All You Need To Know About Metal Casting
inovacast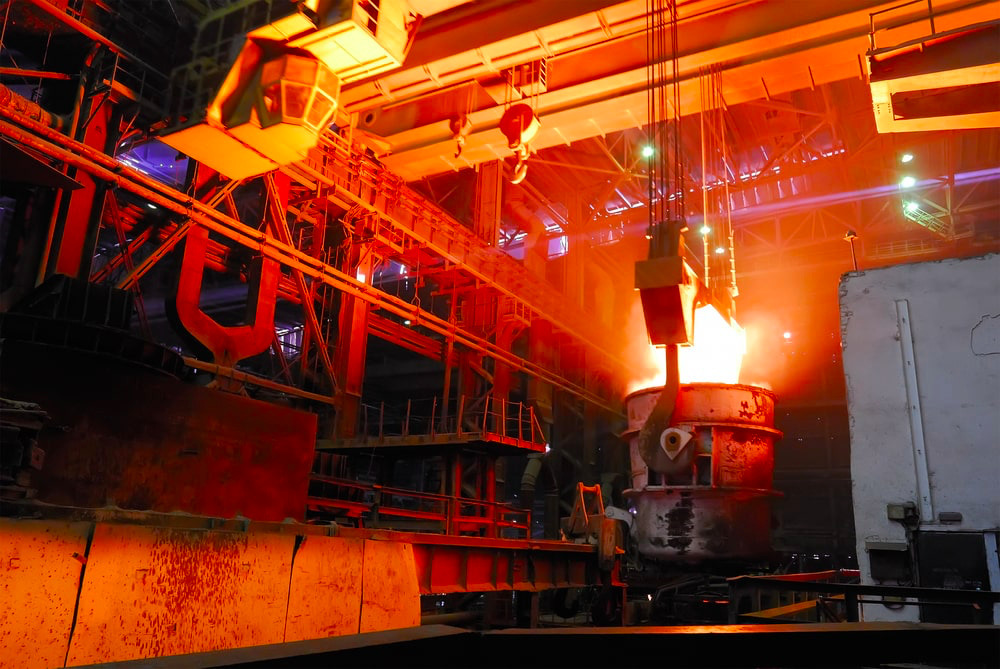
Steel castings in India is a 7,000 year old manufacturing and fine-arts process. Molten metal gets transferred from the crucible into a mold to create a buoyant metal cast object during metal casting. After cooling the metal and the mold, the metal object is removed and finished. Wax loss, plaster mold casting, die casting, and sand casting is just a few traditional metal casting techniques. Metal casting techniques have been around for thousands of years, and they've been used to make sculptures, jewelry, transportation, weapons, and tools.
A copper frog from 3200 BCE was discovered in modern-day Iraq as the first known cast object. Metal casting became extremely popular during the Bronze Age. The Zhou Dynasty was the first to use iron casting. Lost wax casting has been used in the Middle East and West Africa throughout history. Metal casting technology has exploded in the twentieth century, resulting in developing processes that are still used today.
What is metal casting used for?
Metal casting is being used to make tools, weapons, and religious objects throughout history. Casting is a low-cost method of producing complex shapes and designs and multiples of the same thing. Metal casting has a wide range of applications in manufacturing, particularly in the development of technology and transportation. Castings can also be as small as a few grams, such as a cast ring, or as large as thousands of pounds, such as a diesel engine. The complexity of cast shapes ranges from simple to highly intricate.
Steel castings in India is an incredibly versatile process, even though transportation and heavy equipment account for most castings produced worldwide. The objects which use metal casting are:
· Household appliances
· Construction equipment
· Farming equipment
· Electrical equipment
· Defense tools, equipment
· Machining tools
· Artistic and sculptural objects
What Are The Types Of Metal Casting?
Steel castings in India is divided into processes that use reusable molds and methods that use disposable molds. The caster helps to melt the metal material in a crucible, pours it into a mold, and then removes the mold material or the casting once it has cooled and solidified in both processes.
The Process Of Metal Casting?
1. Patternmaking of metal
A pattern is a replica of the casting's exterior. Wood, metal, plastic, and plaster are the common materials for designs. Patternmaking is critical in the production of industrial parts, where precise calculations are required to ensure that pieces fit and function correctly.
2. Constructing the core of metal
If the casting is hollow, an additional piece of sand or metal (referred to as a core) is used to shape the internal form. Cores are typically strong but collapsible, allowing them to be removed from the finished casting with ease.
3. Molding of metal
Molding is a multi-step process that uses molding sand to create a cast around the pattern. A flask is a type of frame that holds a mold during casting. Greensand, also known as molding sand, is packed around the design in the flask.
The Process Of Melting And Pouring Metal
After the metal gets melted, it is poured into the mold cavity and allowed to solidify. After the casting has solidified, the shakeout process begins, in which the molds are vibrated to remove sand from the casting.
1. Cleaning of metal
The cast steel castings in India object is removed from the mold and fettled in this final step. The thing is cleaned of any molding material, and rough edges are removed during the fettling process.
2. Casting with a disposable mold
Expendable mold casting is a technique that involves the use of one-time or temporary molds. Resin-bonded sand, ceramic shell, plaster investments, or foam are common materials for these molds. Making your disposable mold is a relatively inexpensive and straightforward process. It's best used for low-volume production.
3. Casting with a non-replaceable mold
Non-expendable molds are metal casting molds that are reusable and permanent. They are more robust and better suited to withstand molten metal's high temperatures than others. Because of their high strength, low porosity, and heat resistance, permanent molds are frequently made of steel or cast iron. Molds that aren't disposable are ideal for producing multiples of the same cast metal object.
What are the advantages of metal casting?
· Steel castings in India allows for the creation of complex shapes.
· Internal cavities or hollow sections, for example, are simple to implement.
· Large components can be cast in a single piece.
· Casting can be used to make materials that are difficult or expensive to make using other methods.
· For medium to large quantities, casting is less expensive than other manufacturing processes.
· Casting is possible for almost all metals.
· Near-net shape is frequently produced without or with only minor post-processing.
What are the disadvantages of metal casting?
· Surface finish is relatively coarse, requiring a wider tolerance and making it unsuitable for mating interfaces.
· casting, such as shell molding, has size and pattern limitations.
· Although additive manufacturing is a process such as binder jetting that has recently been used to make a mold, patterns are time-consuming and expensive to create.
· Due to the high cost of dies, die casting can be prohibitively expensive for small to medium quantities.
· The size and material of the part are determined by the casting process used. For permanent mold castings, for example, only non-ferrous metal can be used.
Conclusion
You can set up your home foundry and casting station while keeping safety in mind. Protective clothing, such as natural fiber clothing, long pants and sleeves, insulated gloves, and safety goggles, should be worn. To avoid any dangers from dangerous fumes, work in a well-ventilated area.
Ensure you have a chemical fire extinguisher on hand and keep the space between the furnace and the mold-free of obstructions. Expendable or non-expendable molds are used in the most common types of metal casting. Ceramic shell molds are created by dipping a wax model in multiple layers of ceramic shell slurry, burning out the wax, and casting the metal within.