ТМ
Tim- Роль курса ТМ и историческое развитие ТМ
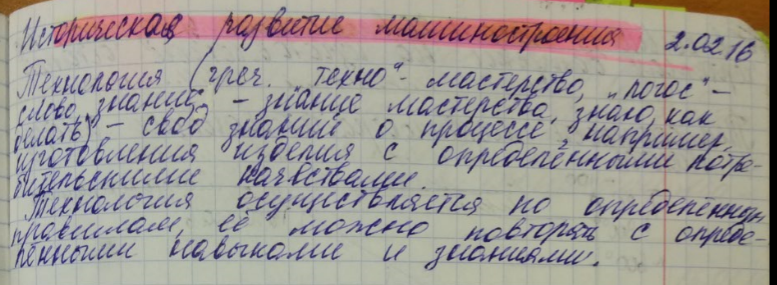
2. Основные современные этапы развития ТМ.
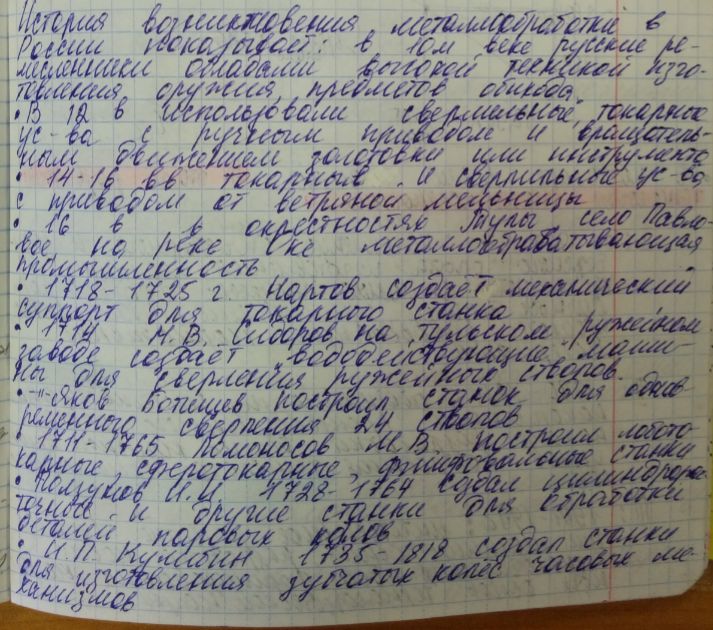
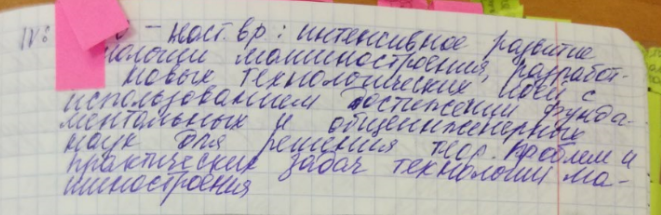
3. Определение и примеры понятий деталь, сборочная единица, комплект, производственный процесс, технологический процесс, рабочее место, операция, установ, позиция, технологический переход, рабочий ход, вспомогательный ход.
Деталь - изделие, изготовленное из однородного материала без применения сборочных операций.
Сборочная единица - изделие, составные части которого подлежат соединению между собой.
Комплект – набор изделий, имеющих общее эксплуатационное назначение вспомогательного характера.
Производственный процесс – совокупность взаимосвязанных действий, в результате которых материалы и полуфабрикаты превращаются в готовое изделие соответствующее своему служебному назначению.
Технологический процесс - часть производственного процесса непосредственно связанная с последовательными изменением состояния объекта
Рабочее место - участок производственной площади оборудованный соответстветствии с выполняемой на нём работе.
Операция - часть технологического процесса выполняемая на одном рабочем месте одним или группой исполнителей непрерывно.
Установ - часть тех. операции, выполняемая при неизменном закрепенной изготавливаемых заготовок или собирании сборочной единице.
Позиция - фиксированное положение занимаемое закрепленной заготовки или собираемом узле, закрепляемом относительно инструмента при выполнении определенной операции.
Технологический переход – законченная часть технологической операции, характеризуемой постоянством применяемого инструмента и поверхностей образуемых при обработке или сборке и характеруземая постоянством режима работы.
Рабочий ход - законченная часть технологического перехода, состоящая из однократного перемещения инструмента относительно заготовки, сопровождается изменением размеров, шероховатостей, свойств.
Вспомогательный ход - законченная часть перехода, состоящая из однократного перемещения инструмента относительно заготовки, не сопровождается изменением фрмы, размеров, шероховатостей или свойств заготовки, но необходима для выполнения рабочего хода.
4. Типы машиностроительных производств и их характеристика.
Коэффициент закрепительных операций
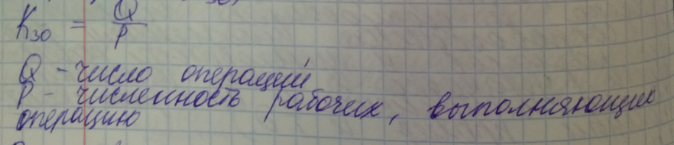
В зависимости от широты номенклатуры изделия различают 3 типа производств


Единичное производство
- широкая непланируемая номенклатура
- малый объём выпуска
- часто обработка выполняется на одном станке
- требуется высокая квалиффикация рабочего
- высокая себестоимость изготовления
- низкая производительность
Серийное производство - основной тип машиностроения (до 80% всех изделий)
- ограниченная номенклатура изготовляемых или ремонтируемых изделий повторяющимися партиями, небольшими выпусками
- Отдельные операции закреплены на определенных рабочих местах
Оборудование различного типа:
- специализированное
- универсальное
- агрегатное
Массовое производство:
- Узкая номенклатура
- высокий объём выпуска изделий, непрерывно изготовляемых в процессе длительного времени
- специальное оборудование, оснастка
- вначале требует большие капитальные затраты
- сложная смена технологий производства
5. Основы выбора заготовок
Заготовка выбирается максимально похожей к конечной детали. В этом случае наблюдается меньший отход металла в стружку, меньшее количество механических операций и увеличивается производительность труда.
Это обуславливает непрерывное повышение точности размеров и формы заготовок, повышение класса чистоты поверхности, обеспечивание заданных физико-механических свойств заготовки к соответствующим физико-механич. свойствам детали. При этом сокращается кол-во операций мех. обработки либо выполняется только финишные (шлифовка - чистовая операция, отделочные: доводка, притирка итд)
Снижение трудоёмкости последующих операций мех. обработки заготовок достигается рациональным выбором способа их изготовления. Это обеспечивает рост производительности на одних и тех же производственных площадках без дополнительного оборудования и оснастки.
Способы изготовления заготовок зависят от способа производства, поскольку кол-во изготавливаемых заготовок и периодичность их повторения, определяет затраты на производство, а следовательно и уровень его технического оснащения.
6. Заготовки из черных и цветных металлов, неметаллические.
7. Заготовки из металлокерамики
Изготавливаются из порошков различных металов или из смеси их с неметаллическими порошками. Для материалов, которые не могут быть созданы другим способом из тугоплавких материалов.
Способ получения металлокерамических материалов основан на прессовании тонких механических порошков требуемой смеси в пресс-формах под давлением от 1000-6000 кг/см2 и последующих спекании их при температуре плавления чуть ниже основного материала.
Получаются материалы с антифрикционными свойствами - подшипники скольжения
+ Получение деталей не требующих последующей обработки
- слабо поддаются механической обработке.
8. Кованные и штампованные заготовки.
При мелкосерийном производстве применяют свободную ковку на ковочных молотах и гидравлических кованных прессах.
Заготовки имеют грубую форму приближенную к форме детали и требуют больших трудозатрат на последующую мех. обработку.
Для дальнейшего приближения форм и размеров заготовок к готовой детали в мелкосерийном производстве применяют ковку в подкладных штампах.
В серийном и мелкосерийном производствах заготовки как правидл делают на штамповочных молотах и прессах в открытых и закрытых штампах.
Штамповка может осуществляться в одно и многоручьевых штампах.
Для изготовления заклёпок применяют холодно высадочные автоматы. Детали имеют высокую точность и низкую шероховатость.
Штамповка из листового металла позволяет получать изделия простой и сложной формы при этом толщина стенок заготовок должна быть постоянно, в том числе в местных изгибах.
Не требует мех. обработки. напрямую поступают на сборку.
10. Основные требования к заготовкам
Общие требования:
- Фасонные детали, испытывающие большие напряжения следует выполнять из стальных отливок
- Фасонные детали, не подвергающиеся ударным нагрузкам и действию напряжения изгиба - чугунные отливки
- Заготовки в виде поковок изготавливаемые ковкой и штамповкой следует применять для деталей, работающих на изгиб, растяжение и кручение, а также имеющим значительную разницу в поперечных сечениях.
- Заготовки в виде поковок применяют для крупных деталей, а в условиях их единичного, мелкосерийного производства для мелких.
- Заготовки в виде штамповок могут применяться в том случае если условия производства крупносерийное производства крупносерийное или массовое. Посольку для их изготовления требуются дорогостоящие штампы.
- Штамповочные заготовки: структура металла более однородная, размеры более близки к окончательным. При этом потребуется минимальная мех. обработка или её отсутствие.
11. Базирование
При обработке заготовок на станках необходимо обеспечить их положение относительно механизмов и узлов станка. Задачей определения положения деталей при обработке на станках и их сборке в узлах и механизмы решаются на основе базирования.
Базирование - придание заготовки или изделию требуемого положения относительно выбранной системы координат
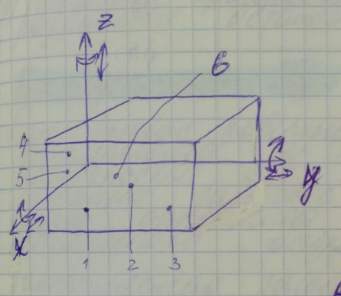
Схема базирования - схема положения опорных точек на базовых поверхностях.
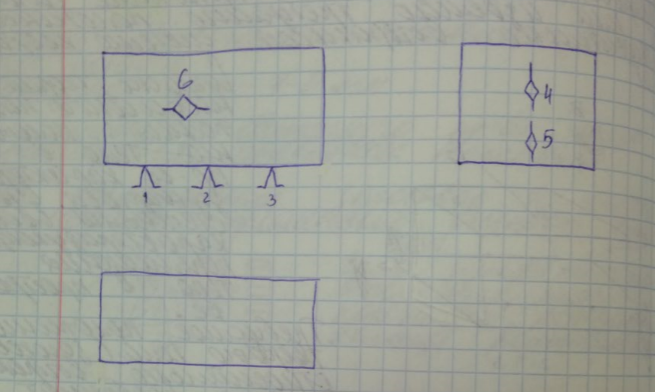
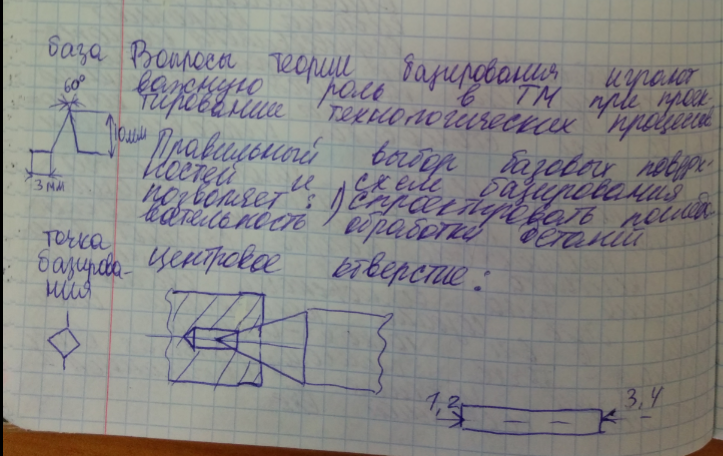
12. Особенности конструкторской, технологической и измерительной базы.
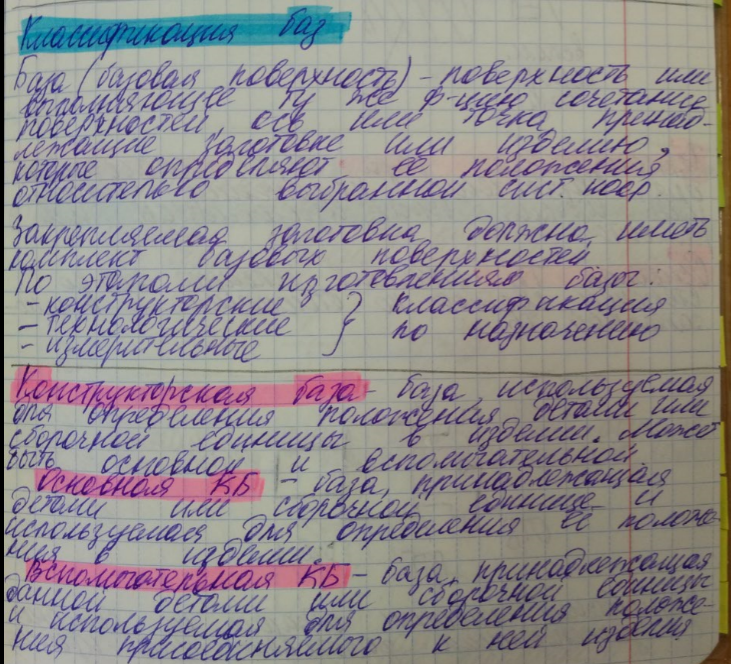
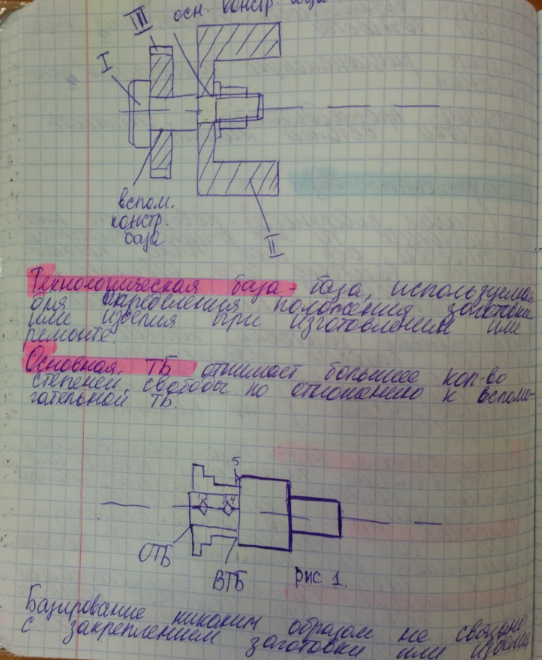
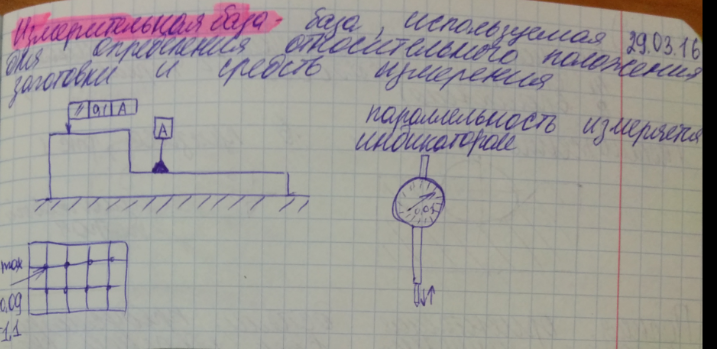
13. Характеристики баз
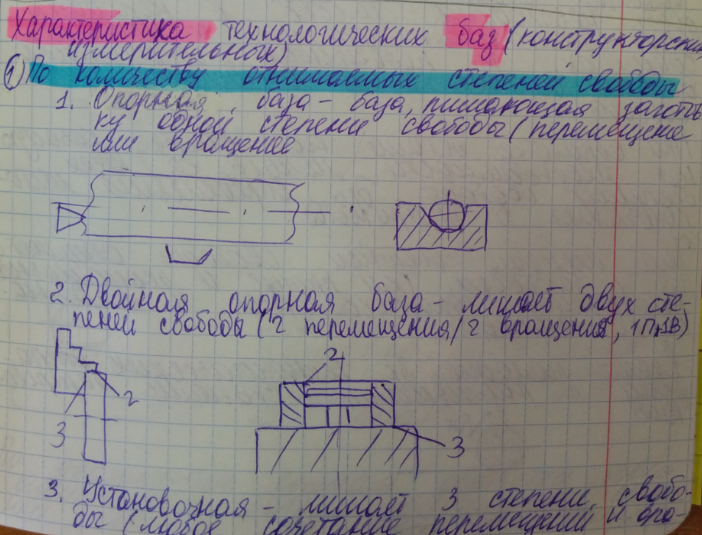
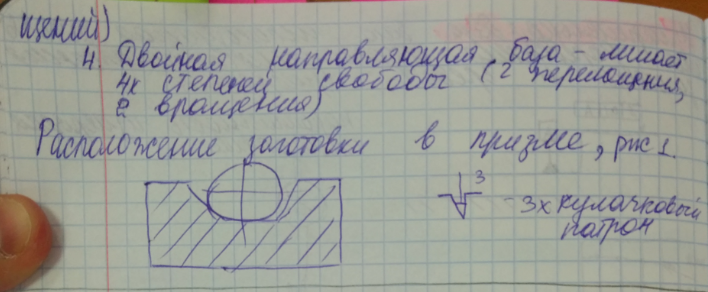
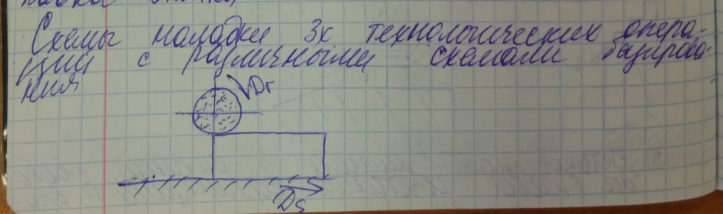
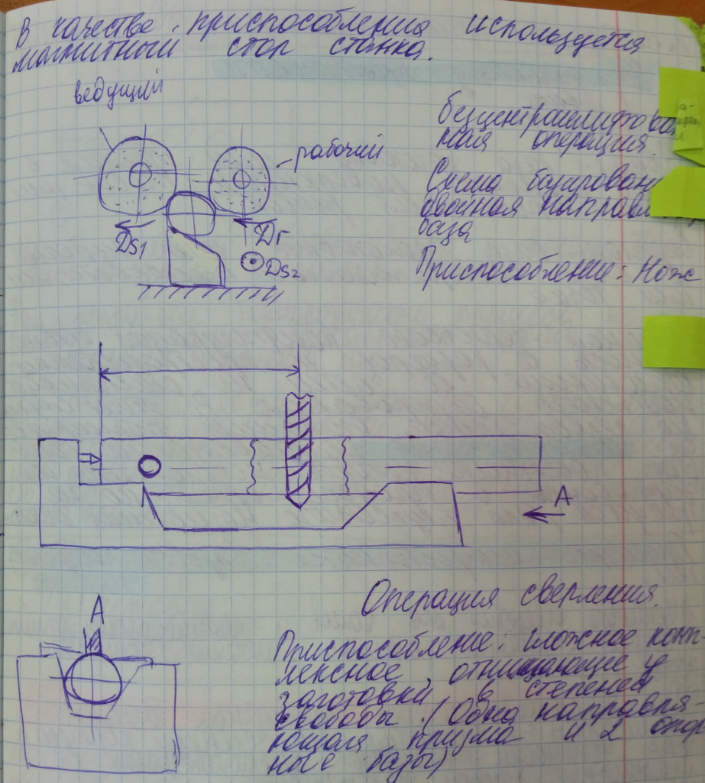
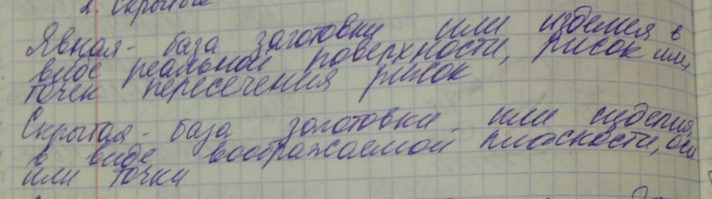
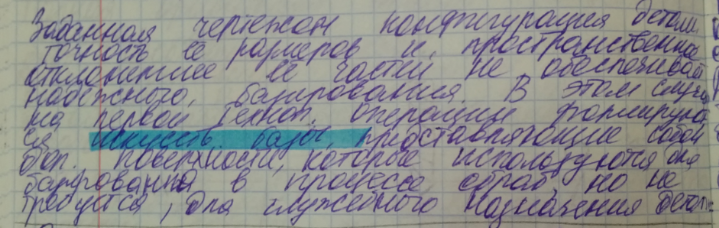
14. Установка заготовок на станке.
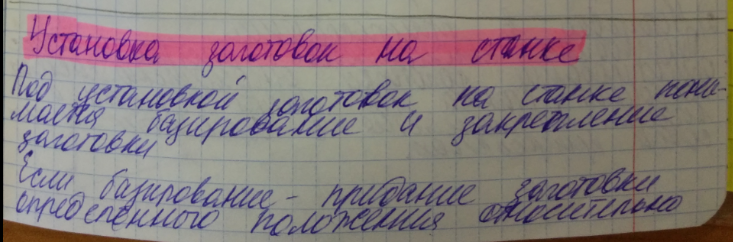
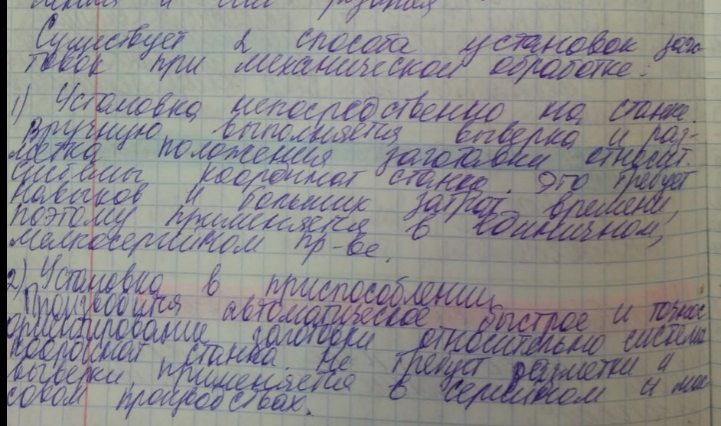
15. Определенность базирования заготовок при изготовлении партии деталей
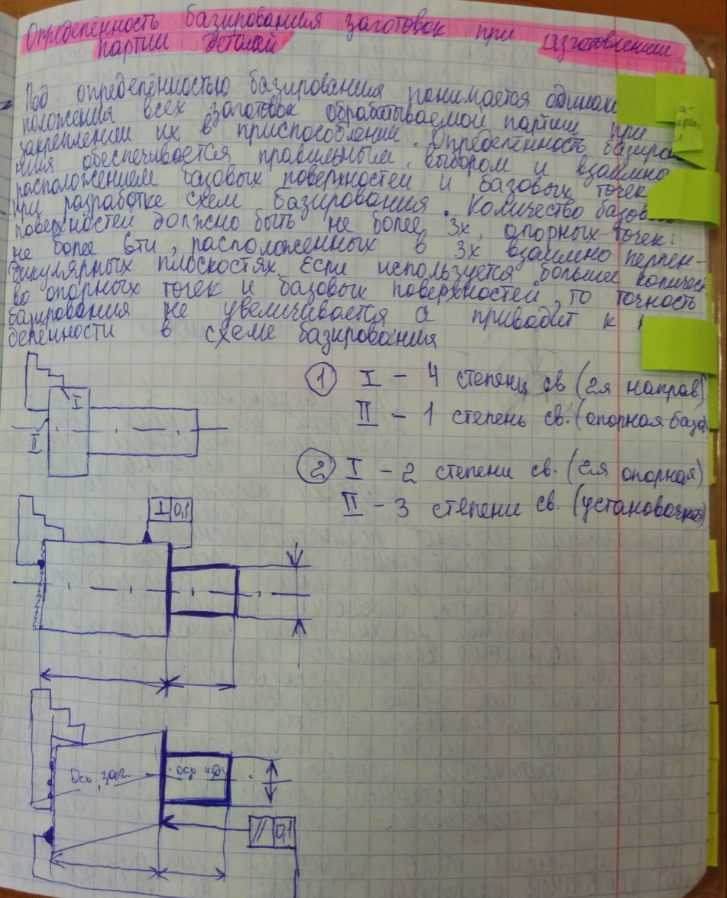
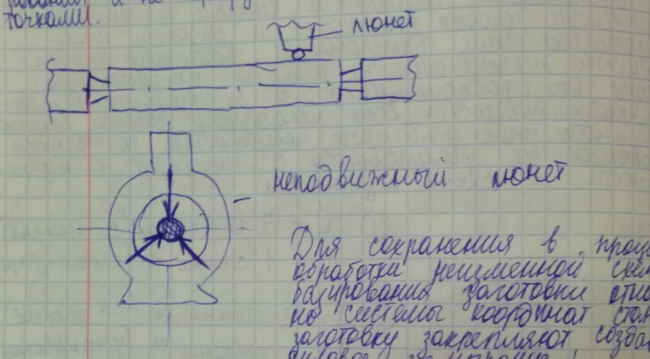
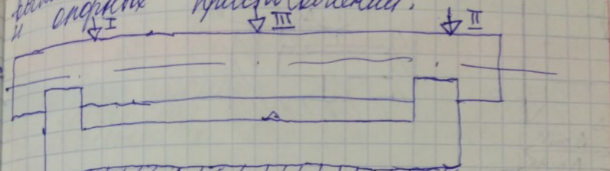
16. Погрешность базирования, закрепления, установки заготовок.
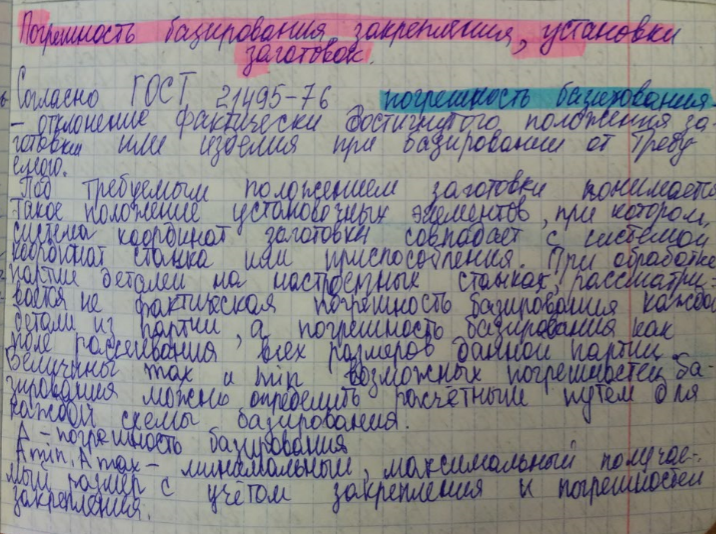
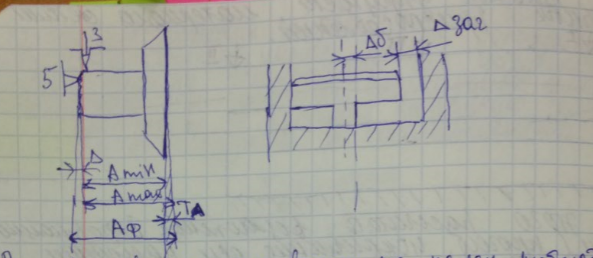
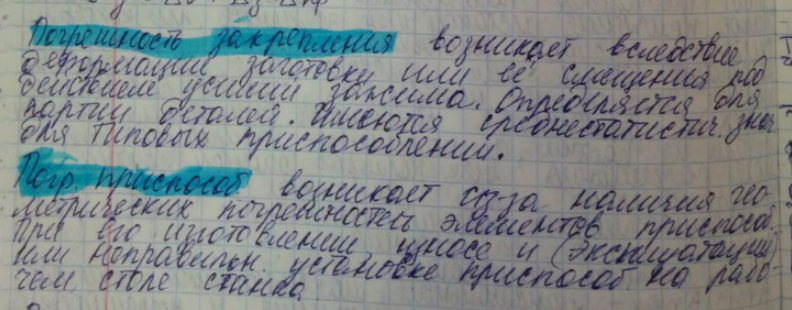
17. Смена баз


18. Выбор баз при проектировании ТП
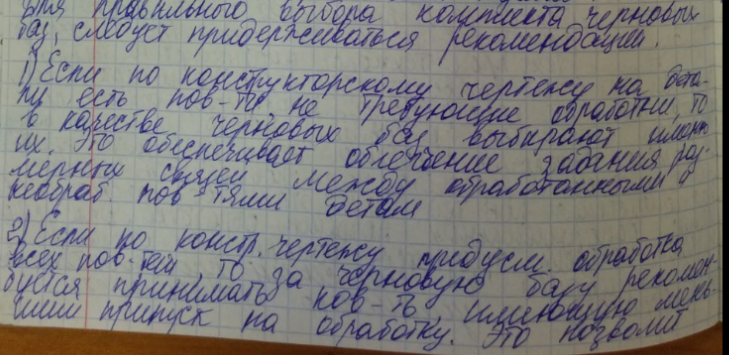
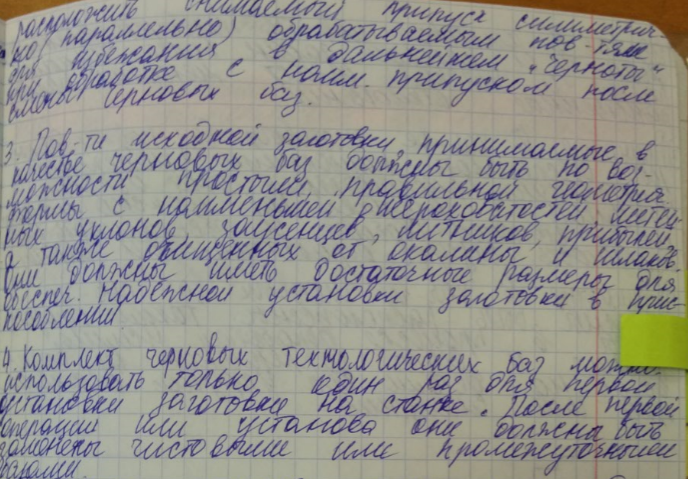
19. Основные комплекты технологических баз, применяемые при обработке.
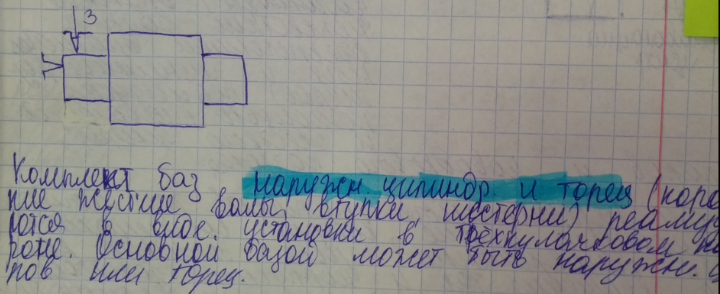
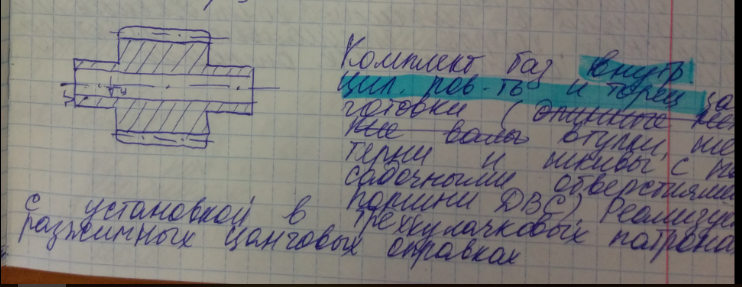
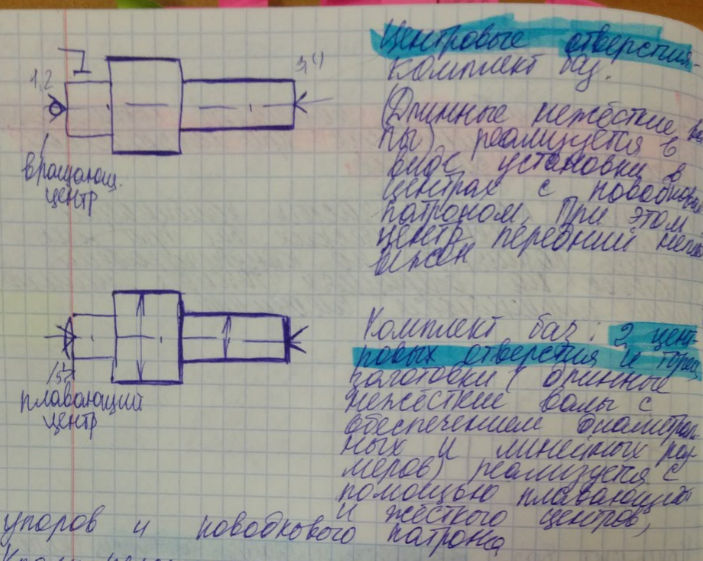
20. Основные понятия точности обработки.


21. Способы обеспечения заданной точности обработки деталей
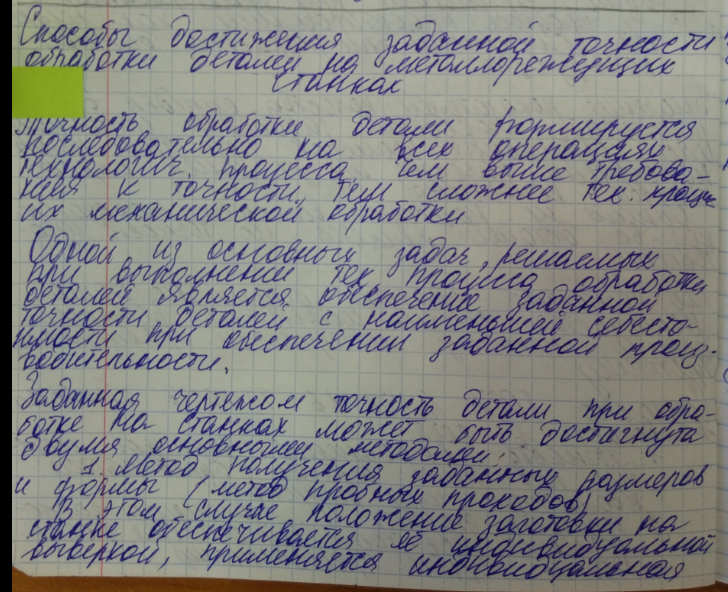

23. Погрешности изготовления режущего инструмента и его размерный износ в процессе эксплуатации


23. Приближённость реальной кинематической схемы обработки к идеальной схеме обработки.


25. Геометрическая погрешность станка и приспособления, и их износ в процессе эксплуатации.
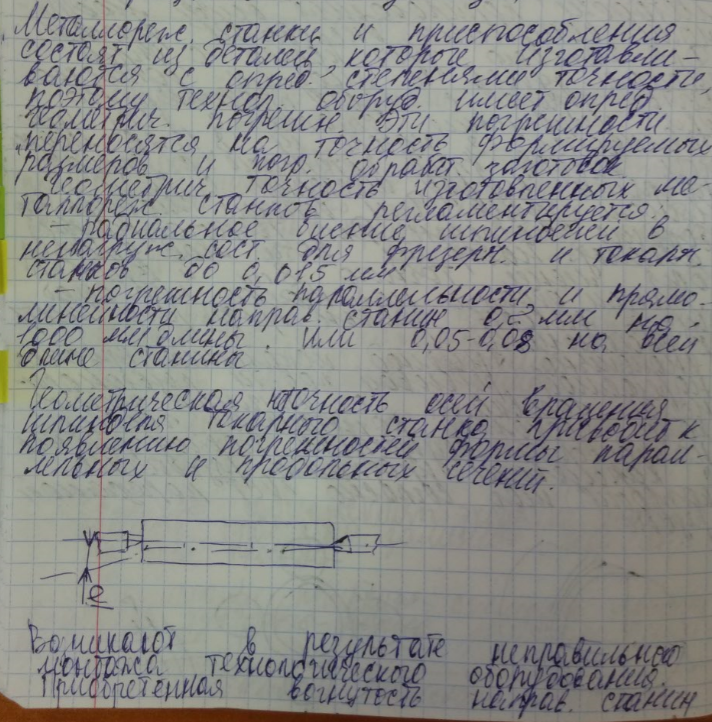
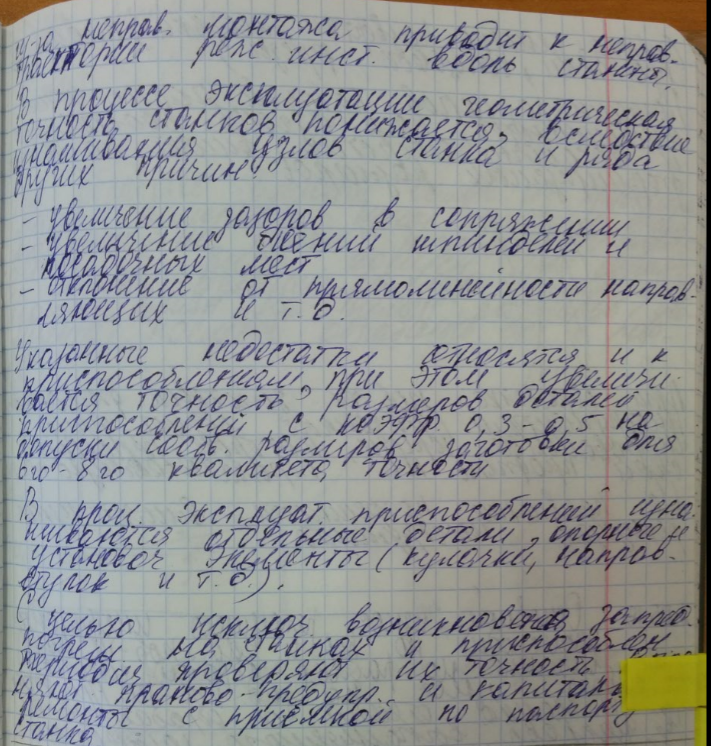
26. Погрешности изготовления режущего инструмента и его размерный износ в процессе эксплуатации
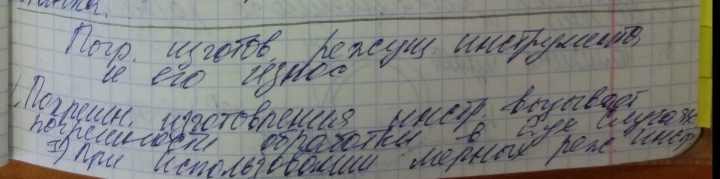
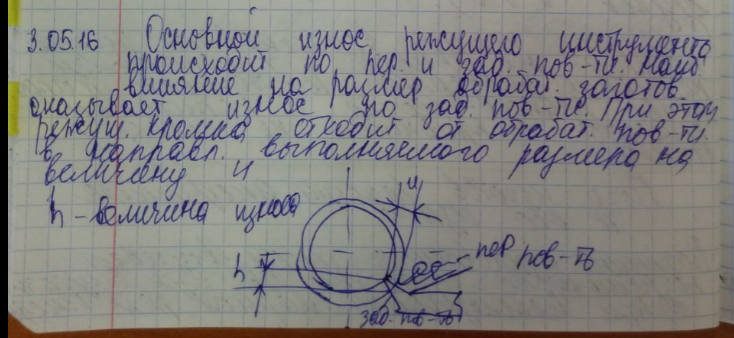
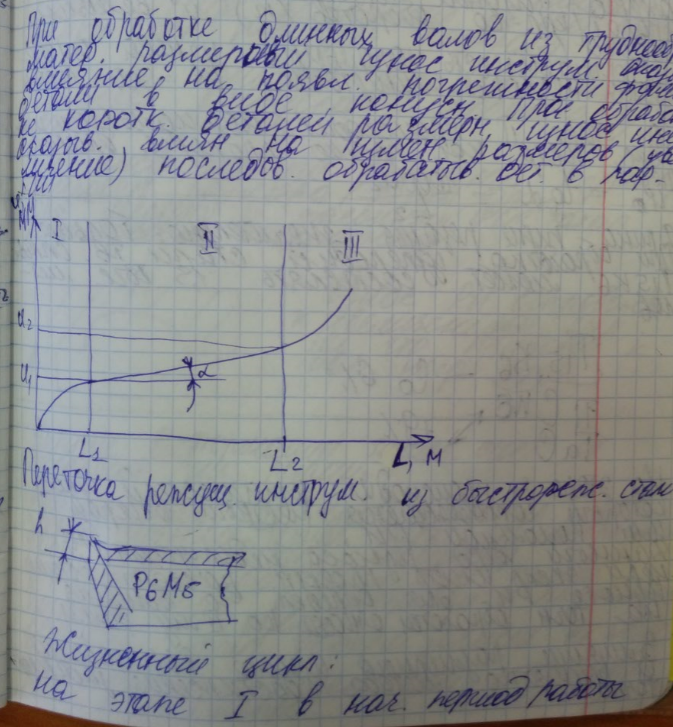
27. Упругие деформации технологической системы от действия сил резания и усилий закрепления.
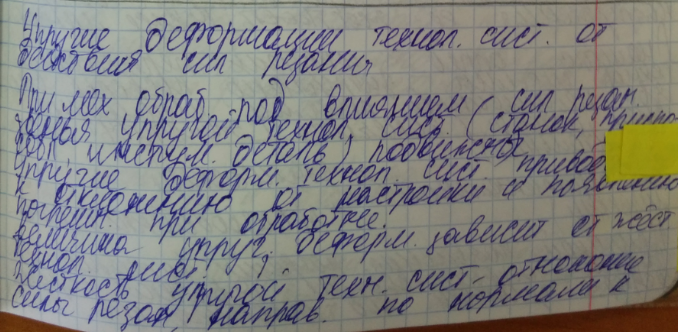

28. Температурные деформации станка, режущего инструмента и обрабатываемой заготовки.
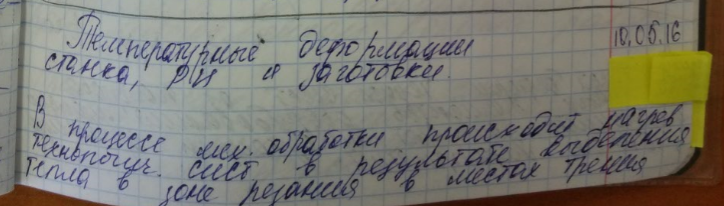
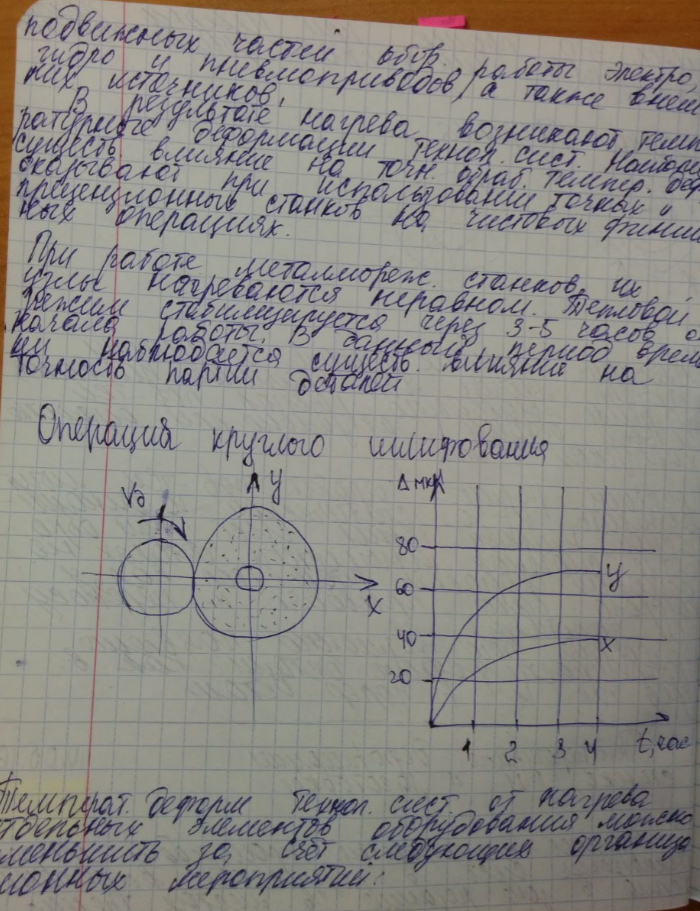
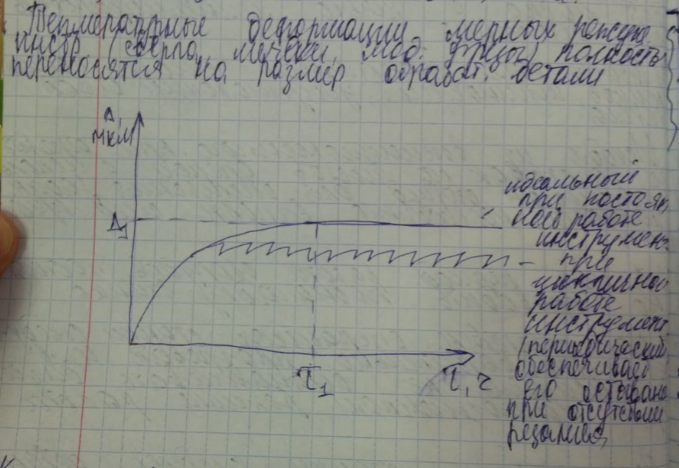
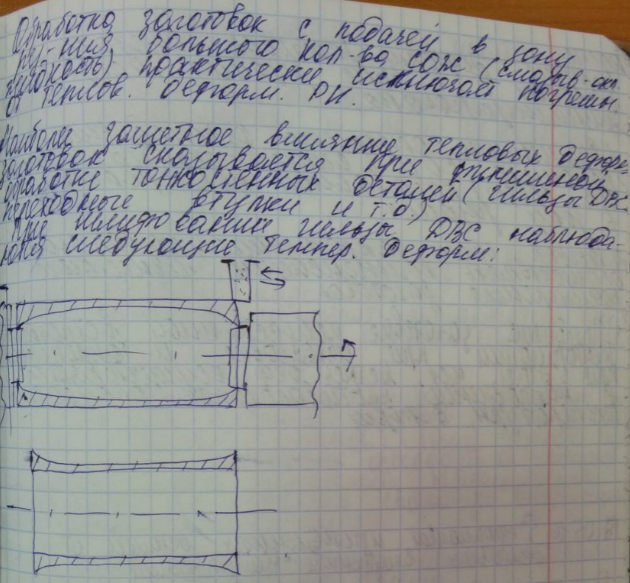
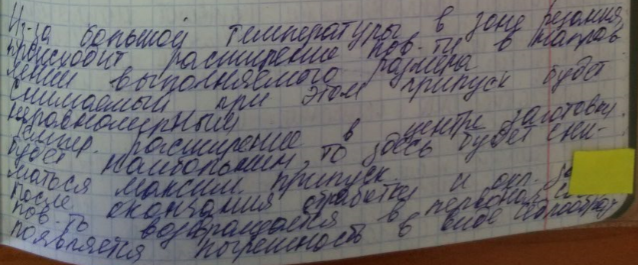
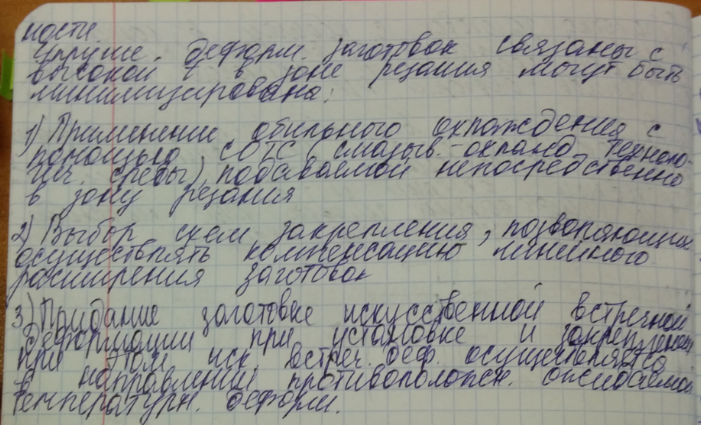
29. Деформации обрабатываемой заготовки от действия внутренних напряжений.
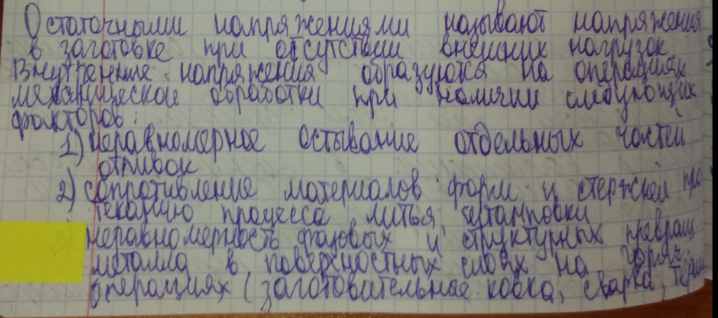
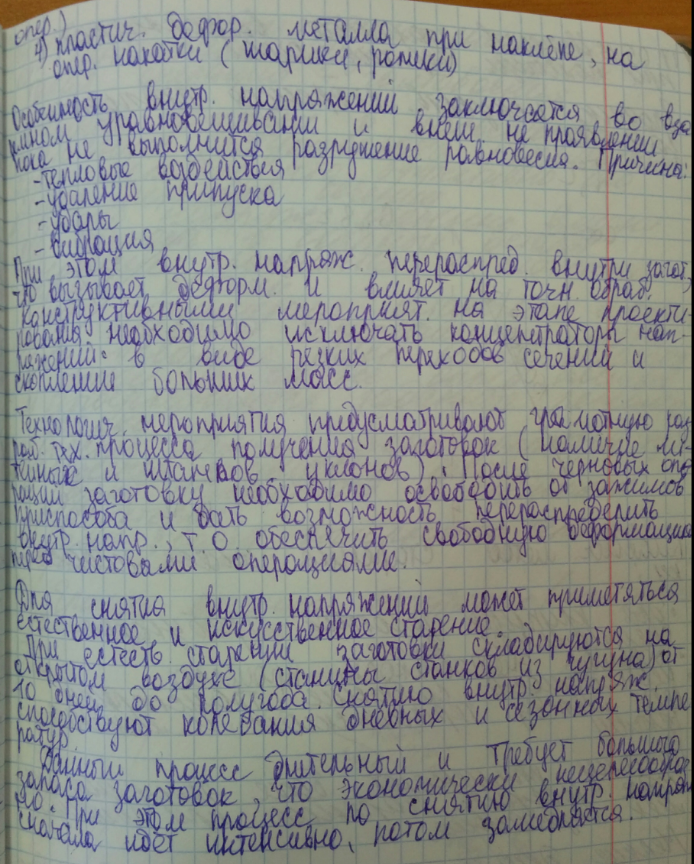

30. Погрешности настройки инструмента на размер.

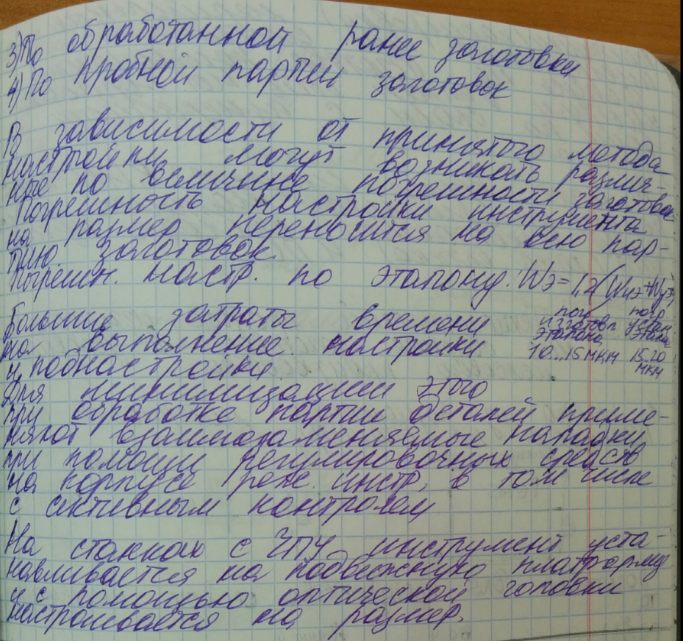
31. Погрешность измерения
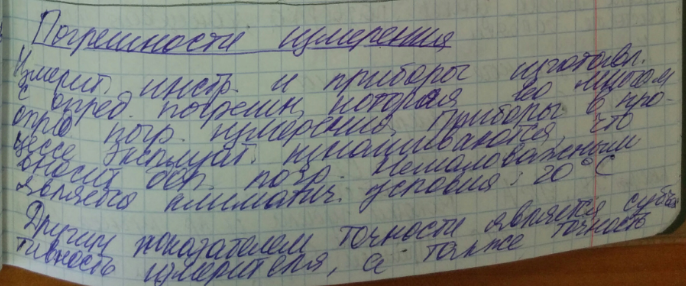
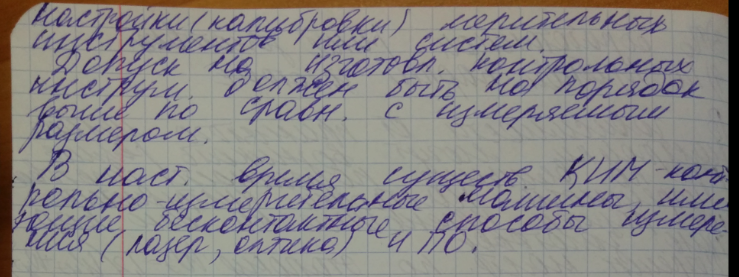
23. характеристика металлорежущих станков
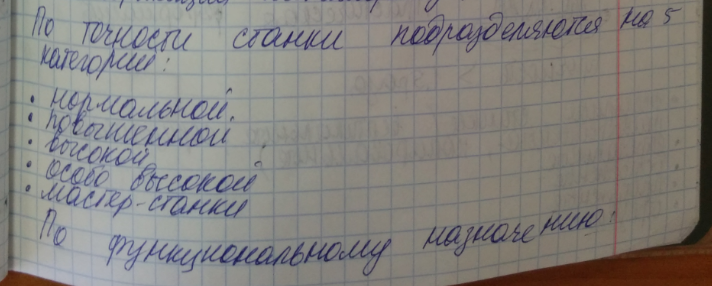

24. Характеристика оборудования
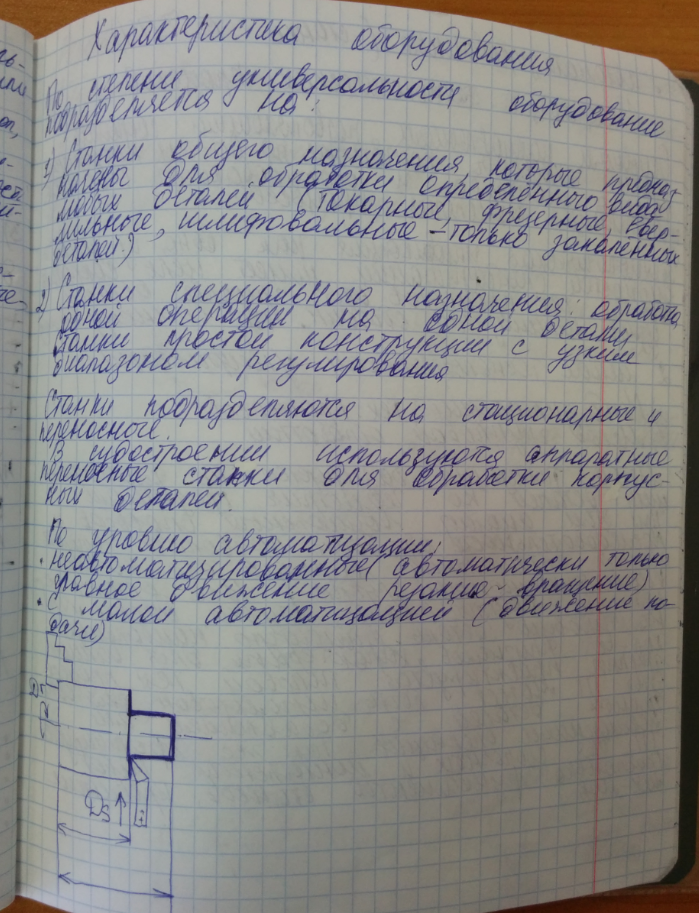
25. Унификация технологических процессов
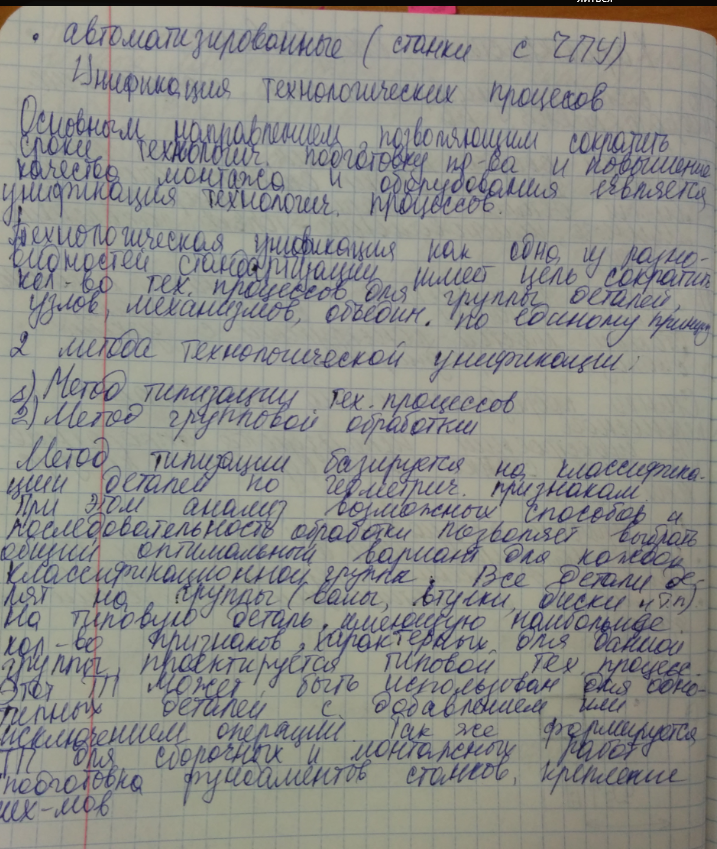
30. Термическая обработка металлов и сплавов
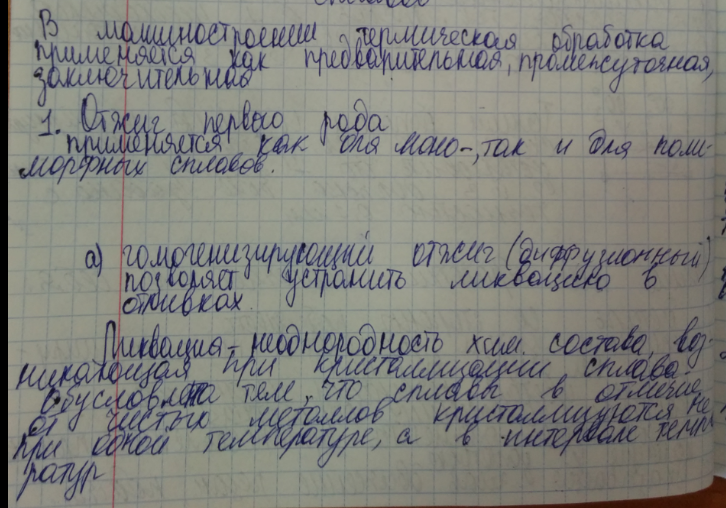
33. Сущность и особенность отжига
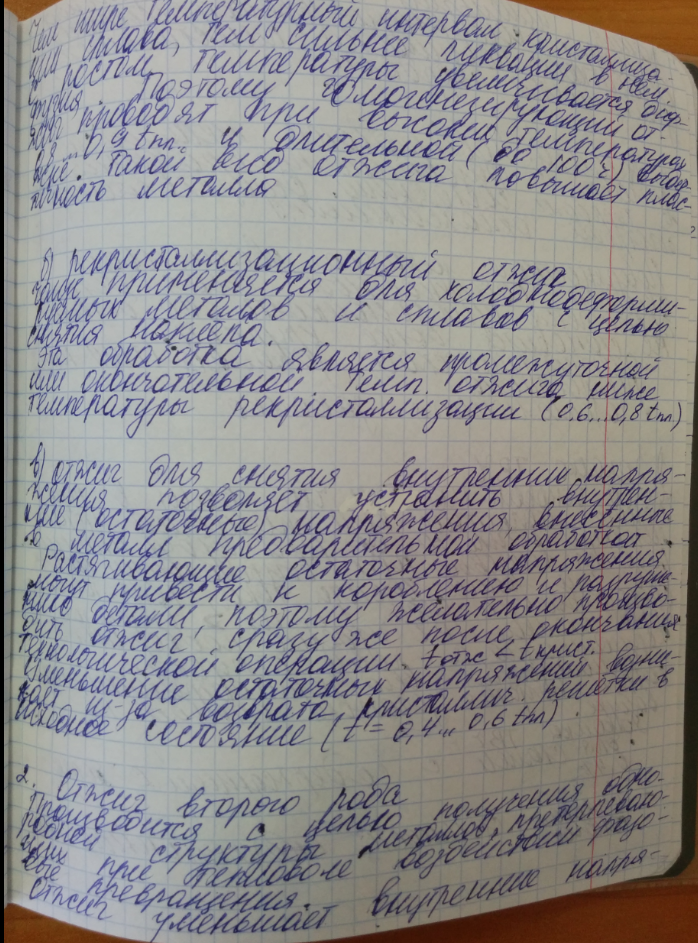
31. Сущность и особенности заказки

32. Сущность и особенности отпуска.
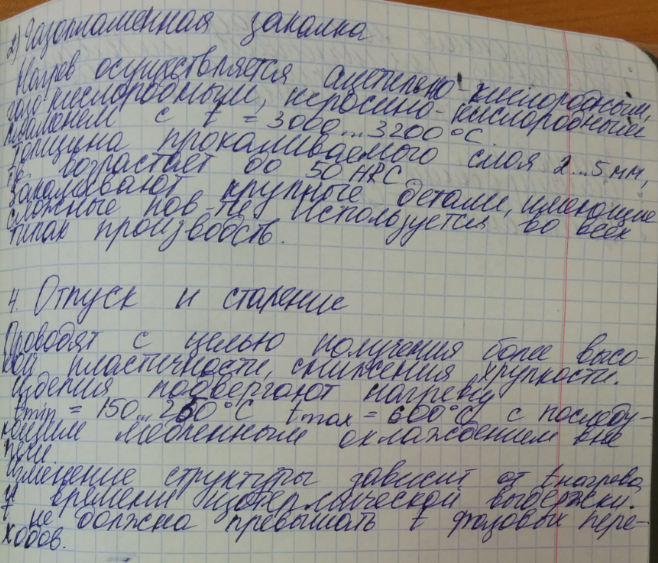
39. Электрические методы обрабтки. Электрохимический метод обработки. Схемы.
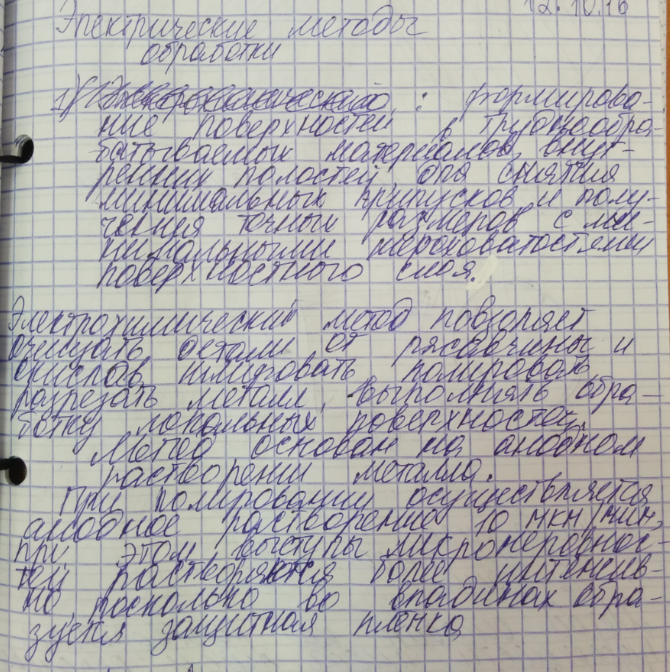
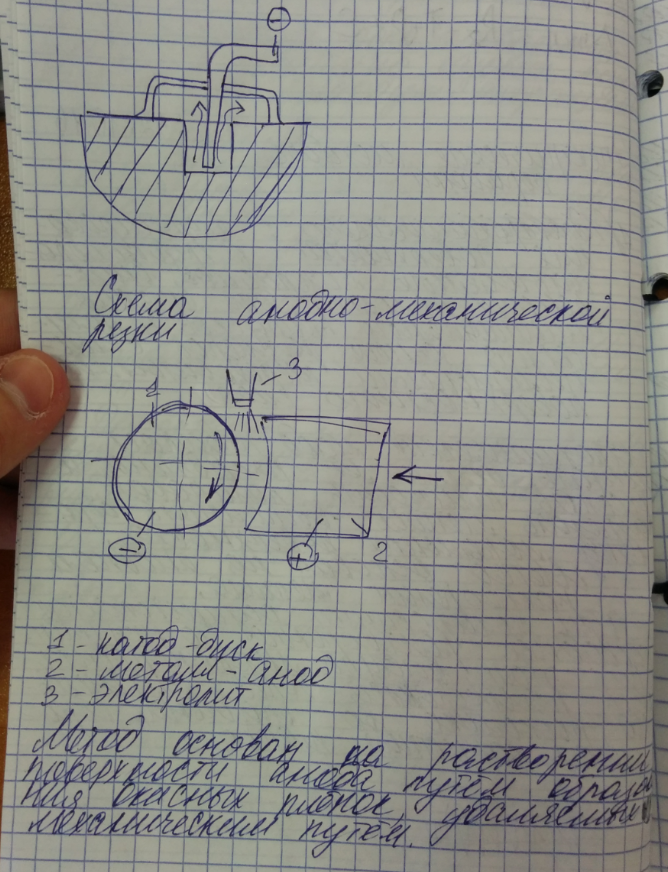
40. Электротермический метод обработки. Схемы.
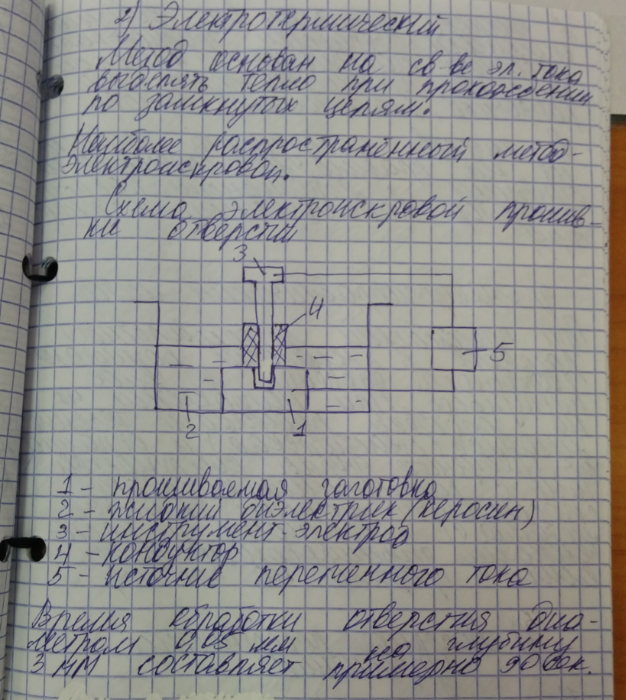
41. Ультразвуковой метод обработки и электрогидравлический метод.


42. Лазерное поверхностное упрочнение и лигирование.
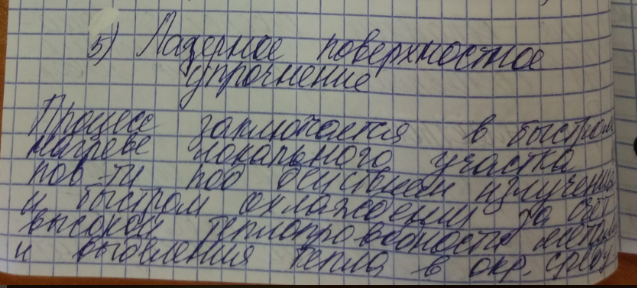
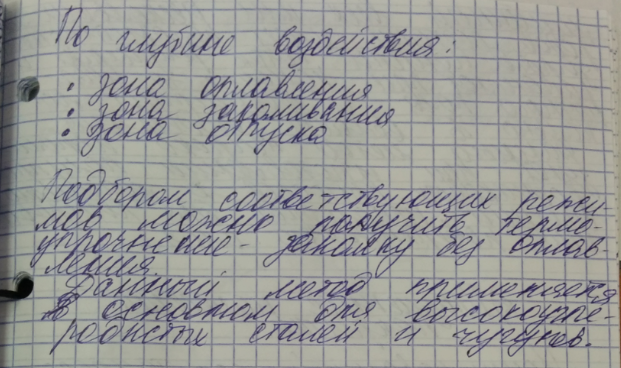

43. Ионная имплантация и плазменное нанесение покрытий.
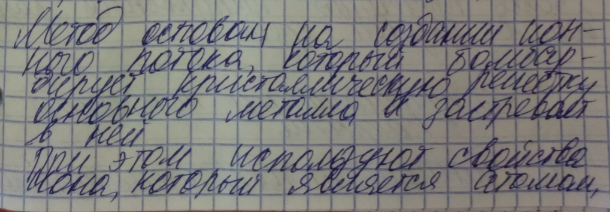
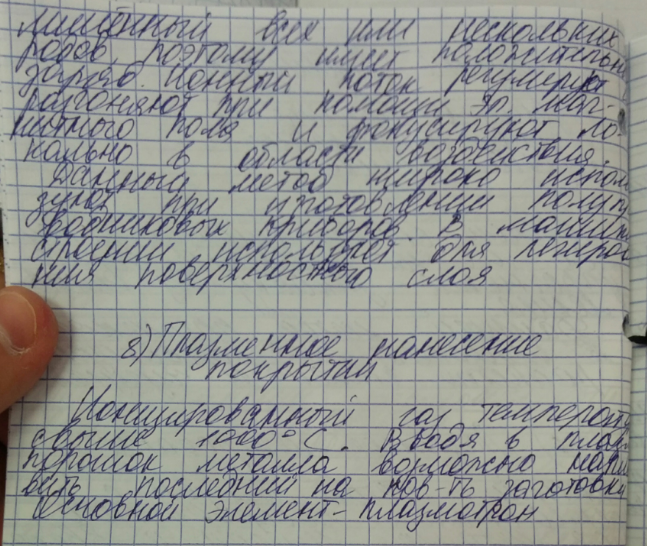
44. Электроискровое легирование и детонационногазовое нанесение покрытия. Схемы.

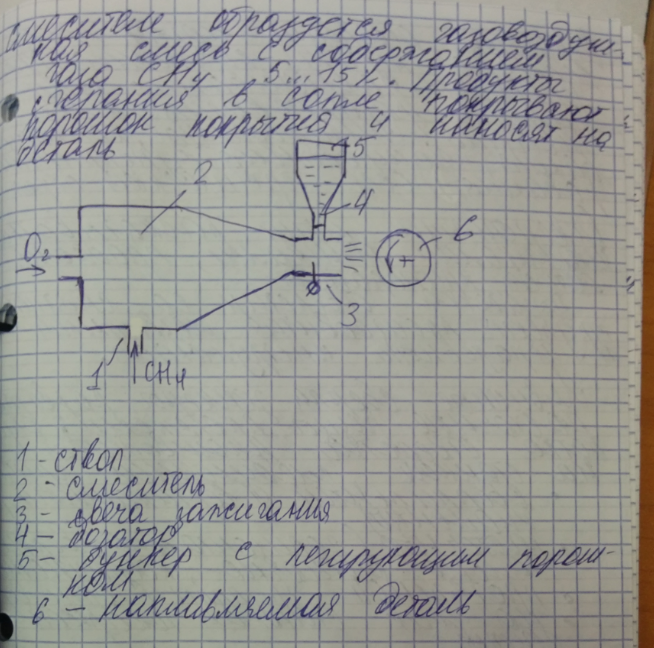
37. Отделочная обработка. Суперфинишироание. Схемы обработки.

38. Полирование
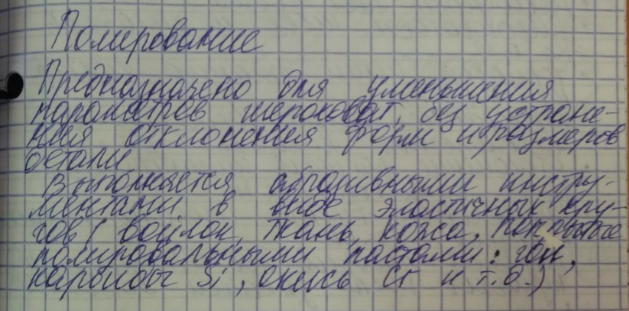
47. Обработка резьбы резцами
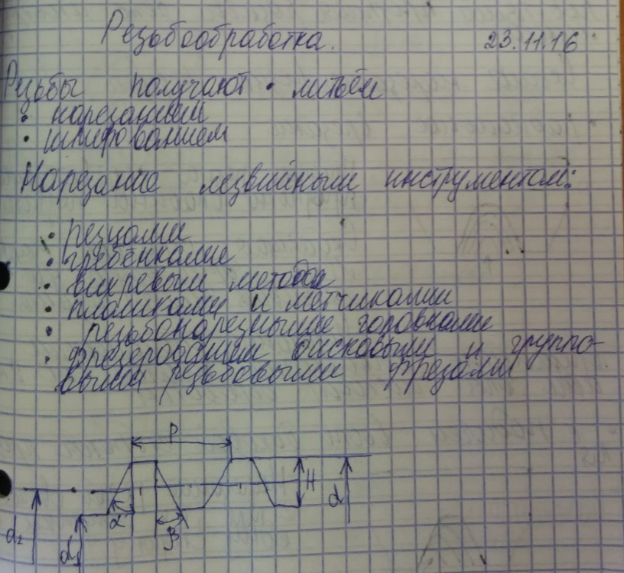

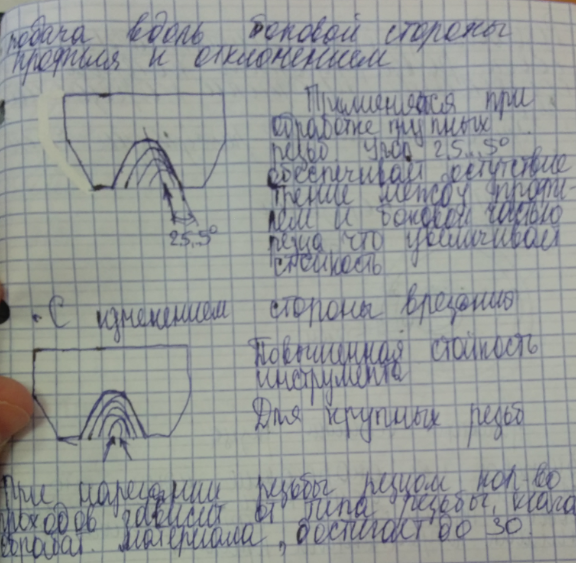
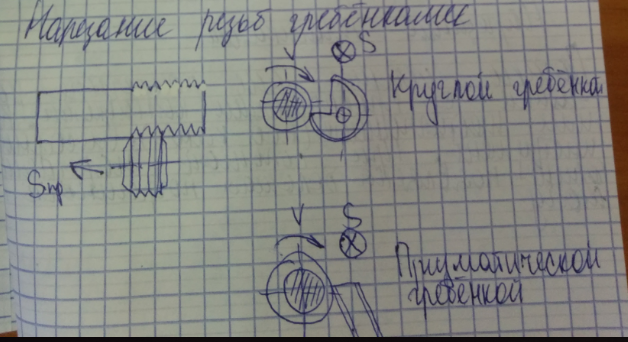
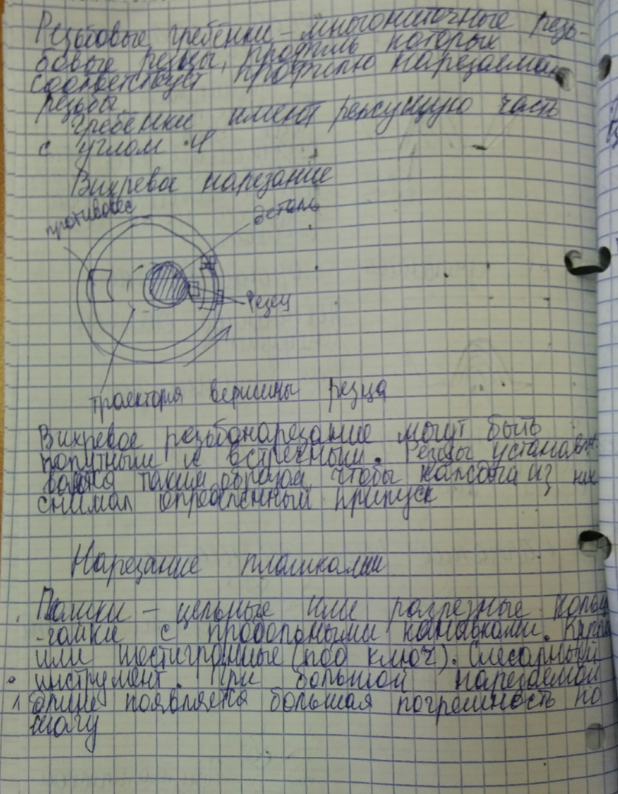
49. Нарезание резьбовыми головками

49. Обработка резьбы резьбонарезными головками, шлифованием. Схемы обработки.
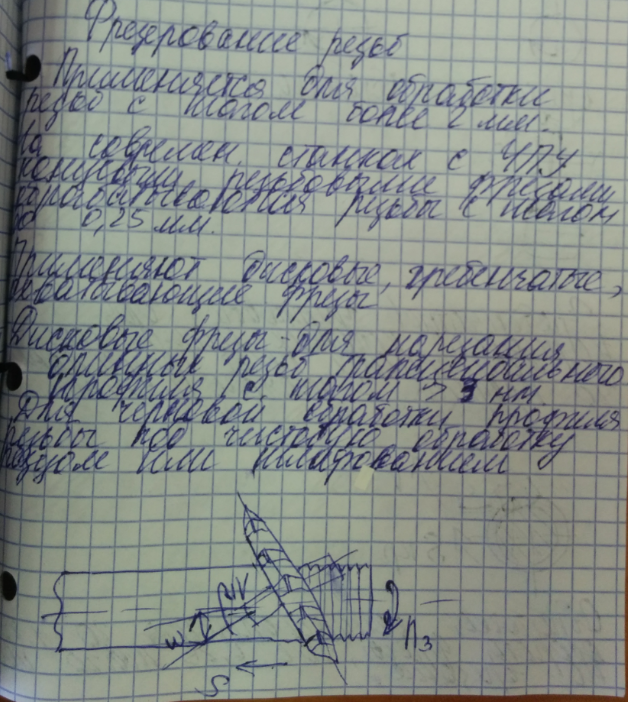

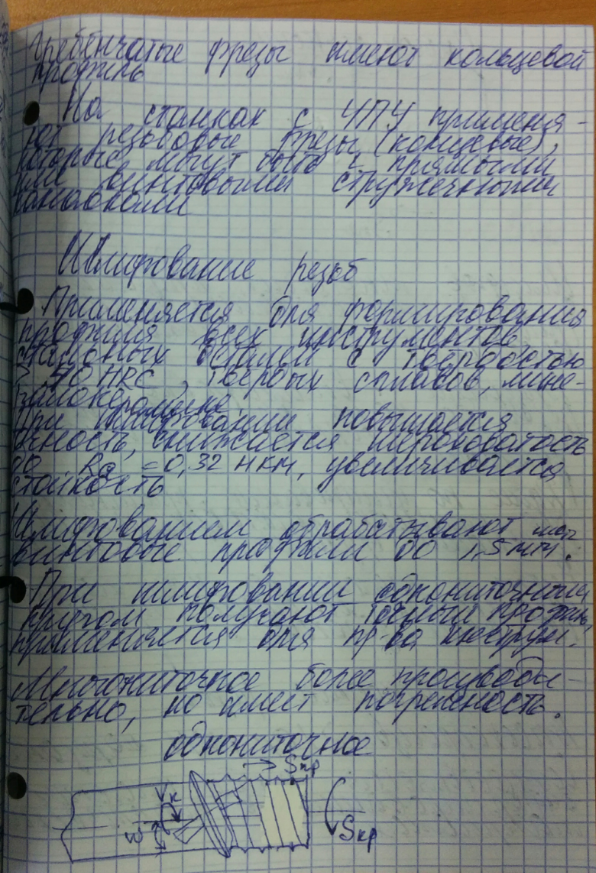
50. Накатывание резьбы. Схемы обработки.


Прочее, но наверное важное

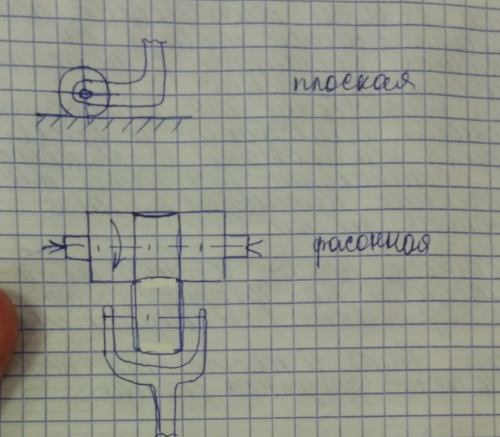