Not all ores are equal and some ores are more equal (apologies to George Orwell)
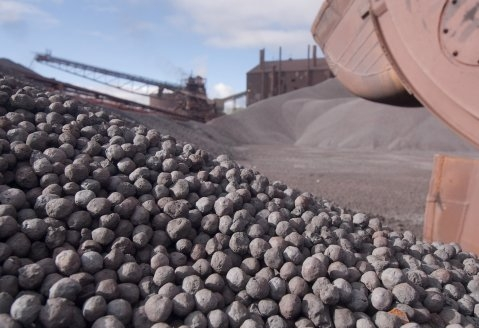
Just as there are clean, sweet crude oils and dirty, sulphurous, polluting crude oils, there are high quality, low emission iron ores and low quality, difficult to process, high emission iron ores.
The focus of steel makers on high productivity with reduced emissions is creating an ever-widening price gap between high quality premium ores and lesser quality ores. You could say that as steel mills strive for higher outputs with lower emissions high grade, high quality ore is ultra-equal.
There is a flight to quality for steel making inputs. “High iron! low phosphorous! low alumina! no sulphur!” are the catch cries among blast furnace operators globally. In this flight, one iron ore type that the steel mills are turning to is magnetite concentrate. Magnetite is the mainstay of the US and Russian steel industries and it was in China until the first decade of this century.
With the right deposits and the right mineralogy, a very high-quality magnetite concentrate can be virtually tailor made. On the other hand, with direct shipping ores such as haematite and goethite, what they shovel is what you get as a steel maker. These haematite and goethite ores are the prevalent product in the Pilbara in Australia and the iron quadrilateral in Brazil. Iron grade is declining and deleterious element content is increasing in both these locations.
In China, traditionally, magnetite was the principal iron feed to blast furnace steel making. Chinese domestic magnetite production, however, is now a third of previous high levels. Deposits are exhausted. Remaining deposits are sub-economic.
Previously, the concentrates were first made in hard baked pellets before being charging into the blast furnace. Now some mills have determined how to improve the quality of the predominantly haematite-fed sinter plants by blending magnetite concentrates into the blend. Sintering is another process for agglomeration of fine ores prior to charging into the blast furnace. All fine ores and concentrates have to be agglomerated before charging to the blast furnace or direct reduction reactor.
The importance of this drive among Chinese mills to high quality inputs to achieve high production rates with lower emissions is underlined by central government restrictions being placed on steel mills, cement plants and coal-fired electric generators in the lead-up to the smog-prone winter that starts this month.
One market segment where high quality magnetite is emerging supreme is in the direct reduction steel making process, where iron ore pellets are reduced to metallic iron by reformed natural gas rather than the coke of blast furnaces. Pellets with an iron grade better than 67.5% iron are required. This means a concentrate grade of at least 69% iron. Of the large big 4 haematite/goethite producers, only one can supply such high grades – but it is haematite.
A key benefit of magnetite is that it is exothermic. That is, it generates heat during the pellet making or sintering process. As a result, it uses four times less energy than haematite in these processes and – pleasingly for Beijing’s pollution policy makers – significantly reduces emissions by up to 108kg of CO2 per tonne of molten iron (hot metal).
While there’s no shortage of magnetite deposits in the world, many have impurities that lessen their quality. There is a quality hierarchy in magnetites just as in haematites. In the words of our chairman Gordon Toll: “Not all magnetites are equal. Some magnetites are more equal.”
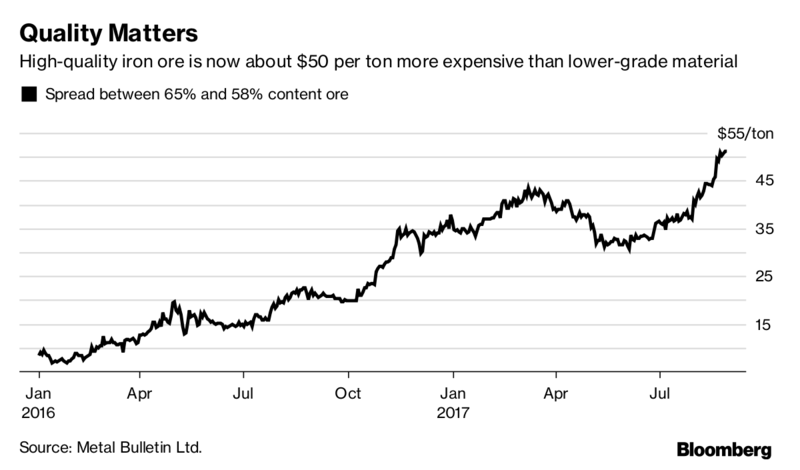
Global ore buyers are currently willing to pay a steep premium over the Pilbara 62% benchmark price for higher-grade ores and concentrates while heavily discounting poor-quality ores.
The current benchmark rate for ore with a 62% iron content is around $US60 a tonne and recently was as high as $US80/t, with prices of $US100/t and beyond achieved for 65%-plus ore.
Toll says a new paradigm of “high quality ores, low emission, high productivity” is emerging among Chinese steel makers in particular.
“The deep discounts on low quality ores and concentrates will continue,” he says. “We may witness a situation in the future when not even deep, deep discounts will ensure the sale of poor quality ores and concentrate.”
Globally, steel usage is bouncing back strongly. According to the World Steel Association, crude steel output grew 6.3% year on year in August to 143.5 million tonnes, with Chinese output surging 8.7% to 74.6mt.
Year to date global production has risen 4.7% to 1.07 billion tonnes. Longer-term projections suggest average annual growth of 1.9-2.1% to 2030, requiring 30-40mt of new product annually.
This does not even factor in demand from India, which is targeting 300mt of steel production by 2030. This would require 480mt a year of iron ore compared with 180mt currently.
In the Middle East and North Africa (MENA), demand for iron ore concentrates is likely to grow by 30-50mt a year, with many other magnetite producers unable to produce the requisite quality.
At Magnetite Mines, we have the good fortune of sitting on a very high-quality deposit – at our flagship Mawson Project in mining friendly South Australia.
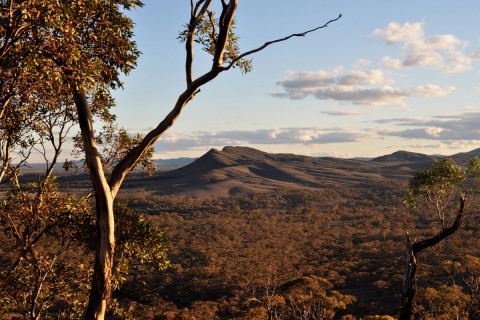
Located 250km northeast of Adelaide on the Braemer Iron Formation, Mawson consists of the Olary and Razorback projects on contiguous ground covering a strike length of 120km.
A feature of the Braemer ore is that it is softer than its Pilbara hard-rock equivalent and the low overburden makes it easy to extract.
Unlike many haematite deposits, ours are low in phosphorous. Phosphorous is one of the most problematic elements in steel making as it is impossible to make good steel with high phosphorous levels.
Mawson is the world’s biggest undeveloped magnetite deposit, with an official (JORC) resource of 4.6 billion tonnes, with further geological potential of 30 to 50 billion tonnes.
The grade of the Mawson ore in the ground varies from 11-25%. However, the grade of concentrates after beneficiation exceed 68%. That is higher than the typical magnetite concentrate in global trade and in China of 66% iron or less.
Toll says that while there’s still a perception of iron ore oversupply, much of the product is “lousy quality” and getting worse.
The Mawson project is predicated on the smaller Olary deposit as a quick-start venture, targeting an initial 5mtpa and then 25mtpa of ultra-high-grade direct-reduction ore to MENA and other direct reduction markets.
Razorback would supply blast furnaces to China and the Far East with initial output of 25mtpa rising to 100mtpa.
Both projects are based on transporting the output by rail or slurry pipe to Spencer Gulf, where the ore would be piped to floating port facilities capable of handling the biggest (cape-size and Vale-size) bulk carriers.
In July, we signed a non-binding letter of intent with Kuwait Steel to supply four million tonnes of high-grade pellets annually from the Olary project. This product will be used in a new direct reduction steel mill
There’s plenty that needs to happen yet and a definitive feasibility study is planned for the near future.
But given the supply and demand dynamics, we are excited about demonstrating that our ores are more equal than other ores.