Анализ взаимодействия процесса получения полистирола с окружающей природной средой. Курсовая работа (т). Экология.
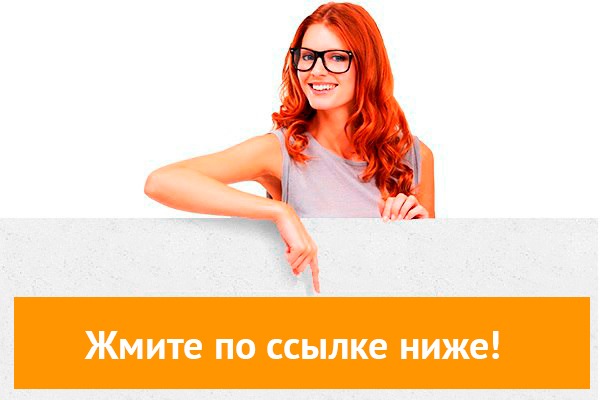
⚡ 👉🏻👉🏻👉🏻 ИНФОРМАЦИЯ ДОСТУПНА ЗДЕСЬ ЖМИТЕ 👈🏻👈🏻👈🏻
Вы можете узнать стоимость помощи в написании студенческой работы.
Помощь в написании работы, которую точно примут!
Похожие работы на - Анализ взаимодействия процесса получения полистирола с окружающей природной средой
Нужна качественная работа без плагиата?
Не нашел материал для своей работы?
Поможем написать качественную работу Без плагиата!
Министерство
образования и науки Российской Федерации
Филиал
федерального государственного бюджетного образовательного учреждения высшего
профессионального образования
«Уфимский
государственный нефтяной технический университет» в г. Салавате
(Филиал
ФГБОУ ВПО УГНТУ в г. Салавате)
Тема: Анализ
взаимодействия процесса получения полистирола с окружающей природной средой
Исполнитель: студент гр. МТП-21 И.В.
Чикиркин
Отходы и побочные продукты, образующиеся и
накапливающиеся на нефтехимических предприятиях являются одними из самых
многочисленных и разнообразных как в количественном, так и в качественном
отношении. Решение проблемы переработки и применения этих отходов неразрывно
связано с промышленной экологией и экологической безопасностью, комплексным
использованием сырья и материалов. Это способствует увеличению
производительности технологических процессов, более полному и экономичному
использованию химического сырья.
Поиск путей рационального использования отходов
затруднен сложностью их состава. Многочисленные отходы нефтехимических
производств содержат в своем составе большое количество разнообразных
реакционноспособных соединений и могут служить ценным исходным сырьем как для
органического синтеза, так и для получения различных полимерных и
композиционных материалов. Однако, при этом необходимо учитывать то, что во
многих случаях методы переработки пригодные для одних промышленных отходов
оказываются совершенно неприемлемыми для других. Разделение такой
углеводородной смеси на индивидуальные компоненты, чаще всего, является очень
сложной и трудоемкой задачей. Поэтому выделять из промышленных отходов
индивидуальные соединения в большинстве случаев оказывается нецелесообразным с
экономической точки зрения. Наиболее перспективным является получение на основе
отходов таких продуктов, которые не требовали бы предварительного разделения
смеси на индивидуальные компоненты.
Структура нефтехимического комплекса от нефти до
получения полистирола.
Стироли и полистирол является одним из ценнейших
мономеров. Непрерывный рост потребности в стироле для производства
полистирольных пластиков, синтетических смол, необходимых для автостроения,
электротехнической промышленности, авиа- и судостроения, в промышленности
синтетических латексов и бутадиен-стирольных каучуков, лакокрасочных
материалов, клеев, пенополистирольных пластиков для строительной индустрии,
АБС-пластиков, ряда термоэластопластов приводит к существенному увеличению
мощности по его производству.
Полимерами называют соединения, макромолекулы
которых состоят из повторяющихся структурных звеньев - мономеров. В состав
высокомолекулярных соединений входят тысячи атомов, соединённых химическими
связями, а молекулярная масса макромолекул может достигать нескольких
миллионов. Полимеры образуются путём многократного последовательного соединения
исходных молекул - мономеров.
В данной работе я рассматриваю производство
полистирола на примере цеху по производству полистирола завода «Мономер» ОАО
«Газпром нефтехим Салават.
Немного истории ОАО «Газпром нефтехим Салават».
Строительство комбината № 18 по производству
искусственного жидкого топлива первоначально планировалось в Хакасии, в г.
Черногорске.
Однако в связи с бурным развитием нефтедобывающей и нефтеперерабатывающей
промышленности между Волгой и Уралом (в городе Ишимбае, прозванном затем
«вторым Баку») правительством страны в 1947 году было принято решение о
перебазировании комбината №18 в Башкирию для гидрирования тяжелых продуктов
нефтепереработки (мазутов) и получения из них бензина и дизельного топлива.
В январе 1948 года Совет Министров СССР своим
распоряжением утвердил площадку строительства предприятия. Вскоре на месте
сегодняшнего Салавата вырос палаточный городок.
В 1954 году был введен в эксплуатацию первый
технологический объект комбината № 18 - катализаторная фабрика. Катализатор
стал первым продуктом предприятия.
В 1955 году начали вводиться в эксплуатацию
установки нефтепереработки, а уже в 1956 году в составе комбината действовал
мощный нефтеперерабатывающий завод. НПЗ стал бурно развиваться, строились новые
установки по переработке нефти, газового конденсата, вторичных процессов
нефтепереработки.
В ноябре 2010 года в ходе встречи
председателя Правления ОАО «Газпром»
<#"878985.files/image002.gif">
Стирол - исходное сырью для производства
полистирола. Это - непредельный углеводород, безцветная житкось с характерным
запахом, температура кипения 145,2 градуса, плотность 906 кг/см2.
Каучук - используется в качестве сырья в
производстве ударопрочного полистирола.
Третбутилпербензоат - используется в качестве
инициатора реакции полимеризации.
Додецилмеркаптан третичный - используется в
качестве регулятора роста цепи реакции полимеризации.
Димер α-метилстирола
- используется в качестве регулятора роста цепи реакции полимеризации.
Масло вазелиновое медицинское - используется в
качестве пластификатора при производствах полистирола общего назначения и
полистирола ударопрочного.
Тринонилфенилфосфи (Irgafos, Doverphos
заменитель)- используется в качестве термостабилизатора при производствах
полистирола общего назначения и полистирола ударопрочного.
Цинка октадеканоаты (Стеарат цинка) -
Используется в качестве внешней смазки полимера.
Ирганокс 1010 (Richnox 1010) - Используется в
качестве термостабилизатора
Двуокись титана - Используется в качестве
наполнителя и красителя.
Принципиальные
схемы производства УПМ
Каучук размельчается на кусачки в дробилке и
далее растворяется в аппарате в который подают стирол, а затем при
перемешивании вводят каучук. Растворение проводят до образования прозрачного
раствора в течении 10 часов при температуре 40 градусов далее загружают
инициаторы, стабилизаторы, регуляторы роста цепи, пластификатор. По окончании
растворения раствор перекачивается в промежуточную ёмкость.
Предварительную полимеризацию проводят в двух
последовательно соединённых реакторах. В форполимеризаторе первой ступени
насосом подаётся раствор с добавками. Полимеризация происходит при Т=105 - 125
градусов в течении 5-6 часов в атмосфере азота до степени конверсии 0,4. Далее
раствор полимера непрерывно подаётся в полимеризатор второй ступени, где
полимеризация продолжается при Т=120-170 градусов в течении 5-6 часов до
степени конверсии 0,8. Формолимеризатор и полимеризатор снабжены рубашками,
мешалками и холодильниками.
Окончательная полимеризация происходит в
аппарате колонного типа с вакуумной-камерой. Полимеризация до степени конверсии
0,9-0,95 завершается при Т=200-230 градусов. В этом же аппарате происходит удаление
непрореагировавшего мономера. Пары стирола с форполимеризатора, полимеризатора
и вакуум-камеры конденсируются и отправляются на блок ректификации для
переработки и возврата стирола в процесс полимеризации.
Расплав полимера поступает в экструдер откуда в
виде прутков выдавливается в охлаждённую ванну. После охлаждения прутки
измельчаются в грануляторе. Гранулы по пневмотранспорту поступают на блок
расфасовки готовой продукции, складирования и отгрузки продукции потребителю
Принципиальные
схемы производства ПСМ
В аппарат подают стирол, добовляют добавки
(какие добавки и колличестово зависит от рецептуры) интенсивно перемешивают при
Т=не более 40 градусов, с частотой вращени мешалки 30-90 об./мин. До полного
растворения добавок в стироле. По окончании растворения раствор перекачивается
в промежуточную ёмкость.Полимеризация в форполимеризаторе протекает при
Т=108-120 градусов до конверсии 32-45%. Съём избыточного тепла происходит
реакции происходит за счёт испарения части стирола из реакционной массы.
Полимеризация в порполимеризаторе протекает при Т=120-170 градусов до конверсии
75-88%. Раствор полистирола в стироле из полимеризатора выгрузным насосом
подаётся в вакуум камеру. Расплав полимера в вакуум камеру поступает с
Т-180-200 градусов. В трубчатке перегревателя вакуум камеры расплав нагревается
до 240 градусов и поступает в полую камеру 10м3 с остаточным давлением 2,0-2,6
кН/м2. При этом происходит испарение стирола из расплава и содержание
остаточного мономера снижается до 0,1-0,3%. Пары стирола поступают на блок
ректификации для переработки и возврата стирола в процесс полимеризации.
Расплав полимера поступает в экструдер откуда в виде прутков выдавливается в
охлаждённую ванну. После охлаждения прутки измельчаются в грануляторе. Гранулы
по пневмотранспорту поступают на блок расфасовки готовой продукции,
складирования и отгрузки продукции потребителю
Классификация основного оборудования по
взрывоопасности
Наименование
оборудования, стадии технологического процесса
Категория
взрывоопасности технологического блока
Относительный
энергетический потенциал технологического блока
Класс
зоны по уровню опасности возможных разрушений, травмирования персонала
Блок
приготовление раствора каучука в стироле и раствора стирола
R 1 =20,1
м R 2 =29,7
м R 3 =50,9
м R 4 =147,5
м R 5 =296,9
м
R 1 =5,65
м R 2 =8,33
м R 3 =14,27
м R 4 =41,63
м R 5 =83,25
м
Блок
полимеризации II
ступени, вакуумирование, экструзия и грануляция
R 1 =9,9
м R 2 =14,5
м R 3 =24,9
м R 4 =72,6
м R 5 =145,2
м
Отходы,
образующиеся при производстве продукции, сточные воды, выбросы в атмосферу,
методы их утилизации, переработки
Условие
(метод) и место захоронения, обезвреживания, утилизации
1.
Масла индустриальные, компрессорные, трансмиссионные
Сбор
в специальные ёмкости, бочки. Вывоз автотранспортом
Вывозится
на площадку “Г” для компаундирова-ния с мазутом или в цех № 13 для
компаундирова-ния с нефтью, или реализуется потребителям
2.
Отходы полимеров после очистки аппара-тов и оборудова-ния:Форполимеризаторов
ФП-52 полимеризаторов поз.П-56/1-3
Сбор
в металлические бочки. Вывоз автотранспортом
Повторно
вовлекается в производство либо реализуется через УМТО
3.
Пыль полимерных материалов с фильтров размалывающих устройств
При
замене фильтрующих элементов в Ф-203, Ф-208/1-4
Повторно
вовлекается в производство либо реализуется через УМТО
4.
Отходы минеральные от газоочистки
Сбор
в металлические контейнеры. Вывоз автотранспортом
Используются
для рекультивации карьера
Токсичные
отходы V класса
опасности
5.
Древесные материалы из чистой древесины
Сбор
на спецплощадке. Вывоз автотранспортом
6.
Полиэтиленовая плёнка упаковочная. Полиэтиленовые мешки, бочки. Бумажные
мешки, упаковочная крафт-бумага
Сбор
на спецплощадке. Вывоз автотранспортом
Используются
для рекультивации карьера
7.
Отходы твёрдого полистирола, полистирольной пены или плёнки
Повторно
вовлекается в производство либо реализуется через УМТО
Кубовые остатки ректификации стирола (КОРС)
содержат до 30 % стирола, 7 - 8 % а-метилстирола, до 60 % смолы, а также
нафталин, фенантрен. Количество остатков зависит от режима ректификации,
ингибитора полимеризации стирола и составляет около 25 кг на 1 т стирола.
Значительную часть кубовых остатков сжигают.
Принципиальная
схема ректификации стирола и сжигания корса
Стирол выделяют под
глубоким вакуумом (остаточное давление 13-2 кПа) и при относительно низких
температурах. В едином агрегате работают две ректификационные колонны: на
первой выделяется этилбензольная фракция, направляемый на дегидрирование, и на
второй - стирол. Колонны снабжены пленочными кипятильниками, что сокращает
время пребывания в них стирола и уменьшает степень его полимеризации. Вакуум
создается мощными паро-эжекционными установками. Кубовые остатки ректификации
стирола сжигаются в печи (термическое сжигание). Сущность сжигания
заключается в том, что корс вводимый в печь сжигания, разлогается при высоких
темературах (900 - 1050 градусов) и органические примеси сгорают образуя
продукты полного сгорания (СО2, Н2О, NО2
и т.д).
Состав КОРС, образующийся в
процессе дегидрирования этилбензола
Неидентифицированные
«легкие» вещества
Сравнительный анализ кубовых
остатков ректификации стирола разных промышленных предприятий, представленный
по содержанию в них мономерного стирола, полимера (полистирола) и
высококипящего «тяжелого» остатка позволяет заметить значительные различия его
состава
Характеристика состава КОРС по
промышленным предприятиям
Средняя
молекулярная масса полимера
Завод
«Пластмасс» (г. Актау, Казахстан)
Завод
«Синтетического каучука» (г. Сумгаит, Азербайджан)
Процесс ректификации загрязнённого стирола по
характеру сырья и получаемых продуктов относится к взрывопожароопасным
производствам с токсичными средами и особо вредными условиями труда.
При атмосферном давлении в отсутствии
инициаторов и ингибиторов стирол начинает медленно полимеризоваться уже при 60 0 С
со скоростью примерно 0,1% в час. При 100ºC эта
скорость уже составляет 2,1% в час, а при 150ºC - 50% в
час. Наличие большого количества насосного оборудования, аппаратов, запорной
арматуры создаёт условия для возникновения подсосов воздуха в систему,
пропусков жидких и газообразных углеводородов, что может привести к образованию
взрывоопасных концентраций внутри аппаратов и трубопроводов, загазованности
помещений и территории, взрыву, возникновению пожаров и загораний. Основными
факторами, характеризующими производство с точки зрения опасности при работе,
являются:
ароматические углеводороды - этилбензол, стирол
- являются токсичными веществами, которые при выделении в атмосферу могут
привести к производственным отравлениям;
опасность получения термических ожогов о
нагретые поверхности при пропуске пара, конденсата, горячих продуктов;
опасность получения механических травм при
нарушении правил обслуживания машинного оборудования;
опасность поражения электрическим током;
опасность получения травм в результате
разгерметизации аппаратов и трубопроводов;
опасность получения травм при проведении работ
на высоте и внутри аппаратов.
Энергетический потенциал блока ректификации
этилбензола, стирола не высок, так как процесс осуществляется под вакуумом при
низких температурах. Находящиеся в блоках продукты характеризуются высокой
химической стабильностью, что исключает возможность внутренних взрывов.
Потенциальной опасностью является
разгерметизация напорных трубопроводов, транспортирующих жидкие углеводороды,
разлив которых при наличии источников зажигания может вызвать пожар.
Важнейшими параметрами процесса ректификации
являются температура и давление. Температура регулируется подводом тепла от
внешних источников. Повышение давления возможно при перегреве материальных
потоков, отсутствии хладоносителей, выходе из строя системы контроля и
регулирования.
Классификация блока по взрывоопасности
Номер
позиций аппаратуры, оборудования по технологической схеме, составляющие
технологический блок
Относительный
энергетический потенциал технологического блока
Класс
зоны по уровню опасности возможных разрушений, травмирования персонала
Насосы
Теплообменники Колонны ректификационные Барометрические баки Емкости
Условие
(метод) и место захоронения, обезвреживания, утилизации
Вывозится
на площадку Г для компаундирования с мазутом или в цех №13 для
компаундирования с нефтью или реализации потребителю
Количество
образующихся сточных вод, м 3 /ч
Условия
(метод) ликвидации, обезвреживания, утилизации
Установленная
норма содержания загрязнений в стоках, мг/л
Стирольная
вода из емкости пароэжекторных установок
Постоянно
при работе блока полимеризации и блока ректификации
При
выходе из строя или ремонте печей в канализацию РО К-17
Нефтепродукты
не более 50 мг/л, стирол - не более 25 мг/л, фосфаты - не более 1 мг/л,
цинк - не более 0,05 мг/л
Гранулы по пневмотранспорту с блока производства
полистирола поступают в бункер через циклон где происходит отделение бисера от
воздуха. Бисер собирается в бункер, а отработанный воздух поступает в рукавный
фильтр (ФРУ), где очищается от пыли и выбрасывается в атмосферу.
Пыль бисера, уловленная рукавным фильтром ФРУ,
ссыпается в мешок и отправляется для дальнейшей переработки в блоке
полимеризации.
Гранулы из бункера через автоматические весы
затаривается в мешки (25кг.) или мягкие контейнеры типа МКР 1,0 С с
полиэтиленовым вкладышем (500кг).
Поддоны с мешками или мягкие контейнеры
электропогрузчиком транспортируются в склад готовой продукции.
В момент расфасовки готовой продукции в мешки
или контейнера происходит отбор пробы гран состава лабораторией ОТК для
определении физико-химического свойств готовой продукции. По результату отбора
пробы расфасованным партиям присваивается сортность. Высший сорт и 1 сорт
отправляется потребителю, бракованная продукция отправляется на переработку.
Готовая продукция расфасованная по партиям
отгружается потребителю в авторефрижераторы или ж/д вагоны.
Количество
образования выбросов по видам (т/год)
Условие
(метод) ликвидации, обезвреживания, утилизации
Установленная
норма содержания загрязнения в выбросах
Объем
потока газовоздушной смеси на выходе из источника выброса
1.
Расфасовочные шкафы (местные отсосы от мест расфасовки красителей), труба
циклона ФРУ-56, ист. № 338: - взвешенные вещества
2.
Расфасовочные шкафы (местные отсосы от мест расфасовки красителей), труба
циклона ФРУ-58, ист. № 339: - взвешенные вещества
3.
Экструдер поз. Э-109/1-3, поз. Э-107/1-3 (местный отсос от головки
экструдера), вентиляционная труба В-78, В-79, В-80, В-81, В-82, В-83, ист. №
342: - стирол
4.
Дробилка каучука поз. Д-30/1-3 (местный отсос), вентиляционная труба В-2,
ист. № 343: - стирол
5.
Местный отсос от сальниковых камер насосов поз. Н-55/1-3, вентиляционная
труба В-3, ист. № 344: - стирол; - пыль полистирола
6.
Дробилка каучука поз. Д-30/4 (местный отсос); местные отсосы от
пробоотборников аппаратов поз. ФП-52/1-3, П-56/1-3; от фильтров поз.
Ф-34/1-6; от лючков и из бельтингового рукава растворителей поз. Р-26/1-4,
вентиляционная труба В-9, ист. № 345: - α-метилстирол;
- стирол; - гидроперекись изопропилбензола; - амилмеркаптан; - дифосфит; -
масло минеральное нефтяное
0,1853 0,3707 0,037 0,1853 0,0741 1,1112
0,0065 0,013 0,0013 0,0065 0,0026 0,039
5,293 10,586 1,059 5,293 2,117 31,758
7.
Теплообменники поз. Х-25/1-4, труба-воздушка, ист. № 346: - стирол
8.
Емкость поз. Е-60, труба воздушка, ист. № 347: - стирол
9.
Барометрические баки поз. Б/Б-66/1-3; поз. Б/Б-71/1-3, труба-воздушка, ист.
№ 348: - стирол
10.
Местный отсос от пробоотборников растворителей поз. Р-26/1-4; выделения из
помещения отделения полимеризации 2 этаж, вентиляционная труба ист. № 1236: -
α-метилстирол; - стирол; - гидроперекись
изопропилбензола; - амилмеркаптан; - дифосфит; - масло минеральное нефтяное
0,002 19,90002 0,002 0,001 0,0079 0,105
0,000056 0,698001 0,00007 0,000035 0,00028 0,0037
0,012 148,293 0,015 0,007 0,059 0,786
11.
Емкость поз. Е-50/1-3, труба-воздушка, ист. № 1237: - α-метилстирол;
- стирол; - гидроперекись изопропилбензола; - амилмеркаптан; - дифосфит; -
масло минеральное нефтяное
0,000006 0,1112 0,00036 0,000001 0,000077 0,000003
0,0000002 0,0039 0,000013 0,0000001 0,0000003 0,0000001
21,704 423222,22 1410,741 10,852 32,556 10,852
12.
Холодильник поз. Х-70/1-3, труба-воздушка, ист. № 1238:- стирол
13.
Бункер поз. Б-110/1-3, труба-воздушка, ист. № 1239: - взвешенные вещества
14.
Скоростной смеситель поз. С-106/1,2, вентиляционная труба В-4, ист. № 1240:
- взвешенные вещества
15.
Скоростной смеситель поз. С-106/3, ист. № 1241: - взвешенные вещества
16.
Выделения из помещения полимеризации, 3 этаж, ист. № 1242: - стирол; -
дифосфит; - масло минеральное нефтяное
17.
Выделения из отделения грануляции, вентиляционная труба В-35, В-36, В-37,
В-38, В-6, ист. № 1243: - пыль полистирола
18.
Емкость поз. Е-8, труба-воздушка, ист. № 1244: - масло минеральное нефтяное
19.
Емкость поз. Е-11, труба-воздушка, ист. № 1245: - дифосфит
20.
Емкость поз. Е-7, труба-воздушка, ист. № 1246: - дифосфит
25.
Отделение расфасовки и упаковки полистирола от точек поз. 151/1-8, 152/1-4,
труба циклона ФРУ-3А, ист. № 334: - пыль полистирола
26.
Бункеры поз. 2231/1-6, труба циклона ФРУ-В-7, ист. № 335: - пыль полистирола
27.
Расфасовка полистирола, труба циклона ФРУ-В-4, ист. № 336: - пыль
полистирола
28.
Расфасовка полистирола, труба циклона, ист. № 337: - пыль полистирола
11.
Труба-воздушка ёмкости поз. Е-1/1,2, ист. № 1253: - стирол.
12.
Дымовая труба циклонной печи сжигания поз. П-5/1,2, ист. № 361: - азота
диоксид; - азот оксид; - сера диоксид; - углерод оксид; - метан; -
бензапирен.
7,356210 4,580282 0,034214 3,250000 0,325000 0,000000001
0,25880040 0,1606440 0,0012000 0,1140000 0,0114000 0,00000001
255,439 159,047 1,188 112,867 11,287 5,7Е-06
13.
Вентиляционная труба В-1,2 из насосной об.1344, ист. № 362: - стирол.
Воздушки
емкостей не плотности ист. № 6107 (359)
-винилбензол
(стирол) 0,613602 - этилбензол 0,020810
Помещение
насосной объекта 1342, Вент. труба В-1,2 ист. № 360
-
винилбензол (стирол) 0,373500 - этилбензол 1,265900
Анализ производства полистирола и взаимодействия
с окружающей средой и методы уменьшения выбросов вредных веществ.
Производство полистирола является одним из
источником загрязнения окружающей среды. Основным объектом загрязнения является
- воздушный бассейн и гидросфера. В атмосферу выбрасывается токсикогенно в виде
непредельных соединений, а также оксидов, щелочей и солей. Из вредных выбросов
две третьих приходится на газообразные продукты, а остальные на твердые
пылевидные частицы. В водный бассейн поступают сточные воды производства.
Удельный расход воды на производство 1 тонны продукции может составлять от 0,5
м3 до 2000 м3. Приведенные данные свидетельствуют об важности мероприятий по
защите окружающей среды. Основными причинами загрязнения окружающей среды
являются: использование морально и физически устаревшего оборудования,
конструктивные недостатки технологического процесса, наличие в них значительной
доли ручного труда и как следствие его потенциальной опасности. К наиболее
распространённым причинам загрязнения воздушной среды относятся:
1. Неполная конверсия мономеров и потери летучих
органических веществ.
2. Выбросы в атмосферу примесей и
загрязнений, присутствующих в используемом сырье.
. Недостаточная герметичность
оборудования.
. Испарение летучих продуктов из
различных резервуаров и хранилищ.
Основные разновидности вредных газообразных
веществ выделяемых в процессе их производства приведены в таблице.
В
пределах производственной площадки мг/м3
Определение состава вредных веществ загрязнения
воздуха требует использование сложного лабораторного оборудования. Это
газоанализаторы, газовые хроматографы. В последнее время большое
распространение получают экспрессные методы анализа, позволяющие получать
результат на месте после взятия пробы. Это такие методы как - с помощью
реакционных бумаг и с использованием колористических трубок.
При производстве полистирола есть разнообразные
газовые выбросы в атмостферу, основным является стирол, этилбензол и
изопропилбензол, пары воды (эмульсионные и суспензионные). Источниками выбросов
являются воздушки аппаратов-реакторов, аппараты, работающие под давлением,
местные отсосы форполимеризаторов, экструдеров-грануляторов, отделения
расфасовки готовой продукции. Среди компонентов газовых выбросов наиболее
токсичным является стирол, концентрация которого может достигать 350мг/м3.
Производство полистирола разработано в 1974 году такт как в те года меньше
всего уделялось по направлению экология. В связи с этим никаких установок по
обезвреживанием газовых выбросов у производства полистирола нет. Рассмотрев
несколько способов очистки выбросов вредных веществ (каталитическое окисление,
адсорбционное извлечение стирола) я остановился на методе адсорбционное
извлечение стирола из загрязненного воздуха на активном угле и последующий
возврат его в производство. В производстве ударопрочного полистирола в газовых
выбросах содержится в основном стирол (остальные примеси на уровне следов). В
этом случае становится возможным адсорбционное извлечение стирола из
загрязненного воздуха на активном угле и последующий возврат его в
производство. Стирол хорошо адсорбируется активным углем и десорбируется острым
водяным паром. Часть адсорбированного стирола (около 5 % от массы угля) прочно
удерживается углем и в процессе десорбции водяным паром не извлекается.
Количество прочно адсорбированного стирола остается практически неизменным на
протяжении большого числа циклов "адсорбция-десорбция" и не зависит
ни от содержания стирола в отходящих газах, ни от времени пребывания его в
адсорбере. Преимущество адсорбционного способа очистки этот способ менее
энергоемкий и дает возможность утилизировать стирол, извлеченный из выбросного
потока. Процесс очистки промышленных газов от стирола заключается в
осуществлении двухфазного цикла "адсорбция-десорбция". При адсорбции
газовые выбросы подаются в нижнюю часть адсорбера 1, в котором происходит
поглощение содержащихся в воздухе веществ активным углем. Очищенный газ
удаляется в атмосферу. Регенерация угля проводится (после насыщения его
стиролом) острым водяным паром. Десорбат собирается в сепараторе 6 (после
охлаждения в холодильнике 2), где происходит расслаивание конденсата на два
слоя (органический и водный).
1
- адсорбер; 2 - холодильник: 3 - парогенератор; 4 - насос; 5 - сборник
конденсата; 6 - сепаратор; 7 - сборник стирола. Рисунок 2- Технологическая
схема очистки промышленных выбросов от паров стирола.
Водный слой поступает в парогенератор 3 для
получения пара на десорбцию, а стирол (органический слой) собирается в сборнике
7, откуда передается в отделение подготовки реагентов для стадии полимеризации.
Температура пара при десорбции от 110 до 120 °С; расход пара от 5 до 7 кг на 1
кг рекуперата; продолжительность процесса десорбции - не менее 60 мин;
продолжительность расслаивания - не менее 2 ч; степень десорбции - 100 %.
Стирол, извлеченный из активного угля после
разделения в сепараторе поступает на установку ректификации для получения
товарного стирола с содержанием основного вещества до 96 %. Ректификация
проводится под вакуумом. Кубовые остатки после стадии ректификации направляются
на установку сжигания.
Водный слой конденсата, полученный в процессе
десорбции, насыщен стиролом и содержит некоторое количество этилбензола и
изопропилбензола. При отстаивании в сепараторе основное количество примесей
переходит в стирольную фазу, а стирол, растворенный в водном слое, отдувается
воздухом. Отдуваемый воздух объединяется с отходящими газами и поступает в
адсорбер. Расход отдуваемого воздуха достигает от 10 до 15 м3 на 1 т водного
конденсата.
Сухие механические пылеуловители. К сухим
пылеуловителям относятся все аппараты, в которых отделение частиц примесей от
воздушного потока происходит механическим путем за счет сил гравитации,
инерции, Кориолиса. Такие пылеуловители условно делятся на три группы:
пылеосадительные камеры, принцип работы которых
основан на действии силы тяжести (гравитационной силы);
инерционные пылеуловители, принцип работы
которых основан на действии силы инерции;
циклоны, батарейные циклоны, вращающиеся
пылеуловители, принцип работы которых основан на действии центробежной силы.
Пылеуловительная камера представляет собой пустотелый
прямоугольный короб, в нижней части которого имеется отверстие или бункер для
сбора пыли. Пылеуловитель такой формы применяются на расфасовочных течках в
складе готовой продукции.
Рис. 1. Пылеосадительные
камеры полая
I- запыленный газ (поток полистирола); II
- очищенный газ (полистирол); III
- пыль, 1 - корпус; 2? 3 - штуцер для удаления пыли в ФРУ;.
Скорость газа в камерах составляет 0,2-1,5 м/с,
гидравлическое сопротивление 50-150 Па. Пылеосадительные камеры пригодны для
улавливания крупных частиц размером не менее 50 мкм. Степень очистки газа в
камерах не превышает 40-50%.
Газ в инерционном аппарате поступает со
скоростью 5-15 м/с. Эти аппараты отличаются от обычных пылеосадительных камер
большим сопротивлением и высокой степенью очистки газа. Такой вид очитки от
пыли применяется в промежуточных бункерах при расфасовки полистирола.
Рис. 2.
Инерционные пылеуловители: а - камера с перегородкой, б - камера
с расширяющимся конусом, в - камера с заглубленным бункером
Для улучшения удаления пыли из пневмотранспорта
полистирола произвести внедрение в линию центробежных циклонов. Центробежные
циклоны выполняют одновременно и роль пылеулавливающего аппарата. Эффективность
улавливания пыли в циклонах повышается с уменьшением диаметра корпуса, но при
этом снижается их пропускная способность. Для обеспечения соответствующей
производительности пневмотранспортной установки небольшие циклоны группируют в
батарею. Коэффициент пылеулавливания батареи циклонов составляет 0,76-0,85 и
несколько повышается с увеличением входной скорости (с 11 до 23 м/с). Циклоны
рекомендуется использовать для предварительной очистки газов и устанавливать
перед высокоэффективными аппаратами (например, фильтрами) очистки.
Рис.
Циклон типа ЦН-15П: 1 - коническая часть циклона; 2 - цилиндрическая часть
циклона; 3 - винтообразная крышка; 4 - камера очищенного газа; 5 - патрубок
входа запыленного газа, 6 - выхлопная труба; 7 - бун
Похожие работы на - Анализ взаимодействия процесса получения полистирола с окружающей природной средой Курсовая работа (т). Экология.
Сочинение По Истории Люди С Ограниченными Возможностями
Доклад: Реконструкция костной ткани
Методичка На Тему Методика Проведення Моніторингу Результативності Управлінської Діяльності Органів Управління Освітою В Автономній Республіці Крим
Реферат: Владение как элемент вещного права. Скачать бесплатно и без регистрации
Курсовая работа: Личные характеристики менеджера
Сочинение Про Мономаха
Реферат: Everything Ends Essay Research Paper Jennifer stopped
Контрольная Работа По Немецкому 7 Класс
Доклады На Тему История Языка Программирования Lisp
Эссе На Тему Древний Египет
Понятие и функции институтов, их социально-экономическое содержание и влияние на эффективность экономической системы. Институциональная структура и институциональная среда
Контрольная Работа На Тему Франкское Государство
Курсовая работа по теме Кривая производственных возможностей. Осуществление ценовой дискриминации
Реферат: Конструкция модели секвенатора дезоксирибонуклеиновой кислоты (ДНК)
Реферат Школа России
Сочинение О Телеведущем 7 Класс Пример
Сочинения Ленина Скачать Бесплатно
Реферат: The Effectiveness Of Blood Brothers Essay Research
Реферат: Особенности построения цепи поставок на рынке уборочной техники
Курсовая Работа Маркетинговые Исследования Рынка Женской Одежды
Реферат: Узбекская литература
Реферат: Основные тенденции применения ЭВМ в сфере образования
Курсовая работа: Використання різних джерел інформації для підготовки та прийняття управлінських рішень