Abs Nylon
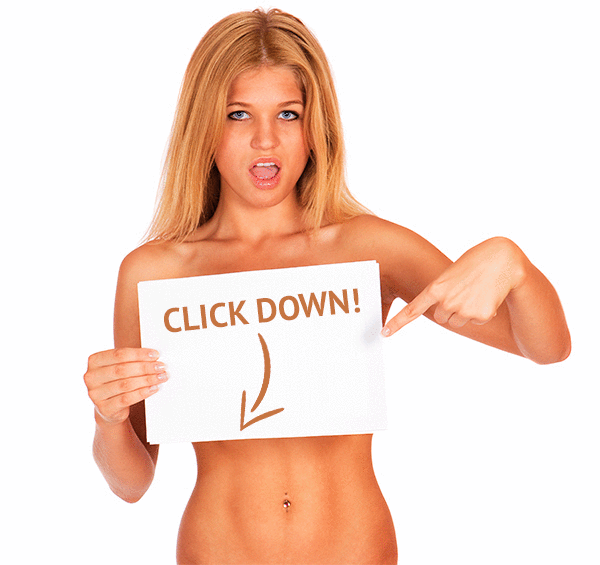
🔞 ALL INFORMATION CLICK HERE 👈🏻👈🏻👈🏻
Abs Nylon
Opens in a new window Opens an external website Opens an external website in a new window
This website stores data such as cookies to enable essential site functionality, as well as marketing, personalization, and analytics. By remaining on this website you indicate your consent. Privacy Policy
Learn
Blog
Read our newest customer success story about a major training base for the U.S. Army.
Industries
Resources
Company
Search
Shop
Support
English
Deutsch
Español
Français
Italiano
日本語
©2022
Markforged. All rights reserved.
PLA, ABS, and nylon are three of the most popular 3D printing materials. All can be extruded on basic desktop 3D printers and, at around $20 per spool, they are among the most affordable filaments available today. Most people focus on the PLA vs ABS debate, but Nylon is a valuable third entrant with different material properties.
PLA and ABS are both thermoplastics. PLA is stronger and stiffer than ABS, but poor heat-resistance properties means PLA is mostly a hobbyist material. ABS is weaker and less rigid, but also tougher and lighter, making it a better plastic for prototyping applications.
Enter nylon, a flexible plastic that injects a new set of filament properties into the mix, featuring greater chemical resistance and toughness compared to PLA and ABS, but also reduced strength.
This post compares PLA vs ABS and now nylon, and then details how one of these thermoplastics has been augmented to serve a wider range of manufacturing applications. Plus, a bonus exploration of Onyx filament.
PLA is a user-friendly thermoplastic with a higher strength and stiffness than both ABS and nylon. With a low melting temperature and minimal warping, PLA is one of the easiest materials to 3D print successfully. Unfortunately, its low melting point also causes it to lose virtually all stiffness and strength at temperatures above 50 degrees Celsius. In addition, PLA is brittle, leading to parts with poor durability and impact resistance.
Although PLA is the strongest of these three plastics, its poor chemical and heat resistance force it into almost exclusively hobbyist applications.
ABS, while weaker and less rigid than PLA, is a tougher, lighter filament more suitable for some applications beyond purely hobbyist. ABS is a bit more durable, is about 25% lighter, and has four times higher impact resistance. ABS does require more effort to print than PLA because it’s more heat resistant and prone to warping. This calls for a heated bed and an extruder that is 40-50 degrees Celsius hotter. ABS, while by no means a heat resistant plastic, has superior heat deflection temperature compared to PLA and nylon.
The improved durability over PLA lends ABS to some more practical applications, such as prototyping and low-stress end-use parts.
Nylon is a flexible, durable plastic with less strength and stiffness than both PLA and ABS. Its malleability lends it much more toughness than the other two, however, with an impact resistance ten times that of ABS. Nylon also boasts a good chemical resistance, which opens the possibility to more industrial applications. As with ABS, nylon requires extra care to print; it needs to be extruded at high temperatures and, due to its tendency to soak up moisture from the air, must be kept in a dry box.
Nylon is tougher and more resistant to chemicals than ABS and PLA, but its low strength and stiffness keep it from being widely used in the manufacturing industry. As a result, advancements in 3D printing materials has introduced nylon-fiber mixtures, opening the door to accessible industrial 3D printing .
Filled nylon is a mixture of nylon with small particles of a stronger material such as fiberglass or carbon fiber. These mixtures preserve the favorable properties of nylon while adding considerable strength and stiffness. Markforged’s Onyx filament is an example of one of these mixtures, combining nylon with chopped carbon fiber in order to improve key properties of the material. Onyx is 1.4 times stronger and stiffer than ABS and can be reinforced with any continuous fiber. The development of 3D printed continuous fibers has enabled a new category of stronger 3D printed parts .
With high strength and stiffness, excellent durability, and good chemical resistance, filled nylons such as Onyx are some of the few 3D printed thermoplastics tough enough for the factory floor. Nylon mixtures are suitable for fixtures, jigs, functional prototypes, and even end use parts.
PLA, ABS, and nylon are great beginner thermoplastics due to their low price point and general ease of printing. If you are looking to begin 3D printing for industrial use cases, however, filled nylons offer the superior material properties needed to withstand manufacturing environments.
To learn more about Markforged's continuous fibers, check out our blog post where we compare fiberglass with carbon fiber!
All of the blogs and the information contained within those blogs are copyright by Markforged, Inc. and may not be copied, modified, or adopted in any way without our written permission. Our blogs may contain our service marks or trademarks, as well as of those our affiliates. Your use of our blogs does not constitute any right or license for you to use our service marks or trademarks without our prior permission. Markforged Information provided in our blogs should not be considered professional advice. We are under no obligation to update or revise blogs based on new information, subsequent events, or otherwise.
Subscribe to get new Markforged content in your inbox
Based on your browser settings it looks like you may prefer to view this page in German, would you like to switch languages?
Based on your browser settings it looks like you may prefer to view this page in German, would you like to switch languages?
Based on your browser settings it looks like you may prefer to view this page in German, would you like to switch languages?
Based on your browser settings it looks like you may prefer to view this page in German, would you like to switch languages?
Based on your browser settings it looks like you may prefer to view this page in German, would you like to switch languages?
Based on your browser settings it looks like you may prefer to view this page in German, would you like to switch languages?
https://www.facebook.com/MachineDesignMagazine/
https://www.linkedin.com/company/10998894
What’s the Difference Between PLA, ABS, and Nylon?
Unlike standard ink cartridges, there are several variations of filament on the market, each with its own unique properties.
Automating the Depowdering of 3D-Printed Parts Streamlines Production
IIoT solutions bring machine data to life to streamline and secure performance
If you’re a machine builder trying to differentiate your company from the competition, you may be considering investing in Industrial Internet of Thi…
What’s Abuzz in Industrial Automation: Insights from Hannover Messe
Last May in Hannover, at one of the world’s largest trade fairs, the future of industrial automation was on everyone’s lips.. What does that future ho…
Why universal automation is a catalyst for enabling profitable machine OEM business transformation
Today’s OEMs who build machines for industrial applications are at a critical crossroads. The way end users make purchasing decisions is altered by n…
The first ride of the team @thoemusmaxon on Brazilian soil to get used to the climate. The UCI World Cup is about t… twitter.com/i/web/status/1…. maxo…
This site requires you to register or login to post a comment.
No comments have been added yet. Want to start the conversation?
Sign up for Machine Design eNewsletters SIGN UP
Advanced Machine Engineering: Technology Changes are Driving Transformation
Give Them Credit: Researcher Sentiment Favors Open Data Mandates and Data Sharing
Programming Languages for Quantum Computing
Pointing to the Future, Siemens Celebrates its Legacy
New Autodesk Fusion App Improves Design process
Bringing High-Tech to the Maritime Industry Improves Safety and the Bottom Line
Owl Wings Inspire Airfoil Design and Noise Suppression
IDEA! Awards: Automation & Software Category Winners
Engineering Design with NX Curriculum Package
Demystifying 3D Printing Resolution, Accuracy, and Precision
Micro 3D Printing Helps Fabricate Microwells for Microgravity
Micro 3D Printing: Enabling Miniaturization
Academic race car manufacturer designs record-breaking race cars from scratch within a few months
https://www.facebook.com/MachineDesignMagazine/
https://www.linkedin.com/company/10998894
3D printing has always, and always will be, an industrial mainstay of manufacturing and prototyping. It also isn’t a surprise to anyone that the technology over the past decade has been leaving corporate barriers and entering the homes of everyday consumers—from tech aficionados to budding DIY enthusiasts.
It is still a relatively new technology, with plenty of vendors that sell their own 3D printers and the substance used to create printed objects—filament. Filament to 3D printers is ink to the conventional printers we all know and love.
Unlike standard ink cartridges, however, there are several variations of filament on the market, each with its own unique properties. This guide is meant to break down the different types of filaments available today, outlining their defining characteristics to help users of 3D printers identify the right filament for the job.
So, let’s dive into some of the more traditional and well-known filaments available: PLA, ABS, and Nylon.
PLA, short for polylactic acid, is currently the standard filament type with the lowest barrier to entry in use. It’s a biodegradable thermoplastic, meaning it’s much more environmentally friendly when compared to other plastics. It is produced using food starches, so it has a more agreeable odor (if any) and may be the safest choice for use in indoor environments as any emissions may be more biocompatible.
PLA generally doesn’t contract once it cools down after printing, meaning if you’re using a printer that lacks a heated bed, it’s easier to maintain bonds between the plastic layers. It’s not quite as robust or tough as its counterpart ABS (more on that below), meaning it’s more brittle, but offers sound strength and rigidity with increased user-friendliness. In the past, ABS was considered the optimal material for best print appearance, but in recent years optimizations to PLA formulas and print settings have made this thermoplastic the best choice for general, run-of-the-mill 3D printer projects and household goods you would create.
Print temperature range for PLA will depend on the exact printer and project, but the accepted standard is between 185°C–225°C. PLA has one drawback, and that is that it must remain under 45°C after printing. So, printed parts will deform when left in a car on a hot summer’s day.
ABS — acrylonitrile butadiene styrene
ABS, short for acrylonitrile butadiene styrene, is a tried and true favorite of engineering sorts—also a thermoplastic, it’s about 20% lighter than PLA and offers more flexibility, but it has none of the user-friendliness of PLA, which makes it a rather niche go-to when it comes to 3D printer projects.
Unlike PLA, a heated print bed, and even a 3D printer enclosure may be called for when using ABS filament. Otherwise the printing layers, once deposited, will cool and the plastic will warp and contract, throwing the entire print job off measure. When it comes to emissions, again unlike PLA, its odors are not pleasant and can cause acute migraines, and thus should only be used in a well-ventilated area. These limitations are among the reasons why PLA has taken dominance when it comes to more mainstream 3D printer projects—but due to its durability, it’s ideal for printing specific parts that must withstand varying stress or loading cycles like enclosures or functional prototypes.
Print temperature range for ABS runs between 230°C–260°C.
Alongside both PLA and ABS, Nylon, also known as polyamide—a repeating molecule linked by an amide bonds—is another niche of filament that is a high-end engineering thermoplastic. It has extreme toughness and durability, but requires excessive fine-tuning to produce successful prints, so it’s best suited to expert users who want to print small machine parts like gears.
The filament itself is strong and flexible, yet light and resilient to “wear and tear” associated with continual use. For reference, weed whacker trimmer line is made with Nylon filament. Due to its increased strength and elasticity over PLA and ABS, Nylon is good for industrial applications, such as machine parts or tools, or replacement of automobile parts. It can also bond to itself very well, meaning it’s a great filament for making parts that can be drilled, tapped, or screwed. To add to its versatility, the filament can also be dyed any number of colors by users—the dying, however, must happen prior to printing.
Nylon doesn’t come without its drawbacks, however—the filament is prone to humidity. To print accurately with Nylon, one must keep the spool completely dry and out of humid environments, otherwise it makes a mess.
Print temperature range for Nylon is between 220°C–260°C and should be used with a heated print bed, and an enclosure for larger parts. Some users find that a Garolite bed is necessary along with an application of glue stick to the surface to promote adhesion.
By clicking “Accept All Cookies”, you agree to the storing of cookies on your device to enhance site navigation, analyze site usage, and assist in our marketing efforts. Privacy Policy
Meager solvent and fatigue resistance
Ordinary grades burn easily and won’t extinguish on their own.
Stress cracks are evident in the presence of some greases
Poor resistance for solvents like ketones, esters, and aromatic
Poor UV resistance without protection
May 21, 2022 by Sagar Habib 3 Comments
ABS material is one of the most popular and utilized thermoplastics in the world. Its applicability is extremely impressive with uses found in various sectors ranging from consumer goods to aerospace. Let’s find out more about the infamous plastic material.
ABS plastic is an impact-resistant thermoplastic and amorphous polymer (which means it does not show the characteristics of crystalline solids). It is opaque in nature. ABS is made up of three monomers called Acrylonitrile, Butadiene, Styrene.
Acrylonitrile: It is produced from propylene and ammonia. The element is responsible for the polymer’s high chemical resistance and heat stability.
Butadiene : It is released from ethylene production and steam crackers. The element is responsible for the ABS polymer’s toughness and impact strength.
Styrene : It is released when a modification is made in ethylbenzene. It contributes to the rigidity & processability of ABS plastic.
The thermoplastic became commercially available back in the 1950s when the previous version was modified by adding the third monomer (Butadiene).
The addition of butadiene made it easy to process and increased its toughness significantly.
The most commonly used method to produce ABS is called emulsion (mixing multiple products that usually would not combine into a single product) or a continuous mass technique. ABS’s natural color is an opaque ivory color and is willingly colored using different pigments depending on the application.
Although ABS is known for its rigidness, strength, and chemical resistance, it is heavily affected by polar solvents.
ABS provides great processability compared to other thermoplastics. It doesn’t need fancy settings and can be smoothly processed in standard machinery.
Because of its low melting temperature, Acrylonitrile Butadiene Styrene can be processed in injection molding, blow molding , extrusion molding, and especially in 3D molding. The continuous mass technique I mentioned earlier is a patented process that is rarely used in special applications. The emulsion method is widely used and is considered the best.
The polymer is an ideal choice for systemic applications. Let’s go through with some of its most important properties:
Below are the typical properties of ABS:
ABS material, thanks to its supreme properties, are utilized in many products. The most commonly seen products are keyboard keys used in computers and laptops, toys, lego blocks, face guards, various components in automobiles, etc.
Acrylonitrile Butadiene Styrene has maximum resistance to corrosive chemicals and physical attacks, making it easy to machine. A low melting temperature makes it compatible with injection molding and 3D printing .
The material doesn’t make a big hole in your pocket as it costs about $1.50 to 2.50 per pound.
It’s not advisable to use ABS in high heat scenarios because of the low melting point.
As we compare both benefits and limitations, the positives without any doubt outnumber the negatives. Certain disadvantages might become a small hurdle within the production, but the overall quality and smoothness wouldn’t be affected significantly.
Injection molding and extrusion molding are the two most common methods for ABS processing.
There are situations where determining drying is needed or not is tricky. In case a vented cylinder is used, drying becomes a must.
In scenarios where drying is needed, 4 hours at 80°C is generally sufficient.
Signs of moisture are evident with stripes, streaks, or bubbles. If any of those factors are seen, pre-drying the mold is advisable.
Material Injection Pressure: 50 – 100 MPa
Extrusion temperature: 200 to 240°C
Screw Design: L/D ratio of 25-30 is advisable
ABS plastic is a biocompatible and recyclable material with a recycling number #9. In addition, it is relatively harmless, and no signs of carcinogens in thermoplastic. To date, there hasn’t been a single incident recorded related to harm caused by ABS, meaning it’s safe for use.
Recycled ABS material is often blended with virgin material to produce
Naughty But Nice Video Porno
Good Gagging
High Heels Office