties corresponding to the conversion at the end of the experiment, typically about 5%. Owing to its continuous mode of operation, the SIP reactor, on the other hand, may produce large quantities of polymeric material at a fixed conversion level, which might be as low as 0.1%. In this way, it is even possible to study the conversion dependence of τ.
In addition, with the SIP reactor, both k p 2 / k t and k p / k t can be measured under identical conditions and with comparable precision. Thus k p and k t data obtained with this method are claimed to be highly reliable.
Primary jig feed normally comprises deslimed minus 10 mm screen undersize fraction, although the sizings may be coarser than 25 mm in exceptional circumstances (e.g., if the gold is very nuggetty). Secondary and tertiary jig feeds are classified according to the size of the screen plate apertures. Pulp density may range from about 10–30% solids by weight, but is optimal around 25%. Jigs operate most efficiently when deslimed feed is introduced evenly and at a controlled pulp density across the full width of the live section. The hutch water should not contain more than 1.4% solids. Too little water results in uneven solids distribution and a tendency for the development of ‘dead’ spots in the jig bed. Slime affects slurry rheology through changes in apparent viscosity and density and is detrimental to the recovery of fines. Allowable slime tolerances are probably much lower than 5%.
Transfer molding requires four key pieces of capital equipment: a preheater, a press, the die mold, and a cure oven. The transfer molding press is normally hydraulically operated. Auxiliary ram-type transfer molds are commonly used in transfer molding.
The mold has a built-in transfer pot separate from the mold cavities as shown in Fig. 3.3 . The molding compound is placed in the pot. Both the volume and the size of the molding compound preforms have to be appropriately selected for the press capacity. The mold is then clamped. The transfer plunger is activated to apply the transfer pressure to the molding compound. The molding compound is driven through the runners and gates into the cavities. Fig. 3.3 A shows the top view of a transfer molding setup design with multiple transfer pots and plunger where each transfer pot is connected to only two cavities. Fig. 3.3 B shows a single transfer pot and plunger connected to multiple cavities.
Fig. 3.3 . Top view of transfer molding designs with (A) multiple transfer pots and (B) single transfer pot with multiple cavities [1] .
Since the 1980s, aperture-plate and multiplunger molds have been the dominant approaches to plastic-encapsulated microelectronics (PEMs) molding. Tables 3.1 and 3.2 compare the features of these methods. Aperture-plate molds are a patented transfer molding technology (US Patent No. 4,332,537, June 1, 1982) exclusively developed for PEMs. An aperture-plate mold design is shown in Fig. 3.4 [1] . An aperture-plate (or cavity plate) mold is constructed by assembling a series of stacked plates. The lead frames form the aperture plates . The top and bottom of the body are formed by separate plates. The bottom body-forming plate contains the runner system, while the top plate is finished for either laser or ink marking. The gates are positioned between the runners, parallel to the bottom of the body; the aperture plate cavities can be formed anywhere along this intersection, and their width can be any fraction of this length of intersection. This flexibility of gate positioning, along with the much lower pressure drop across the gate in an aperture plate, results in negligible wire sweep and paddle shift during molding. These molds are also highly adaptable for different package types and pinouts.
Table 3.1 . Comparison of molding tools
Table 3.2 . Comparison of molding processes
Molding material may be wasted, thus higher material expense
Rapid tool wear (screw and barrel wear)
Few resin systems available for electronic packaging
Suitable for very thin packages, multichip modules, and wafer-level packages
Fig. 3.4 . Aperture-plate (or cavity plate) molding setup [3] .
Multiplunger molds, also called gang-pot molds, have a number of transfer plungers, typically feeding one to four cavities from each transfer pot. They are highly automated and can be easily set and optimized for a new molding compound. However, their productivity is much less than aperture-plate molds due to the number of cavities available (up to 100 in multiplunger vs. 1000 in aperture-plate). Also, the use of low preform-preheat temperatures in manual tools can lead to some molding-compound temperature-related problems. Fig. 3.5 shows a multiplunger mold used for simultaneous encapsulation of dual in-line packages and quad flatpacks (QFPs). Fig. 3.6 shows a multiplunger mold with each pot feeding just one cavity.
Fig. 3.5 . Multiplunger mold used for simultaneous encapsulation of dual in-line packages (DIPs) and quad flatpacks (QFPs).
Fig. 3.6 . Multiplunger mold with each pot feeding just one cavity.
The multiplunger mold consists of two halves, referred to as the top and bottom molds. The mating surface of these two halves is called the “parting line.” Platens are massive blocks of steel used to bolt the two mold halves to the molding press. Fig. 3.7 shows different parts of a transfer mold press including platens and cavities. Fig. 3.8 shows a close-up top view of a transfer pot, runners, and cavities. The mold press also includes guide pins and ejector pins. The guide pins ensure proper alignment and movement of the two halves. The ejector pins aid the ejection of the component after the mold has opened.
Fig. 3.7 . Different parts of a transfer mold.
Fig. 3.8 . A mold used for encapsulation of quad flatpacks.
The gates in the molding equipment are located such that they can be easily removed and polished if necessary. Properly designed gates should allow proper flow of material as it enters the mold cavity. Gates should be located at points away from the functioning parts of the molded component.
Vents are provided in all transfer molds to facilitate the escape of trapped air. The locations of these vents depend on the part design and locations of pins and inserts. Vents should be sufficiently small so that they allow the air but not the molding compound to pass through. Vents are often placed at the far corners of the cavity, near inserts where a knit line will be formed, or at the point where the cavity fills last.
The specific mold design depicted in Fig. 3.8 is used for the encapsulation of quad flat packages (QFPs). In this design, one transfer pot feeds > 10 cavities. The top part of the figure shows the lead frame with the encapsulated packages. The bottom part of the figure shows the cavities. As seen, the material flows through the runners and gates.
Dilip Kumar , Deepak Kumar , in Sustainable Management of Coal Preparation , 2018
In 1892, Fritz Baum of Westphalia in Germany introduced a new type of jig in which compressed air was used to produce the necessary pulsation of water. Like other jigs, several compartments can be put in series with separate controls for each compartment for efficient separation at each stage. The Baum jig is widely used for coal washing. Stratification and separation of the particles take place on the screen plate but some of the finer particles, mainly shale, fall through the screen plate aperture and are conveyed by the worm to the elevator. The clean coal and wash water flow out of the discharge end of the jig. Compressed air supply is controlled by valves. Although slide types of valves were introduced, subsequently rotary valves were fitted for better jigging action. Baum jigs are not usually used for less than 1.5 sp.gr. cut for raw coals having higher near gravity materials.
Refuse extraction can be done both manually and automatically. Manual control has many deficiencies, so automatic control is described here. Among the automatic control systems, there are various designs, but the Acco system is the one discussed here. The basic approach of this system is to maintain a constant thickness of refuse bed. The shale discharge control is actuated by a float which is suspended in a tube in which water moves up and down, shifting the position of the float. If the thickness of the shale bed increases the rising water will get more resistance, then water will find its way into the tube and raise the float, which in turn opens the valve. Then the air chamber creates an air cushion and prevents air pulsation, thus stopping shale discharge. Continuous shale discharge starts after the shale bed returns to its required depth when the valve is closed.
A procedure for the bulge testing of samples of electrolytic foil is described in some detail by Prater 7 , 8 and Read as a result of their pioneering work in this area of technology. This contribution was followed by Lamb and co-workers 9 who determined the mechanical properties, including rupture pressure, of Type E copper as deposited from the commonly available copper plating solutions. More broadly, the Mullen hydraulic bulge test, or some adaptation of it, is widely used 10– 11 for determining the stress-strain properties of sheet metals for the control of forming characteristics.
Rupture testing is uncomplicated, with no special requirement for sample preparation when testing thin sheets or foils. However,
Rule 34 Aninated
Incredible Sexy Legs
Hentai Sword Art Online