AI for drilling machining
GIBcam TeamToday, automated, NC-controlled drilling machining is no longer magic. The manufacturing processes used are not new, have been known for a long time and the technological boundary conditions are easily controllable.
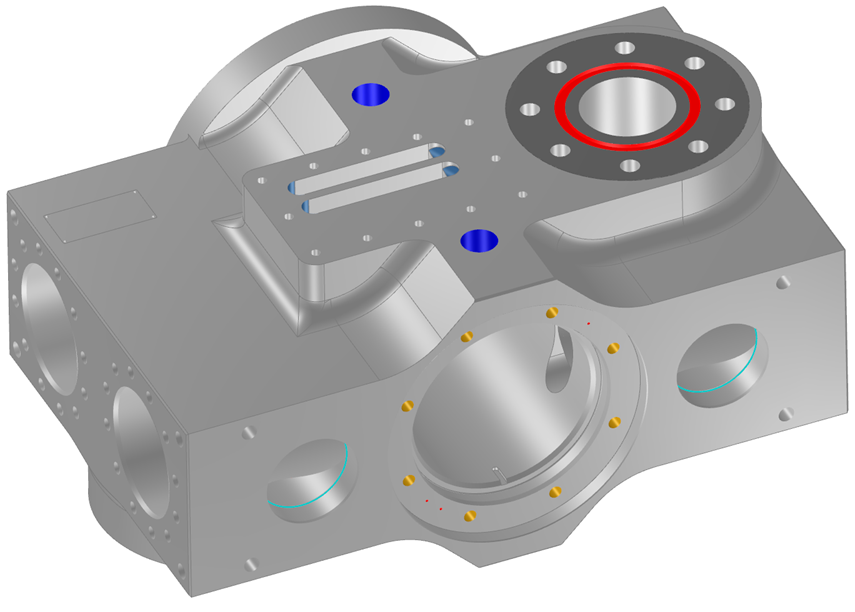
Nevertheless, machining tasks with a high, complex drilling content create challenges for many companies. If one analyses these situations, a few key problem areas often crystallise:
• Data preparation from 3D CAD data takes a long time and is cumbersome. In part, this is only possible manually. Important information about the elements to be drilled is missing or not available transparently.
• The addition of steps necessary for production is not possible or only possible with difficulty in the programming sequence.
• It is not possible to adapt recurring processing steps with individual parameterisation.
• Suitable, available strategies for reducing tool changes are not available.
• The assignment and management of individual cutting values for recurring, identical or comparable machining operations is missing.
• There is no continuous support for multi-sided machining or machining in several clampings or approaches.
• Automatic route optimisation with reduction and control of feed movements is not possible.
• Process safety in particularly complicated or borderline machining situations through complete collision control is not guaranteed.
• The analytical observation of the process sequence on the NC machine in the form of virtual workspace monitoring is not included.
• The possibility of recording or determining the actual state of the machined component as well as the data transfer back into the CAD process cannot be realised.
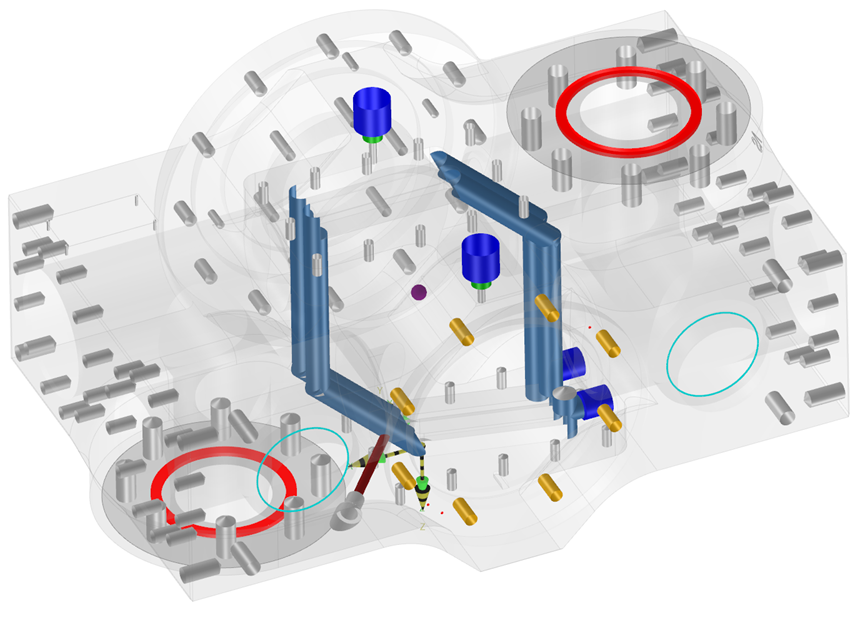
These tasks can be solved today with suitable, highly specialised CAM tools - and AI can be used helpfully for this special application.
For many years, the GIBcam team has been developing, supporting and maintaining GIBcam, a tried-and-tested, production-oriented CAM software that has gained a high degree of recognition through its practice-oriented solutions. The GIBcam 25AX package is the ideal tool for complex 2.5D milling and drilling operations. At its core, the CAM system is based on a feature-based, cycle-oriented methodology, i.e. technological manufacturing features are generated and used that enable a high degree of flexibility and adaptability to the manufacturing process.
Based on the AI integrated in the GIBcam CAM kernel, all necessary steps for data generation and preparation can be mastered with precise flexibility.
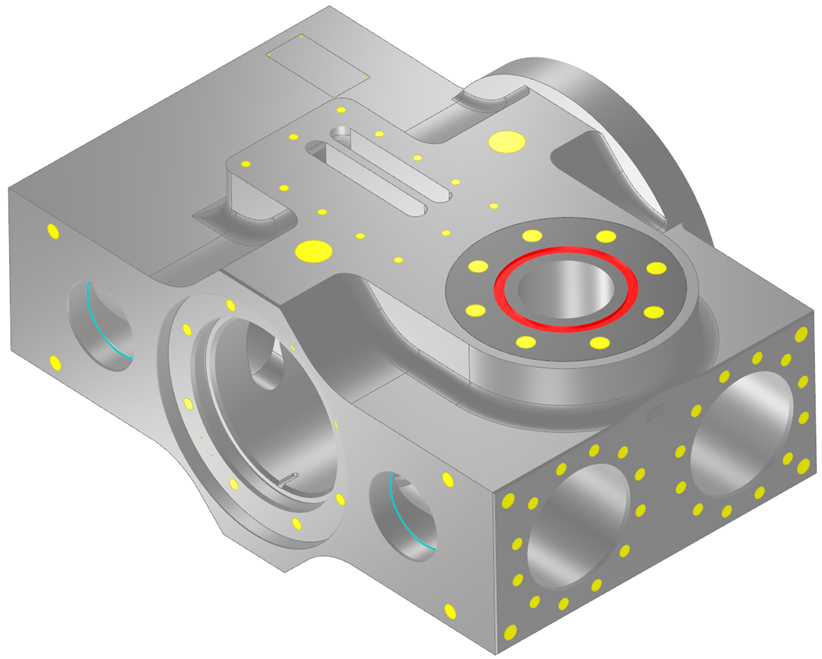
Data preparation from CAD data is thus child's play. The AI kernel generates parameterisable features as a basis for further programming steps. Further technology features supplement standardised technological processes (e.g. sequence of operations for producing a complete thread). In this way, typical facts from the discrepancy between the nominal geometry of the component (i.e. the final state) and the actual state as well as from the planned process steps are taken into account. A high value is placed on the incorporation of one's own individual know-how in order to optimally plan complex manufacturing processes.

An example of this is the creation of linked feature elements - which automatically combine similar machining steps for a complete machining operation using technology features and carry out sequence and infeed optimisation (e.g. according to the <distance minimum> method).
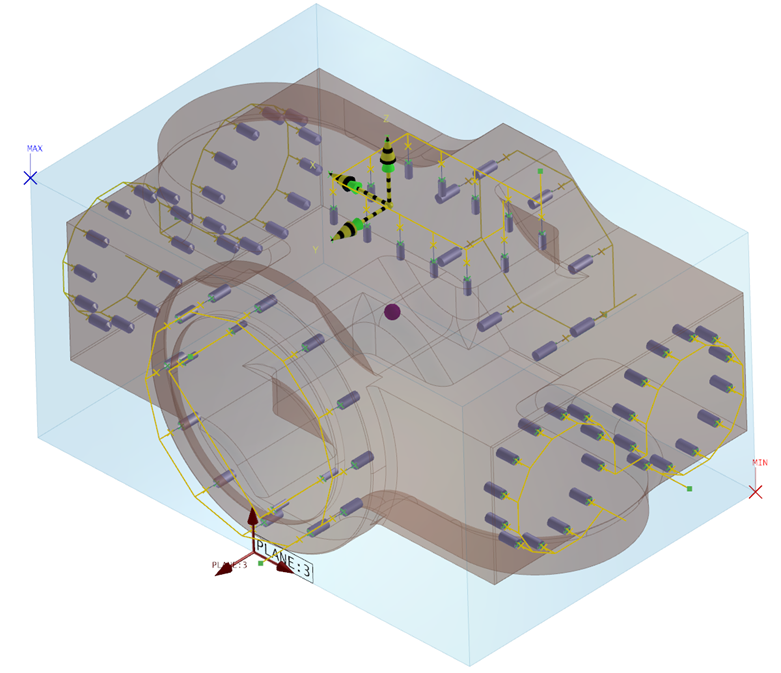
From data representing the initial state before machining and the technology features, analytical descriptions of the actual state after machining can be generated using various methods. These can then be integrated into the CAD/NC information process. Further processing in the CAD design process is also ensured in this way.
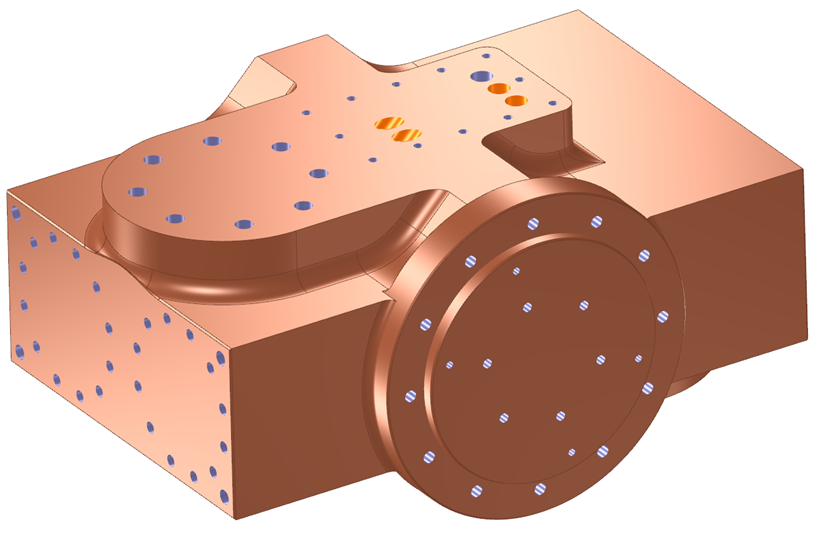
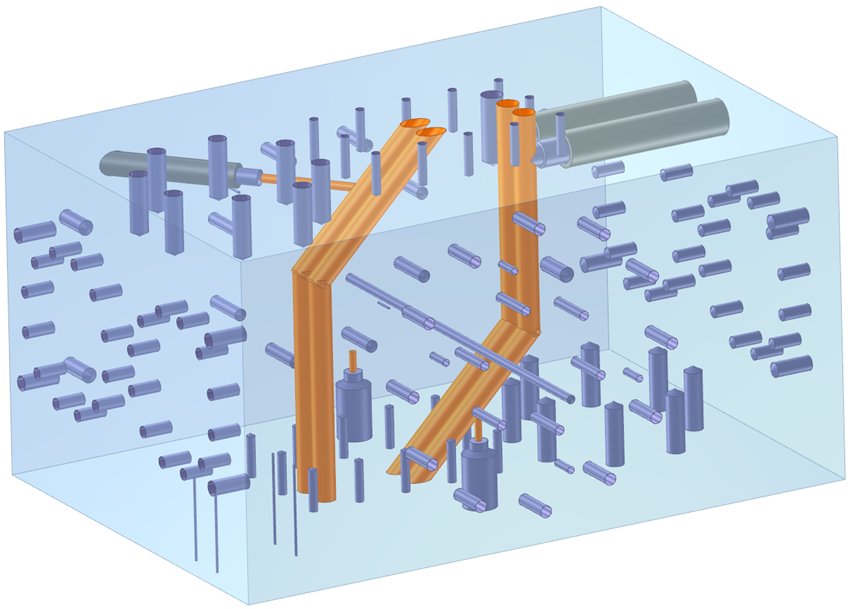
(Variants for different initial situations)
The programming step is completed by work planning with the definition of cutting data matched to the tool and machine. The basis for this is the work values that can be defined in the tool with material/cutting material allocation.
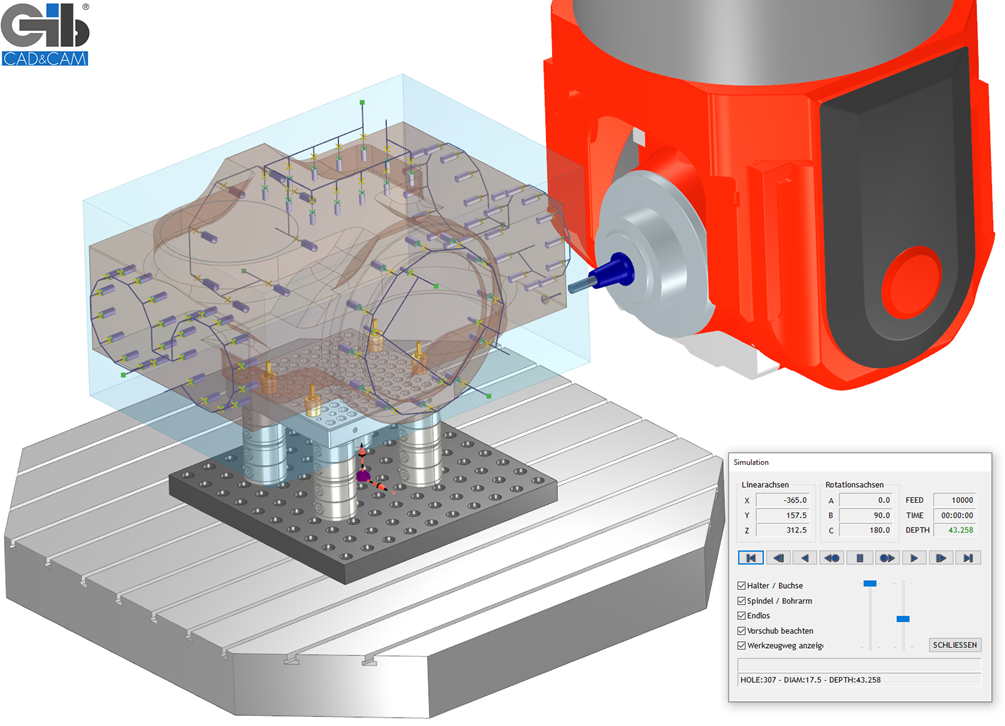
(Machine room simulation for a TRIMILL machining centre)
Ultimately, stable, process-reliable and automatable NC production sequences are planned and programmed with it. Functions such as tool and tool holder collision check, spindle head monitoring, machine room simulation with integrated machine, tool length determination and checking of infeed movements serve this purpose.
________________________________________________________________________
